www.industryemea.com
23
'19
Written on Modified on
A closer look at the RenAM 500Q
Traditional barriers to additive manufacturing (AM) were limited production speed and variation in build quality between machines.
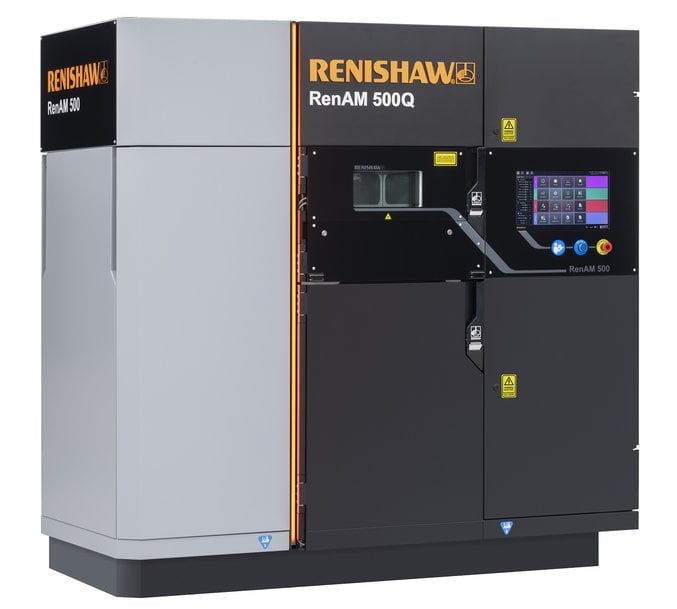
If we are to broaden the applications of metal AM so the technology can realise its full potential, it is important that we speed up the AM process while also creating high quality products in a cost-effective way. Doing so will mean that an ever-wider group of users can turn to AM technology.
Global spending on AM is forecast to reach $26.7bn in 2019. While many different industries are using specialist parts produced with AM, such as fasteners for aircraft, medical implants and tooling, the applications for AM have been limited when it comes to more commonplace products.
For example, aircraft seats could be produced using AM as a strong and lightweight alternative to traditional manufacturing, it could also be used in automotive applications, where lightweight components can have an impact on overall efficiency, particularly with the emergence of hybrid and electric vehicles.
However, AM is not cost-effective if productivity is low. To combat this, Renishaw's latest system, the RenAM 500Q, is leading the way by reducing waste and powder handling, and employing multiple lasers for faster builds and reduced costs per part.
Multiple laser efficiency
Slow build rates have historically been a drawback for AM technology. Traditional metal AM systems have up until recently only been capable of laying down material at a speed of around 20 cubic centimetres (1.2 cubic inch) per hour. If you are producing multiple parts, it is important to reduce time and cost so that the process is efficient and cost-effective.
To achieve this, Renishaw developed the RenAM 500Q system, which is fitted with four high power 500W lasers.
Not only can these lasers access the whole powder bed surface simultaneously, but they also achieve build rates of up to four times faster than conventional single laser systems. Maximum efficiency is achieved on the RenAM 500Q because the lasers can work across the entire build plate, allowing the laser interaction to be managed effectively to ensure quality is unaffected by multi-laser interaction when processing.
Gas emissions — enhancing quality
Quality has been another barrier to the adoption of AM technology, particularly for structural parts in regulated industries such as aeronautics, consumer products and healthcare.
During the laser powder bed fusion process, powder spatter and process emissions can be a major cause of defects in end-products and can undermine product quality if impurities fall back into the metal powder. Therefore, one of the key contributing factors to high quality AM products is the removal of these impurities.
Renishaw has fitted the RenAM 500Q with an intelligent gas flow system that removes process emissions from the build volume, resulting in processing conditions that provide a stable processing environment that has measurably driven up quality standards to levels not previously achieved with metal AM technologies.
This means that the final parts exhibit consistent properties — they are high in density and have high tensile strength with excellent ductility and fatigue performance. This creates an end-product that's both strong and light at the same time. Therefore, the machine can be applied to all sorts of applications, ranging from racing cars to dentistry.
For example, mountain bike brand, Atherton Bikes, uses the RenAM 500Q to produce titanium lugs for its bike frames. The frames themselves are built using carbon fibre tubing, joined together using the AM titanium lugs. Opting for a high productivity machine has made it quicker for Atherton to design and manufacture race-winning bikes and build a solid business case that would not have been possible only a few years ago.
The RenAM 500Q has also been used by precision industrial manufacturing company, Knust-Godwin, to handle serial production for down-the-hole oil field instrumentation. As a company that produces large, complex parts for extreme environments where downtime costs millions of dollars, AM technology allows high quality to be maintained and rapid response times to build components for the oil and gas industry.
www.renishaw.com