www.industryemea.com
18
'11
Written on Modified on
Power tracks for marathon lengths
KABELSCHLEPP can roll their chains with the RCC instead of sliding them
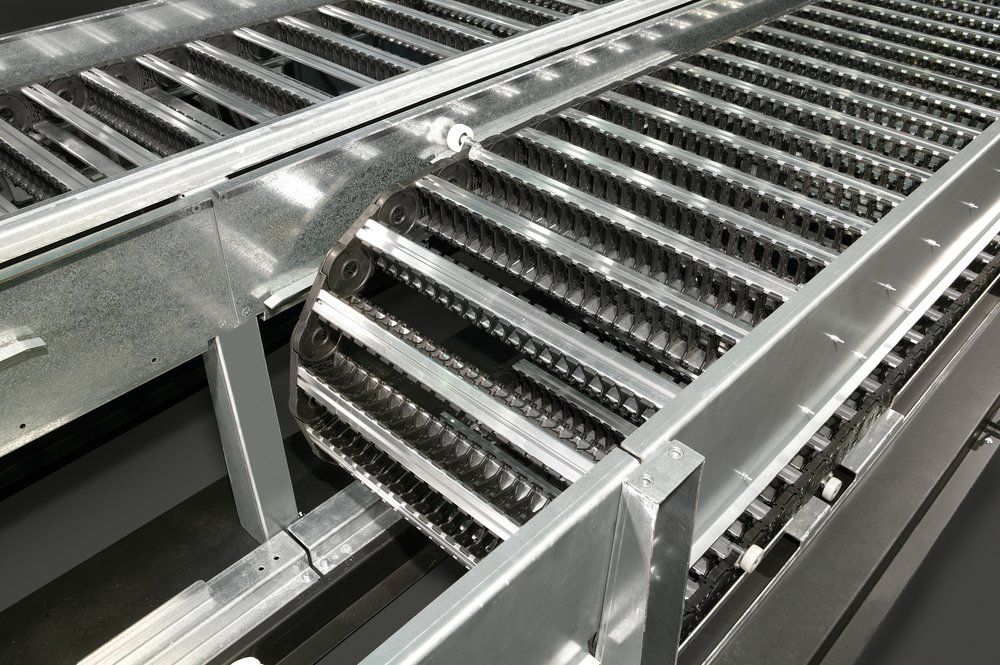
The Rail Cable Carrier (RCC) from KABELSCHLEPP is a power track system fitted with rollers and rails, which can be combined with all power track chains from this manufacturer, regardless of whether they are made from steel or plastic. The system developed according to the motto ›roll not slide‹, which was originally conceived for crane systems with very long stroke lengths, bridges even ›marathon lengths‹ of 500 metres and more with little noise and low vibration. On the Rail Cable Carrier the upper strand does not slide on the lower strand, but runs on the tracks. To do so, ball bearing rollers are fitted on the chain to the sides, thus preventing excessive friction. They run in the tracks and therefore do not collide with other rollers. The RCC is also notable for its low traction and shear forces as well as minimal strain on the routed cables since they are not bent. In addition to all this are the high conveyance speeds, reduced space requirement and a long service life. The machine tool manufacturer WALDRICH SIEGEN fits the RCC into large lathes.
A lathe is ›normally‹ compact and can be set up easily in any plant. The double-crankshaft lathes manufactured by WALDRICH SIEGEN Werkzeugmaschinen GmbH in Burbach are on an entirely different scale, up to 66 m in length, eleven metres wide and seven metres high. The stroke length alone of the crankpin turning attachment can be up to 50 metres long on these machines. With this in mind, the demands on the power track chains which run via the turning attachments increase, as do the opportunities for the Rail Cable Carrier to demonstrate its range of benefits. Alongside the double crankshaft lathes, WALDRICH SIEGEN use the RCC, always fitted horizontally, in other lathes for working crankshafts as well as in heavy-duty lathes, which have large turning lengths between the points.
»Since the RCCs are low vibration and low noise, they minimise the dynamic backlash on the machine, so that the finished surface of the workpiece is untouched «, stresses Gerhard Kleinhans, Design + Development Manager at WALDRICH SIEGEN. The high level of stability of the Rail Cable Carrier System can also accommodate the additional loads generated by the length of the routed cables. Loads of 50 kilograms per metre are possible, at WALDRICH SIEGEN the figure lies at 30 kilograms. This load capacity guarantees a high degree of reliability. The chain can also be easily fitted and serviced.
Roll not slide
KABELSCHLEPP has developed the Rail Cable Carrier according to the motto ›roll not slide ‹ and designed it for stroke lengths of 500 metres and more. Lengths of this scale cannot be bridged using a sliding design, because at just 200 metres the friction generated would be just too great. With the use of the RCC, this problem is prevented by the ball bearing rollers which have a surface coating of polyurethane and are fitted to the sides. They run in tracks which are fitted to the standard height, and therefore do not collide with other rollers. Apart from this, the chain cannot sag. Furthermore, the traction and shear forces are reduced by around 90 percent in comparison with sliding designs, because the upper strand does not slide on the lower cable. As a consequence, the user requires less input power. At WALDRICH SIEGEN the lower levels of friction and shear forces are not factored into the calculation of the input power due to the size of the machine, but they do contribute towards less wear and tear.
The RCC system works with standard power track chains and offers more reliability due to its integrated anti-climb barrier. The reason why the chain cannot climb in the acceleration phase is based on the low roller friction and the resulting low shear forces. Even in the case of a breakdown, KABELSCHLEPP holds the chain in the tracks through the lips on the top of the channel.
Each of the three Rail Cable Carriers in the double crankshaft lathes from WALDRICH SIEGEN carry electrical cable as well hydrostatic, cutting oil, air and coolant hoses. The cables are needed for power supply for the three movable skids, the so-called supports, which serve as a linking element between the control panel and the machine. Two of the RCCs are installed in opposing directions directly next to the machine. They run to the left lathe support and to the crankpin turning attachment. The third chain fitted on the outside leads to the third lathe support. All three chains run in an RCC channel system, which matches the stroke length, as do the chains. In this case the lengths are around 32, 17 and 16 metres long.
Increased efficiency through less wear
Since the Rail Cable Carrier itself and the cables that run through it are under only minimal strain, scarcely any wear and tear results. The beneficial transmission of force to the straight upper strand of the chain also contributes to this. In addition, the cables only bend according to the bend radius of the chain. In contrast to sliding designs, there is no reverse bending. Our customers can therefore expect a long service life for the chain and cables.
WALDRICH SIEGEN uses the RCC at speeds of up to ten metres per minute and therefore does not have to use the maximum possible stroke speed of up to ten metres per second. In fact, the company benefits from the short overhang of the chain which allows space saving installation into the machine. This allows a lesser foundation depth or a smaller installation space in the machine bed and thus saves costs. Shorter chain, cable and channel lengths also contribute to this. The short overhang is enabled because the end connector on the Rail Cable Carrier is positioned at bend height. Sliding designs with a deep end connector need an extended overhang, the result of which is an additional turnaround length, which cannot be used to convey the chain.
Transfer of forces over a large area
After deciding to go with the Rail Cable Carrier, WALDRICH SIEGEN had to select the series type with reference to the power track chain, especially since all Kabelschlepp power track chains can be used. WALDRICH SIEGEN chose the MC 1250 from the multi-variable M-Series from KABELSCHLEPP because the design of the linking elements guaranteed that the forces could be transferred over a wide area. The MC 1250 was chosen as much for its joint structure as its robustness and its suitability for long stroke lengths. In this case, the MC 1250 with a bend radius of 300 mm and an inner width of 640 mm enables a flexible separation of cables. In addition to this, the use of the solid frame rods made from a silicon-aluminum alloy, Silumin, and connected at four points thus ensuring a high degree of mechanical resistance, produces less friction between cables or hoses on the one side and the rods on the other.
Other benefits of the M-Series lie in the variable chain widths with grid widths of eight and 16 millimetres, in an enclosed stop-dog system insensitive to dirt as well as in the transfer of traction and shear forces over a wide area via the optimized joint design which makes the chain very robust. KABELSCHLEPP is aiming for a similar effect with a stable bracket design. Minimal wear of the joints through the pot lid principle as well as attachable partitions and a large selection of partitioning systems are additional benefits. In addition, the power track chains in the M-Series can be opened quickly on the inside and outside. Locking pins make it particularly easy to assemble.
Unique solution
»Through rigorous testing, the Rail Cable Carrier has proved itself to be the right power track system for double crankshaft and other large lathes «, says Gerhard Kleinhans. »Since the double machines and the RCC chain system have been developed around the same time, we did not have to look for alternative power tracks beforehand. « In summary we can say that WALDRICH SIEGEN has benefited in particular from a low vibration and low noise run on long lengths, from minimal traction and shear forces as well as minimal wear to chains and cables. The space saving design and high degree of reliability are other crucial arguments in favour of the Rail Cable Carrier from KABELSCHLEPP.
WALDRICH SIEGEN: Large, technically superior machine tools
With over 500 employees, WALDRICH SIEGEN Werkzeugmaschinen GmbH produces technically superior, large machine tools, e.g. roll grinding and roll texturing machines, automation equipment for rolling mills, high performance lathes and milling machines, end mill machines and rolling lathes. Their customers include international market leaders in the steel, aluminum, PVC and paper industries as well as manufacturers of cylinders, turbines and generators. WALDRICH SIEGEN was founded in 1840 as the H.A. Waldrich machine plant in Siegen. In 1981 the medium sized company moved its main office to Burbach, since 2004 it has been a subsidiary of the Herkules Siegen machine plant. The similar company structure of the Herkules Group, who has four production plants worldwide, gives WALDRICH SIEGEN a sound financial basis for long-term success.
A lathe is ›normally‹ compact and can be set up easily in any plant. The double-crankshaft lathes manufactured by WALDRICH SIEGEN Werkzeugmaschinen GmbH in Burbach are on an entirely different scale, up to 66 m in length, eleven metres wide and seven metres high. The stroke length alone of the crankpin turning attachment can be up to 50 metres long on these machines. With this in mind, the demands on the power track chains which run via the turning attachments increase, as do the opportunities for the Rail Cable Carrier to demonstrate its range of benefits. Alongside the double crankshaft lathes, WALDRICH SIEGEN use the RCC, always fitted horizontally, in other lathes for working crankshafts as well as in heavy-duty lathes, which have large turning lengths between the points.
»Since the RCCs are low vibration and low noise, they minimise the dynamic backlash on the machine, so that the finished surface of the workpiece is untouched «, stresses Gerhard Kleinhans, Design + Development Manager at WALDRICH SIEGEN. The high level of stability of the Rail Cable Carrier System can also accommodate the additional loads generated by the length of the routed cables. Loads of 50 kilograms per metre are possible, at WALDRICH SIEGEN the figure lies at 30 kilograms. This load capacity guarantees a high degree of reliability. The chain can also be easily fitted and serviced.
Roll not slide
KABELSCHLEPP has developed the Rail Cable Carrier according to the motto ›roll not slide ‹ and designed it for stroke lengths of 500 metres and more. Lengths of this scale cannot be bridged using a sliding design, because at just 200 metres the friction generated would be just too great. With the use of the RCC, this problem is prevented by the ball bearing rollers which have a surface coating of polyurethane and are fitted to the sides. They run in tracks which are fitted to the standard height, and therefore do not collide with other rollers. Apart from this, the chain cannot sag. Furthermore, the traction and shear forces are reduced by around 90 percent in comparison with sliding designs, because the upper strand does not slide on the lower cable. As a consequence, the user requires less input power. At WALDRICH SIEGEN the lower levels of friction and shear forces are not factored into the calculation of the input power due to the size of the machine, but they do contribute towards less wear and tear.
The RCC system works with standard power track chains and offers more reliability due to its integrated anti-climb barrier. The reason why the chain cannot climb in the acceleration phase is based on the low roller friction and the resulting low shear forces. Even in the case of a breakdown, KABELSCHLEPP holds the chain in the tracks through the lips on the top of the channel.
Each of the three Rail Cable Carriers in the double crankshaft lathes from WALDRICH SIEGEN carry electrical cable as well hydrostatic, cutting oil, air and coolant hoses. The cables are needed for power supply for the three movable skids, the so-called supports, which serve as a linking element between the control panel and the machine. Two of the RCCs are installed in opposing directions directly next to the machine. They run to the left lathe support and to the crankpin turning attachment. The third chain fitted on the outside leads to the third lathe support. All three chains run in an RCC channel system, which matches the stroke length, as do the chains. In this case the lengths are around 32, 17 and 16 metres long.
Increased efficiency through less wear
Since the Rail Cable Carrier itself and the cables that run through it are under only minimal strain, scarcely any wear and tear results. The beneficial transmission of force to the straight upper strand of the chain also contributes to this. In addition, the cables only bend according to the bend radius of the chain. In contrast to sliding designs, there is no reverse bending. Our customers can therefore expect a long service life for the chain and cables.
WALDRICH SIEGEN uses the RCC at speeds of up to ten metres per minute and therefore does not have to use the maximum possible stroke speed of up to ten metres per second. In fact, the company benefits from the short overhang of the chain which allows space saving installation into the machine. This allows a lesser foundation depth or a smaller installation space in the machine bed and thus saves costs. Shorter chain, cable and channel lengths also contribute to this. The short overhang is enabled because the end connector on the Rail Cable Carrier is positioned at bend height. Sliding designs with a deep end connector need an extended overhang, the result of which is an additional turnaround length, which cannot be used to convey the chain.
Transfer of forces over a large area
After deciding to go with the Rail Cable Carrier, WALDRICH SIEGEN had to select the series type with reference to the power track chain, especially since all Kabelschlepp power track chains can be used. WALDRICH SIEGEN chose the MC 1250 from the multi-variable M-Series from KABELSCHLEPP because the design of the linking elements guaranteed that the forces could be transferred over a wide area. The MC 1250 was chosen as much for its joint structure as its robustness and its suitability for long stroke lengths. In this case, the MC 1250 with a bend radius of 300 mm and an inner width of 640 mm enables a flexible separation of cables. In addition to this, the use of the solid frame rods made from a silicon-aluminum alloy, Silumin, and connected at four points thus ensuring a high degree of mechanical resistance, produces less friction between cables or hoses on the one side and the rods on the other.
Other benefits of the M-Series lie in the variable chain widths with grid widths of eight and 16 millimetres, in an enclosed stop-dog system insensitive to dirt as well as in the transfer of traction and shear forces over a wide area via the optimized joint design which makes the chain very robust. KABELSCHLEPP is aiming for a similar effect with a stable bracket design. Minimal wear of the joints through the pot lid principle as well as attachable partitions and a large selection of partitioning systems are additional benefits. In addition, the power track chains in the M-Series can be opened quickly on the inside and outside. Locking pins make it particularly easy to assemble.
Unique solution
»Through rigorous testing, the Rail Cable Carrier has proved itself to be the right power track system for double crankshaft and other large lathes «, says Gerhard Kleinhans. »Since the double machines and the RCC chain system have been developed around the same time, we did not have to look for alternative power tracks beforehand. « In summary we can say that WALDRICH SIEGEN has benefited in particular from a low vibration and low noise run on long lengths, from minimal traction and shear forces as well as minimal wear to chains and cables. The space saving design and high degree of reliability are other crucial arguments in favour of the Rail Cable Carrier from KABELSCHLEPP.
WALDRICH SIEGEN: Large, technically superior machine tools
With over 500 employees, WALDRICH SIEGEN Werkzeugmaschinen GmbH produces technically superior, large machine tools, e.g. roll grinding and roll texturing machines, automation equipment for rolling mills, high performance lathes and milling machines, end mill machines and rolling lathes. Their customers include international market leaders in the steel, aluminum, PVC and paper industries as well as manufacturers of cylinders, turbines and generators. WALDRICH SIEGEN was founded in 1840 as the H.A. Waldrich machine plant in Siegen. In 1981 the medium sized company moved its main office to Burbach, since 2004 it has been a subsidiary of the Herkules Siegen machine plant. The similar company structure of the Herkules Group, who has four production plants worldwide, gives WALDRICH SIEGEN a sound financial basis for long-term success.