Avoid Unnecessary Linear Guide Implementation Challenges for Packaging Equipment
Builders of bagging and cartoning equipment, case erectors, packers and sealers, tray formers, palletizers, pallet dispensers and related machines often choose high-precision linear bearing guides.
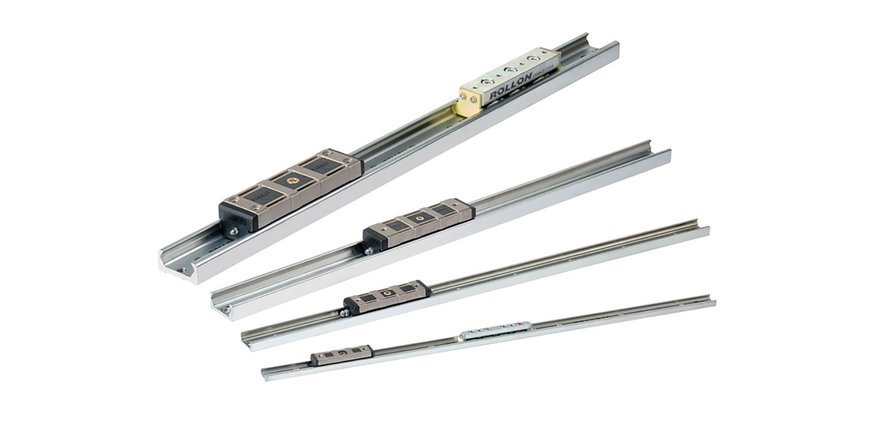
However, they often add challenges when they specify linear guides with higher accuracy than typically needed in packaging machines that simply require reliable, repeatable linear motion.
For example, the assembly will require machined plates to align the guides for flatness and parallelism, and the additional fabrication, machining and assembly involved increases time and labor costs. And if the rails are not properly installed, the precision bearings will experience constant load from binding.
This will prematurely wear the bearings and can lead to more frequent replacement. Builders can solve the problem by paying more for larger profiled bearings, but this will also increase the size and weight of the assembly, which translates to higher costs for power transmission and motion control components.
In addition to machining and installation considerations, machine builders must also pay attention to the contamination risks that primary and secondary packaging machinery present for linear bearings. In secondary packaging, for instance, dust from corrugated materials can easily collect on the rail and consequently collect inside the bearing block. This leads to premature wear on the bearing and, in the worst-case scenarios, will completely jam the bearing and result in a costly shutdown.
Roller Guides Deliver the Right Precision
Using roller guides, such as Rollon’s Compact Rail in medium-accuracy applications can, for example, eliminate the added machining, fabrication and assembly efforts typically associated with recirculating ball guides. Compact Rail features large rolling elements, rail profiles that allow some play and an easy preload adjustment that enables equal loading of all elements.
Not only is it a more compliant guide than a profiled rail, it can even compensate for misalignment by mitigating uneven load points that may otherwise promote wear and pitting. Compact Rail linear bearings provide numerous features and benefits for packaging applications:
- The rails comply to assemble directly to weldments, reducing fabrication and assembly costs.
- Sealed bearings keep dust away from the balls, protecting the bearings from contamination. Roller assemblies can also be configured with scrapers to prevent larger particulates from getting trapped in the sliders.
- Compact Rail bearings are particularly useful in secondary packaging, where the containers are already sealed and the primary contaminant in the environment is dust from packaging.
- For primary packaging applications, stainless steel linear rails and roller bearings can withstand washdown applications.
Unlike high-precision recirculating ball guides, medium-precision bearing guides like Rollon Corporation’s Compact Rail do not saddle packaging machine builders with expensive and unnecessary machining and assembly requirements. Not only will they deliver sufficient accuracy and precision for packaging equipment applications, they’ll keep assembly time and costs in line with their goals.
www.rollon.com