www.industryemea.com
22
'18
Written on Modified on
Askja Audio Overcomes the Limitations of Traditional Manufacturing by 3D Printing Ultra-Deluxe Sound System
Sound Decision
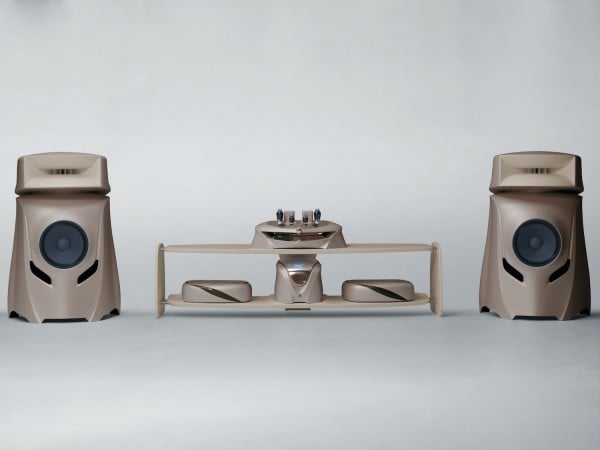
Didier Kwak, Founder and President of Askja Audio
Executive Summary:
Didier Kwak is an established figure in the French audio-visual industry. Having worked with some of the biggest movie producers, he has always strived for the highest resolution imagery and audio. Aware that the quality level of acoustic technologies available to him did not meet the standards he could achieve in his visual work, he decided to embark on a mission to design and create an ultra-high-end sound system. Launching Askja Audio, Kwak discovered that Stratasys 3D printing technology would be pivotal in bringing his flagship, ‘Origin’, audio system to market.
Benefits/Value:
• Stratasys FDM additive manufacturing enables manufacture of low-volume complex parts quickly and cost-effectively
• Ability to produce complex shapes not possible with traditional production methods
• Rigidity and stability of Stratasys ASA and ULTEM 9085 materials key to producing high-level sound emission, eliminating any unwanted resonances or vibration inside the enclosures of the electronic devices
• Additive manufacturing also enables Askja to add personalization options for clients
A recognized figure within the French audio-visual industry thanks to his use of highly sophisticated imagery, Didier Kwak is perhaps best known for his work on movies and adverts – notably his collaboration on the film, The Fifth Element, as well as his association with prestigious brands like Chanel. Using meticulous and precise techniques, Kwak is renowned for his ability to convey messages and emotions through his image work with the highest production resolution achievable. However, he decided several years ago that the quality level of acoustic technologies available to him, would have some way to go before it matched the intensity achievable in his visual work.
“For me, the level of audio quality has drastically decreased since the 1970s with the use of cheaper materials by audio system manufacturers and the rise of digital music streaming services largely to blame,” he explains. “For years, manufacturers have developed increasingly powerful devices whilst using substandard materials and, as a consequence, the output does not meet quality expectations.”
This inspired a thirst to learn about psychoacoustics – the perception of sound and its physiological effects – which, in the early 2000s, would eventually see Kwak, as a hobbyist, create his own personal audio system using wood and metals.
Spurred on by encouraging feedback from industry colleagues impressed by the sound emitted from his homemade effort, Kwak decided it was time to get serious and develop a professional audio system for the audio-visual industry. As he puts it, a product that would ‘bridge exquisite sound and art’. This culminated in 2014 with the creation of Askja Audio, of which Kwak is both founder and president. So began the quest to develop an ultra-high-end audio system that would meet his exacting standards for the utmost perfection. This would ultimately result in the high-end Askja Origin which was designed and developed thanks to Stratasys FDM additive manufacturing.
Challenges with traditional manufacturing processes
With the support of Swiss Fibertec, a company specialized in designing carbon fiber and composite molds and partner of the Sauber F1 Team, Kwak worked on the design of the audio system to achieve the ultimate sound aerodynamics. However, the choice of materials, size, shapes and the manufacturing processes, presented a fundamental challenge.
In particular, the manufacture of the hybrid amplifier was critical. A unique design was developed to achieve both a superior sound quality together with an aesthetically pleasing look. But Askja’s team did not want to produce the design with conventional manufacturing methods using traditional materials like wood and metal. Indeed, the complex design of this large format amplifier incorporated a very unusual curved shape that raised questions as to how it could actually be manufactured.
A fundamental challenge required production of several parts, that would have necessitated assembly with obvious joints. This would not only have negatively impacted its look, but also the vibratory continuity vital to achieving a perfect sound.
“We initially considered molding the only viable solution to produce the hybrid amplifier, but at 80 cm x 65 cm x 27cm, the part was too complex to be removed from the mold,” explains Kwak. “After some research, we realized that Stratasys FDM additive manufacturing offered us the ability to produce any complicated shape with no geometric limitation. This capability proved to be the cornerstone to realizing the design and production of our hybrid amplifier, filters and power supply unit.”
Kwak used the large-scale Stratasys Fortus 900mc Production 3D Printer to produce the Origin design and final parts. Stratasys’ ULTEM 9085 and ASA materials were selected, thanks to their dimensional stability and toughness. These enable the audio signal to only travel in the electronic components without mechanical distortion from the enclosure. Such mechanical distortions can often alter the electronic qualities of components, and therefore the resulting sound.
Offering strong rigidity, ULTEM 9085 was used to prevent any unwanted resonances and vibrations in the amplifier. Meanwhile, ASA’s more mellow features bring balance between stiffness and handling to the system’s core design.
Large and complex parts produced without constraint
Using the Fortus 900mc, Askja was able to 3D print very large and complex parts without constraint. Leveraging proven methods adopted by Ferrari’s engineers, Askja modified the design of significantly complex part assemblies and consolidated these to just a few large parts. According to Kwak, the huge time and costs associated with tooling manufacture would have made the production of such parts unfeasible.
“The Askja Origin’s hybrid amplifier is one of the biggest parts and features a complicated, unusually-shaped design – two issues that made it virtually impossible to produce via conventional methods. We were looking at several months wait and an incredible amount of expense just to produce the tooling,” he explains. “Additive manufacturing allowed us to overcome tooling and traditional manufacturing limitations and produce unusually-shaped final parts on-demand, cost-effectively. Indeed, we had the parts produced and in our hands within several days – something that would have been physically impossible without Stratasys 3D printing.”
Such short lead times also made it possible for Askja to be more experimental at the design phase – testing concepts and making any necessary iterations to optimize the final designs prior to final production.
Customization – a must for a luxury product
Additionally, Stratasys FDM additive manufacturing enables Askja to add surface customization options for customers. This, for example, makes it possible to create ridges on top of the power supply unit for the addition of ‘skins’ made from materials such as leather – without affecting the efficiency of the sound system.
“The unique quality of our audio system ranks Askja within the luxury goods category, but the use of additive manufacturing to permit clients to customize their own design is a tremendous asset,” explains Kwak. “We even had a request from one client to add diamonds all around the surface of the hybrid amplifier, which was made possible by incorporating a layer of holes in which the diamonds were embedded.”
Thanks to this technology, Askja has developed a unique range of high-quality audio systems, and so delighted by the results, the team is now undertaking new designs to release in the coming years. “The use of Stratasys FDM 3D printing enables us to bring our creative design aspirations to reality, and beyond that it also forms a great part of Askja’s unique selling proposition as no other audio system companies have ever designed their final products with additive manufacturing,” Kwak concludes.
www.askja-audio.com