www.industryemea.com
26
'18
Written on Modified on
Morgan Advanced Materials delivers comprehensive supply chain solution for medical and dental implant market
The Technical Ceramics business of Morgan Advanced Materials is advising manufacturers of medical and dental components to consolidate their supply chains, in response to an imminent surge in demand within the implant market.
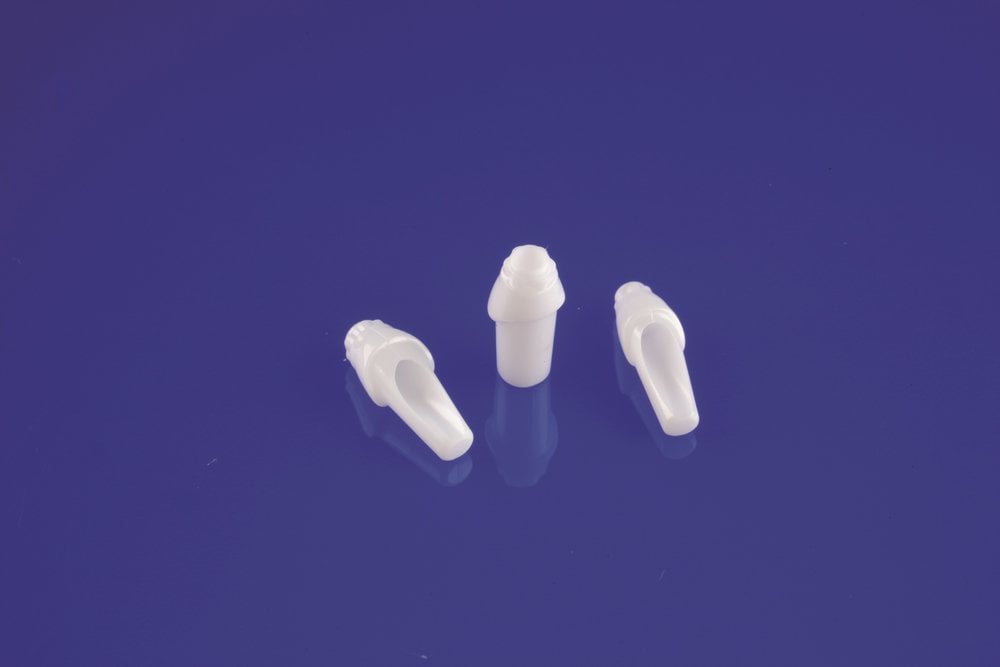
A global specialist in advanced ceramic materials, Morgan’s proprietary zirconia grade is ISO 13356 approved, ensuring full compliance with stringent regulations around the production of medical implements. Such applications include surgical tips that are widely used in microwave ablation operations for cancer treatment, as well as implantable casings that can become part of a miniaturised bioelectronic device used in cranial and spinal implants. Unlike other material suppliers, Morgan’s Technical Ceramics business has the capability to deliver ceramic to metal assemblies utilising molybdenum manganese (MoMn) brazing and metallised ceramics as well as active alloy brazing with Morgan Technical Ceramics’ extensive range of active braze alloys (ABAs).
Moreover, Morgan’s Technical Ceramics business is embracing the ‘metal free concept’ for dental implants that is widely acknowledged as the next phase in dental implant technology, where its industry-leading expertise in ceramic materials is enabling the business to meet future demand.
This has been made possible by Morgan’s continued investment in Ceramic Injection Moulding (CIM) technology, which is allowing for complex parts to be produced in high volumes to tolerances as low as 0.5%. Compared with conventional methods for manufacturing engineering ceramic components, where tolerances are typically between 1-2%, this approach eliminates the time and cost associated with additional machining of components, resulting in high tolerance parts in complex geometries for manufacturers within shorter lead times.
Many implants now incorporate electrical circuits as part of their design, adding further complexity to the supply chain due to the requirement for specialist brazing. Morgan’s Technical Ceramics business has world-leading expertise in this area, and its global presence of manufacturing sites located in the UK, Germany, and USA, are helping implant manufacturers to consolidate their supply chains while providing reassurance that rigorous quality control standards are upheld.
Dr Yifei Zhang, Business Development Manager at Morgan’s Technical Ceramics business explained: “We are expecting a real increase in demand for medical implants and our integrated business model means we are well positioned to help accommodate future demand. By working with a single supplier, as opposed to a network of multiple suppliers, this can facilitate time and cost savings, shorter lead times and better component quality. Our longstanding relationship with the medical sector makes us the ideal partner for manufacturers of implants.”
For further information, please visit: http://www.morgantechnicalceramics.com/Medical