www.industryemea.com
26
'19
Written on Modified on
ITP Aero designs and manufactures its first components with additive layer manufacturing
The company's own design criteria enable relevant cost savings and components weight reduction of up to 40%.
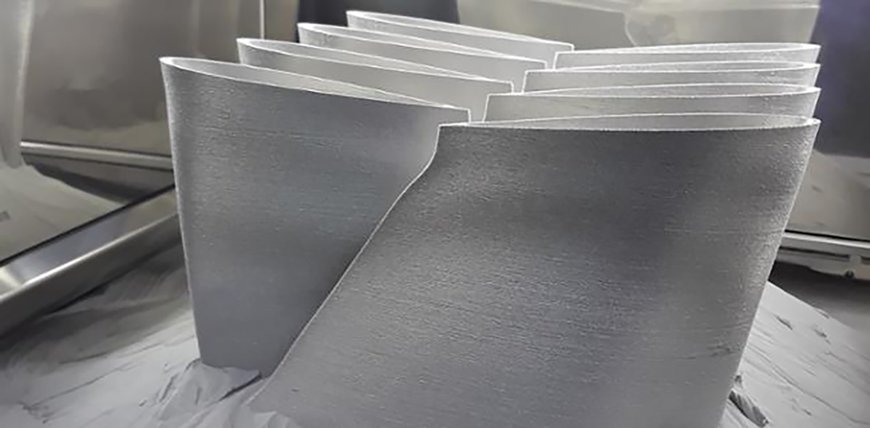
These are two different components: low pressure turbine seal segments for the Rolls-Royce Trent XWB-84 engine for the Airbus A350 XWB aircraft, and (Turbine Exhaust Case) non-structural vanes for the TP400 engine that powers the Airbus A400M military transport aircraft. It is estimated that the proprietary design criteria used by ITP Aero will result in a component weight reduction of up to 40% and significant cost savings.
The first turbine featuring development standard segments manufactured with additive layer manufacturing was delivered in June to Rolls-Royce's test bench facility in Derby for assembly on a Trent XWB-84.
As part of our standard process for demonstrating maturity, these segments will be subsequently tested, validated and certified with a view to future incorporation into production versions of the engine. Segments are components located between the rotating blades and the turbine casing, and their function is to minimize the airflow between both.
In addition, the TP400 TEC vanes design phase is underway aiming at validation and standardization of the components in 2020. The TEC is located at the rear of the engine and fulfils a vital role as one of the two anchor points to the wing of the aircraft. The TEC is subjected to temperatures of up to 600 degrees and channels the engine’s exhaust air. It is estimated that the production with additive technology at industrial level of this component will be operative by 2021.
The additive manufacturing technology used for these components is the Selective Laser Fusion method - also known as industrial 3D manufacturing. First, the 3D model of the component is digitally divided into individual layers, and then a laser melts the superalloy of powdered nickel to form the component layer by layer.
This method allows to produce complex geometry components, using only small amounts of powder. It’s worth mentioning that all components produced with additive layer manufacturing need to be approved by the European Union Aviation Agency (EASA).
ITP Aero has an additives manufacturing cell and a team of professionals dedicated exclusively to this technology at its Zamudio facilities. The company, thanks to its investment in collaborative technology development projects, is able to apply its own standards and specifications for the application of this technology in aircraft engine components subjected to high temperatures.
A clear example of this is the MTR390-E engine delivered to Airbus Helicopters last December, which incorporated a lubrication tube designed by ITP Aero using additive technology, as well as the complex instrumentation probes already tested in Rolls-Royce engines.
Regarding the potential use of additive manufacturing and its role in the production of aircraft engine components, Iñaki Ulizar, Executive Director of Technology for ITP Aero, believes that "as a leading-edge technology group, at ITP Aero we embrace the most advanced manufacturing systems. Moving forward, we are looking at the use of new materials and expanding the range of components produced through additive manufacturing such as complex tubes or bearing housings.”
www.itpaero.com