www.industryemea.com
12
'24
Written on Modified on
BATTERY MANUFACTURING: THE EMERGING GLOBAL SCENARIO
When it comes to electric mobility and green energy, the world has enough battery capacity, says Milton D’Silva.
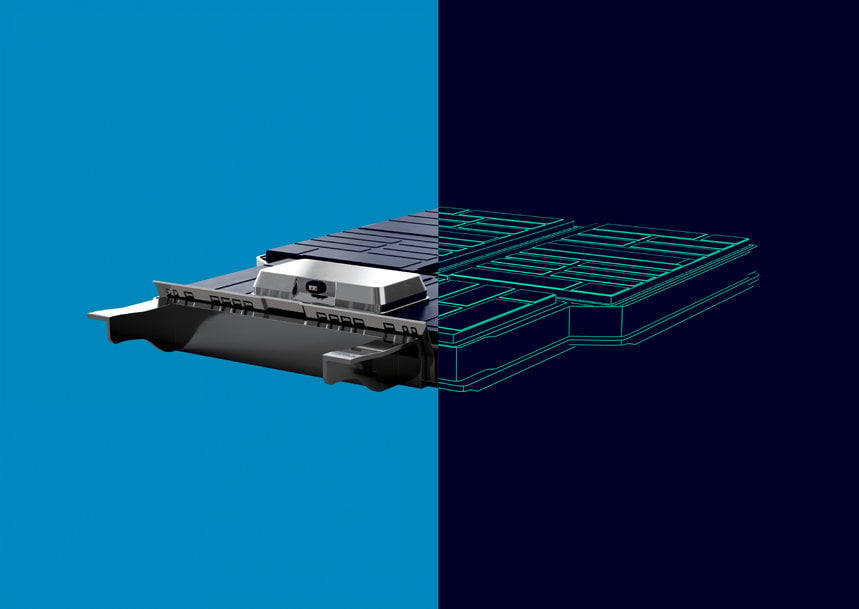
Siemens recently joined the Global Battery Alliance to accelerate development of the sustainable battery industry. Image source: Siemens Press
The global battery manufacturing scenario is complex and rapidly evolving, thanks to the gradual shift towards electrical mobility on one hand, and decarbonisation of electricity on the other. Consequently, the demand for batteries – the secondary, rechargeable type – is increasing. Though there are many different types of batteries, when it comes to electric vehicles (EV) or battery energy storage systems (BESS), the preferred type is the lithium-ion (Li-ion) battery, widely considered to be the most energy efficient. The Li-ion battery boasts a round trip efficiency of over 80%, which means the loss of energy is just about 20% or less. During charging, Li-ion batteries reach almost 100% capacity, which in case of conventional lead-acid batteries peaks at 85%.
There are two broad types of Li-ion batteries based on the chemistries used – Lithium Iron Phosphate (LFP) and Nickel Manganese Cobalt (NMC). The LFP is known for higher safety and is hence more commonly used, while NMC is the choice for higher energy density requirements.
With the rapid scaling up of the EV ecosystem globally – estimates suggest over 18% of new cars sold globally are EVs – the demand for batteries is increasing; and hence the urgency to scale up battery manufacturing capacities. A 2019 McKinsey study had projected a market size of 2.6 TWh and yearly growth of 25 percent by 2030. However, a more recent, 2023 study by the same firm predicts that the Li-ion battery chain, from mining through recycling, could grow by over 30 percent annually from 2022 to 2030 to reach a value of more than $400 billion and a market size of 4.7 TWh.
According to the Global Battery Alliance (GBA), batteries will be a major driver in reducing the carbon footprint of the transport and power sectors through the use of electric vehicles and renewable energy. The GBA is a public-private collaboration platform founded in 2017 at the World Economic Forum to help establish a sustainable battery value chain. It brings together 170 leading international organisations, NGOs, industry actors, academics and multiple governments in order to drive systemic change along the entire value chain. In order to help companies and governments, the GBA in 2020 designed 10 guiding principles for the creation of a sustainable battery chain by 2030. The 10 principles are clubbed under three broad guidelines:
The global battery manufacturing scenario is complex and rapidly evolving, thanks to the gradual shift towards electrical mobility on one hand, and decarbonisation of electricity on the other. Consequently, the demand for batteries – the secondary, rechargeable type – is increasing. Though there are many different types of batteries, when it comes to electric vehicles (EV) or battery energy storage systems (BESS), the preferred type is the lithium-ion (Li-ion) battery, widely considered to be the most energy efficient. The Li-ion battery boasts a round trip efficiency of over 80%, which means the loss of energy is just about 20% or less. During charging, Li-ion batteries reach almost 100% capacity, which in case of conventional lead-acid batteries peaks at 85%.
There are two broad types of Li-ion batteries based on the chemistries used – Lithium Iron Phosphate (LFP) and Nickel Manganese Cobalt (NMC). The LFP is known for higher safety and is hence more commonly used, while NMC is the choice for higher energy density requirements.
With the rapid scaling up of the EV ecosystem globally – estimates suggest over 18% of new cars sold globally are EVs – the demand for batteries is increasing; and hence the urgency to scale up battery manufacturing capacities. A 2019 McKinsey study had projected a market size of 2.6 TWh and yearly growth of 25 percent by 2030. However, a more recent, 2023 study by the same firm predicts that the Li-ion battery chain, from mining through recycling, could grow by over 30 percent annually from 2022 to 2030 to reach a value of more than $400 billion and a market size of 4.7 TWh.
According to the Global Battery Alliance (GBA), batteries will be a major driver in reducing the carbon footprint of the transport and power sectors through the use of electric vehicles and renewable energy. The GBA is a public-private collaboration platform founded in 2017 at the World Economic Forum to help establish a sustainable battery value chain. It brings together 170 leading international organisations, NGOs, industry actors, academics and multiple governments in order to drive systemic change along the entire value chain. In order to help companies and governments, the GBA in 2020 designed 10 guiding principles for the creation of a sustainable battery chain by 2030. The 10 principles are clubbed under three broad guidelines:
- Establish a circular battery value chain as a major driver to achieve the Paris Agreement
- Establish a low carbon economy in the value chain, create new jobs and additional economic value, and
- Safeguard human rights and economic development consistent with the UN Sustainable Development Goals.
Against this backdrop, it would be interesting to examine the current status of battery manufacturing in the three main regional markets of the world – the United States, Europe and Asia.
Before proceeding to do that, a brief look at the battery manufacturing ecosystem could help.
The battery manufacturing ecosystem
Manufacturing high energy, high capacity batteries is like solving a jigsaw puzzle – every piece must fall in a precise place to make the whole. The end product is the result of assembling many different parts made from a variety of raw materials chosen carefully to provide the optimum result.
The process of battery manufacturing involves several steps and requirements, which is roughly divided in three phases:
Before proceeding to do that, a brief look at the battery manufacturing ecosystem could help.
The battery manufacturing ecosystem
Manufacturing high energy, high capacity batteries is like solving a jigsaw puzzle – every piece must fall in a precise place to make the whole. The end product is the result of assembling many different parts made from a variety of raw materials chosen carefully to provide the optimum result.
The process of battery manufacturing involves several steps and requirements, which is roughly divided in three phases:
- Upstream – Raw Materials: The process begins with mining raw materials such as lithium, cobalt, manganese, nickel, and graphite. These are minerals extracted by countries that have large deposits, e.g., Africa, Australia and South America.
- Midstream – Processing: The raw materials are then refined and purified into cathode and anode active battery materials. Most of the processing is done in Asian countries presently, mainly in China.
- Downstream – Assembly: The battery cells are assembled into modules, the modules assembled into packs, and packs into batteries ready for use in EVs or for energy storage.
Some challenges to manufacturing EV batteries include:
- Supply chain constraints – The need for specific materials, tight tolerances, and high volumes can make it difficult to manage the supply chain.
- Manufacturing complexities – The complexity of the components can make it difficult to maintain consistent quality, efficiency, and reliability.
- Technological advancements – Standard production processes may still be in development or optimisation stages.
Not all battery manufacturing plants globally are vertically integrated to undertake all these operations at one site. In fact many plants are simply doing the assembly by sourcing processed materials from China and other Asian countries.
The US battery landscape
Globally, China, Europe and the US are the three biggest automobile markets that account for 60% of all passenger cars. According to the statistics compiled by the World Resources Institute, China is leading EV adoption at double the rate of the global average. While Europe is a little above the global average when it comes to preference for EVs, the US is lagging behind. A JD Power survey terms the US situation as the ‘Divided States of EV Adoption’ with reference to the wide difference between the top 10 states and bottom 10 states of USA. While EV sales in the top states are growing steadily, those in the bottom 10 are actually declining. According to a BBC report, the low adoption is mainly due to three factors that may be termed as the ‘ABC of low adoption’ – Affordability, Battery charging infrastructure, and Choice of suitable model or the lack of it. Americans traditionally have preferred large muscular cars and SUVs and also suffer from the phenomenon of ‘range anxiety’. This is the fear of the EV running out of charge even when the distance an average car covers in a day is much less than what a fully charged EV can cover. Regardless of these factors, analysts believe that EV sales in the US, as elsewhere, would increase, albeit slowly, in what is one of the largest automobile markets globally.
While it is difficult to pinpoint exactly when did the US start manufacturing EV batteries on scale, until 2019 it had only two battery manufacturing plants. Available information suggests it was Ford Motors that was engaged in manufacturing mid-to-large size battery packs for EVs in the late 1990s. These were either lead-acid batteries or nickel-metal hydride batteries (NiMH) developed for the Ford Ranger EV, a compact pickup truck. This was the first all-electric production vehicle Ford built in 1998 and was in production just for 4 years, until 2002. General Motors released its Chevy Bolt plug-in Hybrid in 2010 using batteries developed with technology from the US Department of Energy. Between these two developments, Tesla – the company formed in 2003, launched its first car, the Roadster Sports in 2008. It was the first street legal EV in the US to use a lithium-ion battery pack, assembled from cylindrical cells manufactured by Panasonic Corporation of Japan. In 2014, Panasonic, thanks to its association with Tesla, was the first to announce a large-scale battery manufacturing plant for lithium-ion batteries, at the Tesla Gigafactory at Nevada. The real impetus for domestic battery manufacturing in the US was however provided by the supply chain crisis during Covid. Automakers then realised how dependent they were on China for building their EVs and equipping them with the appropriate battery packs.
In May 2021, Ford and SK Innovation of South Korea signed a MoU to create a joint venture to produce approximately 60 GWh annually in traction battery cells and array modules, with potential for further expansion. A year later, in May 2022, Hyundai Motor Group announced it has entered into an agreement with the State of Georgia to build its first dedicated all-electric vehicle and battery manufacturing facilities in the US. Already a significant player in the North American EV market, the Hyundai Group aims to become one of the top three EV manufacturers by 2026. Thus began the gradual movement in the US for onshoring the EV supply chain, including the batteries. These early efforts received a massive boost when the Inflation Reduction Act (IRA) was signed into law in August 2022, which opened the doors further for more investments to follow. According to Benchmark Mineral Intelligence, a market intelligence publisher for the lithium ion battery to electric vehicle (EV) supply chain, the IRA has led to over $110 billion of capital investments announced for clean energy manufacturing projects, including over $70 billion towards EV and battery supply chains across the US.
In October 2022, Our Next Energy (ONE), a battery startup, announced plans to build a gigafactory in Michigan devoted to LFP cells. The scope of the plant, supported by a $200 million grant from the state of Michigan, includes raw material refinement, cathode materials production, and cell and battery manufacturing.
In November 2022, Norwegian company FREYR Battery, a developer of clean, next-generation battery cell production capacity, announced Coweta County in Georgia as the site for its Giga America battery plant. The initial phase of Giga America is planned to be a cell production module of approximately 34 GWh based on the SemiSolid™ technology of FREYR’s US-based licensing partner, 24M at an initial projected capital cost of $1.7 billion, with more investments in the pipeline. Upon completion of all the contemplated construction phases, the Giga America complex is expected to be one of the largest battery cell manufacturing developments globally.
In June 2023, 6K Energy, a division of 6K and leader in the sustainable production of critical materials for lithium-ion batteries, broke ground in Jackson, Tennessee for the construction of the world’s first sustainable multi-chemistry cathode manufacturing plant scheduled to open in Q3, 2024. “Our PlusCAM facility is the world’s most sustainable process that fulfills the need for domestically sourced low-cost battery material for our nation’s critical infrastructure, grid storage, and electric vehicles,” said 6K Energy President Sam Trinch.
In September 2023, Swedish producer of lithium-ion batteries, Northvolt, announced plans to open its first gigafactory in North America, thanks to the incentives promised by the IRA. The estimated project cost of over $7 billion will be split between Northvolt ($3 billion) with local and federal governments contributing around $4 billion.
Also in September 2023, three companies – Accelera, the zero-emissions business unit of Cummins Inc; Daimler Trucks & Buses US Holding LLC; and PACCAR – announced they are partnering to accelerate and localise battery cell production and the battery supply chain in the US. The planned joint venture, Amplify Cell Technologies, will manufacture battery cells for electric commercial vehicles and industrial applications at the Marshall County site in Mississippi, creating highly desirable US manufacturing jobs in the growing clean technology sector. Total investment is expected to be in the range of $2-3 billion for the 21-gigawatt hour (GWh) factory.
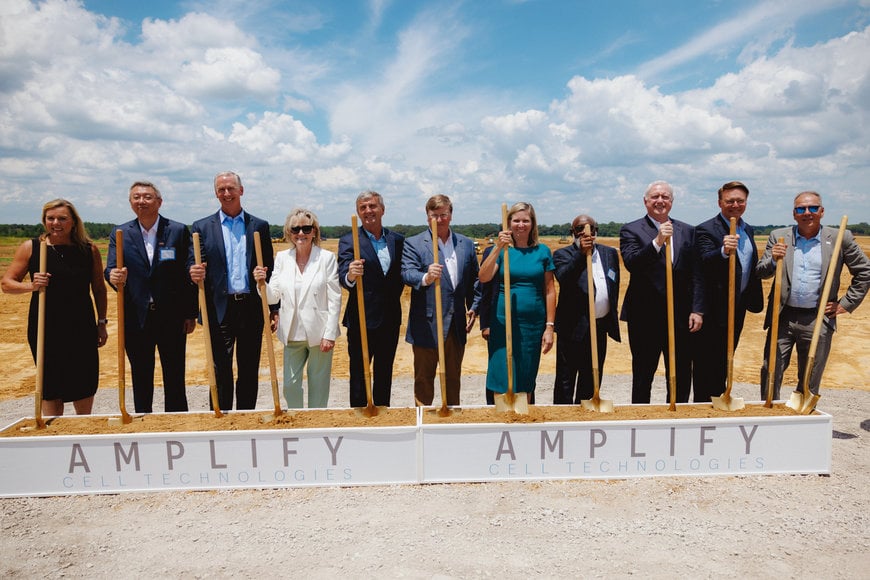
The shovel ceremony – groundbreaking at Amplify Cell Technologies’ Marshall County site in Mississippi. Image source: Amplify
According to figures presented by Statista Research Department in June 2024, the capacity of the battery manufacturing industry in the United States in 2022 amounted to 90 gigawatt-hours, and increased to 114 gigawatt-hours in 2023. This is estimated to grow five-fold between 2023 and 2030, reaching almost one terawatt-hour of battery manufacturing capacity that year.
The scenario in Europe
In Europe, the Directorate-General for Climate Action (DG CLIMA) leads the European Commission's efforts to fight climate change domestically and at international level. The organisation believes that transport is responsible for one-quarter of all greenhouse gas emissions in the EU, and road transport makes up 70% of that amount, primarily from petrol and diesel cars. As a result, in order to cut emissions, the EU in 2023 adopted a law to make all new cars and vans sold in Europe zero-emission from 2035. Europe, as mentioned earlier in this article, is a little above the global average in EV adoption and this move will further accelerate the growth of EVs in the continent. In fact Norway boasts the highest EV adoption rate in the world, with 82% of new car sales registered in 2003 being EVs. This rapid electrification of mobility in Europe also calls for a massive expansion of battery manufacturing capacities.
Fortunately, the European Commission had launched the European Battery Alliance in October 2017, anticipating the trends and movement towards clean mobility. With an estimated annual market value of €250 billion from 2025, the European Commission had realised the imperative for a clean energy transition and a competitive industry with a complete domestic battery value chain.
Samsung SDI is one of the earliest foreign companies to manufacture batteries in Europe and the first one in Hungary. The company which was founded in South Korea in 1970 to manufacture vacuum tubes for B&W TVs owned a cathode ray tube factory at Göd in Hungary which it decided to turn into a battery manufacturing plant in 2016. After its inauguration in 2017, Samsung SDI added a second plant in 2019 at the same location, and by early 2022 had a total production of 40 GWh/year. The company manufactures prismatic battery cells in Hungary that are used by several EV manufacturers like BMW, Volkswagen and Stellantis. It is now in the process of setting up a third plant, reportedly for cylindrical cells that could be supplied to BMW and/or Hyundai according to informed sources.
Another Korean company, LG Electronics, formed LG Energy Solution Wrocław in Poland in 2016. Today it has become Europe's largest and the world's leading producer of lithium-ion batteries for the automotive industry. Based in Biskupice Podgórne, Poland, the plant covers an area of about 100 ha, with tens of modern production lines. LG Energy Solution Wrocław manufactures all battery elements up to the product ready for installation in a car, in the process making Poland the European leader in the industry. With a current capacity of 86 GWh, the batteries produced in this facility are used in EVs of such automotive giants as Audi, BMW, Fiat, Ford, Porsche and Volkswagen.
In 2021, Northvolt AB, a Swedish battery manufacturer, commissioned its first gigafactory, Northvolt Ett, in Skellefteå, Sweden. Northvolt Ett – a lithium-ion battery gigafactory – is touted as Europe’s first homegrown response to explore opportunities and fulfill needs of an electric world. The project was financed by the European Investment Bank (EIB) and supported by the European Fund for Strategic Investments (EFSI). In early 2024, the EIB announced further lending to the Northvolt gigafactory for further expansion, which is expected to increase the annual output capacity for battery production to up to 60 GWh. According to the EIB, the deal is the largest green loan raised in Europe to date and will facilitate the creation of a fully integrated circular battery production facility that has not previously existed outside Asia.
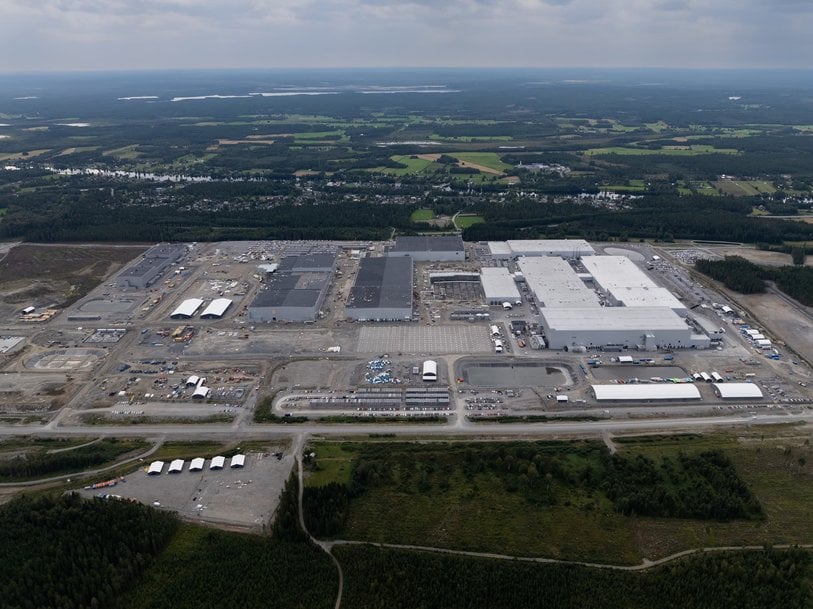
Northvolt Ett – a lithium-ion battery gigafactory in Skellefteå, Sweden. Image source: Northvolt
In April 2023, ElevenEs, the pioneer in LFP cathode battery technology, announced the opening of the first industrial facility dedicated to LFP battery cell production in Europe. ElevenEs, backed by EIT InnoEnergy, is leading battery innovation in Europe with its new production site, located in Subotica, Serbia. The company specialises in producing high-quality LFP prismatic cells for use across a variety of applications, including electric cars, buses, trucks, and energy storage systems. The industrial facility will expand to become the company's Mega-Factory by late 2024, producing 500MWh. ElevenEs's roadmap over the next five years includes operating two Gigafactories at a combined capacity of 48GWh – equivalent to the energy needed for one million electric cars annually.
In mid-August 2024, Norwegian battery startup Morrow Batteries opened its first battery cell production site in southern Norway, with deliveries expected to begin by the end of the year. "This is a hugely important day in Norwegian industrial history and a testament to the bold vision and risk-taking spirit of our founders and the dedication of our diverse team of Morrowers, now consisting of 200 individuals from 34 nationalities,” said Lars Christian Bacher, CEO of Morrow Batteries. Founded in 2020, Morrow is fully European owned, the owners include Siemens, ABB, the Danish pension fund PKA, the Norwegian state’s climate investment company Nysnø Climate Investments, Norwegian environmental company Noah AS, and the Norwegian renewable energy company Å Energy. The first European GWh manufacturer of prismatic LFP batteries, Morrow claims its products offer top-tier safety features, extended cycle life and a low carbon footprint. The company plans to produce 43-gigawatt hours annually from 2028.
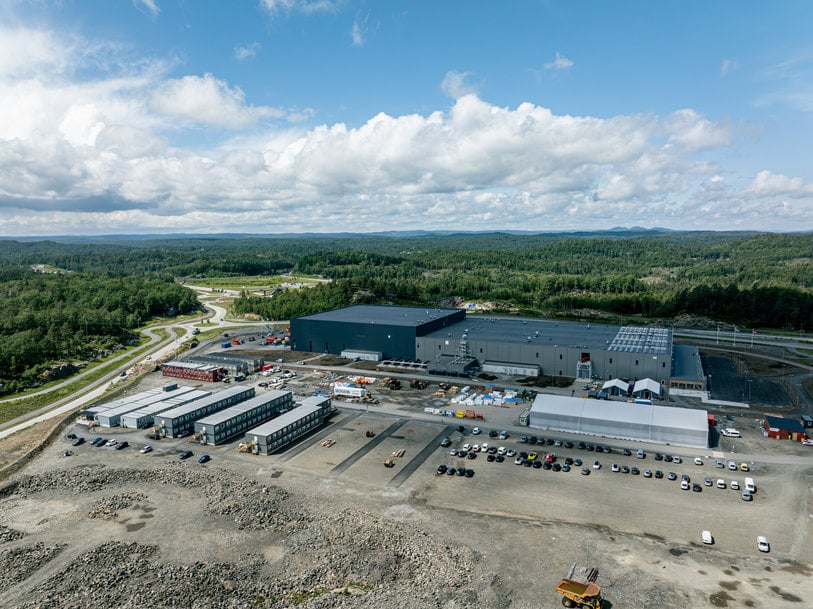
Drone photo of the Morrow gigafactory. Image source: Morrow Newsroom
The Asian dominance
When it comes to Asia, batteries with a total capacity of one terawatt hour (TWh) were manufactured in 2023 for use across EVs, energy storage and consumer electronics, with three-quarters of these made in China. The Asian dominance in batteries is actually the Chinese dominance, the country alone producing enough batteries at the moment to cater to the global demand. Six of the top 10 global battery manufacturers are Chinese companies. These include:
1. Contemporary Amperex Technology Limited (CATL) – One of the largest battery manufacturers in China, CATL was formed in 2011 in the Chinese city of Nindge, but has its roots in ATL, which was founded in 1999. CATL has grown rapidly by investing heavily in R&D and by 2017 became the world's largest manufacturer of lithium ion batteries for electric vehicles. CATL batteries are used in passenger vehicles, commercial vehicles, construction machinery, electric ships, and electric commercial aircraft. Its global market share in 2022 was a humongous 34% with a reported capacity of 191.6 GWh.
2. BYD Co – Established in 1995 as a manufacturer of different types of batteries, the company diversified in manufacturing automobiles in 2003 and has since grown to become the world’s largest manufacturer of battery electric vehicles (BEVs) and the second largest manufacturer of EV batteries after CATL. The company is engaged in diversified businesses but automobiles and batteries contribute over 80% to its revenue.
3. China Aviation Lithium Battery Co Ltd (CALB) – Founded in 2007, CALB started as part of the Aviation Industry Corporation of China (AVIC) but was spun of in 2021 and has grown to become the third largest battery manufacturer in China after CATL and BYD, with over 10% market share. A leading player in the global lithium battery industry, CALB caters to the requirements of diverse sectors such as electric vehicles, energy storage systems, aerospace applications, and more.
Other leading Chinese battery manufacturers are Gotion High-Tech, Sunwoda Electronic Co and Farasis Energy.
Other than China, South Korea is also a major manufacturer of batteries in Asia. As per Invest KOREA, South Korea’s national investment promotion agency, the country is the world's second-largest battery producer, accounting for 21% of the world's electric vehicle battery (including energy storage systems) capacity (as of 2021). The country has globally competitive manufacturers of finished battery products, and is also performing well in anode and cathode materials. The three main producers of batteries, components and allied systems in South Korea are LG Chem, Samsung SDI and SK Innovation.
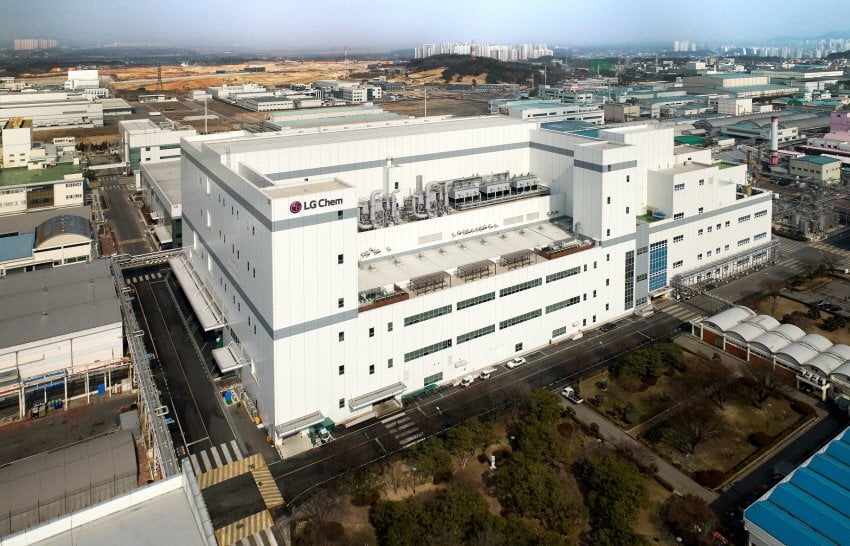
LG Chem single crystal high nickel cathode manufacturing plant in South Korea.
For a host of reasons like the reluctance of most automakers to go for all electric vehicles and preference for hybrid electric vehicles, Japan did not invest in EV battery manufacturing capacities until now. Ironically, Panasonic is a major producer of batteries outside Japan and a supplier to Tesla. But all that is going to change now as Japan has recently approved $2.4 billion aid for EV battery projects. Most of this funding will go to Toyota, Nissan and Panasonic to increase Japan’s annual battery production capacity by 50%, from 80 GWh to 120 GWh.
Indonesia and India are the two other countries with firm plans for manufacturing batteries on a large scale. Indonesia recently opened its first battery cell production facility at Karawang in West Java, which is owned by HLI Green Power, a joint venture between LG Energy Solution and Hyundai Motor Group. The plant has an annual capacity of 10 gigawatt hours (GWh) of battery cells, which is enough to power 150,000 electric vehicles. Indonesia also has signed an agreement with CATL of China to develop an EV ecosystem in the country.
India has made a beginning by putting a policy framework in place with the Production Linked Incentive (PLI) scheme for manufacturing batteries on scale. Currently the country imports most of its requirements. With the PLI Advanced Chemistry Cell (ACC) scheme for battery production initiated in 2021, the government has already allocated 30 GWh of the proposed 50 GWh, with a gestation period of two years. India’s largest company, Reliance Industries Ltd, with businesses spanning oil refining, petrochemicals, gas, retail, and telecommunications, is setting up a Gigafactory at its Jamnagar location for manufacturing batteries for EVs and storage systems. The company has secured 5 GWh capacity under PLI ACC scheme and is bidding for an additional 10 GWh. When completed, the Gigafactory will feature an annual capacity of 30 GWh, positioning it among the largest battery manufacturing facilities in India. Other bidders under the scheme are major industry players such as ACME Cleantech Solutions, Amara Raja Advanced Cell Technologies, Anvi Power Industries, JSW Neo Energy, Lucas TVS, and Waaree Energies. Apart from that, automakers Maruti-Suzuki and Tata Motors are also in the fray.
Summing up
That brings to the fore the question, can Europe and America challenge the global domination of Asia in the battery manufacturing ecosystem? From the preceding paragraphs it becomes obvious this is not going to happen in a hurry. Globally, including in China, the battery manufacturing industry has flourished and thrived on government and institutional support, backed by massive R&D efforts and a robust supply chain and assured supply of raw materials. China has stolen a march over Europe and the US on all these parameters, especially in the last 15 years, and is now comfortably perched on the top by a wide margin. Another important factor is that not all the commitments made by the government backed initiatives in the US and Europe are going to end in actual production for the capacities announced. So does this mean it is going to be a continued case of China dominating the battery value chain?
The jury is still out on this. With technology evolving rapidly, the quest for new solutions continues unabated. Sodium-ion batteries are a promising alternative to lithium-ion batteries for EVs, even as there are certain limitations like lower energy density and slower charge/discharge cycles. Another promising technology is solid-state batteries which promise a more economical and safer alternative to conventional lithium-ion batteries. A technological breakthrough may well change the equation, as solid-state batteries promise three to four times as much energy density as batteries with liquid electrolytes. Then there is the emerging hydrogen economy with the promise of fuel cell electric vehicles (FCEVs) and synthetic fuels that could well substitute fossil fuels. One thing is clear though – when it comes to electric mobility and green energy, the world has enough battery capacity to embrace both!
References
1. https://www.globalbattery.org/media/publications/gba-10-guiding-principles.pdf
2. https://chargelab.co/blog/how-are-ev-batteries-made
3. https://www.statista.com/statistics/1418340/battery-manufacturing-capacity-united-states-forecast/
4. https://source.benchmarkminerals.com/article/one-year-on-the-ira-has-changed-the-battery-landscape-in-the-us
5. https://www.6kinc.com/news/press-release/tennessee-governor-bill-lee-joins-6k-executives-for-official-groundbreaking-ceremony-for-the-6k-energy-pluscam-battery-material-production-plant-in-jackson-tn/
The US battery landscape
Globally, China, Europe and the US are the three biggest automobile markets that account for 60% of all passenger cars. According to the statistics compiled by the World Resources Institute, China is leading EV adoption at double the rate of the global average. While Europe is a little above the global average when it comes to preference for EVs, the US is lagging behind. A JD Power survey terms the US situation as the ‘Divided States of EV Adoption’ with reference to the wide difference between the top 10 states and bottom 10 states of USA. While EV sales in the top states are growing steadily, those in the bottom 10 are actually declining. According to a BBC report, the low adoption is mainly due to three factors that may be termed as the ‘ABC of low adoption’ – Affordability, Battery charging infrastructure, and Choice of suitable model or the lack of it. Americans traditionally have preferred large muscular cars and SUVs and also suffer from the phenomenon of ‘range anxiety’. This is the fear of the EV running out of charge even when the distance an average car covers in a day is much less than what a fully charged EV can cover. Regardless of these factors, analysts believe that EV sales in the US, as elsewhere, would increase, albeit slowly, in what is one of the largest automobile markets globally.
While it is difficult to pinpoint exactly when did the US start manufacturing EV batteries on scale, until 2019 it had only two battery manufacturing plants. Available information suggests it was Ford Motors that was engaged in manufacturing mid-to-large size battery packs for EVs in the late 1990s. These were either lead-acid batteries or nickel-metal hydride batteries (NiMH) developed for the Ford Ranger EV, a compact pickup truck. This was the first all-electric production vehicle Ford built in 1998 and was in production just for 4 years, until 2002. General Motors released its Chevy Bolt plug-in Hybrid in 2010 using batteries developed with technology from the US Department of Energy. Between these two developments, Tesla – the company formed in 2003, launched its first car, the Roadster Sports in 2008. It was the first street legal EV in the US to use a lithium-ion battery pack, assembled from cylindrical cells manufactured by Panasonic Corporation of Japan. In 2014, Panasonic, thanks to its association with Tesla, was the first to announce a large-scale battery manufacturing plant for lithium-ion batteries, at the Tesla Gigafactory at Nevada. The real impetus for domestic battery manufacturing in the US was however provided by the supply chain crisis during Covid. Automakers then realised how dependent they were on China for building their EVs and equipping them with the appropriate battery packs.
In May 2021, Ford and SK Innovation of South Korea signed a MoU to create a joint venture to produce approximately 60 GWh annually in traction battery cells and array modules, with potential for further expansion. A year later, in May 2022, Hyundai Motor Group announced it has entered into an agreement with the State of Georgia to build its first dedicated all-electric vehicle and battery manufacturing facilities in the US. Already a significant player in the North American EV market, the Hyundai Group aims to become one of the top three EV manufacturers by 2026. Thus began the gradual movement in the US for onshoring the EV supply chain, including the batteries. These early efforts received a massive boost when the Inflation Reduction Act (IRA) was signed into law in August 2022, which opened the doors further for more investments to follow. According to Benchmark Mineral Intelligence, a market intelligence publisher for the lithium ion battery to electric vehicle (EV) supply chain, the IRA has led to over $110 billion of capital investments announced for clean energy manufacturing projects, including over $70 billion towards EV and battery supply chains across the US.
In October 2022, Our Next Energy (ONE), a battery startup, announced plans to build a gigafactory in Michigan devoted to LFP cells. The scope of the plant, supported by a $200 million grant from the state of Michigan, includes raw material refinement, cathode materials production, and cell and battery manufacturing.
In November 2022, Norwegian company FREYR Battery, a developer of clean, next-generation battery cell production capacity, announced Coweta County in Georgia as the site for its Giga America battery plant. The initial phase of Giga America is planned to be a cell production module of approximately 34 GWh based on the SemiSolid™ technology of FREYR’s US-based licensing partner, 24M at an initial projected capital cost of $1.7 billion, with more investments in the pipeline. Upon completion of all the contemplated construction phases, the Giga America complex is expected to be one of the largest battery cell manufacturing developments globally.
In June 2023, 6K Energy, a division of 6K and leader in the sustainable production of critical materials for lithium-ion batteries, broke ground in Jackson, Tennessee for the construction of the world’s first sustainable multi-chemistry cathode manufacturing plant scheduled to open in Q3, 2024. “Our PlusCAM facility is the world’s most sustainable process that fulfills the need for domestically sourced low-cost battery material for our nation’s critical infrastructure, grid storage, and electric vehicles,” said 6K Energy President Sam Trinch.
In September 2023, Swedish producer of lithium-ion batteries, Northvolt, announced plans to open its first gigafactory in North America, thanks to the incentives promised by the IRA. The estimated project cost of over $7 billion will be split between Northvolt ($3 billion) with local and federal governments contributing around $4 billion.
Also in September 2023, three companies – Accelera, the zero-emissions business unit of Cummins Inc; Daimler Trucks & Buses US Holding LLC; and PACCAR – announced they are partnering to accelerate and localise battery cell production and the battery supply chain in the US. The planned joint venture, Amplify Cell Technologies, will manufacture battery cells for electric commercial vehicles and industrial applications at the Marshall County site in Mississippi, creating highly desirable US manufacturing jobs in the growing clean technology sector. Total investment is expected to be in the range of $2-3 billion for the 21-gigawatt hour (GWh) factory.
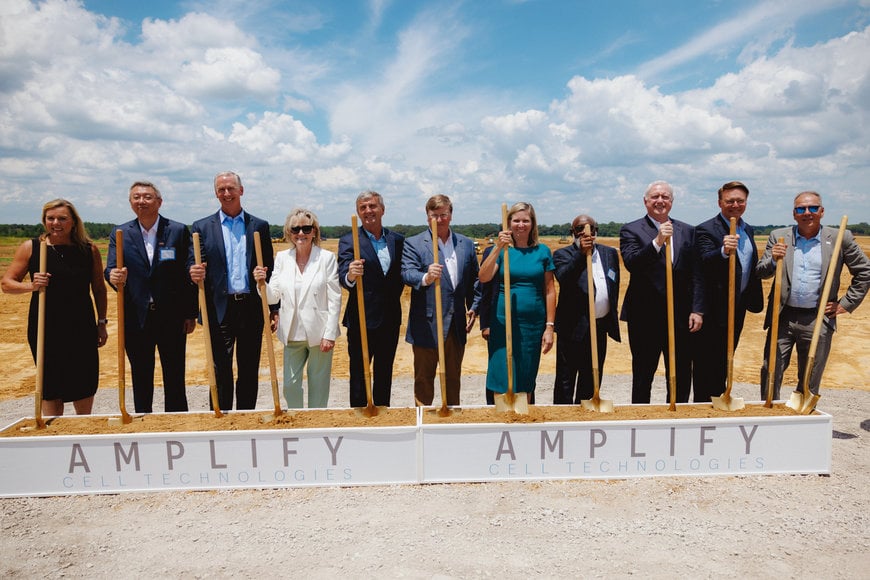
The shovel ceremony – groundbreaking at Amplify Cell Technologies’ Marshall County site in Mississippi. Image source: Amplify
According to figures presented by Statista Research Department in June 2024, the capacity of the battery manufacturing industry in the United States in 2022 amounted to 90 gigawatt-hours, and increased to 114 gigawatt-hours in 2023. This is estimated to grow five-fold between 2023 and 2030, reaching almost one terawatt-hour of battery manufacturing capacity that year.
The scenario in Europe
In Europe, the Directorate-General for Climate Action (DG CLIMA) leads the European Commission's efforts to fight climate change domestically and at international level. The organisation believes that transport is responsible for one-quarter of all greenhouse gas emissions in the EU, and road transport makes up 70% of that amount, primarily from petrol and diesel cars. As a result, in order to cut emissions, the EU in 2023 adopted a law to make all new cars and vans sold in Europe zero-emission from 2035. Europe, as mentioned earlier in this article, is a little above the global average in EV adoption and this move will further accelerate the growth of EVs in the continent. In fact Norway boasts the highest EV adoption rate in the world, with 82% of new car sales registered in 2003 being EVs. This rapid electrification of mobility in Europe also calls for a massive expansion of battery manufacturing capacities.
Fortunately, the European Commission had launched the European Battery Alliance in October 2017, anticipating the trends and movement towards clean mobility. With an estimated annual market value of €250 billion from 2025, the European Commission had realised the imperative for a clean energy transition and a competitive industry with a complete domestic battery value chain.
Samsung SDI is one of the earliest foreign companies to manufacture batteries in Europe and the first one in Hungary. The company which was founded in South Korea in 1970 to manufacture vacuum tubes for B&W TVs owned a cathode ray tube factory at Göd in Hungary which it decided to turn into a battery manufacturing plant in 2016. After its inauguration in 2017, Samsung SDI added a second plant in 2019 at the same location, and by early 2022 had a total production of 40 GWh/year. The company manufactures prismatic battery cells in Hungary that are used by several EV manufacturers like BMW, Volkswagen and Stellantis. It is now in the process of setting up a third plant, reportedly for cylindrical cells that could be supplied to BMW and/or Hyundai according to informed sources.
Another Korean company, LG Electronics, formed LG Energy Solution Wrocław in Poland in 2016. Today it has become Europe's largest and the world's leading producer of lithium-ion batteries for the automotive industry. Based in Biskupice Podgórne, Poland, the plant covers an area of about 100 ha, with tens of modern production lines. LG Energy Solution Wrocław manufactures all battery elements up to the product ready for installation in a car, in the process making Poland the European leader in the industry. With a current capacity of 86 GWh, the batteries produced in this facility are used in EVs of such automotive giants as Audi, BMW, Fiat, Ford, Porsche and Volkswagen.
In 2021, Northvolt AB, a Swedish battery manufacturer, commissioned its first gigafactory, Northvolt Ett, in Skellefteå, Sweden. Northvolt Ett – a lithium-ion battery gigafactory – is touted as Europe’s first homegrown response to explore opportunities and fulfill needs of an electric world. The project was financed by the European Investment Bank (EIB) and supported by the European Fund for Strategic Investments (EFSI). In early 2024, the EIB announced further lending to the Northvolt gigafactory for further expansion, which is expected to increase the annual output capacity for battery production to up to 60 GWh. According to the EIB, the deal is the largest green loan raised in Europe to date and will facilitate the creation of a fully integrated circular battery production facility that has not previously existed outside Asia.
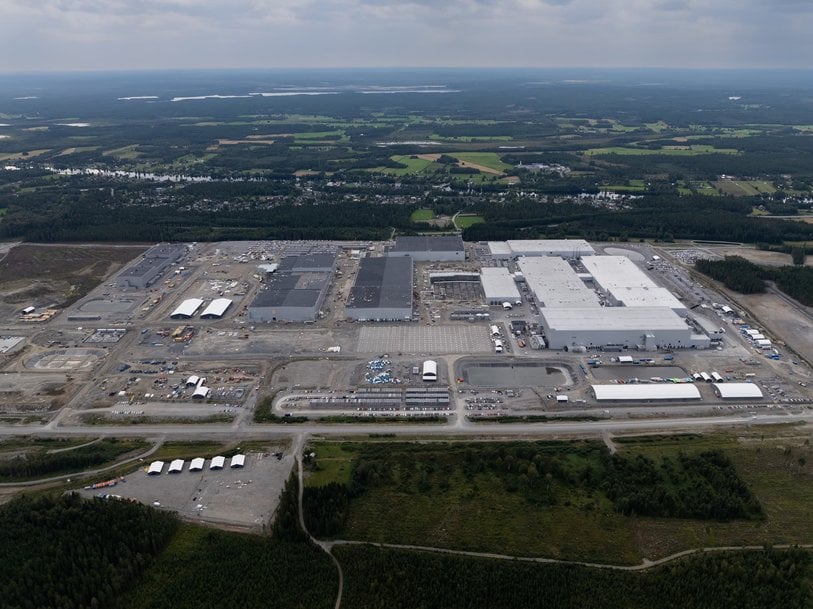
Northvolt Ett – a lithium-ion battery gigafactory in Skellefteå, Sweden. Image source: Northvolt
In April 2023, ElevenEs, the pioneer in LFP cathode battery technology, announced the opening of the first industrial facility dedicated to LFP battery cell production in Europe. ElevenEs, backed by EIT InnoEnergy, is leading battery innovation in Europe with its new production site, located in Subotica, Serbia. The company specialises in producing high-quality LFP prismatic cells for use across a variety of applications, including electric cars, buses, trucks, and energy storage systems. The industrial facility will expand to become the company's Mega-Factory by late 2024, producing 500MWh. ElevenEs's roadmap over the next five years includes operating two Gigafactories at a combined capacity of 48GWh – equivalent to the energy needed for one million electric cars annually.
In mid-August 2024, Norwegian battery startup Morrow Batteries opened its first battery cell production site in southern Norway, with deliveries expected to begin by the end of the year. "This is a hugely important day in Norwegian industrial history and a testament to the bold vision and risk-taking spirit of our founders and the dedication of our diverse team of Morrowers, now consisting of 200 individuals from 34 nationalities,” said Lars Christian Bacher, CEO of Morrow Batteries. Founded in 2020, Morrow is fully European owned, the owners include Siemens, ABB, the Danish pension fund PKA, the Norwegian state’s climate investment company Nysnø Climate Investments, Norwegian environmental company Noah AS, and the Norwegian renewable energy company Å Energy. The first European GWh manufacturer of prismatic LFP batteries, Morrow claims its products offer top-tier safety features, extended cycle life and a low carbon footprint. The company plans to produce 43-gigawatt hours annually from 2028.
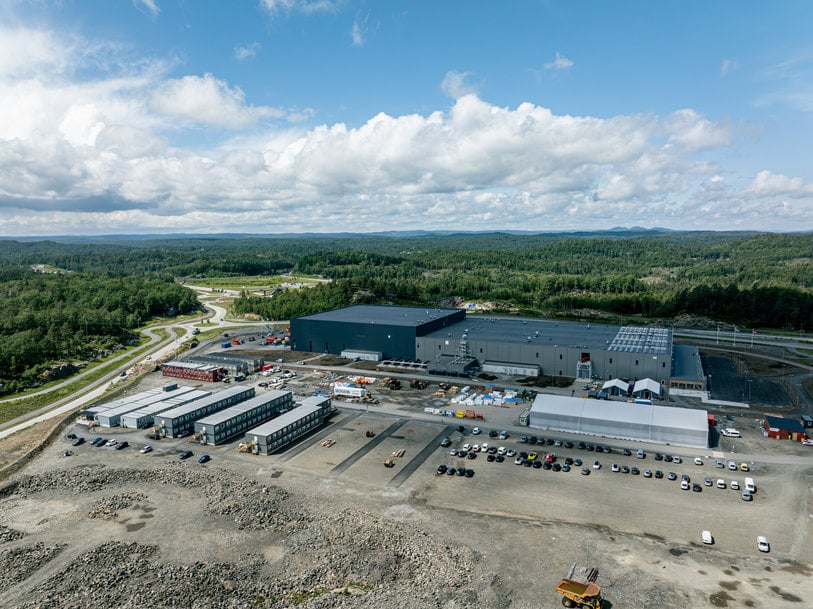
Drone photo of the Morrow gigafactory. Image source: Morrow Newsroom
The Asian dominance
When it comes to Asia, batteries with a total capacity of one terawatt hour (TWh) were manufactured in 2023 for use across EVs, energy storage and consumer electronics, with three-quarters of these made in China. The Asian dominance in batteries is actually the Chinese dominance, the country alone producing enough batteries at the moment to cater to the global demand. Six of the top 10 global battery manufacturers are Chinese companies. These include:
1. Contemporary Amperex Technology Limited (CATL) – One of the largest battery manufacturers in China, CATL was formed in 2011 in the Chinese city of Nindge, but has its roots in ATL, which was founded in 1999. CATL has grown rapidly by investing heavily in R&D and by 2017 became the world's largest manufacturer of lithium ion batteries for electric vehicles. CATL batteries are used in passenger vehicles, commercial vehicles, construction machinery, electric ships, and electric commercial aircraft. Its global market share in 2022 was a humongous 34% with a reported capacity of 191.6 GWh.
2. BYD Co – Established in 1995 as a manufacturer of different types of batteries, the company diversified in manufacturing automobiles in 2003 and has since grown to become the world’s largest manufacturer of battery electric vehicles (BEVs) and the second largest manufacturer of EV batteries after CATL. The company is engaged in diversified businesses but automobiles and batteries contribute over 80% to its revenue.
3. China Aviation Lithium Battery Co Ltd (CALB) – Founded in 2007, CALB started as part of the Aviation Industry Corporation of China (AVIC) but was spun of in 2021 and has grown to become the third largest battery manufacturer in China after CATL and BYD, with over 10% market share. A leading player in the global lithium battery industry, CALB caters to the requirements of diverse sectors such as electric vehicles, energy storage systems, aerospace applications, and more.
Other leading Chinese battery manufacturers are Gotion High-Tech, Sunwoda Electronic Co and Farasis Energy.
Other than China, South Korea is also a major manufacturer of batteries in Asia. As per Invest KOREA, South Korea’s national investment promotion agency, the country is the world's second-largest battery producer, accounting for 21% of the world's electric vehicle battery (including energy storage systems) capacity (as of 2021). The country has globally competitive manufacturers of finished battery products, and is also performing well in anode and cathode materials. The three main producers of batteries, components and allied systems in South Korea are LG Chem, Samsung SDI and SK Innovation.
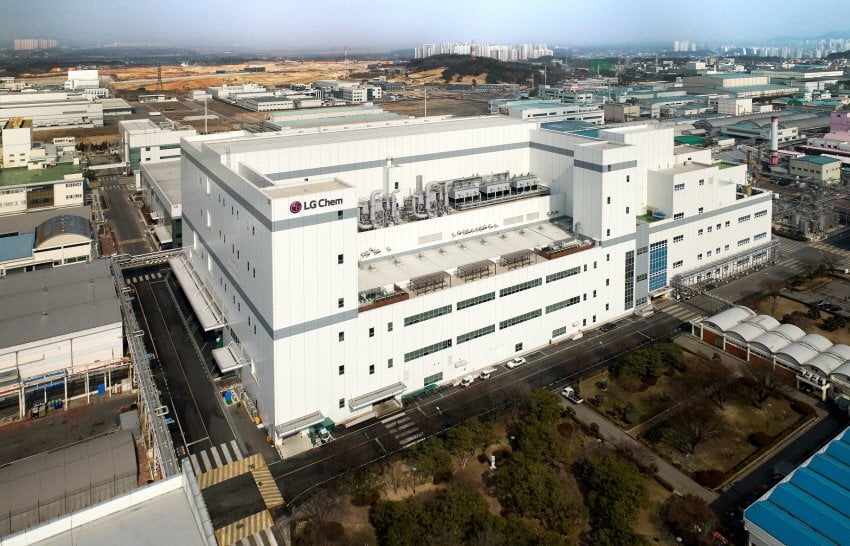
LG Chem single crystal high nickel cathode manufacturing plant in South Korea.
For a host of reasons like the reluctance of most automakers to go for all electric vehicles and preference for hybrid electric vehicles, Japan did not invest in EV battery manufacturing capacities until now. Ironically, Panasonic is a major producer of batteries outside Japan and a supplier to Tesla. But all that is going to change now as Japan has recently approved $2.4 billion aid for EV battery projects. Most of this funding will go to Toyota, Nissan and Panasonic to increase Japan’s annual battery production capacity by 50%, from 80 GWh to 120 GWh.
Indonesia and India are the two other countries with firm plans for manufacturing batteries on a large scale. Indonesia recently opened its first battery cell production facility at Karawang in West Java, which is owned by HLI Green Power, a joint venture between LG Energy Solution and Hyundai Motor Group. The plant has an annual capacity of 10 gigawatt hours (GWh) of battery cells, which is enough to power 150,000 electric vehicles. Indonesia also has signed an agreement with CATL of China to develop an EV ecosystem in the country.
India has made a beginning by putting a policy framework in place with the Production Linked Incentive (PLI) scheme for manufacturing batteries on scale. Currently the country imports most of its requirements. With the PLI Advanced Chemistry Cell (ACC) scheme for battery production initiated in 2021, the government has already allocated 30 GWh of the proposed 50 GWh, with a gestation period of two years. India’s largest company, Reliance Industries Ltd, with businesses spanning oil refining, petrochemicals, gas, retail, and telecommunications, is setting up a Gigafactory at its Jamnagar location for manufacturing batteries for EVs and storage systems. The company has secured 5 GWh capacity under PLI ACC scheme and is bidding for an additional 10 GWh. When completed, the Gigafactory will feature an annual capacity of 30 GWh, positioning it among the largest battery manufacturing facilities in India. Other bidders under the scheme are major industry players such as ACME Cleantech Solutions, Amara Raja Advanced Cell Technologies, Anvi Power Industries, JSW Neo Energy, Lucas TVS, and Waaree Energies. Apart from that, automakers Maruti-Suzuki and Tata Motors are also in the fray.
Summing up
That brings to the fore the question, can Europe and America challenge the global domination of Asia in the battery manufacturing ecosystem? From the preceding paragraphs it becomes obvious this is not going to happen in a hurry. Globally, including in China, the battery manufacturing industry has flourished and thrived on government and institutional support, backed by massive R&D efforts and a robust supply chain and assured supply of raw materials. China has stolen a march over Europe and the US on all these parameters, especially in the last 15 years, and is now comfortably perched on the top by a wide margin. Another important factor is that not all the commitments made by the government backed initiatives in the US and Europe are going to end in actual production for the capacities announced. So does this mean it is going to be a continued case of China dominating the battery value chain?
The jury is still out on this. With technology evolving rapidly, the quest for new solutions continues unabated. Sodium-ion batteries are a promising alternative to lithium-ion batteries for EVs, even as there are certain limitations like lower energy density and slower charge/discharge cycles. Another promising technology is solid-state batteries which promise a more economical and safer alternative to conventional lithium-ion batteries. A technological breakthrough may well change the equation, as solid-state batteries promise three to four times as much energy density as batteries with liquid electrolytes. Then there is the emerging hydrogen economy with the promise of fuel cell electric vehicles (FCEVs) and synthetic fuels that could well substitute fossil fuels. One thing is clear though – when it comes to electric mobility and green energy, the world has enough battery capacity to embrace both!
References
1. https://www.globalbattery.org/media/publications/gba-10-guiding-principles.pdf
2. https://chargelab.co/blog/how-are-ev-batteries-made
3. https://www.statista.com/statistics/1418340/battery-manufacturing-capacity-united-states-forecast/
4. https://source.benchmarkminerals.com/article/one-year-on-the-ira-has-changed-the-battery-landscape-in-the-us
5. https://www.6kinc.com/news/press-release/tennessee-governor-bill-lee-joins-6k-executives-for-official-groundbreaking-ceremony-for-the-6k-energy-pluscam-battery-material-production-plant-in-jackson-tn/