www.industryemea.com
03
'11
Written on Modified on
LineRunner 300: 3D measurement with the laser light sensor from Pepperl+Fuchs
Whether path correction, edge or gap measurement, volume measurement or tolerance verification, the tasks and requirements of modern vision solutions are varied. Pepperl+Fuchs has developed a powerful and reliable laser light sensor in the form of the LineRunner 300 (LR300) to overcome these challenges.
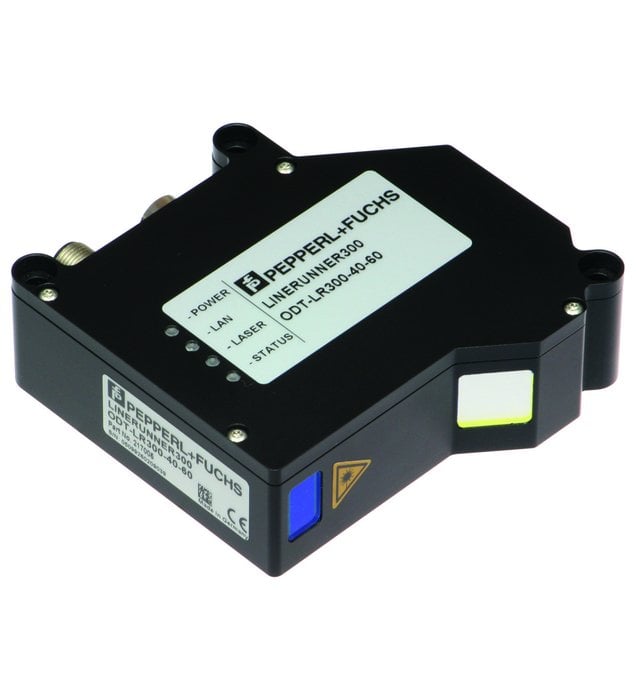
In the laser light process, a line projected onto an object is detected by a camera at a specific angle. Height and width information are determined using the triangulation principle.
As a result, the LR300 is able to process even the most problematic color and contrast characteristics using a sophisticated exposure time control and due to its laser protection class 1 conformity, saves on costs that would otherwise be incurred through workplace safety measures for higher laser protection classes.
As a result, the LR300 is able to process even the most problematic color and contrast characteristics using a sophisticated exposure time control and due to its laser protection class 1 conformity, saves on costs that would otherwise be incurred through workplace safety measures for higher laser protection classes.
The LineRunner delivers width and height data in millimeters via an Ethernet interface, enabling direct connection to an evaluation system.
The LineRunner 300 by Pepperl+Fuchs is a reliable, robust laser light sensor with an impressive safe laser protection class and sophisticated exposure time control.
Main features at a glance
- Laser protection class 1
- Intelligent illumination control
- Saves money at safeguarding work stations
- No manual change of the parameterizing is needed with different surfaces
- Dual Laser System
- Infrared measuring reader
- Red measuring point indication laser
- Vision Configurator
- Standard intuitive control software for all vision-sensors
- Simple implementation thanks to measuring point
- Invisible measuring without employee irritation
- Simple to exchange sensors without new calibration
- Relearning not necessary