www.industryemea.com
04
'19
Written on Modified on
3D-Printed Fashion: Coming to a Boutique Near You?
Stratasys partners with designers threeASFOUR and Travis Fitch at New YorkFashion Week to showcase commercial possibilities of 3D printing directly on clothing.
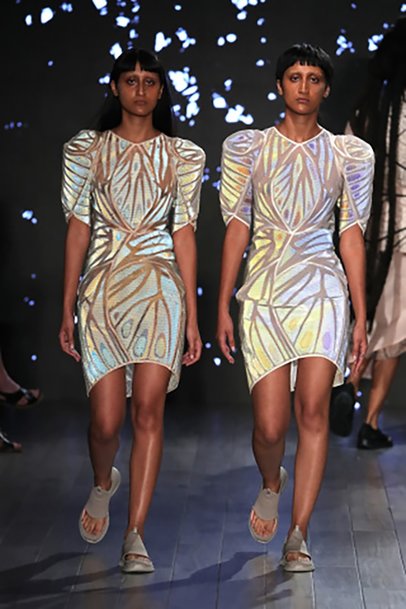
Designers have used 3D printing in fashion for several years; however, printed elements have been created separately and affixed to garments. Stratasys sees the technique of printing directly on textiles, which provides unparalleled flexibility and integrity, as the key to creating modern, functional apparel and unlocking 3D printing’s commercial viability in the fashion industry.
“Within the next two years, I believe consumers will be able to purchase an array of 3D-printed garments from high-fashion brands,” said Stratasys Art, Design and Fashion Director Naomi Kaempfer. “And the result will be access to an explosion of unique color and texture combinations that are simply not possible through traditional methods.”
The ‘Chro-Morpho’ collection shown during Fashion Week evokes the beauty and color morphology of insects. “We’ve created the skin-like illusion of switching shades and depth to portray the insect’s innate camouflage, color diversion and luminosity,” said Adi Gill, co-founder and creative director of threeASFOUR. “With 3D design and printing, we’ve embodied the fragility and light wing movement of the butterfly. It’s a stunning display of nature, fashion and technology.”
One Greta-Oto dress from the collection, for example, uses a Stratasys-engineered lenticular effect to play with light and color. By printing spherical, fish scale-sized cells made of photopolymers directly onto polyester fabric, the color of the dress shifts with each small movement. The thousands of cells on the dress’s 27 parts consist of a clear lens with strips of color contained inside. 3D-printing takes approximately 17 hours.
Designers used the Stratasys J750 PolyJet™ printer, also making its Fashion Week debut, to add the polymers to the material. The J750 printer can produce more than 500,000 combinations of colors, textures, gradients and transparencies, and has the processing power and finesse to handle the delicate geometries and microscopic layers applied to the garments.
This gives designers unlimited design freedom and potentially enables end users to be involved in the design. There are also tangible business benefits: A single 3D printer can replace a wide variety of other manufacturing machines, from 2D-printing to embroidery, thermoforming, foiling and ultrasound. This saves apparel- and textile-makers space, cost and time, including a simpler supply chain.
Kaempfer said the union of textiles and 3D printing is about working in harmony with materials rather than replacing them. “Soft, lithe fabric touches the skin, while 3D-printed designs adorn the outer garment. This approach, developed through months of collaboration and testing, was the only way to realize the designers’ vision. It brings the intricacy, nuance and splendor of the dresses to life.”
The project is a significant step in Stratasys’ work to merge fashion and 3D printing — for high-end couture and, eventually, series production. Along with threeASFOUR and Travis Fitch, the company has collaborated with Iris van Herpen and other industry luminaries. In addition, it recently announced a partnership with Pantone to integrate the Pantone color matching system, the de facto standard for designers, into Stratasys printers.
Stratasys is also providing its PolyJet technology to the European UnionRe-FREAM program, part of the broader Science, Technology & the Arts (STARTS) initiative, to encourage artists, designers, engineers and scientists to co-explore the use of technology and 3D printing for the future of fashion.
“We are always looking to revolutionize manufacturing methods, pioneer new design options, and inspire designers and students to create without boundaries,” Kaempfer said. “Our mission is to change the way people think about design and to redefine what’s possible.”
After New York Fashion Week, the innovative Chro-Morpho collection will travel to museums across the country. The collection will be displayed at the Philadelphia Museum of Art’s “Designs for Different Futures” exhibition beginning Oct. 21. The collection will also visit the Walker Art Center in Minneapolis and the Art Institute of Chicago in 2020.
www.stratasys.com