www.industryemea.com
26
'23
Written on Modified on
A COMPLETE GUIDE TO OFFLINE ROBOT PROGRAMMING (OLP) FROM VISUAL COMPONENTS
This is your complete and comprehensive guide to offline robot programming (OLP). After introducing the topic, it addresses common misconceptions, the problems it resolves, benefits, and real-life examples of its successful implementation.
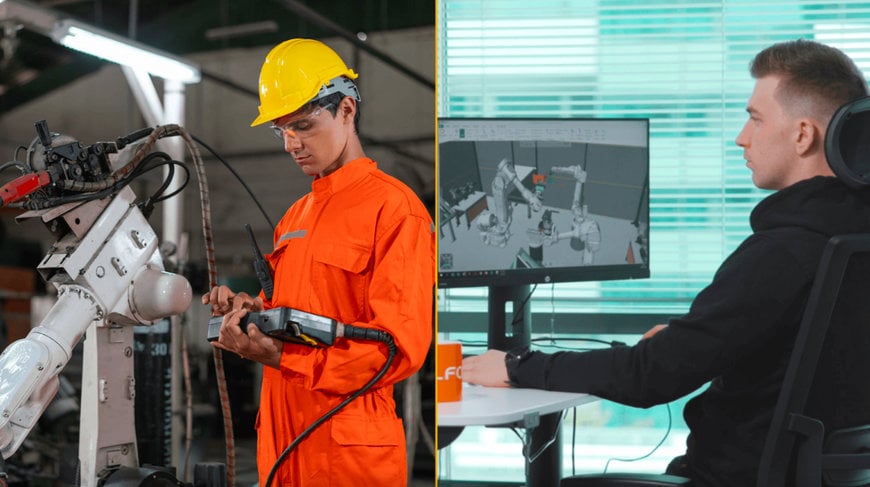
The concept of Offline Robot Programming (OLP) has been discussed for several years but we believe that the manufacturing businesses still don’t fully understand the value of OLP, especially in the production environments where industrial robots are used for applications like welding, processing, spraying, and more.
What is OLP?
Offline Robot Programming (OLP) is a method of generating robot programs in computer software (virtual environment) based on 3D CAD data. Once the robot program is generated and verified in the software, it can be downloaded to the physical robot.
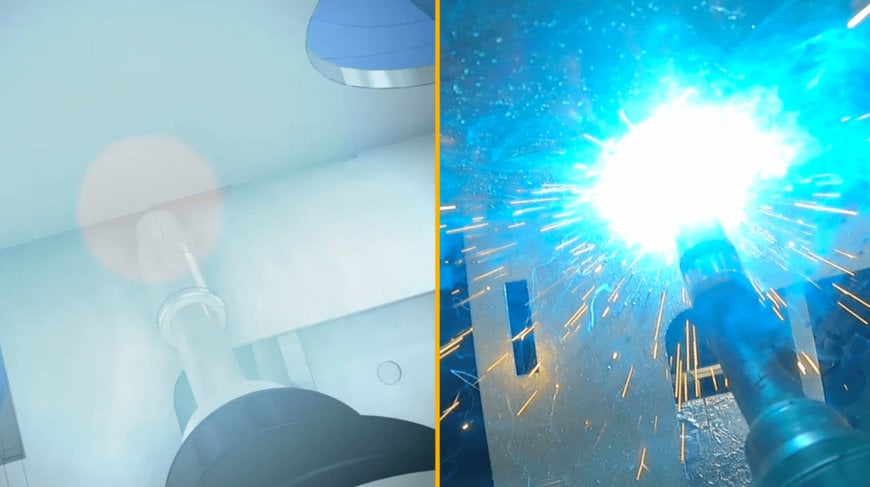
Welding program in OLP software (left) and real welding on the shop floor (right)
Let’s start with an example that illustrates why you might want to use OLP.
Imagine programming a robot to weld a circular part on a metal workpiece. The robot needs to move the welding torch in a 3D arc around the circumference of the part, and at the same time maintain a precise orientation with respect to the surface.
You can do this by teaching points with a pendant, but you’ll need a lot of points, and it will take a long time. The gap between the torch will almost certainly vary, as will the orientation of the torch. What’s more, the robot cell won’t be available for production until you’ve finished programming. This stoppage might take from days to weeks. With OLP producing the robot program is much easier. Import a CAD file of the welding cell into the OLP software and show the path you want the torch to take. Once finished, the software generates the robot program and verifies the program for e.g., potential collisions. Once verified, download the program into the robot controller, run once at low speed to double-check, and the cell is ready to resume work.
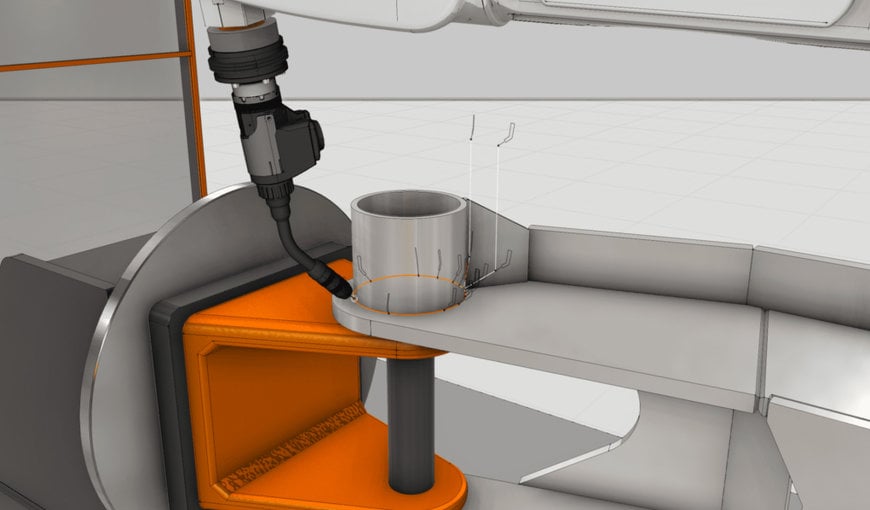
Circular weld program visualization in OLP software
Common Misconceptions and Misunderstandings About OLP
While OLP has been available for quite a few years, adoption has been relatively slow. This is due, at least in part, to a lack of understanding of what it is and how it’s used. It’s time to clarify the understanding of this topic.
#1: OLP is only for large manufacturers
This stems from the assumption that high production volumes are needed to benefit from OLP. The reality is a slightly different story. OLP is especially beneficial when the production runs are short, setups or changeovers are frequent, and there’s a lot of variety in the tasks. Small and mid-sized manufacturers can greatly benefit from OLP if they are running small-batch production.
#2: OLP is difficult to use
Like any software, OLP requires some training and has a learning curve. Plus, there are probably some OLP products that are not particularly user-friendly. The best products though are intuitive, logical, and easy to use, letting novice users quickly become proficient.
Furthermore, don’t underestimate the complexity of programming by robot teach pendant. Different robot brands have different commands and then additionally the systems can change from older to newer robot models. This makes it even more complicated to use manual programming.
#3: OLP is expensive
An OLP product is an additional purchase. However, it only needs buying once and can support whatever brands of robot a facility uses. (This also helps a facility avoid being locked into a single robot vendor.)
OLP users report improved ROI from their robot cells, as downtime is reduced, and robot utilization increased. There’s evidence it can cut robot downtime due to programming by as much as 90% and can pay for itself on a single project.
#4: OLP eliminates the need for skilled programmers
OLP software speeds up program creation, reducing the time required for programming, but it does not eliminate the need for skilled programmers. Path planning and optimization, collision avoidance, and so on are all best done by an experienced programmer. However, OLP software can make them more productive, giving them time to work on more complex programming tasks and innovate in a safer work environment.
Pain Points in the Typical Workflow Without OLP
The alternative to using OLP is programming directly at the robot. There are at least three problems with this.
- Risk of project delays and additional costs
- Safety concerns
- Lost production capacity
There’s a substantial risk of project delays when programming is done at the robot. To reach this point all the tooling and fixtures have been designed, built, and installed. The conveyors or other material handling devices are set up and parts are ready to use. Only now can the programmer start teaching points for the robot.
It’s almost guaranteed that problems will arise. Perhaps the robot can’t reach a particular location, possibly parts are in the wrong place, or maybe the target cycle time isn’t achievable.
With any of these, the only solution is to redesign the problem points of the cell. Inevitably, that delays the start of production, possibly by weeks, and adds significant additional costs.
Teaching points with a pendant often requires the programmer to enter the cell: it may be the only way to see where the tool is going or to check for collisions. Putting the robot into “teach” mode should ensure it’s safe, but there’s always a risk of unexpected movement, either of the robot itself or of one of the other mechanisms in the cell.
Last, while the programmer is teaching points inside the work cell, the robot can’t do anything else. This is all non-productive time until the programmer has finished and the program is proven. And even the best programmers are prone to underestimating the time needed for the task!
Benefits of OLP
Manufacturers who use OLP software report multiple benefits:
It’s almost guaranteed that problems will arise. Perhaps the robot can’t reach a particular location, possibly parts are in the wrong place, or maybe the target cycle time isn’t achievable.
With any of these, the only solution is to redesign the problem points of the cell. Inevitably, that delays the start of production, possibly by weeks, and adds significant additional costs.
Teaching points with a pendant often requires the programmer to enter the cell: it may be the only way to see where the tool is going or to check for collisions. Putting the robot into “teach” mode should ensure it’s safe, but there’s always a risk of unexpected movement, either of the robot itself or of one of the other mechanisms in the cell.
Last, while the programmer is teaching points inside the work cell, the robot can’t do anything else. This is all non-productive time until the programmer has finished and the program is proven. And even the best programmers are prone to underestimating the time needed for the task!
Benefits of OLP
Manufacturers who use OLP software report multiple benefits:
- No Robot Downtime: Programming time can be reduced up to 80% and robot utilization increased by as much as 95%, boosting programmer productivity and cutting cell downtime
- Quick Set-Up Times: Less time is needed to launch a new product into production – programming happens concurrently rather than sequentially
- Increased Safety: Reduced risk of accidents and injuries
- Higher and Repeatable Quality: Robot programs are better optimized, (shorter cycle times, higher accuracy and consistency,) resulting in higher and repeatable production quality.
- Robot Brand and Process Agnostic: Regardless of robot brands or types of processes, advanced OLP software can cover all applications.
- No More Surprises: Last-minute fixture and tooling modifications are avoided
A significant additional benefit is the contribution OLP makes to Design for Manufacturability (DfM). Primarily, this flows from everyone having access to the same process knowledge, rather than different standards, systems, design methodologies, and so on. In addition, by parallelizing programming with cell design and construction, there are more opportunities to optimize designs for shorter cycle times and better product quality.
Applications of OLP
Every robot application is a candidate for OLP; the only requirement is to have digital models of the work cell, parts, tooling, and fixtures. (And today everything is designed in CAD, so that should not be a problem.) However, the benefits are magnified as robot paths become more complex and more points need to be taught.
With these points in mind, some of the best use cases for OLP are:
Applications of OLP
Every robot application is a candidate for OLP; the only requirement is to have digital models of the work cell, parts, tooling, and fixtures. (And today everything is designed in CAD, so that should not be a problem.) However, the benefits are magnified as robot paths become more complex and more points need to be taught.
With these points in mind, some of the best use cases for OLP are:
- Welding – access, and orientation are particular challenges that OLP helps with, and complex weld beads can require large numbers of points
- Coating (Painting) – as with welding, orientation is important, and so too are unified paint thickness and standoff distance, plus ensuring all areas can be reached and painted optimally.
- Dispensing – many assembly operations require the deposition of long, complex adhesive beads: OLP helps to create the tool paths rapidly offline with consistent quality.
- Processing (Surface) – applications like bead blasting and deburring often need long, complicated paths that require a lot of points
- Assembly applications (jigless) – grasping and insertion-type moves need precise control over gripper orientation, which is achieved at a higher level with OLP
- Material handling applications – OLP lets a programmer determine the fastest distance between two locations, which may not always be the most obvious route
- Cutting – Plasma or laser cutting or waterjet cutting may work for standard parts but for complex geometries, robots are needed with accurate cutting patterns that can be generated with OLP.
Impact on Small Batch Manufacturing
While any manufacturer using robots will benefit from OLP, the biggest gains are seen where batch sizes are small and production runs short. The problem is that, when programming the robot, frequent changeovers and setups will eat into availability and running hours. However, with OLP, programs are tested virtually and downloaded to the robots while physical aspects of the cell (fixtures, grippers, and so on,) are being changed. Prudence suggests running the robot through a cycle at low speed to check for collisions, after which the cell is ready to restart production.
Furthermore, any design-related issues in the documentation or models are identified in advance and can be communicated to other teams and resolved without losing production downtime.
Examples of Successful OLP Cases
Afrit, a South African manufacturer of large trailers, implemented OLP. They saw the time spent on robot programming cut from two weeks in the cell to four days offline.
Volvo is implementing OLP in their articulated haulers, and wheel loaders manufacturing businesses. A pilot cell targeted at a family of high variety, low volume components is using it to implement “jigless welding” in a cell using two robots, one for handling, and one for welding.
In Finland, HT Laser performs small-batch robotic cutting and welding using robots from several manufacturers. They adopted OLP to save programming time and increase production capacity.
Why OLP Should be a Standard Tool for Manufacturers Using Robots
Given the step-change in productivity that OLP provides, robot users who stick with manual programming at the work cell are putting themselves at a disadvantage. OLP:
- Is a cost-effective solution for robot programming
- Reduces the need for physical testing and debugging of robots
- Improves safety and reduces the risk of accidents and injuries
- Enables faster and more accurate programming
The Delfoi Robotics OLP Solution
Visual Components has long been a leader in 3D manufacturing simulation. As OLP grew out of robot simulation, the two technologies are complementary. This is why Visual Components Group acquired Delfoi Robotics OLP software, (which is built on top of the Visual Components platform) in October 2022.
Here’s what makes the Delfoi OLP solution unique:
Visual Components has long been a leader in 3D manufacturing simulation. As OLP grew out of robot simulation, the two technologies are complementary. This is why Visual Components Group acquired Delfoi Robotics OLP software, (which is built on top of the Visual Components platform) in October 2022.
Here’s what makes the Delfoi OLP solution unique:
- Intuitive, Fast to Learn
- Layout and Process independent – one software covers most robot applications (Welding, Processing, Coating)
- Robot independent – this software covers OLP for all major brands including 17 post-processors in one product (more to be added in future) and 40 robot controller versions (old and new)
- Institutionalizes and stores core process knowledge, making it available to all stakeholders involved in product, cell and fixture design
- Extremely Fast, Automated, and Reliable program generation and validation.
- Intelligent and Automatic tools for solving robot program problems.
- Used in over 30 countries and supports multiple languages.
It’s Time to Move to Offline Robot Programming
Manually Programming a robot at the work cell is slow and imperfect. It ties up the cell for days or weeks and delays the start of production. OLP solves these problems by enabling programming in a virtual environment. Then, when ready and verified the program is downloaded to the robot and production can begin.
OLP provides manufacturers with substantial speed, cost, efficiency, and quality advantages over those who aren’t using it. The Delfoi Robotics OLP solution from Visual Components is easy to learn and works with all leading robot brands.