www.industryemea.com
13
'23
Written on Modified on
SECOND GIANT HS2 TUNNEL BORING MACHINE GETS READY TO START DIGGING UNDER BIRMINGHAM
A 90-strong specialist team has assembled the 1,600-tonne machine set to build the second bore of Bromford Tunnel.
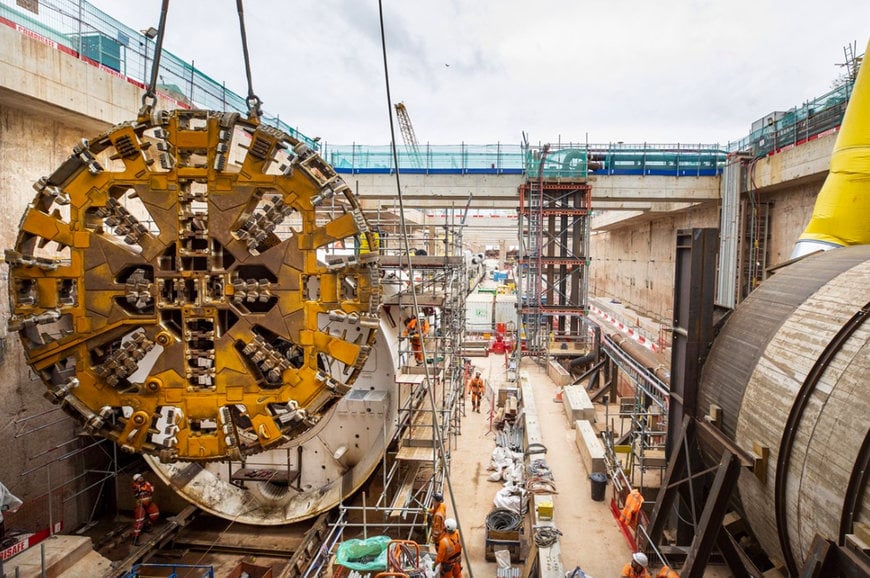
The giant 125-tonne cutterhead being moved into place
A team of 90 specialist engineers have completed the assembly of HS2’s giant tunnel boring machine (TBM) which will start digging the second bore of the 3.5 mile Bromford Tunnel into Birmingham next year.
In an assembly operation to move sections of the machine into a 12-metre deep launch pit, two 600 tonne cranes lifted the huge 125-tonne cutterhead into place at the front of the 125-metre-long machine in the pit bottom.
The first TBM, named ‘Mary Ann’ after Mary Ann Evans – the real name of Victorian writer George Eliot who was born in Nuneaton – started digging the first bore from the east portal site near Water Orton in August this year. It has already built more than 500 tunnel rings, which is 0.6 miles of the 3.5 mile long tunnel between North Warwickshire and Washwood Heath in Birmingham.
The name of the second TBM will be revealed before it launches in Spring next year. ‘Mary Ann’ is set to break through at the end of 2024, with the second TBM planned to complete its journey in the middle of 2025.
Both TBMs will remove 1.87 million tonnes of excavated material, which will be sifted at the on-site slurry treatment plant and reused on HS2’s nearby sites at Delta Junction, where a complex network of nine viaducts is being built.
The majority of the second TBM, including the gantries and the centre part of the cutterhead, have been re-used from TBM ‘Dorothy’ after completing the one-mile twin bore Long Itchington Wood Tunnel in Warwickshire earlier this year.
Disassembled sections of ‘Dorothy’ have been moved to the Bromford Tunnel portal site near Water Orton over the last few months, where they have been lowered and reassembled into the underground launch area.
At 8.62 metres in diameter, the Bromford Tunnel is smaller than the 10-metre-diameter Long Itchington Wood Tunnel because trains will be travelling slower on the approach into Birmingham Curzon Street Station. For this reason, the TBM needed a new outer part cutterhead and a new shield, which were manufactured by Herrenknecht in Germany.
A total of 41,594 concrete segments will create 5,942 rings to make the twin bore tunnel, with each ring weighing 49 tonnes.
The segments are being produced at Balfour Beatty VINCI’s pre-cast factory at Avonmouth near Bristol. In the concrete mix used at the factory 40% of the cement is replaced with Ground Granulated Blast-furnace Slag (GGBS) which has a much lower carbon footprint than traditional cement. 3D scanning is used in the production process of the segments to guarantee accuracy.
A team of 90 specialist engineers have completed the assembly of HS2’s giant tunnel boring machine (TBM) which will start digging the second bore of the 3.5 mile Bromford Tunnel into Birmingham next year.
In an assembly operation to move sections of the machine into a 12-metre deep launch pit, two 600 tonne cranes lifted the huge 125-tonne cutterhead into place at the front of the 125-metre-long machine in the pit bottom.
The first TBM, named ‘Mary Ann’ after Mary Ann Evans – the real name of Victorian writer George Eliot who was born in Nuneaton – started digging the first bore from the east portal site near Water Orton in August this year. It has already built more than 500 tunnel rings, which is 0.6 miles of the 3.5 mile long tunnel between North Warwickshire and Washwood Heath in Birmingham.
The name of the second TBM will be revealed before it launches in Spring next year. ‘Mary Ann’ is set to break through at the end of 2024, with the second TBM planned to complete its journey in the middle of 2025.
Both TBMs will remove 1.87 million tonnes of excavated material, which will be sifted at the on-site slurry treatment plant and reused on HS2’s nearby sites at Delta Junction, where a complex network of nine viaducts is being built.
The majority of the second TBM, including the gantries and the centre part of the cutterhead, have been re-used from TBM ‘Dorothy’ after completing the one-mile twin bore Long Itchington Wood Tunnel in Warwickshire earlier this year.
Disassembled sections of ‘Dorothy’ have been moved to the Bromford Tunnel portal site near Water Orton over the last few months, where they have been lowered and reassembled into the underground launch area.
At 8.62 metres in diameter, the Bromford Tunnel is smaller than the 10-metre-diameter Long Itchington Wood Tunnel because trains will be travelling slower on the approach into Birmingham Curzon Street Station. For this reason, the TBM needed a new outer part cutterhead and a new shield, which were manufactured by Herrenknecht in Germany.
A total of 41,594 concrete segments will create 5,942 rings to make the twin bore tunnel, with each ring weighing 49 tonnes.
The segments are being produced at Balfour Beatty VINCI’s pre-cast factory at Avonmouth near Bristol. In the concrete mix used at the factory 40% of the cement is replaced with Ground Granulated Blast-furnace Slag (GGBS) which has a much lower carbon footprint than traditional cement. 3D scanning is used in the production process of the segments to guarantee accuracy.
www.hs2.org.uk