www.industryemea.com
04
'11
Written on Modified on
Volvo cars increases the tempo in its car factory using iX
Just as with road traffic, planning, movement and tempo are also decisive when manufacturing cars. Volvo Cars is using Beijer Electronics' HMI solution iX to optimize the flow and thus rationalize its bodywork factory. The intuitive iX system is being used not only by operators and other production staff, but also in administration.
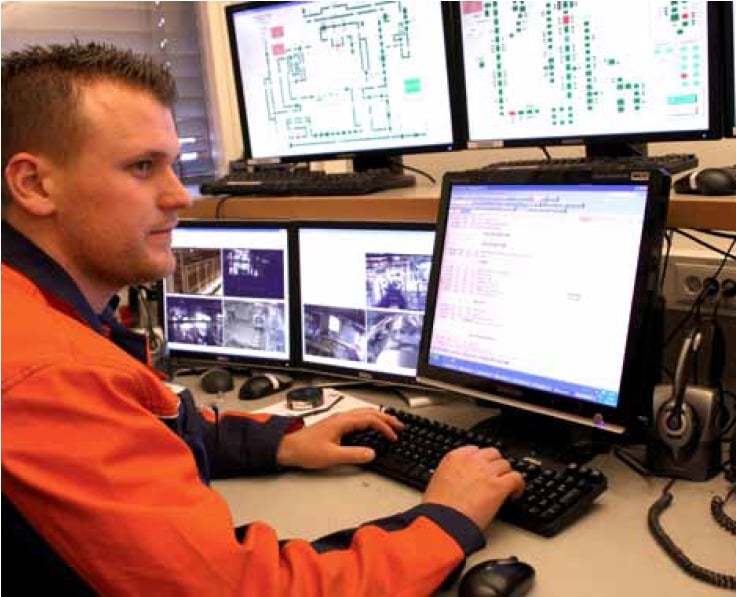
The heart of the Swedish car industry is in Västra Götaland. In Gothenburg, Volvo Cars builds larger cars such as the XC90, S80 and V70. The smaller models in its range, such as the C30, V50, S60 and XC60, are manufactured at the plant in the Belgian city of Ghent. The Torslanda factory, which currently employs around 3,000 people of 41 nationalities, actually consists of three closely interconnected factories. The first one manufactures the bodies, which are painted in the next one before moving on to final assembly. Volvo Cars' production is order-based. Following a few tough years for the car industry, there is now a tangible increase in demand. A recovering economy and a new owner in Geely, combined with the promising new V60 model, are contributing to the sense of positivism that permeates the air. "Even though we have small buffer stocks in various places, the flow through the factory is absolutely decisive for the production tempo, and thus also for profitability," says John Selander, who explains that it takes about three days, one for each factory, to produce a car.
Together with Andreas Pettersson and Thomas Bernhed, John Selander maintains and further develops the bodywork factory's automation systems. This means that these three colleagues have a major, important role to play in the team effort that has to produce 160,000 cars every year that are both safe and enjoyable to drive.
Optimized flow
John Selander points up to the ceiling of the bright, surprisingly quiet bodywork factory, where a two-shift system operates. To judge by the 46-inch monitors, which show all stations colored green, right now everything's just as it should be. All in all, a dozen or so large screens have been installed at various places around the factory. It is strategically important that all employees can easily monitor production status: "By being able to quickly identify any possible problems and bottlenecks in the production lines, we can reduce setup times and optimize the flow."
The large screens are one effect of the technology shift that took place in autumn 2009, when iX from Beijer Electronics replaced an ageing SCADA program of the SattLine type as the master system.
The upgrade took place to keep up with the times - and to facilitate development and support:
"It's become increasingly difficult to find programmers who master SattLine, and at the same time we were attracted by features such as the vector-based graphics in iX," explains Thomas Bernhed.
Full control
The entire manufacturing process in the bodywork factory is monitored from the permanently staffed "bridge". In the past this was simply a bridge that was raised above the factory floor to provide a view over the whole plant. Today's bridge is a normal office, albeit crammed with technology, where the operator has full control via monitors and video cameras. "The operator's summary screen is the same one as is shown on the big screens out in the factory," explains Thomas Bernhed, who was responsible for HMI programming, as he shows us how easy it is to click down to a detailed level for various stations.
Using the Windows-based development tool iX Developer, an intuitive master system has been created for production monitoring. The ease of use is proven by the breadth of use. Administrative staff and managers also log in to monitor the production status via the internal data network. Thomas Bernhed gives iX Developer top marks. He describes the tool as structured and easy to use for programmers. "It only took us a couple of weeks to create an initial version of the application, which we then supplemented and extended with more functions and screens."
Andreas Pettersson explains that Volvo Cars was invited by Beijer Electronics to be test pilots even during the development phase for iX. Impressed by the inbuilt opportunities offered by iX, they started immediately to build this application. "Our stringent demands for operational reliability probably say it all about how well we thought that iX worked even then."
Profitable standard
Operational reliability and quality explain a relationship between Volvo Cars and Beijer Electronics that spans several years. The bodywork factory's first PLC from Beijer Electronics was installed back in 1993 – and the number that has broken down over the years doesn't take much counting.
The factory's robots, pressing and welding stations, and transport systems are now controlled by around 350 PLC units from the MELSEC family. These are controlled via more or less the same number of operator terminals. "We've standardized around MELSEC and have everything from small FX units to System Q," says Andreas Pettersson, who explains that operator terminals and frequency inverters are also bought from Beijer Electronics. Even if the PLC environment in this particular case is extremely uniform, the open architecture also favors iX. This HMI solution works on both operator panel and PC monitor, and together with a wide range of control systems. Data sharing in real time with SQL databases and OPC communication with third-party equipment and other IT systems are also no problem at all. There is no doubt at all that the "sneak preview" of iX whetted the appetite: "Many of our wishes have been met in the finished product. We've had and continue to have a good, open dialogue with Beijer Electronics and have received good support," says Thomas Bernhed.
One call is all it takes
The fact that the car company, with its skilled automation engineers as beta testers, has also made an important contribution for all of the other companies now using iX is evident. Erik Odhed is an account manager at Beijer Electronics' office in Gothenburg: "Our close collaboration and the opportunity during the development phase to try out iX in such a demanding, complex environment as car manufacturing was incredibly valuable," he says, explaining that the iX HMI solution was launched officially in spring 2010 and that it is now being used all around the world in a wide range of industrial environments.
As well as gaining a modern master system in iX, John Selander, Thomas Bernhed and Andreas Pettersson mention an additional benefit: "Having one single supplier for all key components, from PLC to HMI, means that one call is all it takes if you need help with any problems that may occur."
Caption 1: The final assembly takes place here in Torslanda, where a total of the 160.000 cars will leave the factory this year. It all starts in the bodywork factory where Beijer Electronics' HMI solution iX optimizes the flow.
Caption 2: From the "bridge" Andreas Pettersson monitors the bodywork factory closely.
Together with Andreas Pettersson and Thomas Bernhed, John Selander maintains and further develops the bodywork factory's automation systems. This means that these three colleagues have a major, important role to play in the team effort that has to produce 160,000 cars every year that are both safe and enjoyable to drive.
Optimized flow
John Selander points up to the ceiling of the bright, surprisingly quiet bodywork factory, where a two-shift system operates. To judge by the 46-inch monitors, which show all stations colored green, right now everything's just as it should be. All in all, a dozen or so large screens have been installed at various places around the factory. It is strategically important that all employees can easily monitor production status: "By being able to quickly identify any possible problems and bottlenecks in the production lines, we can reduce setup times and optimize the flow."
The large screens are one effect of the technology shift that took place in autumn 2009, when iX from Beijer Electronics replaced an ageing SCADA program of the SattLine type as the master system.
The upgrade took place to keep up with the times - and to facilitate development and support:
"It's become increasingly difficult to find programmers who master SattLine, and at the same time we were attracted by features such as the vector-based graphics in iX," explains Thomas Bernhed.
Full control
The entire manufacturing process in the bodywork factory is monitored from the permanently staffed "bridge". In the past this was simply a bridge that was raised above the factory floor to provide a view over the whole plant. Today's bridge is a normal office, albeit crammed with technology, where the operator has full control via monitors and video cameras. "The operator's summary screen is the same one as is shown on the big screens out in the factory," explains Thomas Bernhed, who was responsible for HMI programming, as he shows us how easy it is to click down to a detailed level for various stations.
Using the Windows-based development tool iX Developer, an intuitive master system has been created for production monitoring. The ease of use is proven by the breadth of use. Administrative staff and managers also log in to monitor the production status via the internal data network. Thomas Bernhed gives iX Developer top marks. He describes the tool as structured and easy to use for programmers. "It only took us a couple of weeks to create an initial version of the application, which we then supplemented and extended with more functions and screens."
Andreas Pettersson explains that Volvo Cars was invited by Beijer Electronics to be test pilots even during the development phase for iX. Impressed by the inbuilt opportunities offered by iX, they started immediately to build this application. "Our stringent demands for operational reliability probably say it all about how well we thought that iX worked even then."
Profitable standard
Operational reliability and quality explain a relationship between Volvo Cars and Beijer Electronics that spans several years. The bodywork factory's first PLC from Beijer Electronics was installed back in 1993 – and the number that has broken down over the years doesn't take much counting.
The factory's robots, pressing and welding stations, and transport systems are now controlled by around 350 PLC units from the MELSEC family. These are controlled via more or less the same number of operator terminals. "We've standardized around MELSEC and have everything from small FX units to System Q," says Andreas Pettersson, who explains that operator terminals and frequency inverters are also bought from Beijer Electronics. Even if the PLC environment in this particular case is extremely uniform, the open architecture also favors iX. This HMI solution works on both operator panel and PC monitor, and together with a wide range of control systems. Data sharing in real time with SQL databases and OPC communication with third-party equipment and other IT systems are also no problem at all. There is no doubt at all that the "sneak preview" of iX whetted the appetite: "Many of our wishes have been met in the finished product. We've had and continue to have a good, open dialogue with Beijer Electronics and have received good support," says Thomas Bernhed.
One call is all it takes
The fact that the car company, with its skilled automation engineers as beta testers, has also made an important contribution for all of the other companies now using iX is evident. Erik Odhed is an account manager at Beijer Electronics' office in Gothenburg: "Our close collaboration and the opportunity during the development phase to try out iX in such a demanding, complex environment as car manufacturing was incredibly valuable," he says, explaining that the iX HMI solution was launched officially in spring 2010 and that it is now being used all around the world in a wide range of industrial environments.
As well as gaining a modern master system in iX, John Selander, Thomas Bernhed and Andreas Pettersson mention an additional benefit: "Having one single supplier for all key components, from PLC to HMI, means that one call is all it takes if you need help with any problems that may occur."
Caption 1: The final assembly takes place here in Torslanda, where a total of the 160.000 cars will leave the factory this year. It all starts in the bodywork factory where Beijer Electronics' HMI solution iX optimizes the flow.
Caption 2: From the "bridge" Andreas Pettersson monitors the bodywork factory closely.