www.industryemea.com
04
'19
Written on Modified on
Cobots for business-critical inspections
Carrying out inspections on business-critical objects and production installations can prevent loss of quality and production stoppages.
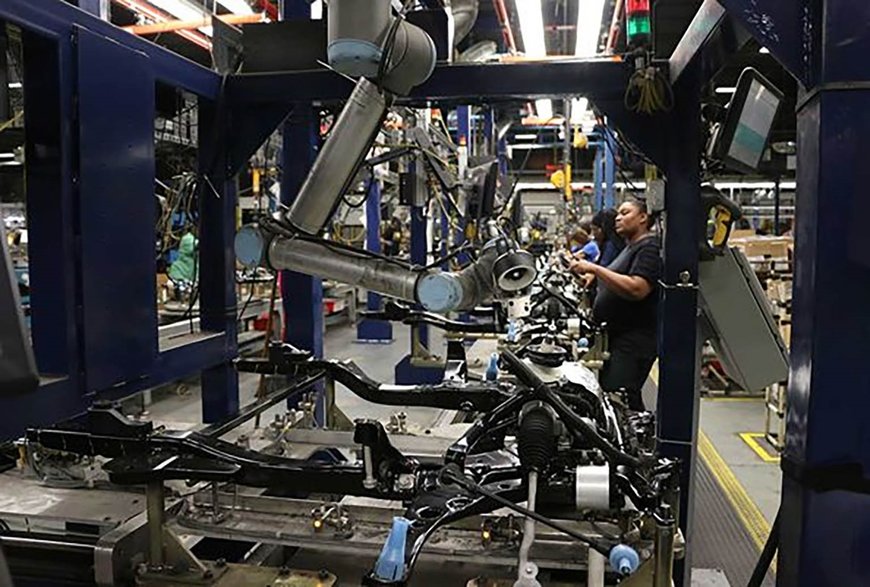
Product improvement via quality inspection
Operators who have to check thousands of components each day sometimes miss identifying a defect, which is something robots never do. For example, cobots connected to cameras are used to carry out product quality inspections in a whole range of sectors including automotive and aviation. Depending on the inspection, the cobot can approve or reject products then sort them according to the results.
There is typically a smaller distribution on inspection results when performed by a cobot with camera, even zero defects can be achieved and greater tolerances on the objects can be specified than would otherwise be possible with manual inspections. Apart from that, it is often difficult to find personnel for such repetitive tasks and cobots can carry out these operations at a more constant pace and more accurately.
The use of cobots provides more versatility and flexibility in comparison with customised inspection automation, which is advantageous with regularly changing products. An operator can feed the cobot with components to be inspected and remove the components that have already been inspected.
More efficient inspection of assembly lines
There is no room for error on assembly lines where everything happens according to a just-in-time and specific sequence. Stoppages caused by defects result in production loss or even hazardous situations. Steering equipment with a defective connection because a plug is not properly inserted can lead to loss of power steering for example.
Manual inspections are not always able to prevent such defects from occurring and visual inspections using a fixed camera are not always ideal or even possible, for example where space is limited.
A cost-effective robot that can repeatedly and safely reposition the camera offers a user-friendly solution and is easy to integrate with processes and operators on the line. A cobot with such a camera that is installed on the ceiling can rapidly move between the various inspection points and take a picture of each connection before returning to the rest position.
Integrated software can monitor the line and tell the robot which products have to be inspected. Each picture is immediately displayed on a screen next to the robot, while a second screen displays each inspection point in which the approved and rejected points are marked out in different colours.
www.sirris.com