Digitisation of tap changers: Modernising power transformers efficiently
Renewable energies and distributed energy resources are reflections of the era of energy transition. Smart grids with optimal load distribution are now closer to becoming reality. However, what happens to the existing substations in the distribution net-works? Will they able to handle the requirements, now that power quality concerns are emerging more and more? What is to happen to the older systems which now still operate manually or semi-manually? What is to be done about distribution networks with power transformers that are based on different technologies?
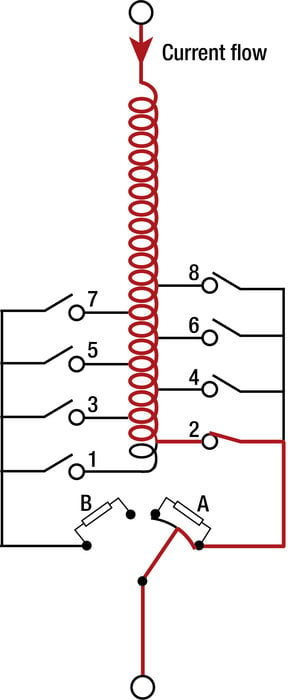
Tap changers for power transformers
In this article two different types of tap changers are considered. A distinction is made between the type that switches with no load (NLTC as no-load tap changer) and the type that switches without interrupt-ing the load, so it switches back and forth between dif-ferent transformation ratios while still under load (OLTC as on-load tap changer). In general, taps on the trans-former are routed to the tap changer, depending on the operating currents to be handled. The mechanical connection of the taps to the tap changer is implemented as a rotary drive in this ex-ample. This is activated ei-ther manually or semi-manually or else by means of electrical signals. 1 or 3-phase tap changer are used, normally selected and installed depending on the load capacity or switch con-figuration (star or delta).
Picture 1 : Simplified diagram of tap changer
Technical concept:
Within a measurement task, an accurate meas-urement device, with ac-curacy class 0.2, is used to measure the 3-phase secondary load of the transformer of a medium voltage station. The measurement values are passed by a converter to the measurement device and processed algorith-mically. They are then displayed and optionally passed to a control sys-tem (SCADA).
In parallel to the meas-urement task, the posi-tion of tap changer is captured directly by the integrated PLC using the IEC61131 protocol. Commands issued by the higher level control system then activate the outputs of the integrated PLC and control the in-crease or reduction of the secondary voltage of the transformer. The mo-tor of the tap changer starts to turn. This causes the voltage level to change and this in turn is monitored both by detecting the position and directly detecting the load.
The 2-in-1 concept, combining a highly accu-rate measurement de-vice with an integrated PLC, enables overhead and costs to be reduced and allows the energy automation task to be optimally implemented.
The requirement
In existing substations, the installation can consist of an interconnection of many dif-ferent technologies, suppli-ers and equipment model years. Networks have been expanded over the years and have not always been modernised when they were expanded. This has often been due to reasons of cost and lack of resources. As a result, the initial require-ment may be to automate the tap changer appropriate-ly, depending on the higher-level automated voltage control of the high-voltage network. The requirements may be similar to the following example:
- Transfer accurate data in quasi-real-time, report-ing the position of the tap changer to a SCADA system
- Automated control of the existing tap changer via remote control
- Manual control of the ex-isting tap changer via remote control
- As well as the automated remote access, a manual and local access capa-bility in case of on-site maintenance and repair
Problem description
Due to frequent load chang-es and the relatively high mechanical and electrical stresses put on on the com-ponents of a tap changer, it is subject to wear, which makes it susceptible to fail-ure as well as being maintenance-intensive. Fur-thermore, in legacy sys-tems, the tap changer is frequently not yet fully au-tomated by means of sys-tem integration, in other words not directly net-worked via a SCADA. Load peaks can cause the tap changer to immediately switch levels even when this is unnecessary. This in turn leads to increased wear and has a negative effect its susceptibility to failure both from a technical as well as cost point of view. For this reason, efficient control of the tap changer is essential for ensuring long service life.
Another possible aspect of the problem of a lack of networked automation can occur if the equipment in the various substations is sourced from different man-ufacturers. Due to the dif-ferent equipment designs, different sensor technolo-gies have to be used to re-turn the exact position of the tap changer to the SCADA. This may possibly mean that the automation solution in each substation of the same network will not based on identical components. Also in many cases, the technical skills in in terms of energy automation avail-able on-site are not always sufficient to be able to im-plement this type of project without support.
One last aspect of the prob-lem description is based on the fact that substations are frequently not connected to the digital communications network. Because of this, it is recommended to split the networking and hence the digitisation of the data into implementation steps. The following three steps can serve as a proposal:
(1) Local Automation: Stor-age of the data via data logger in the substation. Retrieval of the data can then be done locally and on demand
(2) Remote Monitoring: Transfer of selected da-ta, limited to a small specific data set, via power line, EDGE, GPRS, etc.
(3) Remote Control: Remote monitoring and monitor-ing control based on broadband communica-tion via LTE, fibre optics, etc.
The technology available for modernisation
To implement the automa-tion and digitisation of a tap changer, and taking all as-pects of the previously de-scribed requirement and problem description into ac-count, a highly precise measurement device with accuracy class 0.2, is cou-pled with a soft-PLC. This coupling or integration in this case is done by using the CENTRAX CU3000 or CENTRAX CU5000 2-in-1 device from Camille Bauer which act as the basic plat-form for the energy automa-tion solution. The measure-ment device performs the measurement of the electri-cal parameters, voltage and current consumption. Addi-tional measurements and data are also generated by the measurement device and used to evaluate the quality of the electrical pa-rameters, such as for ex-ample harmonics, imbal-ances, power factors, etc. Energy values are also vis-ualized directly. The meas-urement values are either stored locally (Local Auto-mation) or directly transmit-ted to the database or SCADA system via power line (Remote Monitoring) or Modbus (Remote Control). In the case of Remote Moni-tor and Remote Control ap-plications, the system is thus always kept up to date of the voltage and current values in quasi real time.
To implement the mainte-nance access previously described in the require-ments, the tap changer is controlled by the soft-PLC of the CENTRAX CU3000 or CENTRAX CU5000. The required trigger is generat-ed either manually or by the SCADA system based on the electrical values re-turned by the measurement device of the CENTRAX CU3000/5000. This acti-vates the tap changer caus-ing the voltage to be either increased or reduced. The position of the tap changer has to be treated in the con-text of the measurement value in order to prevent any disruption or switching error. This plausibility check (control loop) is implement-ed by checking the mechan-ical position of the tap changer. Because of the differences in the design of various on-load tap chang-ers, values are sampled from either axial signals, resistance values, BCD coded signals or the ratio between the primary voltage Up and the secondary volt-age Us, which is then com-pared to the values in the tap changer table.
Costs and benefits
With the 2-in-1 approach, the advantages from a cost/benefit point of view are evident. The integration of a highly precise meas-urement instrument and a soft-PLC in a single housing means that the component cost alone is reduced by 50%. Procurement and lo-gistics-centred processes are optimized and compo-nents that are not directly compatible are eliminated at the same time. Furthermore, the functional integration has an immediate positive impact on planning and im-plementation costs, both fi-nancially and time-wise. The length of service life and reproducibility of all used components have a positive effect on the overall result The local control of the tap changer takes the corresponding status of the communication network into into account whereby each tap change is recorded with a timestamp. This creates reliable data which is also kept on record to enable preventive as well as cost-optimised maintenance.
Digitisation and automation approach using position monitoring of the tap changer by means of resistive signal processing
More information available from www.camillebauer.com/starkstrommonitoring