www.industryemea.com
15
'10
Written on Modified on
Director for complex conveyor tasks: decentralised inverter controls cyclic operation and positioning
For the very first time, the new conveyor belt systems of the INOTEC AP GmbH in Hesse achieve the wide range of functions of servo drive technology using decentralised inverters. Integrated drives from NORD DRIVESYSTEMS enable complex functions such as cycling, positioning and start-stop operation to be realised with cost-effective units.
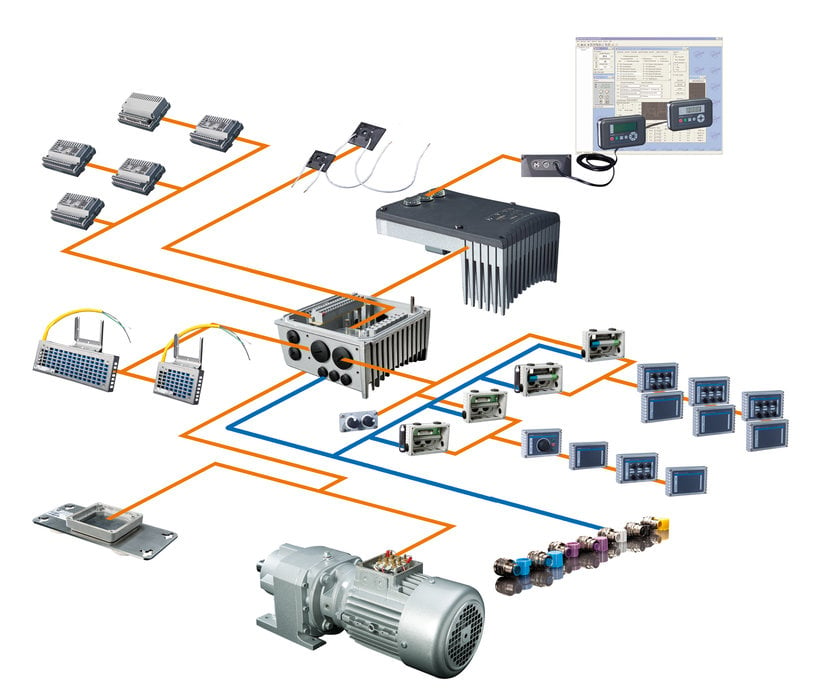
Inotec AP, an innovative manufacturer of special systems for a wide range of industrial applications has developed an intelligent automation system, which is suitable for a highly varied range of conveyor applications. On the one hand, the modular structure enables the simple adaptation of the new TAKTFLEX conveyor belt system to individual customers´ requirements with regard to length, width and belt material as well as allowing short delivery times. On the other hand, the implementation of various sophisticated functions in combination with the SK 200E frequency inverter series allows a wide range of industrial application and therefore distinguishes this system from conventional conveyor systems. The system is supplied complete with a convenient Siemens S7 program and can be commissioned within a very short time. End users merely need to install the power supply and bus cables. Complex cabling between a control unit in the switching cabinet and the drive unit is no longer needed, thanks to the integrated frequency inverter.
Drive technology tailored to the application
The heart of the system is the NORD drive technology. The optimum size of the drive unit is designed to cater for the special requirements of the application. Conveyor belt speeds cover a wide range from about 0.5 m/min. to 100 m/min. Because of the large overload reserves, the correspondingly powerful worm gear motor can have very lean dimensions; typical overload capacities are 200% for 3.5 sec and 150% for 60 sec. The gear motor is controlled by a suitable SK 200E series frequency inverter which is mounted directly on the terminal box and preferably controlled via Profibus DP. A control display allows the operator to select the functions necessary for the process and to change parameter values. Especially for this purpose Inotec AP has developed a Simatic S7 program, which includes all functions necessary to control the frequency inverter.
Versatile functions for modular conveyor systems
The SK 200E frequency inverter series includes a wide range of models, which are graded according to their performance. Even the basic model SK 295E provides a wide range of functions such as sensorless current vector control, POSICON positioning control, an integrated brake chopper and a control unit for an electromagnetic brake. In combination with individually extendable function modules, sophisticated conveyor applications can be implemented, which up to now could only be realised with expensive servo technology. The compact decentralised inverter controls the main operating modes such as speed regulation, cycling, positioning (precision ±0.5 mm) and start-stop operation. In addition, the SK 205E allows automatic referencing of the incremental encoder used for positioning. By means of an intelligent control unit, referencing can be carried out during operation in the form of a deliberate reference run or referencing “on-the-fly” according to requirements. The frequency inverter is equipped with four freely programmable parameter sets in which the settings for the various functions can be made (positioning function, ramp times, frequencies, selection of process data, digital functions etc.). For local manual operation the frequency inverter can be fitted with a potentiometer unit or an I/O extension. The necessary modular components can either be integrated into the inverter, mounted on it, of installed in the vicinity of the inverter.
Simple parameterisation for complex control tasks
The SK 205E is commissioned with the one-off loading of standard values e.g. motor data. After this, the application-specific parameter values are transferred to the SK 205E via Profibus DP with each new start. The settings for the main operating modes of the system are stored in three parameter sets. The functions necessary for normal inverter operation are activated by the selection of the corresponding parameter set. The values for “reference point run” and “on-the-fly referencing” (Reset Position) are stored in a fourth parameter set. During operation, the double function of this parameter set only requires an adaptation of individual functions as required. These adaptations are coordinated by the control unit and take place in the background, unnoticed by the user. Reference point runs are triggered by the user via the visualisation unit. In contrast, automatic referencing is activated in cyclic operation by means of a timer which is implemented in the control unit. Subsequently, cyclic operation is automatically resumed.
A well coordinated team – the control program and the drive electronics
Together, the control unit of the TAKTFLEX system and the frequency inverter form a high performance unit. The basic functions set in the parameter sets of the frequency inverter, such as positioning (absolute positioning), cyclic operation (relative positioning), start-stop operation, constant running and referencing (optionally with set-up mode or on-the-fly referencing), are activated via a control word in the same manner as e.g. enabling of selection of the direction of rotation. In addition, the position values and frequencies, or alternatively the correspondingly parameterised BUS I/O bits, e.g. the reference run function are communicated in the process data. For further digital functions, the PLC accesses two bits which can be parameterised in the control word of the SK 205E. For example, in order to carry out the next positioning step in cyclic operation bit 8 is linked with the function “Sync. Position array”. The system achieves ultimate flexibility though the possibility of online specification of certain parameter values such as the function of a digital input. Thanks to this, double functions of a sensor signal (e.g. digital input 1, function "reset position" or function "reference point”) can be implemented with a minimum of installation and wiring.
Flexible communication possibilities
The SK 205E provides various control interfaces. In the simplest case, the frequency inverter can be configured for simple start-stop operation independent of a control unit with the aid of a few DIP switches. For all other requirements, the SK 205E can be controlled via digital or analog I/Os or a wide range of field bus systems. In the most sophisticated version of the TAKTFLEX system, the frequency inverter communicates with the PLC via a Profibus DP interface. By means of a Profibus DP gateway implemented in this interface, up to four frequency inverters can be connected to each Profibus DP module. With a possible total of 122 Profibus DP modules, up to 488 frequency inverters can be directly controlled via a single bus system.
Company background: inotec automation & inspection technology
inotec AP GmbH was founded in 1996 in Wettenberg in the German state of Hesse. It has developed from a design provider to a manufacturer of complete systems for automation and inspection technology. From its first staff of three, the company has grown to its present total of eleven employees in the fields of development, design, production and sales. Based on many years experience in the construction of special machinery, in addition to customised solutions inotec AP also supplies various automation products in the form of system components. The modular TAKTFLEX system now opens up the segment of series-produced systems. Short paths between design and production enable this SME to satisfy the highest demands for quality and short delivery times.
Drive technology tailored to the application
The heart of the system is the NORD drive technology. The optimum size of the drive unit is designed to cater for the special requirements of the application. Conveyor belt speeds cover a wide range from about 0.5 m/min. to 100 m/min. Because of the large overload reserves, the correspondingly powerful worm gear motor can have very lean dimensions; typical overload capacities are 200% for 3.5 sec and 150% for 60 sec. The gear motor is controlled by a suitable SK 200E series frequency inverter which is mounted directly on the terminal box and preferably controlled via Profibus DP. A control display allows the operator to select the functions necessary for the process and to change parameter values. Especially for this purpose Inotec AP has developed a Simatic S7 program, which includes all functions necessary to control the frequency inverter.
Versatile functions for modular conveyor systems
The SK 200E frequency inverter series includes a wide range of models, which are graded according to their performance. Even the basic model SK 295E provides a wide range of functions such as sensorless current vector control, POSICON positioning control, an integrated brake chopper and a control unit for an electromagnetic brake. In combination with individually extendable function modules, sophisticated conveyor applications can be implemented, which up to now could only be realised with expensive servo technology. The compact decentralised inverter controls the main operating modes such as speed regulation, cycling, positioning (precision ±0.5 mm) and start-stop operation. In addition, the SK 205E allows automatic referencing of the incremental encoder used for positioning. By means of an intelligent control unit, referencing can be carried out during operation in the form of a deliberate reference run or referencing “on-the-fly” according to requirements. The frequency inverter is equipped with four freely programmable parameter sets in which the settings for the various functions can be made (positioning function, ramp times, frequencies, selection of process data, digital functions etc.). For local manual operation the frequency inverter can be fitted with a potentiometer unit or an I/O extension. The necessary modular components can either be integrated into the inverter, mounted on it, of installed in the vicinity of the inverter.
Simple parameterisation for complex control tasks
The SK 205E is commissioned with the one-off loading of standard values e.g. motor data. After this, the application-specific parameter values are transferred to the SK 205E via Profibus DP with each new start. The settings for the main operating modes of the system are stored in three parameter sets. The functions necessary for normal inverter operation are activated by the selection of the corresponding parameter set. The values for “reference point run” and “on-the-fly referencing” (Reset Position) are stored in a fourth parameter set. During operation, the double function of this parameter set only requires an adaptation of individual functions as required. These adaptations are coordinated by the control unit and take place in the background, unnoticed by the user. Reference point runs are triggered by the user via the visualisation unit. In contrast, automatic referencing is activated in cyclic operation by means of a timer which is implemented in the control unit. Subsequently, cyclic operation is automatically resumed.
A well coordinated team – the control program and the drive electronics
Together, the control unit of the TAKTFLEX system and the frequency inverter form a high performance unit. The basic functions set in the parameter sets of the frequency inverter, such as positioning (absolute positioning), cyclic operation (relative positioning), start-stop operation, constant running and referencing (optionally with set-up mode or on-the-fly referencing), are activated via a control word in the same manner as e.g. enabling of selection of the direction of rotation. In addition, the position values and frequencies, or alternatively the correspondingly parameterised BUS I/O bits, e.g. the reference run function are communicated in the process data. For further digital functions, the PLC accesses two bits which can be parameterised in the control word of the SK 205E. For example, in order to carry out the next positioning step in cyclic operation bit 8 is linked with the function “Sync. Position array”. The system achieves ultimate flexibility though the possibility of online specification of certain parameter values such as the function of a digital input. Thanks to this, double functions of a sensor signal (e.g. digital input 1, function "reset position" or function "reference point”) can be implemented with a minimum of installation and wiring.
Flexible communication possibilities
The SK 205E provides various control interfaces. In the simplest case, the frequency inverter can be configured for simple start-stop operation independent of a control unit with the aid of a few DIP switches. For all other requirements, the SK 205E can be controlled via digital or analog I/Os or a wide range of field bus systems. In the most sophisticated version of the TAKTFLEX system, the frequency inverter communicates with the PLC via a Profibus DP interface. By means of a Profibus DP gateway implemented in this interface, up to four frequency inverters can be connected to each Profibus DP module. With a possible total of 122 Profibus DP modules, up to 488 frequency inverters can be directly controlled via a single bus system.
Company background: inotec automation & inspection technology
inotec AP GmbH was founded in 1996 in Wettenberg in the German state of Hesse. It has developed from a design provider to a manufacturer of complete systems for automation and inspection technology. From its first staff of three, the company has grown to its present total of eleven employees in the fields of development, design, production and sales. Based on many years experience in the construction of special machinery, in addition to customised solutions inotec AP also supplies various automation products in the form of system components. The modular TAKTFLEX system now opens up the segment of series-produced systems. Short paths between design and production enable this SME to satisfy the highest demands for quality and short delivery times.
Fig. 1: TAKTFLEX modules and versions for a wide range of applications
Fig. 2: A gear motor with directly mounted SK 205E frequency inverter and external fan controls cyclic conveyor operation
Fig. 3: Primary operating modes of the conveyor system with fully integrated drive unit
Fig. 4: The system, consisting of decentralised frequency inverters and modules enables cost–effective implementation of a wide range of functions as well as connection to all common field bus systems.
|