www.industryemea.com
04
'24
Written on Modified on
Deutsche Bahn uses 3D printing to improve vehicle maintenance and employee comfort
Deutsche Bahn uses 3D printing to improve vehicle maintenance and comfort Deutsche Bahn (DB) is one of the world's largest rail companies, handling more than 10 million passengers a day.
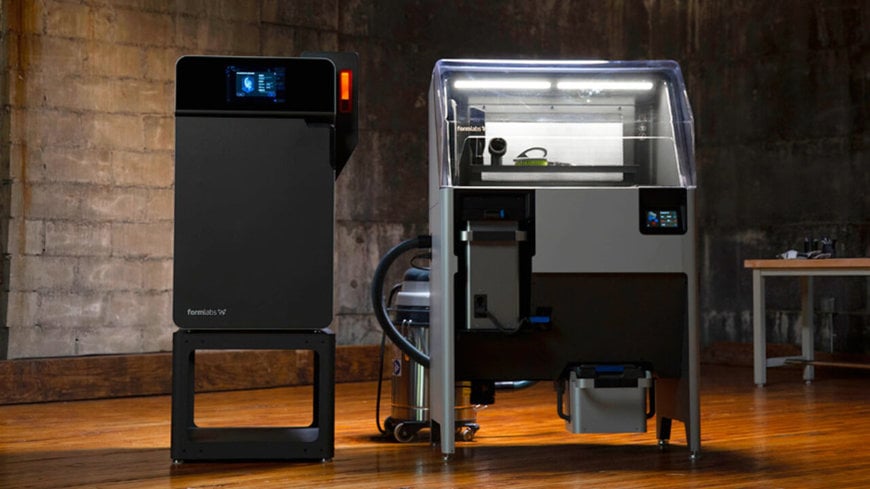
Managing, maintaining and developing its infrastructure and rolling stock is no mean feat. The company uses 50 workshops throughout Germany to maintain its fleet of passenger and goods trains.
The DB vehicle maintenance workshop in Neumünster employs around 750 people who maintain, repair and sometimes completely modify or modernize passenger carriages for intercity and regional trains. The workshop has an on-site 3D printing facility to make operations more efficient.
"We embarked on 3D printing in 2015, and since then we have already produced more than 100,000 parts that have saved Deutsche Bahn millions of euros," explains Susanne Tost, marketing manager for the DB Group's 3D printing project. "Deutsche Bahn chose Formlabs' 3D printing solutions to produce manufacturing aids that simplify workflows, reduce costs and help get trains back on the rails faster. But 3D printing is also being used to manufacture old parts that are no longer available as well as new ones for DB's trains and staff."
Neumünster's 3D printing workshop has ten 3D printers on site, covering a wide range of technologies. Two of these are SLS printers from the Fuse series: one uses the versatile and resistant Nylon 12 Powder, while the other 3D prints with the flexible TPU 90A Powder material. The workshop also has two SLA printers, a Form 3L (large format) and a Form 3.
Designed for business travellers and long-distance commuters, the Intercity Express or ICE is Deutsche Bahn's flagship passenger train. It travels at speeds of up to 320 km/h. The first-generation ICE 1 carriages, which have been in service for over 30 years, are now being completely refurbished. This major modernisation project requires close collaboration between several workshops and departments, as well as with different trades, such as painters, locksmiths, electricians, etc... Neumünster is one of the workshops acting as a hub for this transnational operation.
During the restoration process, the team noticed, for example, that the caps that protect and guide the cables of the electrical sockets installed under the seats had either been broken during cleaning or had completely disappeared over time. As these were made-to-measure parts, they are no longer produced and cannot be easily replaced.
"After reverse engineering by the DB Group, we were asked to print prototypes using SLS 3D printing in Nylon 12 Powder to test the fit and get an idea of the actual dimensions. The second version was already a perfect fit, and it was easy to put it in place," explains Carsten Wolfgramm, manufacturing engineer and additive manufacturing expert, Deutsche Bahn Vehicle Maintenance. "We use Formlabs 3D printers because the value for money is unbeatable for us. They are reliable and always ready to use, especially the SLS printers. This makes it much easier to work with parts that need to be constantly modified. They work 24 hours a day, seven days a week, all year round.”
The ultimate aim, of course, is to be able to manufacture more 3D printed parts for trains. However, the safety regulations applicable to trains are just as strict, if not stricter, than those applicable to aircraft. Deutsche Bahn is therefore working with Formlabs and other partners to develop workflows and materials that can meet these regulatory requirements.
"Our aim is to digitize 10% of all spare parts used in vehicle maintenance by 2030. We'll be able to remanufacture parts on demand in a very short space of time. This will enable us to continue to deliver parts quickly, but also to be more respectful of the environment and treat materials and resources in an environmentally friendly way, which will also solve many other problems," he adds.
3D printing for employees
"Manufacturing aids are essential, because conventional tools all have their limitations," explains Carsten Wolfgramm. "When wagons are dismantled or reassembled, many steps can be optimised to save time or guarantee greater quality and consistency. When dozens of wagons are modernised, the benefits of these tools quickly add up."
"Thanks to 3D printing, we are developing a number of practical tools that help workers to stick pictograms, draw lines or draw points to drill holes without having to spend a lot of time taking measurements. These models make the work of our employees much easier," adds Carsten Wolfgramm.
Previously, these manufacturing aids were made of wood and produced by sawing, sanding and milling, or when metal parts were required, with lathes or milling machines. However, these techniques are much more time-consuming, laborious and expensive.
In addition, 3D printing is benefiting other employees of the group: employees at the DB Fernverkehr site, one of the group's warehouses, who work in materials management and use portable scanners to identify and manage materials. Previously, they had to pick up the scanners and put them down if they wanted to pick something up or use both hands.
They then asked if it was possible to design a holder for this portable scanner so that they could carry it around and always have it to hand. In the end, three different holders were created that could be attached to a bag, a belt or a tool panel. SLS 3D printing is ideal because it adapts perfectly to the shape of the object, and reduces post-processing to dust removal and sanding.
Having a 3D printing workshop in Neumünster enables the team to remain agile and respond quickly to any requests. "We are no longer dependent on long delivery times and supply chains," concludes Carsten Wolfgramm.
www.formlabs.com