www.industryemea.com
04
'24
Written on Modified on
Fives demonstrates Advanced automation for solar tube production
Lock Joint Tube entrusted Fives to supply a completely automatic tube mill to expand its capacity and meet the growing demand for renewable energy.
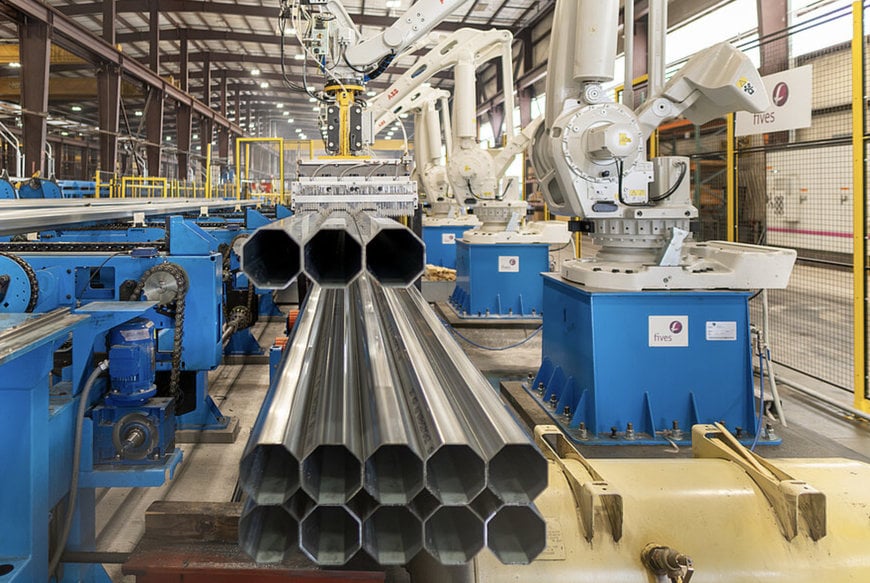
Lock Joint Tube, a leading US steel tube manufacturer, is doubling production at its plant in Temple, Texas to provide solar tubes to key customers who are investing in the solar energy sector. Fives supplied a new OTO tube mill, equipped with the latest-generation technology that ensures the best performance for a wide range of applications.
The global expansion of renewable energy is expected to increase by more than 440 gigawatts in 2023 - the largest increase in history, according to the International Energy Agency. Solar energy accounts for two-thirds of this year’s projected increase in global renewable energy capacity.
“Prior to the installation of the new tube mill, we could only produce small tubes for mechanical and structural applications. We saw a soaring demand from our customers supplying support structures for solar trackers and invested in new technology. The OTO tube mill is fully automated from the entry line to packaging and flexible enough to produce tubes for all types of applications: solar, mechanical, or structural,” says Michael Donnelly, Corporate Project Manager at Lock Joint Tube.
Fives supplied a fully automated OTO tube mill to Lock Joint Tube to double its production capacity up to 4,000 tons per month. The mill was fully operational in spring 2023 and has produced 3,000 tubes per day in both octagonal and square shapes.
It includes a complete entry system from coil loading to accumulator, a single stand motorization forming section, and a double-blade cut-off, ensuring consistent tube production, repeatable high product quality, and reduced energy consumption. The mill is equipped with software modules that suggest the best parameters, monitor production, and adjust them if necessary. The automation is deeply integrated with the mechanics to achieve advanced and cost-effective results.
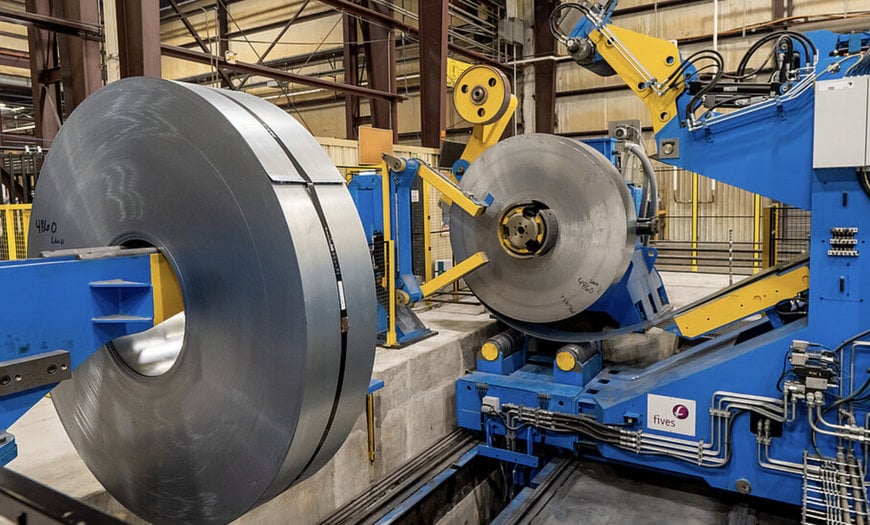
“Automation was our top priority because we wanted to increase safety, reduce heavy work, and speed up production. With the new OTO tube mill, we are doubling our original capacity with a single operator on the line. These exceptional results were only possible because of Fives’ advanced technologies and our successful cooperation,” says Mark Richner, Temple Plant Manager at Lock Joint Tube.
Increased productivity is ensured by Robopack, a fully automated packaging system developed by Fives. The system at Lock Joint Tube consists of a complex configuration, where three robots work synchronized to handle special tube lengths up to 15 m. It offers greater flexibility and quality standards while providing consistent and safe operation.
www.fivesgroup.com