www.industryemea.com
26
'19
Written on Modified on
Skiving of Large Gear Modules
Gear teeth from module 3 without the need for special gear cutting machines.
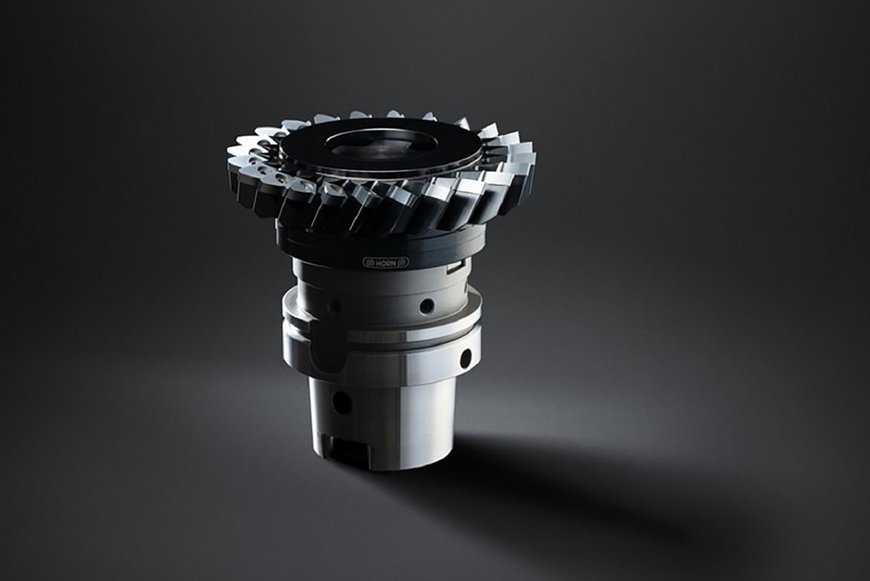
The tool system is based on the cutting insert type S117. The patented insert seat of the single-edged tool ensures precise clamping and positioning for high rigidity of the system as a whole with precise repeatability. The ground chipbreaker form and the direct threaded connection of the inserts enable very effective chip removal from the machining zone. All cutting edges are cooled directly by an internal coolant supply.
Horn gear skiving tools are specially designed and manufactured for every application. The feasibility of each application is verified by HORN engineers prior to implementation and the tool design and recommendations for the process are discussed with the user.
Horn’s product portfolio comprises a wide range of tools for the production of various gear tooth geometries from module 0.5 to module 30. Whether this involves gear teeth for spur gears, shaft/hub connections, worm shafts, bevel gears, pinions or customised profiles, all these tooth profiles can be manufactured extremely cost-effectively with milling or broaching tools.
The gear skiving range is yet more testament to the company’s gear tooth machining expertise. It is a process that has been in use for over a century, but has only been incorporated into a wider range of applications since machining centres and universal turning machines with fully synchronised spindles and process-optimised software have been able to accommodate the highly complex technology.
www.phorn.com