www.industryemea.com
06
'24
Written on
Modified on
Fraunhofer News
New system revolutionizes production of bipolar plates
The Fraunhofer Institute for Machine Tools and Forming Technology IWU has now taken a major step toward lower costs and mass production of bipolar plates by introducing an innovative sys-tem for roll embossing: BPPflexRoll.
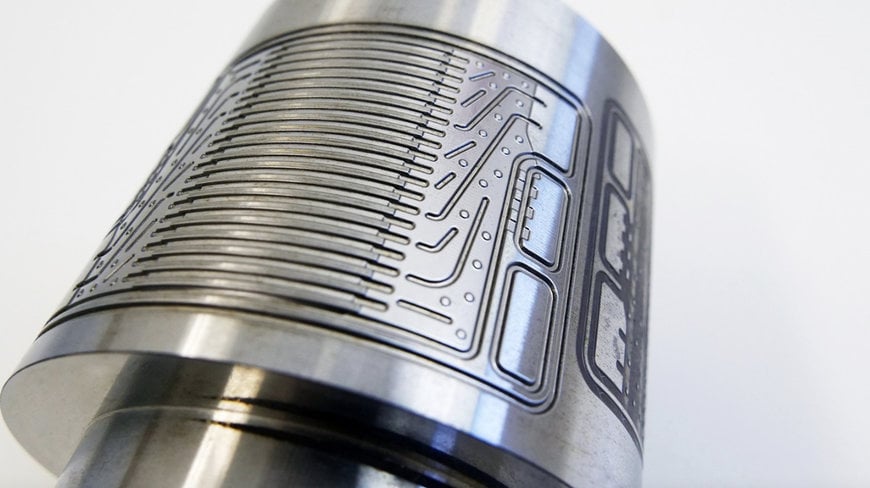
Hydrogen fuel cells are highly efficient. They use hydrogen and oxygen to produce electricity, powering machines such as ecofriendly vehicles. Electrolyzers reverse this process by using electrical energy to split water into hydrogen and oxygen. Both types of hydrogen systems require bipolar plates (BPPs), which include two key conversion components: the membrane electrode assembly (MEA), in a fuel cell system, and the catalyst coated membrane (CCM), in an electrolyzer. In a fuel cell stack, the double-walled structure of the bipolar plates allows oxygen and hydrogen to flow to both sides of the MEA while water cools the stack. The problem is that the current process of producing bipolar plates is expensive, which prevents the application of hydrogen technology and thus, for example, the widespread and cost-efficient use of hydrogen-powered fuel cell vehicles. This potential can only be unleashed if the cost of mass production of the core components involved is lowered. Researchers at Fraunhofer IWU in Chemnitz, in partnership with Profiroll Technologies GmbH, have now developed a prototype system for roll embossing: BPPflexRoll. The production line is up and running at Fraunhofer IWU. It is already equipped with control technology and an operating concept that align with an industrial facility on key points. The system consists of three roll stands and requires an installation footprint of 4,500 mm x 3,300 mm.
Continuous processing replaces discontinuous batch production
One of the reasons that metallic BPPs are so expensive is that they are produced in discontinuous batches. “Each bipolar plate consists of two stainless steel halves. Structures for the gas flow and heat dissipation are embossed onto the halves in a discontinuous forming process, and then they are joined together. Our roll embossing system has the potential to replace these discontinuous process chains or production steps with a continuous process. With no stops and starts, this process will allow for high unit volume output,” explains Stefan Polster, head of the Sheet Metal Processing and Tool Design group at Fraunhofer IWU. “One major advantage of roll embossing is the higher process speeds involved. As many as 120 BPP half plates can be produced every minute,” notes Robin Kurth, group manager for forming machines at Fraunhofer IWU. The researchers hope that this shift in production methods will cut the costs of manufacturing BPPs in half.
In the newly developed technology, the structure of the bipolar plate is embossed using a pair of rollers, with the wafer-thin metal band running continuously between them. One of the forming rollers is defined as the punch, the other as the die. Since the rollers used to form the flow channels have approximately only one line contact with the workpiece, the step-by-step forming can reduce the process forces by a factor of ten on average compared to conventional embossing. That results in smaller, lower-cost machine technology. Flexibility is another of the system’s advantages: The number of roller sets required can be adjusted individually, depending on the geometry of the bipolar plates.
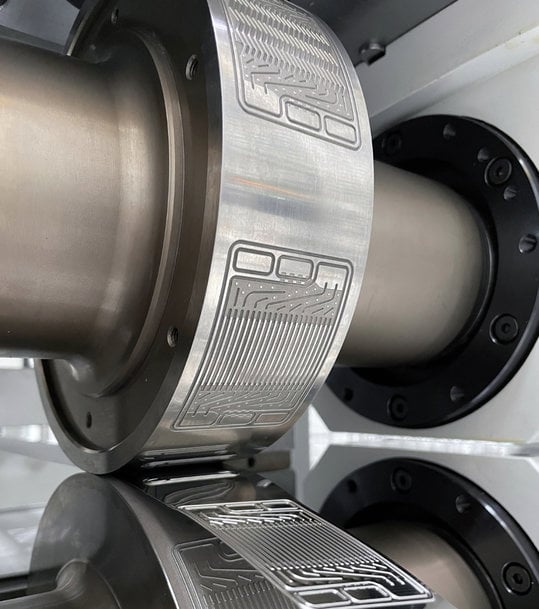
Roll embossing of bipolar plates using BPPflexRoll. In the newly developed technology, the structure of the bipolar plate is embossed by a pair of rollers.
Cognitive forming machine with integrated monitoring system
With the new pilot system, the researchers at Fraunhofer IWU are also taking an important step towards cognitive forming machines, which can use sensors and smart algorithms to monitor and control themselves. “Unlike previous systems, we will in the future monitor the quality of the BPP in real-time by capturing, consolidating, and analyzing the process parameters with sensors,” Kurth says. The data will then be processed and made usable via cloud solutions. The first bipolar plates produced with the facility are already being tested in fuel cells at the Fraunhofer Institute for Solar Energy Systems ISE in Freiburg.
With BPPflexRoll, the researchers are paving the way for mass production of high-efficiency, low-cost bipolar plates. At the Hannover Messe, from April 22 to 26 at the Fraunhofer joint stand in Hall 2, Stand B24, they will present a roll as a component of BPPflexRoll, plus bipolar plates manufactured with it.
www.fraunhofer.com