www.industryemea.com
30
'23
Written on Modified on
Smart Factory: fully automated flexible production, even for small quantities
24/7 production with automated clamping device change-over from Hainbuch, even for batch size 1.

Inside WTO’s Smart Factory.
For years, production costs have been heading in only one direction steeply upward, while the demand is for ever lower manufacturing prices. Also, there is a lack of skilled workers. These are the challenges that confront many manufacturers, including WTO, a manufacturer of static and driven precision toolholders. The solution appears obvious: a fully automated production hall. Batch production always relies on established methods, but for small quantities, new processes have to be developed and integrated into an overall system. Why? Because clamping devices, for example, have to be changed several times a day, which presents enormous challenges in terms of process and safety. Working together with Hainbuch, the Marbach-based workholding technology manufacturer, WTO has overcome the obstacles by performing a closely coordinated series of measurements and tests. In WTO's new Smart Factory, all processes are automated, with robots inserting the components, changing the clamping devices, and driverless transport systems bringing everything from A to B. Since the end of 2022, production of one of the components of the driven tools has been running autonomously 24/7 in batch sizes from 1 to 100. This is a milestone for WTO and Hainbuch after a 3-year development phase.
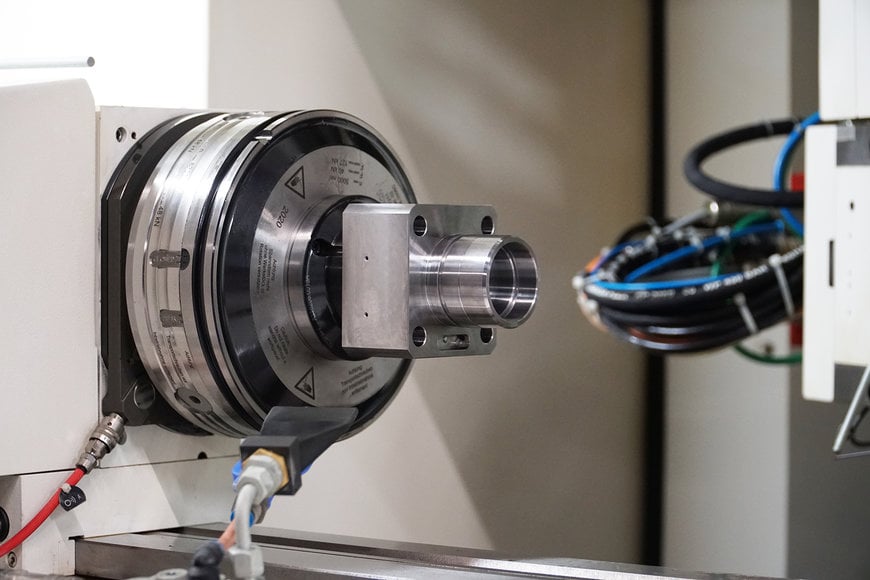
The workpiece is clamped from the inside on a clamping mandrel.
Smart Factory was the only option
WTO is based in Ohlsbach near Offenburg, away from major cities there is a lack of skilled workers. Due to demographic developments, this situation will continue to worsen. In addition, fewer and fewer people want to become machine operators and there is less and less willingness to work in shifts. Sascha Tschiggfrei, managing director of WTO, recognised this and in 2016 began to think about solutions. "Skilled workers are one thing, cost increases are another. Because we operate internationally, the competitive pressure is great. Some companies make the choice to relocate abroad where costs are lower. However, we wanted to keep our location in Germany, so we had to react to ensure our company stays competitive over the long term. Our future lies with the Smart Factory, producing around the clock and operating fully automatically. It gives us a competitive edge and also allows us to attract more highly qualified people", said Tschiggfrei.
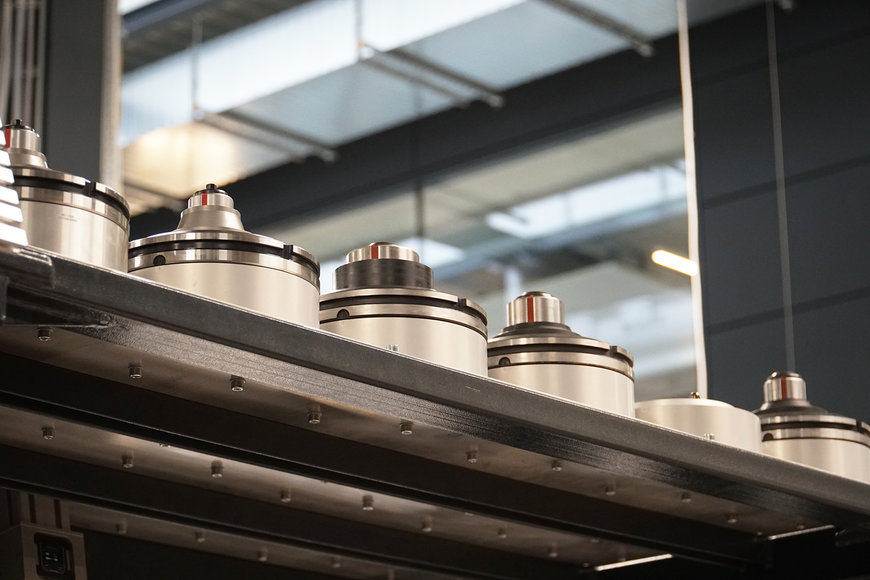
The pre-equipped mandrels are ready for the automated clamping device change-over.
The search for an exclusive partner
For this mammoth project, WTO wanted an exclusive partner for the clamping equipment, with the commitment and expertise to contribute with suitable technology. "We worked out the technical details in project teams. The questions were: How do we clamp the workpieces, how can we automate the clamping, and how can we change the clamping devices automatically? The goal was for the machines to execute change-overs completely autonomously. This requires clamping devices that have this capability. In addition, we have a high precision grinding process, with a maximum 3 µm tolerance range", said Tschiggfrei. Once the Smart Factory concept was in place, the next step was to look for a partner. Since WTO and Hainbuch had already worked successfully together on various international projects, Hainbuch was the partner of choice. At the end of 2019, they began the initial discussions to define the clamping device requirements. The design proposals developed by Hainbuch were accepted.
The start button is pressed
WTO has an existing production hall with over 50 CNC machines. Clamping on these machines is mainly done with jaw chucks, and change-over and alignment for each OP is done manually. The first completely unmanned manufacturing process to be implemented in the Smart Factory was to produce a housing, with soft machining followed by hard machining. Tschiggfrei explained further: "The machines in the Smart Factory are all new. They are standard machines, but they are specifically adapted to allow the automatic change-over of clamping devices using a robot." Hainbuch was to equip four machines with clamping devices. Two turning/milling centres in one cell with I.D. clamping on the counter spindle, and two cylindrical grinding machines in another cell, one with O.D. clamping and one with I.D. clamping. To clamp externally for grinding, Hainbuch already had a standard chuck, the Toplus AC 100 with axial pull-back. For the various housings, there are now 18 clamping sets, consisting of a clamping head with end-stop, which are automatically changed over in the chuck. However, for the I.D. clamping when turning and grinding, a completely new development was required. It was based on the existing Maxxos T211 mandrel, however in this version with safety checks, a specific mandrel was developed.
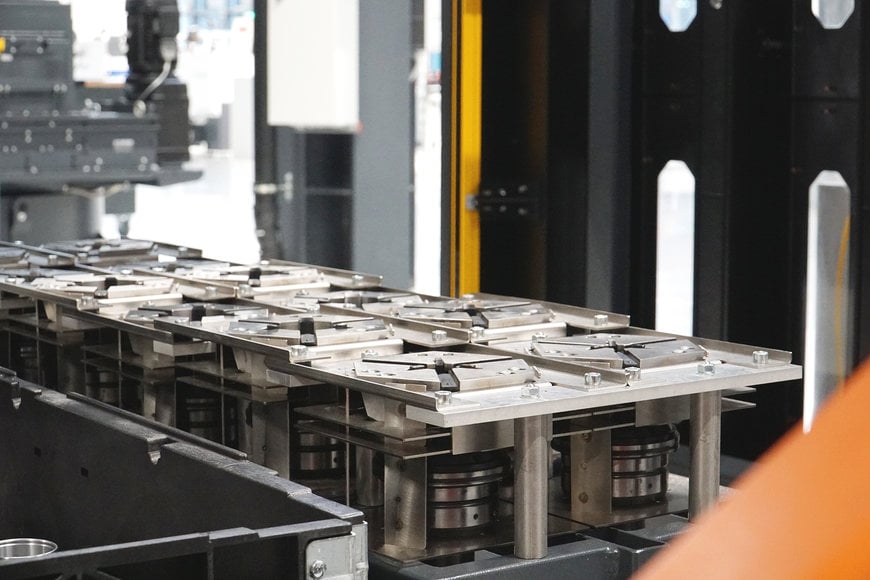
For the production of different housings, 18 clamping sets are available, each consisting of a clamping head with end-stop
Stringent requirements on the clamping devices
For Björn Schiesling, a design engineer in Hainbuch's automation department who has been involved from the beginning, there are fundamental requirements that must be considered in automation. "What is missing from automated workholding change-over? It is the employee who cleans the contact surfaces. Even the smallest dirt particles cause the accuracy to go out of specification. Then, there are the safety checks. Is the spindle allowed to rotate? Is it correctly tensioned? Is it sitting correctly? Can anything come loose? In general, all the things that are normally checked and adjusted by the operator. This is no longer the case with automation. For us, it was a huge challenge to implement these checks in the clamping devices. Of course, we also had to work out with the machine manufacturer how this could be implemented in terms of control technology by monitoring the stroke position. For example: to check by air sensing, I can provide the channels in the clamping device so that air sensing can be implemented. But the machine manufacturer has to fit the air supply and the sensors behind it that communicate with the machine control system. There were many obstacles on the way to the final solution, but we were able to successfully overcome them," says Schiesling.
Safety has priority
For I.D. clamping, Hainbuch also considered changing over the segmented clamping bushings and end stops individually. After evaluating the aspects of safety, accuracy and contamination, and comparing different approaches, it was clear that a safe process could only be achieved with pre-equipped mandrels. Now, the grinding cell and the turning/milling cell each have ten Maxxos mandrels with a centrotex AC quick change-over interface. These are kept in stock for the different housings with the appropriate set-up and are changed over automatically by the robot.
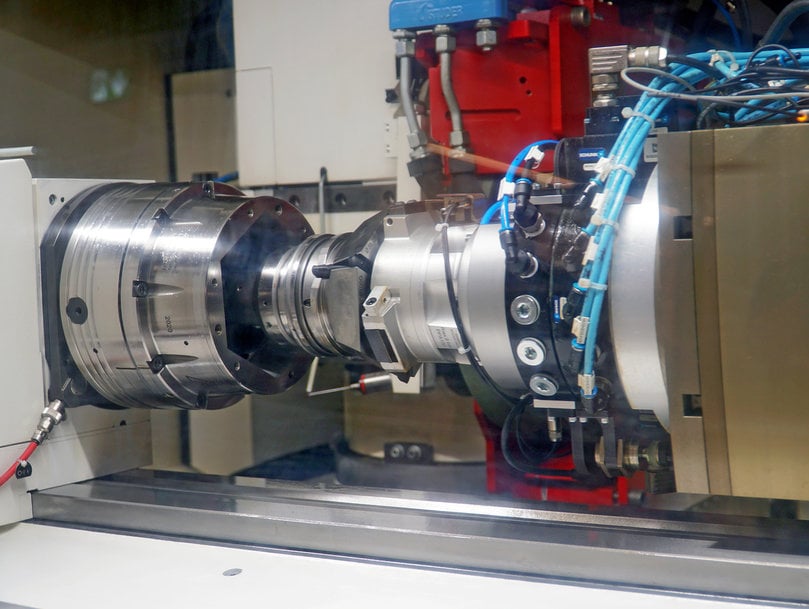
The clamping head with end-stop is automatically inserted into the Toplus AC 100 chuck with axial pull-back.
Hainbuch has more than met the requirements
Philipp Wußler, Grinding Division Manager at WTO, initially had major doubts as to whether everything would work. "Fortunately, these doubts have vanished. The clamping devices meet all the requirements, be it cleanliness, accuracy and what is very important, repeatability. With every mandrel change-over, we are within the required 3 µm," remarks Wußler with satisfaction. The automated manufacturing process has reduced the set-up time by 25 percent compared to the old method, when jaw chucks had to be changed over, aligned by hand and jaws ground for accuracy. "Scrap has also been significantly reduced or is almost zero. This is because clamping used to be less accurate. Now we clamp with axial pull-back on the end stop and it's much more accurate. Once I have run-in the workpiece, I know the next set-up process will work fine. This means I no longer have any clamping device worries", adds Wußler. For WTO it is quite clear: If the clamping is safer, then the process is safer, too.
Employees are now only in the command centre
"The Smart Factory is designed so that the only manual operation is the delivery of the raw material. A driverless transport system even picks up the finished housings, which are inspected and measured in the production cell, and takes them from the machine into storage. The Smart Factory includes a command centre with offices for the planning of the manufacturing processes and the programming. The clamping devices and the definition of the handling parameters for the automation is planned there as well," says Tschiggfrei. Further projects are already planned and Hainbuch will again be supplying the clamping devices and be involved in the start-up process. Tschiggfrei says in conclusion: "We are very satisfied. We wanted a partner to carry out this development project together with us. Hainbuch put everything into reaching the very last "µm". Mr. Schiesling and Mr. Wußler were passionately committed to the project. It takes people like that to successfully implement something like this. From my point of view, the outcome has been even better than expected.”
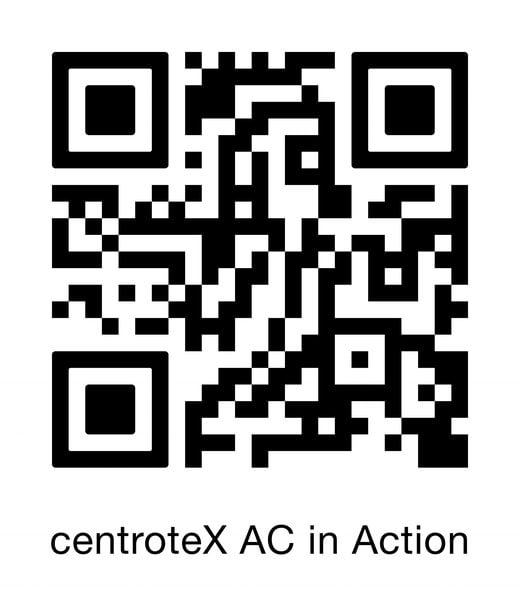
centroteX AC in action at HAINBUCH and further product information
User: WTO Werkzeug-Einrichtungen GmbH
WTO is a second-generation family business with 280 employees located in Ohlsbach and is celebrating its 40th anniversary this year. WTO is a pioneer in the development and manufacture of driven precision toolholders for CNC turning centres. With the Smart Factory, in which WTO invested 40 million euros, they are setting standards in the digitalization and automation of low-volume manufacturing. The new 14,000 m² building consists of 9,000 m² for the Smart Factory and a 5,000 m² office complex. The Smart Factory is also designed for sustainability and relies on renewable energy. It has a photovoltaic system and the process waste heat is used for heating. This accounts for a saving of almost 1,000 tons of CO2 per year.
For years, production costs have been heading in only one direction steeply upward, while the demand is for ever lower manufacturing prices. Also, there is a lack of skilled workers. These are the challenges that confront many manufacturers, including WTO, a manufacturer of static and driven precision toolholders. The solution appears obvious: a fully automated production hall. Batch production always relies on established methods, but for small quantities, new processes have to be developed and integrated into an overall system. Why? Because clamping devices, for example, have to be changed several times a day, which presents enormous challenges in terms of process and safety. Working together with Hainbuch, the Marbach-based workholding technology manufacturer, WTO has overcome the obstacles by performing a closely coordinated series of measurements and tests. In WTO's new Smart Factory, all processes are automated, with robots inserting the components, changing the clamping devices, and driverless transport systems bringing everything from A to B. Since the end of 2022, production of one of the components of the driven tools has been running autonomously 24/7 in batch sizes from 1 to 100. This is a milestone for WTO and Hainbuch after a 3-year development phase.
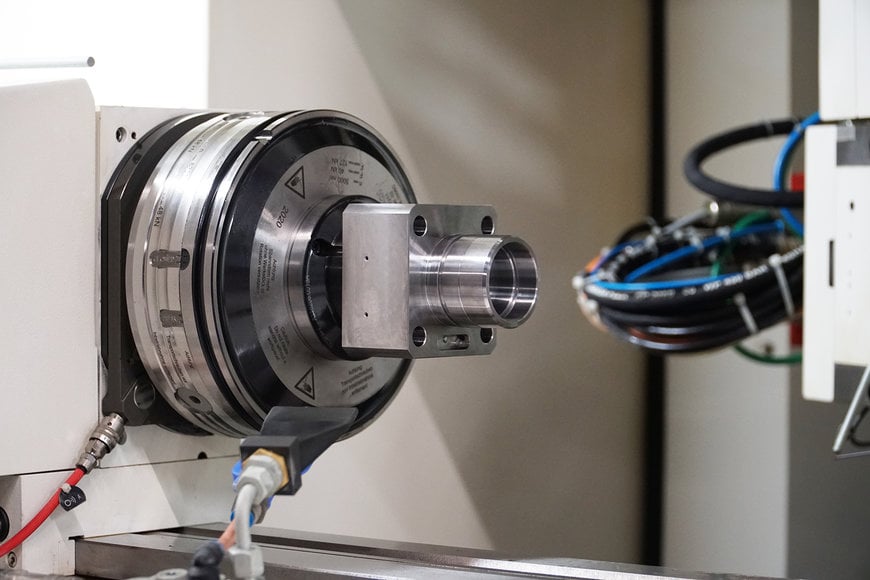
The workpiece is clamped from the inside on a clamping mandrel.
Smart Factory was the only option
WTO is based in Ohlsbach near Offenburg, away from major cities there is a lack of skilled workers. Due to demographic developments, this situation will continue to worsen. In addition, fewer and fewer people want to become machine operators and there is less and less willingness to work in shifts. Sascha Tschiggfrei, managing director of WTO, recognised this and in 2016 began to think about solutions. "Skilled workers are one thing, cost increases are another. Because we operate internationally, the competitive pressure is great. Some companies make the choice to relocate abroad where costs are lower. However, we wanted to keep our location in Germany, so we had to react to ensure our company stays competitive over the long term. Our future lies with the Smart Factory, producing around the clock and operating fully automatically. It gives us a competitive edge and also allows us to attract more highly qualified people", said Tschiggfrei.
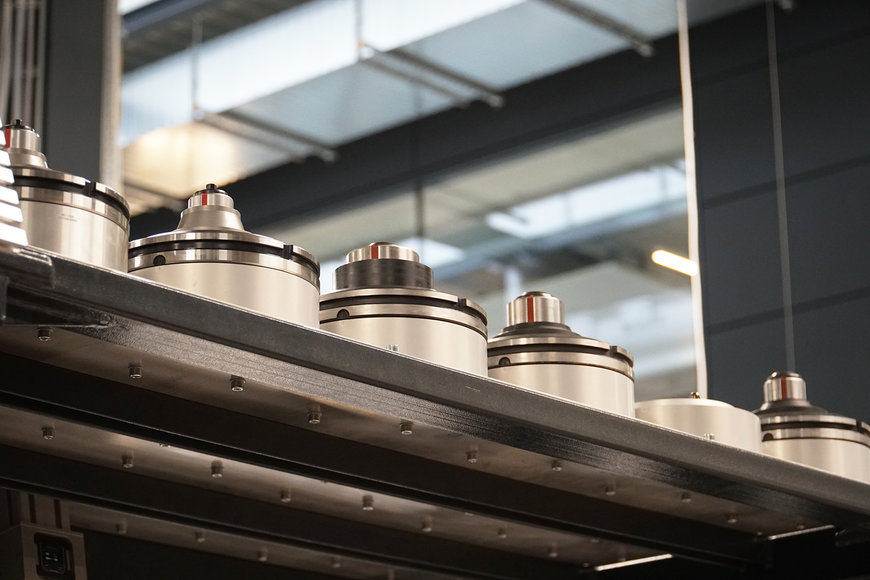
The pre-equipped mandrels are ready for the automated clamping device change-over.
The search for an exclusive partner
For this mammoth project, WTO wanted an exclusive partner for the clamping equipment, with the commitment and expertise to contribute with suitable technology. "We worked out the technical details in project teams. The questions were: How do we clamp the workpieces, how can we automate the clamping, and how can we change the clamping devices automatically? The goal was for the machines to execute change-overs completely autonomously. This requires clamping devices that have this capability. In addition, we have a high precision grinding process, with a maximum 3 µm tolerance range", said Tschiggfrei. Once the Smart Factory concept was in place, the next step was to look for a partner. Since WTO and Hainbuch had already worked successfully together on various international projects, Hainbuch was the partner of choice. At the end of 2019, they began the initial discussions to define the clamping device requirements. The design proposals developed by Hainbuch were accepted.
The start button is pressed
WTO has an existing production hall with over 50 CNC machines. Clamping on these machines is mainly done with jaw chucks, and change-over and alignment for each OP is done manually. The first completely unmanned manufacturing process to be implemented in the Smart Factory was to produce a housing, with soft machining followed by hard machining. Tschiggfrei explained further: "The machines in the Smart Factory are all new. They are standard machines, but they are specifically adapted to allow the automatic change-over of clamping devices using a robot." Hainbuch was to equip four machines with clamping devices. Two turning/milling centres in one cell with I.D. clamping on the counter spindle, and two cylindrical grinding machines in another cell, one with O.D. clamping and one with I.D. clamping. To clamp externally for grinding, Hainbuch already had a standard chuck, the Toplus AC 100 with axial pull-back. For the various housings, there are now 18 clamping sets, consisting of a clamping head with end-stop, which are automatically changed over in the chuck. However, for the I.D. clamping when turning and grinding, a completely new development was required. It was based on the existing Maxxos T211 mandrel, however in this version with safety checks, a specific mandrel was developed.
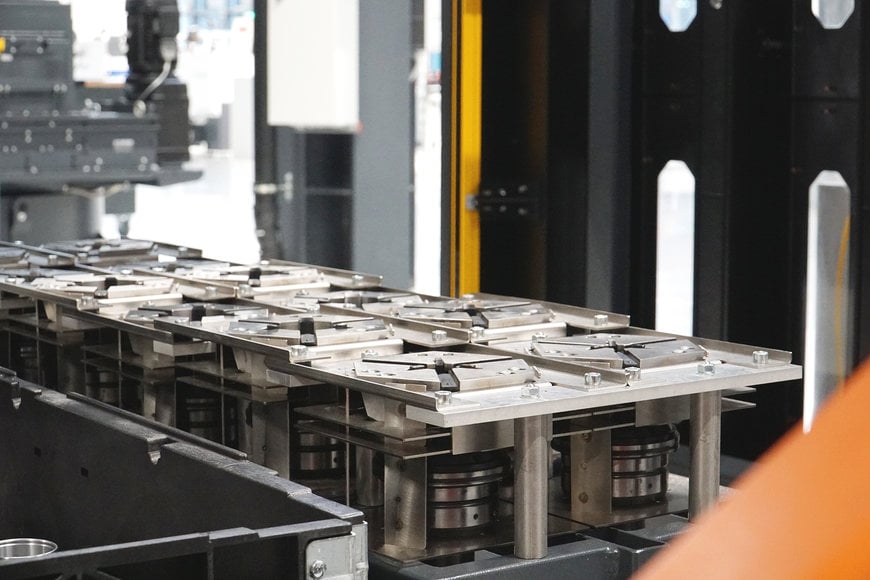
For the production of different housings, 18 clamping sets are available, each consisting of a clamping head with end-stop
Stringent requirements on the clamping devices
For Björn Schiesling, a design engineer in Hainbuch's automation department who has been involved from the beginning, there are fundamental requirements that must be considered in automation. "What is missing from automated workholding change-over? It is the employee who cleans the contact surfaces. Even the smallest dirt particles cause the accuracy to go out of specification. Then, there are the safety checks. Is the spindle allowed to rotate? Is it correctly tensioned? Is it sitting correctly? Can anything come loose? In general, all the things that are normally checked and adjusted by the operator. This is no longer the case with automation. For us, it was a huge challenge to implement these checks in the clamping devices. Of course, we also had to work out with the machine manufacturer how this could be implemented in terms of control technology by monitoring the stroke position. For example: to check by air sensing, I can provide the channels in the clamping device so that air sensing can be implemented. But the machine manufacturer has to fit the air supply and the sensors behind it that communicate with the machine control system. There were many obstacles on the way to the final solution, but we were able to successfully overcome them," says Schiesling.
Safety has priority
For I.D. clamping, Hainbuch also considered changing over the segmented clamping bushings and end stops individually. After evaluating the aspects of safety, accuracy and contamination, and comparing different approaches, it was clear that a safe process could only be achieved with pre-equipped mandrels. Now, the grinding cell and the turning/milling cell each have ten Maxxos mandrels with a centrotex AC quick change-over interface. These are kept in stock for the different housings with the appropriate set-up and are changed over automatically by the robot.
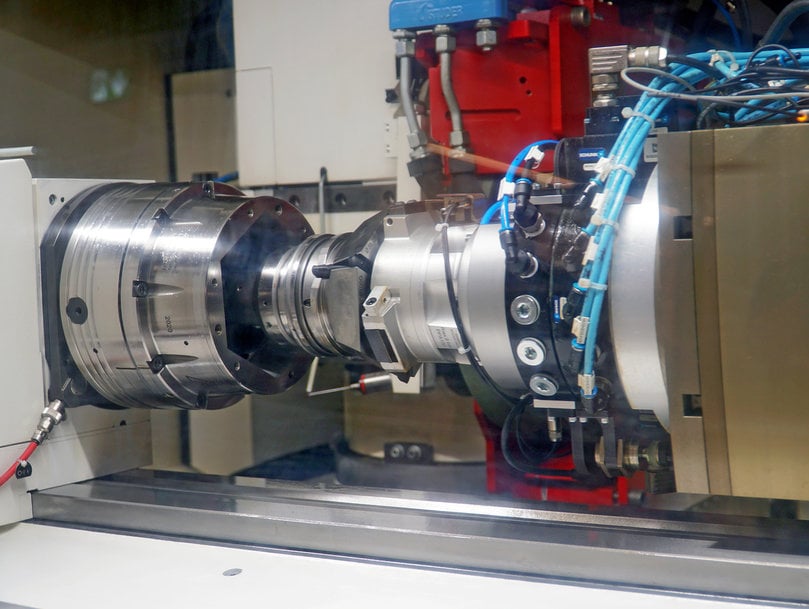
The clamping head with end-stop is automatically inserted into the Toplus AC 100 chuck with axial pull-back.
Hainbuch has more than met the requirements
Philipp Wußler, Grinding Division Manager at WTO, initially had major doubts as to whether everything would work. "Fortunately, these doubts have vanished. The clamping devices meet all the requirements, be it cleanliness, accuracy and what is very important, repeatability. With every mandrel change-over, we are within the required 3 µm," remarks Wußler with satisfaction. The automated manufacturing process has reduced the set-up time by 25 percent compared to the old method, when jaw chucks had to be changed over, aligned by hand and jaws ground for accuracy. "Scrap has also been significantly reduced or is almost zero. This is because clamping used to be less accurate. Now we clamp with axial pull-back on the end stop and it's much more accurate. Once I have run-in the workpiece, I know the next set-up process will work fine. This means I no longer have any clamping device worries", adds Wußler. For WTO it is quite clear: If the clamping is safer, then the process is safer, too.
Employees are now only in the command centre
"The Smart Factory is designed so that the only manual operation is the delivery of the raw material. A driverless transport system even picks up the finished housings, which are inspected and measured in the production cell, and takes them from the machine into storage. The Smart Factory includes a command centre with offices for the planning of the manufacturing processes and the programming. The clamping devices and the definition of the handling parameters for the automation is planned there as well," says Tschiggfrei. Further projects are already planned and Hainbuch will again be supplying the clamping devices and be involved in the start-up process. Tschiggfrei says in conclusion: "We are very satisfied. We wanted a partner to carry out this development project together with us. Hainbuch put everything into reaching the very last "µm". Mr. Schiesling and Mr. Wußler were passionately committed to the project. It takes people like that to successfully implement something like this. From my point of view, the outcome has been even better than expected.”
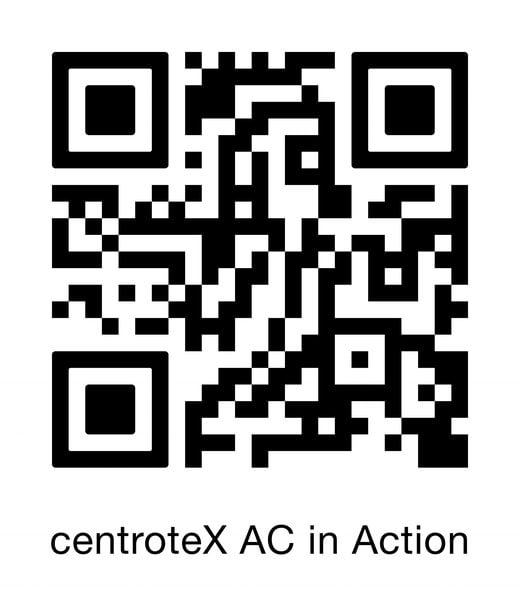
centroteX AC in action at HAINBUCH and further product information
User: WTO Werkzeug-Einrichtungen GmbH
WTO is a second-generation family business with 280 employees located in Ohlsbach and is celebrating its 40th anniversary this year. WTO is a pioneer in the development and manufacture of driven precision toolholders for CNC turning centres. With the Smart Factory, in which WTO invested 40 million euros, they are setting standards in the digitalization and automation of low-volume manufacturing. The new 14,000 m² building consists of 9,000 m² for the Smart Factory and a 5,000 m² office complex. The Smart Factory is also designed for sustainability and relies on renewable energy. It has a photovoltaic system and the process waste heat is used for heating. This accounts for a saving of almost 1,000 tons of CO2 per year.