www.industryemea.com
20
'17
Written on Modified on
The way to greater efficiency throughout the value chain? Standard components.
Design engineers are playing a more active role throughout the value engineering process than ever before. No longer do they simply oversee the conceptual aesthetic and ergonomic aspects of a new product design, they are increasingly accountable for the cost of producing a product in the most effective and efficient way possible. As a result, there is an industry-wide drive to engineer more functional products and systems at a lower cost, while continuing to deliver on quality. In this article, Marcus Schneck, CEO at leading standard component manufacturer norelem, explores some of the simple, yet often overlooked, strategies that design engineers can adopt to realise time and cost savings, ensure predictive availability of components, and manufacture more effective products.
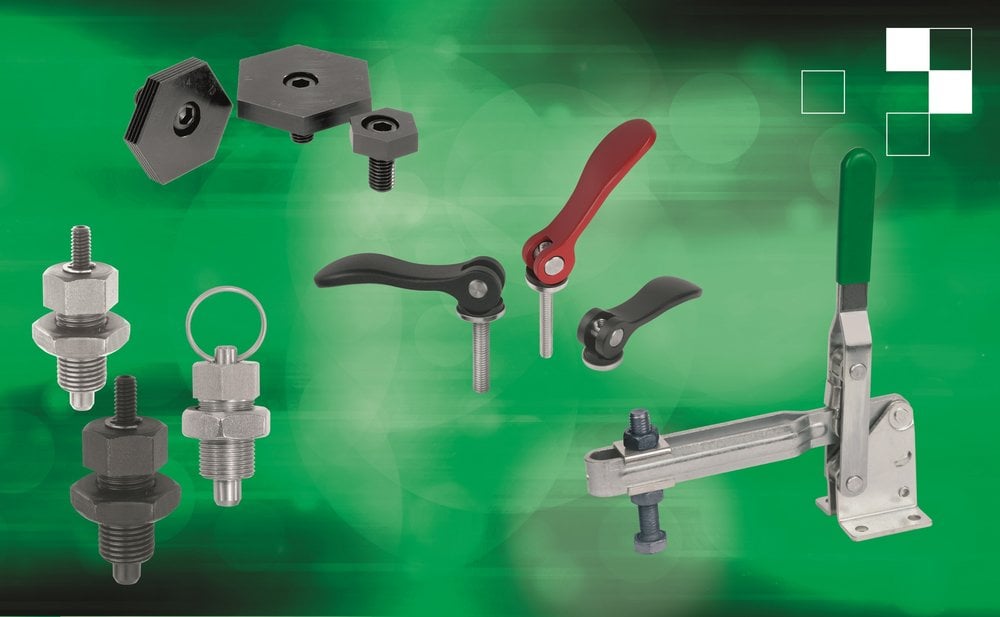
No need to reinvent the wheel, just download existing CAD models
At a time when self-sufficient engineering is the done thing, many businesses are keen to keep as much engineering production as possible in-house, eliminating long lead times and minimising dependency on suppliers. Although this offers engineering firms greater control over the production process, it requires a significant time investment, not to mention a number of additional associated costs.
For example, it is not uncommon for an engineering business to manufacture its own workpiece bolts. Even for a relatively simple component like this, a designer is required to produce a drawing that is appropriate for production, taking into account all of the necessary dimensions. If you consider that the typical process cost for one working hour equates to £50 - £90, depending on the CAD system used and the individual company, this represents at least £15 incurred for each component, even before it has reached production stage. If a business is designing a large number of standard components in addition to this, the additional expense begins to add up.
As a standard component, engineering businesses create additional work by designing their own workpiece bolts when they can be sourced at lower cost and with widespread availability from a professional standard component supplier. Components such as bolts, stop, or clamps which are sourced from an external supplier often come with all of the relevant design data and drawings, which can then be integrated into an existing CAD system. This makes CAD drawings available as static references, eliminating the excess time and cost incurred when producing and configuring these designs manually. If a typical production line favours standard components over bespoke, this can result in significant time and cost savings over time.
Quality as standard
For design engineers, exploring which components are available as standard during the manufacturing process, prior to starting work on their own designs is a worthwhile activity. Partnering with a competent parts supplier can also reap benefits should components fail during production. Rather than re-engineering a component to the same dimensions and designs specified on the CAD drawing, design engineers can just re-order the same component, using a catalogue or reference number. By implementing a pick and place process, it is possible to substantially reduce times-to-market.
It is also important to remember that standard components delivered through an external partner will already be tried and tested with known performance capabilities, reducing any internal test and development time required in house. As a result, standard components very often have easier tensioning and defining positions, which can make for faster assembly times; another marginal gain which can help to make a design engineer even more productive over a period of time.
Lowering design and production costs
A design engineer’s time is precious. In a role that is acutely information intensive, design engineers have enough work to do with technical and computer-based work tasks, without spending yet more time searching for information about a certain component, or redesigning standard components from scratch. This is why norelem first introduced THE BIG GREEN BOOK, back in 2003, as a complete reference guide to standard components for design engineers. Not only does THE BIG GREEN BOOK list norelem’s extensive range of over 38,000 products, of which 98% are available immediately from stock, but it also includes all the information design engineers need to turn their ideas into reality. It has been structured in a logical way to guide readers through an explanation of how standard parts can be integrated to further aid the design process, helping design engineers lower costs and time as standard.
For further information about norelem’s extensive product range, please visit:
https://www.norelem.se/se/sv/Produkt%C3%B6versikt.html