www.industryemea.com
25
'18
Written on Modified on
Interroll and Conveyroll – walking the extra mile for upgrading Andrea’s distribution
Sant’Antonino, Switzerland; Mexico City, Mexico September 6 2018. Mexico’s leading shoe catalog brand Andrea dramatically reduced delivery times and improved their internal processes by boosting their level of precision and quality of their shipments, with Interroll and Conveyroll enabling them to make the right steps in a retrofit project.
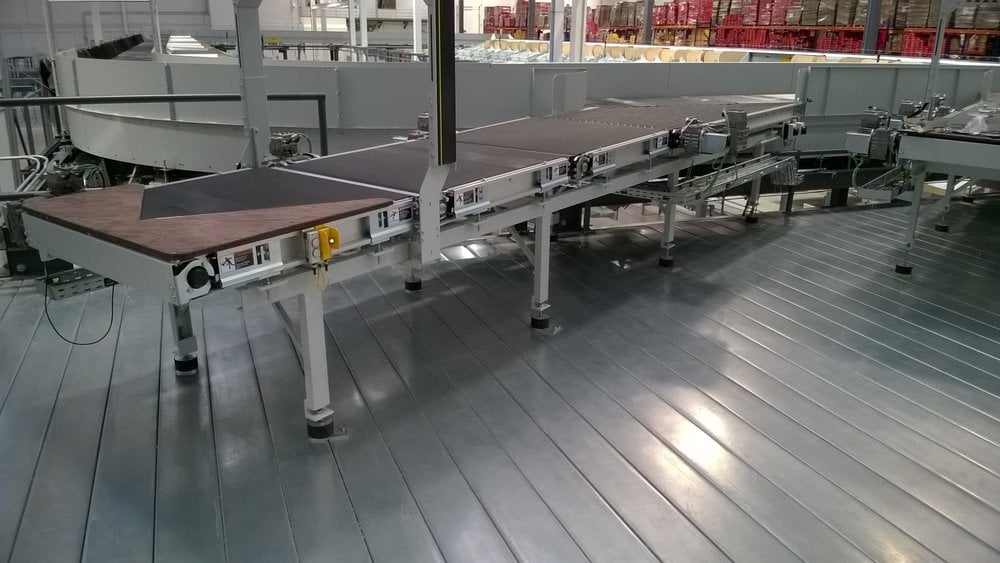
To face this challenge, Interroll and Conveyroll worked on the design of a logistics solution that would allow Andrea not only to make shipments more efficiently, but also to double check each shipment to ensure that both the product and the address to which it would be sent were correct.
"After reviewing the client's requirements, we set ourselves the task of designing the solution that would adapt to the installed capacities of the client. They wanted to improve their delivery times while increasing the precision of their shipments. This was something that was taking too much time and too much effort, considering how important it is for them to deliver as fast as they can and with minimal errors” commented Alfonso López of Conveyroll.
The design and implementation of the project took about 18 months (from its conception until its full operation). "We worked with the Conveyroll team to design a solution that would allow Andrea to impact their business indicators and significantly improve their delivery times." Commented Stephen Cwiak, responsible for the project at Interroll.
The final system configuration and scope of the project for Andrea includes three semi-auto induction conveyors to load items onto the crossbelt sorter. The sorter loop with a total throughput of 6.000 units per hour acts as the “heart” of the system transferring the goods via the crossbelt sorter carrier to one of 100 chutes dispersed around the loop. The machine level controls provide a smoothly controlled system that uses a scan tunnel to identify the goods via a bar code on each item. The bar code information is used to communicate with the Warehouse Management System in order to deliver the goods to the proper destination.
Smart retrofit solution tripled Andrea’s material flow capacity
Thanks to the installed technology, Andrea's material flow operations are now 3 times more efficient and delivery times of previously between 4 and 7 days were reduced to 2 to 3 days for delivery.
Also, the order errors reached a minimum thanks to the duplicated review configuration programmed in the system, thus guaranteeing that each package arrives at its correct destination. "During the analysis and planning session, we reviewed the minimum and maximum sizes, as well as the weight range in order to design a solution that could meet all the requests," added Alfonso López.
The material flow solution has 200 outputs that allow Andrea to generate delivery cycles to all of Mexico’s cities, either through their own stores or directly to the final customer. The design of the solution was made in such a way that it easily allows modification or upgrades, making it possible to double its capacity in the short term.
"This has been a very interesting project, given the characteristics of Andrea's systems, their operation and the needs presented. It has been very rewarding to work with the Conveyroll team to offer this solution "added Stephen Cwiak
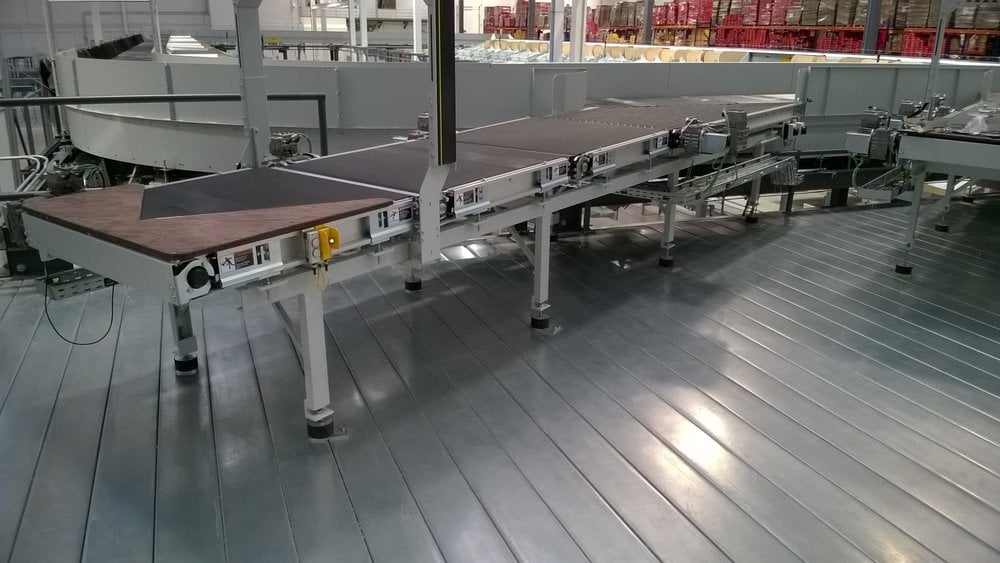
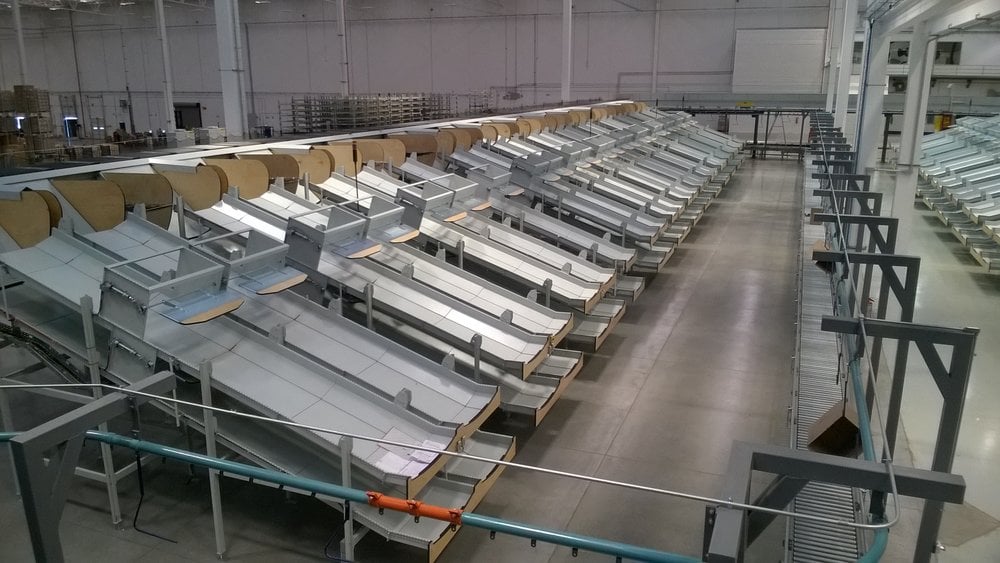
Caption left: Scan tunnels identify the goods via barcode
Caption right: Andrea’s sorter loop is the “heart of the system and has a total throughput of 6,000 units per hour