www.industryemea.com
09
'18
Written on Modified on
Measurement: NKE Precision measurements for perfect glazing
The glazing process of car glass parts - windscreens, rear windows, side windows - must provide high levels of quality to ensure durability, quality of the seal and soundproofing of the passenger compartment. It is therefore necessary that the glazing is carried out with great precision, by using quality materials and both automated and, above all, strictly monitored processes.
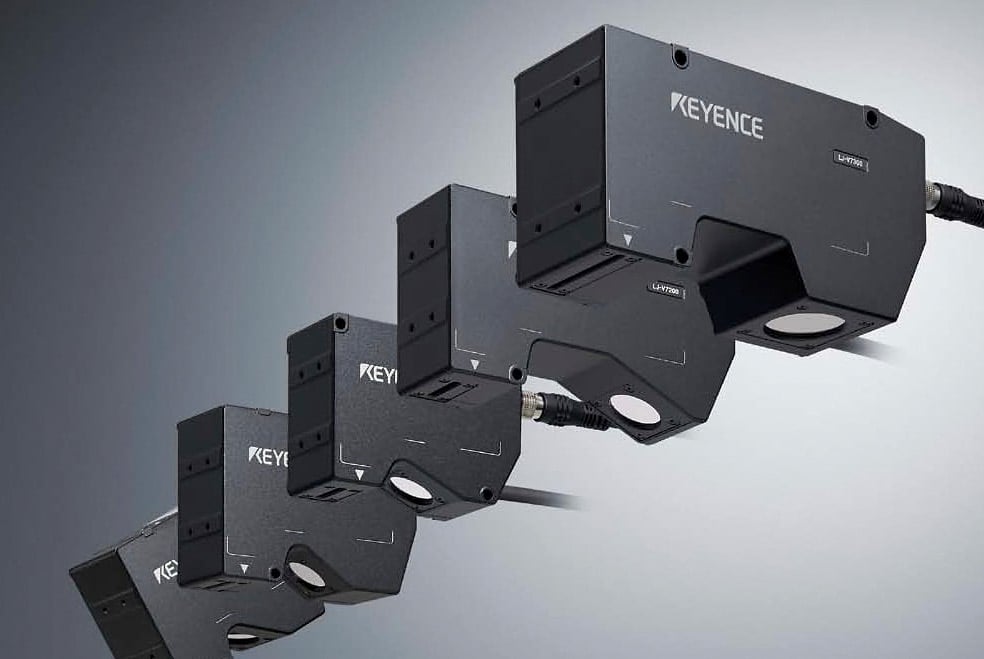
Among the values that make up the Piedmontese company's mission there is the constant commitment to research and development of innovative products able to meet market needs.
Integrated robot-profilometer system
The glazing procedure is a process that, thanks to technological progress, is today highly automated. In addition to the positioning onto the body, one of the most critical phases of this process is the glue coating along the glass perimeter, which is performed by an anthropomorphic robot.
Although it is an automated process, the gluing filling phase must be monitored in real time to ensure that the bead has the uniformity and dimensions compatible with the customer's needs.
To perform quality control of the glue coating process, NKE used a package consisting of a Keyence profilometer and an application developed by a third-party company. Recently, however, the Piedmontese company has decided to improve this process to provide greater performance and quality guarantees to its customers, who are all important companies in the automotive sector.
And so NKE has decided to create a new coating quality control system, by developing its own application and seizing the opportunity to update the hardware component with a profilometer that offers the best performances available on the market. Today the new integrated system is in use in several plants of the FCA group (Mirafiori, Suzzara, Valladolid and Melfi) for the glass assembly on Fiat, Maserati and Iveco cars.
Stable and accurate measurements
As the previously used product had proven satisfactory, the choice of the measuring system fell once again on a Keyence product, in particular on an in-line profilometer of the new LJ-V series. It is a product which, by delivering a blue light laser, enables extremely stable and accurate measurements. The LJ-V offers high sampling rates and can perform measurements on either black or inclined surfaces with low reflectance as well as on highly reflective metal surfaces. The accuracy of the acquired profile is very high even when the target has finishes of various colours and materials.
“The glue coating process must guarantee that the material is supplied without interruptions and that the bead is large enough to guarantee compliance with the requirements set by the customer”, explains Mr Assone.
Thanks to the work of NKE's mechanical department, the LJ-V profilometer was then installed onto a support joint to the robotic arm. “In this way the sensor can follow the glue coating, by measuring in real time the base and height of the profile. Data is transmitted to the newly developed application software, which allows us to collect and display all relevant data, including the measurement of base and height of the profile for each point and the bead's average measure. In this way a profile map is generated, characterised by green, yellow and red colours that indicate whether or not measurements are within the tolerances required by the customer” – continues Mr Assone – “At the end of the process, the software generates a summary screen with the OK-KO type result and all statistical data requested by the customer”.
Easy integration
“The LJ-V profilometer proved to be perfect for this application thanks to the reading accuracy and the high sampling frequency provided” – explains Mr Assone. The integration of the product in the application was simple: “Thanks to the clear and exhaustive manual we understood how to extract data collected by the sensor to input them into our application”.
NKE is satisfied with the quality found in this experience with the Keyence product. For this reason, a possible expansion of the partnership with Keyence is under consideration in order to use its technologies also in other applications. “For example, we are planning to use Keyence OCR cameras in our code-marking system on the chassis and, to this effect, we have already started laboratory tests”, concludes Mr Assone.
www.keyence.it/nke
http://tekinfo.link/r8e8d5c1599
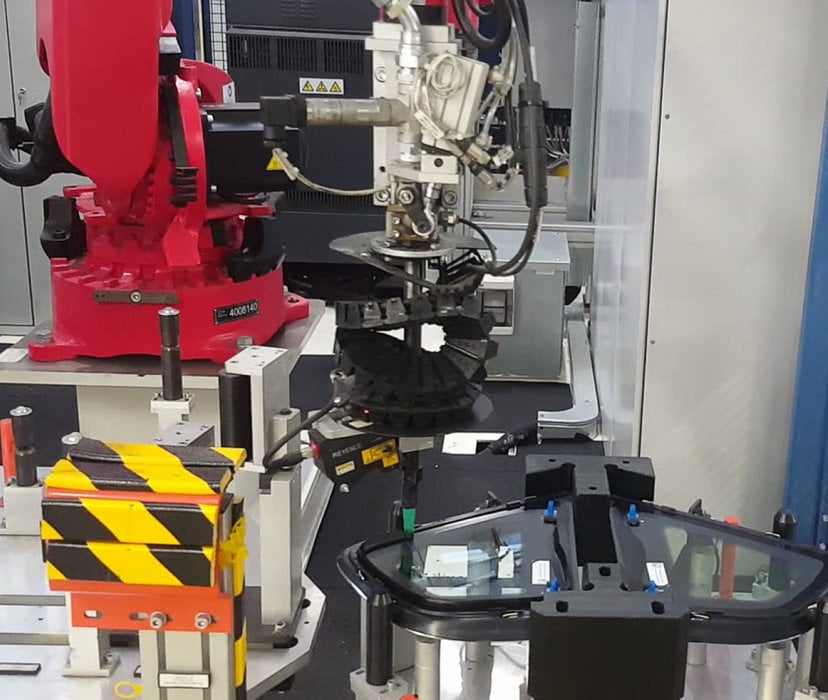
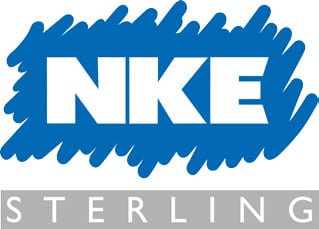
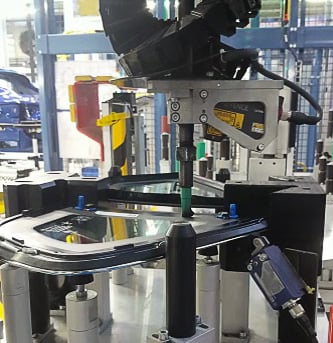
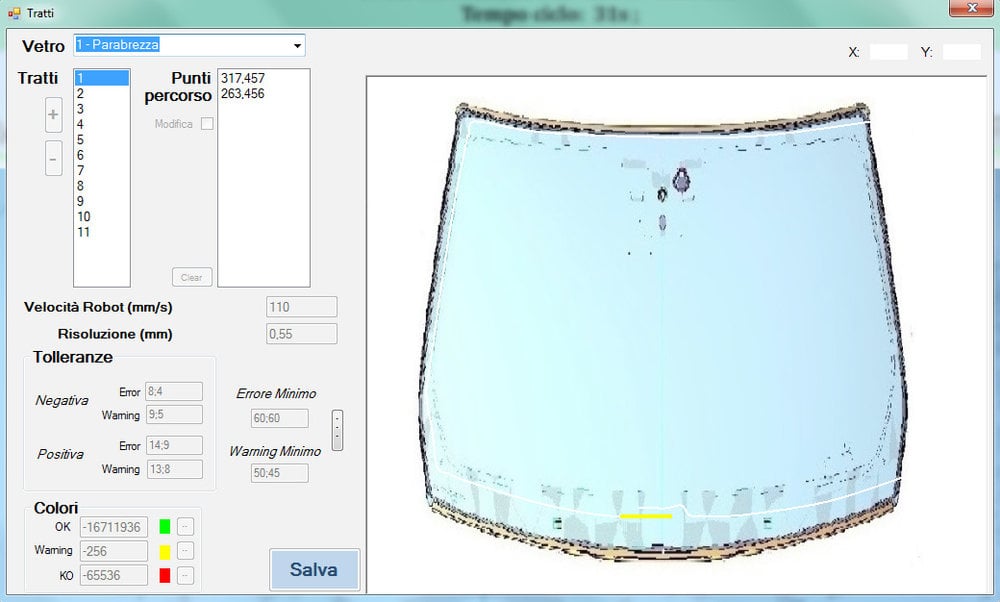
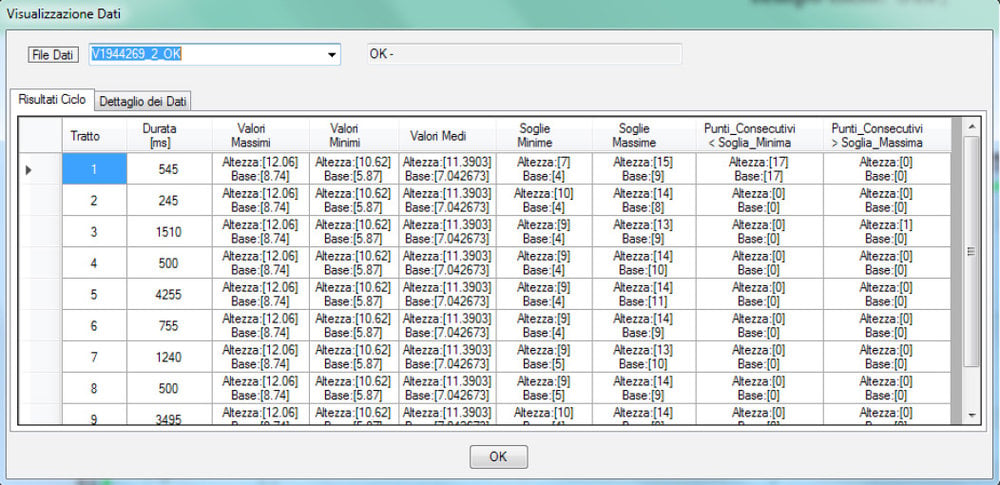