Making internal combustion engines fit for the future
Fuel consumption and CO2 emissions can be reduced by up to 15 percent thanks to Schaeffler.
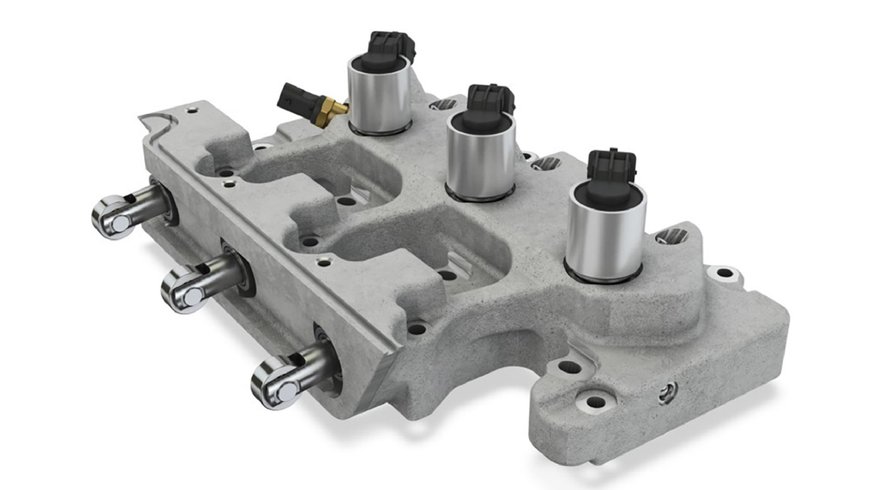
- Optimized drives based on internal combustion engines contribute to the achievement of the Paris Agreement’s environmental targets
- Fuel consumption can be reduced by as much as 15 percent depending on the engine and vehicle class
- New compact version of the UniAir system with optimized weight characteristics presented
The world of mobility is changing. For the two-degree target specified by the Paris Agreement to be achieved, a mix of all-electric drives, hybridized drives, and eco-friendly drives based on internal combustion engines is absolutely essential. Schaeffler predicts that the internal combustion engine will also continue to play a decisive role in the future.
In the year 2030, internal combustion engines will still be installed in around 70 percent of vehicles – of which 30 percent will rely solely on the internal combustion engine and 40 percent will be hybrids. It is therefore essential for the further development of conventional drives to continue.
“The solutions that we will be presenting at the IAA make fuel savings of up to 15 percent possible depending on the engine and vehicle class”, explains Matthias Zink, CEO Automotive OEM at Schaeffler. “We are giving our customers a lot of leverage with which to fulfill the strict legal requirements and reduce CO2 emissions during real operation as well.”
Valve train variability
At the IAA, Schaeffler will be presenting the latest version of its fully variable UniAir valve train system. As well as being more compact, this system is also 30 percent lighter than the previous version, and it allows the air path in the engine to be fully optimized and maximum dynamics achieved when load and speed changes occur.
The system comprises a module that is installed between the camshaft and the valve stem, together with the relevant software. As a strong partner to the automotive industry, Schaeffler uses its comprehensive expertise in thermodynamics to help its customers optimally match the system to the relevant engine and select the corresponding operating strategies.
Schaeffler’s eRocker solution is designed for the exhaust side. The system’s electromechanical actuation makes it independent of the engine’s oil circuit, and it can also be applied with relative ease. Schaeffler will be presenting a further highlight with its electric cam phasing (ECP) unit.
This system makes rapid adjustments based on the speed and temperature and allows the valve timing to be optimized throughout the entire operating and temperature range, which plays an increasingly important role when it comes to hybridization since internal combustion engines in hybrid vehicles have to be started with significantly greater frequency than those installed as the sole drive source.
The electric camshaft phasing unit ensures that this start process takes place quickly, efficiently, and (most importantly) with low vibration levels.
48 V hybridization makes fuel savings of up to seven percent possible
Hybridization supports the internal combustion engine while reducing its workload and, in conjunction with braking energy recuperation, improves the overall efficiency of the system.
At the IAA, Schaeffler will be demonstrating 48 V hybridization using a belt-driven starter generator, which allows a significant reduction in fuel consumption and emissions of 5 to 7 percent to be achieved. This type of solution makes comfortable and efficient start-stop operation of the engine possible and can also be configured for boost operation.
Thermal management module
Thermal management is another key element when it comes to increasing efficiency. Schaeffler’s individually adjustable thermal management module (TMM) for internal combustion engines and hybrid and electric drives provides enhanced control of the operating temperature throughout the entire powertrain, including the engine, transmission, and electrical components like the battery, power electronics, and electric motor.
The module allows precise regulation of volume flows using electromechanically powered rotary slide units that are controlled by position sensors. Alongside reduced CO2 emissions, the shorter warm-up phase also has another positive side effect: Passenger comfort is increased.
Less friction inside the engine
Even conventional bearing solutions still improve drives based on internal combustion engines: Innovative solutions for rolling bearing supports in balancer shafts, camshafts, and crankshafts offer considerable potential for reducing power losses in the engine and thus for improving fuel economy and lowering emissions.
Balancer shafts with rolling bearing supports generate approximately 50 percent less friction compared with shafts supported by plain bearings, for example. Schaeffler has also succeeded in developing an optimized design for balancer shafts that is up to 40 percent lighter without any loss of function.