www.industryemea.com
09
'19
Written on Modified on
Faster mould set-up, less maintenance
The e-flomo premium electronic temperature control water manifold system by ENGEL goes on show at K 2019 from October 16th to 23rd in Düsseldorf with a new feature.
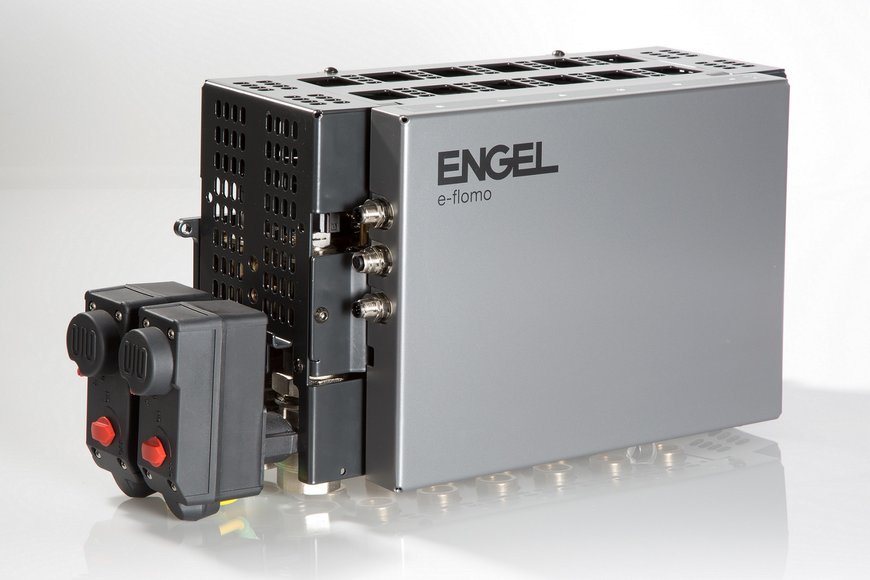
Residual water and dirt in the temperature control channels of injection moulds can lead to corrosion, shortening the service life of the moulds and impacting on temperature stability. Before moulds and mould inserts are changed, the temperature-control channels are therefore usually blown out with compressed air.
Traditionally, this is a manual process that not only takes a lot of time, but also involves a residual risk, as compressed air often does not flow evenly through the ducts. To ensure greater efficiency and safety here, ENGEL is offering a new option for the premium version of its e-flomo electronic temperature control water manifold system: automated sequential blowing out of the manifold channels.
Automating the blow-out process accelerates the mould set-up and minimises the risk of residual water in the temperature-control channels. This extends the maintenance intervals for the mould and reduces maintenance costs. A further benefit results when mounting the mould. The new feature ensures optimum ventilation of the temperature-control channels, ensuring premium part quality from the outset.
Temperature control process in development focus
“Mould temperature control has a significant influence on the efficiency and quality of the injection moulding process,” as Klaus Tänzler, Product Manager Temperature Control at ENGEL AUSTRIA emphasises. As a systems expert, ENGEL therefore considers the continuous optimisation of the temperature control process to be one of its core competencies and is actively promoting digitalisation in this area.
The electronic temperature control water manifold system plays a central role in this. The iQ flow control software developed by ENGEL controls the flow rates on the basis of the measured values determined by e-flomo and adapts the temperature control process dynamically and independently to the respective process conditions.
Where ENGEL e-temp temperature control units are used, this also includes demand-dependent control of the pump speed in the temperature control units. “ENGEL's connected temperature control solution makes it possible to combine maximum temperature stability with maximum productivity and energy efficiency,” says Tänzler.
ENGEL at K 2019: Hall 15, Stand C58
www.engelglobal.com