www.industryemea.com
01
'19
Written on Modified on
Local production of advanced machining technology
At Manufacturing Days in Davis, California, DMG MORI presents a holistic portfolio of the latest production technologies in Horizontal Machining, Automation, and ADDITIVE MANUFACTURING.
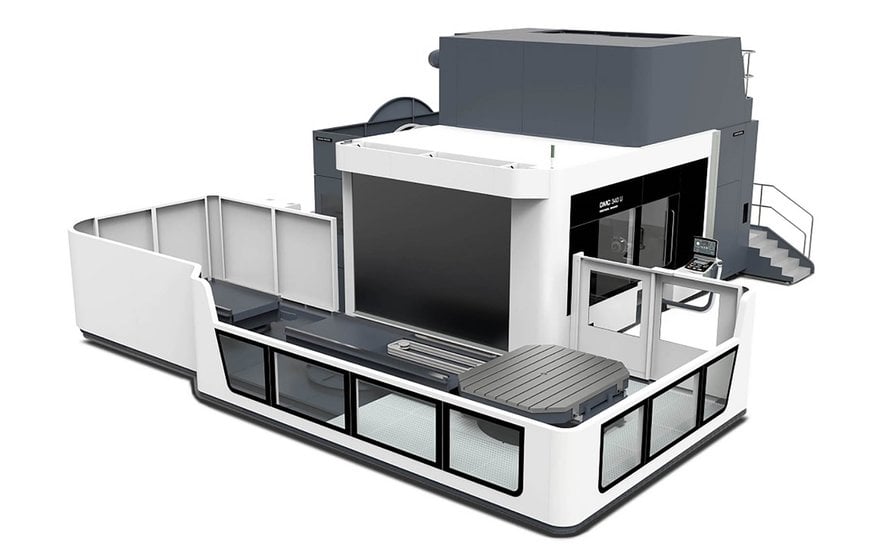
The ALX 2500|500 with GX, the CMX 1100 V with MATRIS, and the NHX 4000 with LPP are just three of these highlights. Additionally, the Manufacturing Days schedule includes multiple training sessions and seminars.
The DMG MORI campus in Davis holds the U.S. factory and DMG MORI’s American Research and Development hub. The location between San Francisco and Sacramento allows the machine tool manufacturer to be closer to its North American customers.
The extensive use of automation, combined with a highly skilled workforce, makes Davis one of the most advanced factories in the world. The facility utilizes DMG MORI machines and automation systems including a DMC 340 U, three NHX 10000’s and two NH 6300 DCGII. All are integral parts of the plant.
With the local production of the NHX and NH machines, DMG MORI emphasizes its competence in horizontal machining. During Manufacturing Days, six of these machines will be shown to visitors, four of them automated with LPP or RPS solutions. The factory’s production portfolio also includes the universal turning machines ALX 2000 and ALX 2500, as well as the vertical milling center CMX 1100 V.
Automation: More value creation through integral automation
Automated machines are crucial components of a digital factory and therefore an integral part of intelligent and networked production. DMG MORI sees automation as a strategic and future-oriented field. As every DMG MORI plant, the factory in Davis assumes an important role in the development and implementation of automation solutions.
This includes technical consultations and budgeting to possible modifications to machines in use and on to include installation and commissioning. The local experts also assume other optimizations, the tooling and teaching of robots, which enables customers to receive a complete automation solution from a single source.
The ALX 2500|500 with GX, the CMX 1100 V with MATRIS, and the NHX 4000 with LPP are three of the many automation highlights at Manufacturing Days. In the field of complex 5-axis milling DMG MORI will demonstrate the DMU 50 with PH 150.
US premiere: LASERTEC 12 SLM High precision building of 3D parts with a 4.9 x 4.9 x 7.9 in. building volume
Being a complete supplier in additive manufacturing of metal parts DMG MORI offers the LASERTEC 3D hybrid and LASERTEC 3D series for laser deposition welding and LASERTEC SLM series in the field of powder bed machines. At Manufacturing Days, DMG MORI presents the LASERTEC 12 SLM as a US premiere.
The most precise model of the LASERTEC SLM series has the biggest building volume of its class, offering 4.9 x 4.9 x 7.9 in. The LASERTEC 12 SLM achieves its precision with a focus diameter of only 35 µm (0.0014 in). The LASERTEC 12 SLM offers material changes in less than 2 hours by changing the rePLUG powder modules. Being compatible with the bigger LASERTEC 30 SLM (11.8 x 11.8 x 11.8 in), the SLM platform concept is fully utilized.
Designed for applications in selective laser melting, DMG MORI offers the new OPTOMET software. It has self-adjusting and learning algorithms that calculate the required parameters of the SLM process in advance within minutes. OPTOMET reduces material development efforts by 70 % using its material database that allows users to use material from all manufacturers without having to test them in advance.
The open system also allows independent expansion of the database using the customer’s own experiments. OPTOMET is able to adjust parameters in such a way that material properties, such as hardness, porosity, and elasticity, can be optimized.
Integrated Digitization and DMG MORI Connectivity: Intelligent services and applications with integral connectivity for networked production
For DMG MORI “connectivity” constitutes one of the core features on the path to the digital factory, because only open interfaces and standardized communication protocols can ensure future-oriented end-to-end integration and interoperability of machines and processes.
That is why in future all new machines from DMG MORI will be connectivity compliant in major industry standards – MTConnect and MQTT protocols as well as the new umati (universal machine and tool interface) branch standard based on OPC UA – as the new IIoT interface.
Seminars and hands-on trainings for visitors
The list of seminars and training sessions for Manufacturing Days visitors provides good insights into the development and future of machine tool manufacturing. Experts will talk about the benefits of automation solutions, the Digital factory, and complex machining applications. Additionally, DMG MORI offers a factory tour that explains the anatomy of a machine tool first-hand.
www.dmgmori.com