www.industryemea.com
11
'19
Written on Modified on
Optical Gas Imaging Tools for the Oil and Gas Industry
Visualizing hydrocarbon gases helps prevent venting to the atmosphere
By Craig O’Neill, Strategic Business Development Manager, FLIR
Infrared (IR) thermal imaging cameras have been used for decades for a variety of oil and gas applications, including electrical/ mechanical inspections, tank level inspections, and even examinations of pipe integrity within process equipment. In recent years, new optical gas imaging (OGI) technology has been developed which can “see” hydrocarbon gases and volatile organic compounds (VOCs) that are venting or leaking to the atmosphere. OGI can be used for meeting regulatory emission reduction requirements, while also helping to reduce product loss, which in turn provides positive return on investment. OGI cameras are a huge time saver compared to other inspection technologies and also offer safety advantages for operators. Major energy companies are using OGI cameras like the FLIR GF320 to quickly check thousands of components and identify potential gas leaks in real-time.
Technologies for reducing fugitive emissions in oil and gas applications
The U.S. natural gas industry as a whole emitted 162.4 million metric tons CO2 equivalent of methane in 2015.[1] In addition to regulatory compliance issues, this equates to lost product for operators. The industry is faced with how to best find and repair natural gas leaks at potential escape points, including compressor stations, processing plants, hydraulically-fractured wells, and along transportation lines.
Before the development of OGI cameras, most oil and gas facilities used a toxic vapor analyzer (TVA), otherwise known as a “sniffer,” to analyze gas concentration levels and quantify gas emitted to the atmosphere. TVAs are reliable, relatively low cost, and can identify most gases. The disadvantage compared to an OGI camera is that the operator must know exactly where to go to look for the fault – and physically touch it. In other words, sniffers are like playing pin the tail on the donkey, while optical gas imaging is the same game – but without a blindfold. Also, OGI is considerably (5-10 times) faster than a sniffer.
Optical gas imaging also offers several safety advantages over a traditional TVA. It enables remote detection of a gas that could potentially explode or cause health issues to those breathing in the gas. OGI cameras enable operators to remain at a safe distance away during inspections. Rather than standing in a cloud of gas, they can remain on the ground, point to a spot 10 or 20 feet high, and determine if it is leaking gas into the atmosphere.
Looking deeper at optical gas imaging
An optical gas imaging camera is a highly specialized version of an IR or thermal imaging camera. It consists of a lens, a detector, electronics that process the signal from the detector, and a viewfinder or screen for the user to see the image produced by the camera. [2]
Optical gas imaging can be likened to looking through a camcorder – the operator sees a plume of gas blowing out that would otherwise be completely invisible to the naked eye. The gas plume looks as if it is emanating from a burning object, almost like smoke from a cigarette or a cigar.
To see this plume of gas, an OGI camera uses a unique spectral filter method that enables it to detect a particular gas compound. The filter is mounted in front of the detector and cooled along with it to prevent any radiation exchange between the filter and the detector. The filter restricts the wavelengths of radiation allowed to pass through to the detector to a very narrow band called the band pass. This technique is called spectral adaptation. See Figure 1.
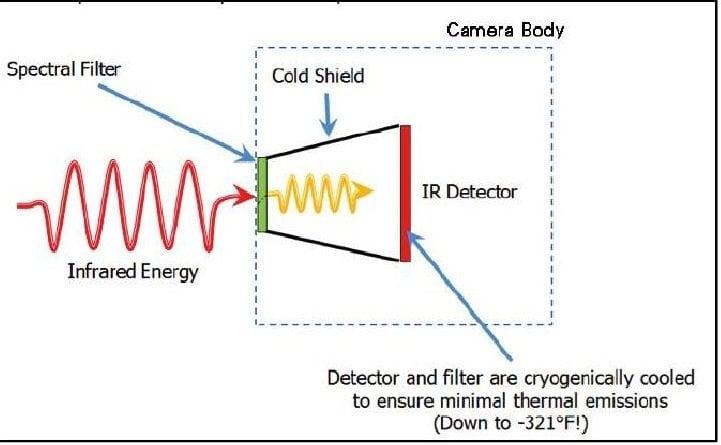
OGI cameras use quantum detectors that require cooling to cryogenic temperatures (around 70K or -203°C). Midwave cameras that detect hydrocarbon gases such as methane commonly operate in the 3-5 micrometer (μm) range and use an indium antimonide (InSb) detector. Longwave cameras that detect gases such as sulfur hexafluoride tend to operate in the 8-12 μm range and use a quantum well infrared photodetector (QWIP).
OGI cameras take advantage of the absorbing nature of certain molecules to visualize them in their native environments. The camera focal plane arrays (FPAs) and optical systems are specifically tuned to very narrow spectral ranges, on the order of hundreds of nanometers, and are therefore ultra-selective. Only gases absorbent in the infrared region that is delimited by a narrow band pass filter can be detected. For the majority of gas compounds, infrared absorption characteristics are wavelength dependent.
For example, the yellow region in Figure 2 shows a spectral filter designed to correspond to the wavelength range where most background infrared energy would be absorbed by methane.
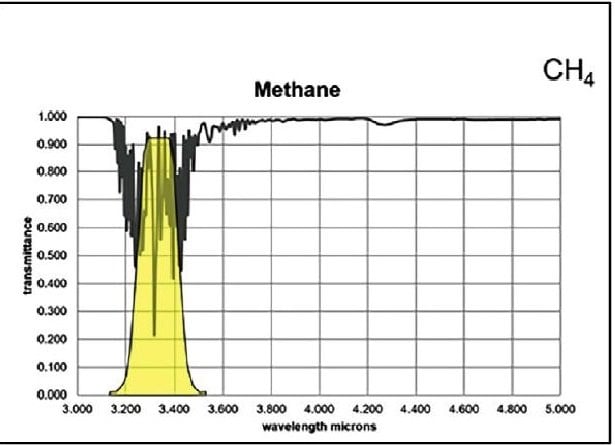
If the camera is directed at a scene without a gas leak, objects in the field of view will emit and reflect infrared radiation through the lens and filter of the camera. If a gas cloud exists between the objects and the camera and that gas absorbs radiation in the band pass range of the filter, the amount of radiation passing through the cloud to the detector will be reduced. To see the cloud in relation to the background, there must be a radiant contrast between the cloud and the background.
To sum up the keys to making the cloud visible – the gas must absorb infrared radiation in the waveband the camera sees; the gas cloud must have radiant contrast with the background; and the apparent temperature of the cloud must be different than the background. In addition, motion makes the cloud easier to see.
Regulatory standards guide technology used to detect gas emitted to the atmosphere
Several regulatory standards affect which technology is used to detect gas emitted to the atmosphere. The sniffer remains the required method for some oil and gas regulations, with OGI cameras a secondary tool. For newer regulatory standards in the U.S. oil and gas industry, OGI is considered the best method, with the sniffer the secondary method.
The Environmental Protection Agency’s Method 21 - Determination of Volatile Organic Compound Leaks, specifies that optical gas technology can be considered an alternative work practice (AWP) for complying with Method 21. (The sniffer was the method originally specified, and operators must still use the sniffer method once per year.)
In 2016, the EPA issued Quad Oa, short for Code of Federal Regulations (CFR) 40, Part 60, Subpart OOOOa. These amendments to the EPA’s New Source Performance Standards (NSPS) define emission standards for volatile organic compounds (VOCs) and quantify necessary emission reductions. Quad Oa includes methane regulations that require upstream oil and gas facilities to limit emissions; the regulations apply mainly to well pads and compression stations. For Quad Oa, optical gas imaging is considered the best system of emission reduction (BSER).
In addition, Environment and Climate Change Canada (ECCC) and Alberta Environment and Parks (AEP) have recently launched new regulations that will require inspection of all equipment with either an optical gas camera or a sniffer by 2019.
Other countries around the world are likely to implement regulations similar to these proactive North American emissions control and methane reduction regulations in the years to come.
New OGI technology ideal for oil and gas applications
In recent years, new technology has come on the market to meet the need for OGI for oil and gas applications. For example, the FLIR GF320 works with the Providence Photonics QL320 to give users the ability to reduce emissions while quantifying benefits in terms of liters per minute, or grams per hour emitted – useful information for those looking for an economic justification for an optical gas imaging program. Not only can it be used to stop emissions and quantify leak detection program effectiveness, it can also be used to quantify and prioritize repairs. Embedded GPS data helps operators identify the precise location of faults and leaks, for faster repairs.
Another innovative technology from FLIR is the GFx320, an OGI camera that has been independently certified as Intrinsically Safe for Zone 2 and Class 1; Div 2 environments. This Intrinsically Safe designation means surveyors can work confidently inside critical safety zones and hazardous locations.
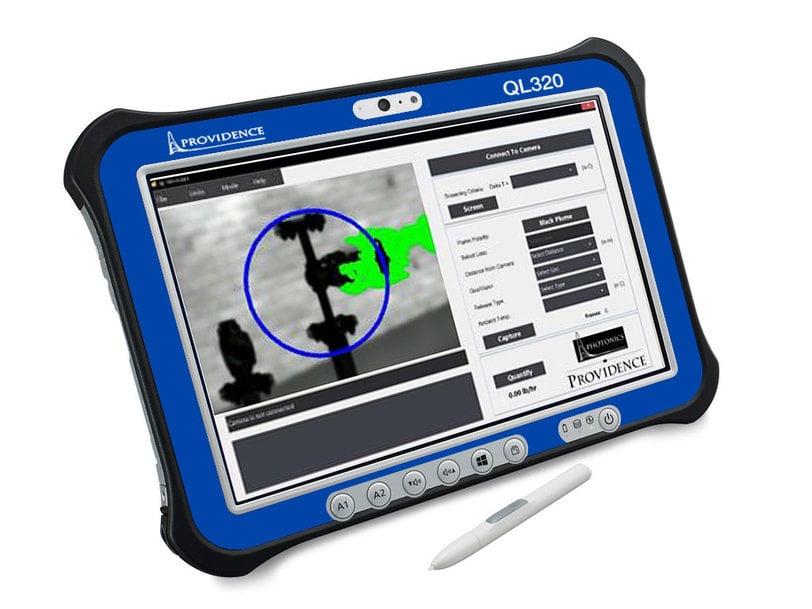
In addition, the FLIR optical gas imager can also be used to measure temperature as part of the more typical IR camera electrical/mechanical inspection tasks, so the cameras actually offer dual purpose functionality.
Optical gas imaging reduces costs and improves safety for major oil and gas companies
Optical gas imaging has been used to comply with regulations while saving money and improving operator safety. One example is Wyoming-based Jonah Energy, which began using optical gas imaging technology in 2005 to find fugitive emissions at its production facilities.[3] The company inspects 150 facilities every month, and inspects the 1,700 wells within a one-year period. Jonah uses a FLIR GF320 infrared camera for methane and VOC detection, providing visual confirmation of leaks as small as 0.8 grams/hour.
Jonah Energy found that the main advantage of the FLIR GF320 is its ability to scan large areas and visualize gas plumes in real-time. This helps inspectors pinpoint the source of fugitive emissions and begin the repair process immediately, making OGI inspections more efficient than Method 21 surveys. In fact, during a field study conducted for the City of Fort Worth, TX, surveyors determined that scanning with infrared cameras was at least nine times faster than performing Method 21 scans on the same site equipment.
The speed of OGI scans makes it easier for oil and gas producers to survey equipment more often. The EPA notes that more frequent inspections and repairs can reduce fugitive methane and VOC emissions significantly. For example, quarterly surveys can cut emissions by 80 percent, while semi-annual monitoring surveys and repairs can reduce emissions by 60 percent.
Since 2010, Jonah has reduced fugitive emissions by 75 percent. It also reduced repair time from 705 hours to 106, cut labor costs from $58,369 to $7,500, and dropped its gas losses from $348,000 to $20,500. Emissions in tons went from 351 to 31.
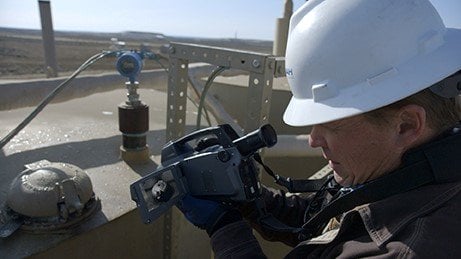
Jonah Energy says that their monthly Leak Detection and Repair (LDAR) program using OGI technology has been both effective and consistently profitable. Their cumulative gas savings exceeded $5 million in the past six years, which more than covered the overall program costs.
Another example is ConocoPhillips, which performed an optical leak detection and measurement pilot study at 22 CPC facilities to test best management practices for fugitive emissions management. The study findings were used to evaluate the benefits of using OGI technology as part of fugitive emission management plan for the company’s Canadian operations.[4]
The study identified 144 leaking components, which collectively amounted to about $358,000 in lost product. The lost product resulted in methane leaks contributing more than 21,000 tons per year of carbon dioxide equivalent (CO2e) to greenhouse gas (GHG) emissions. The study estimated that 92 percent of the sources could be repaired economically, resulting in net present savings of more than $2 million.[3]
Inspectair, a leading international supplier of specialist remote visual inspection technology and solutions, relies on the FLIR GF320 optical gas imaging camera for both maintenance inspections and hydrocarbon leak detection in hydrocarbon production plants or for the inspection of any material that uses hydrocarbon as a fuel. They find the GF320 camera can scan a broader area much more rapidly and monitor areas that are difficult to reach with contact measurement tools
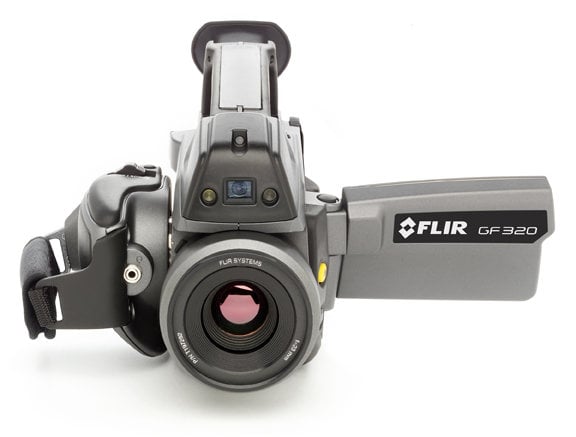
“We have been using certain contact measurement tools like laser detectors or leak sniffers,” says Inspectair’s Cailean Forrester. “But the problem is that you have to go right up to the object, which is not always safe or even possible. In other words, this approach is limited and not very precise. With an optical gas imaging camera like the GF320 however, you can keep a safe distance and still detect gas leaks with great precision.”
Ron Lucier, an instructor at the Infrared Training Center in Nashua, NH, cites the importance of being able to check for gas plumes from a safe distance. “Methane and other hydrocarbons are not only flammable, but in high concentrations they can cause asphyxiation,” Lucier explains. “With TVA gas ‘sniffers’ you know the gas is there, but you don’t know how much. OGI users can immediately see the size of the gas plume – something that’s impossible to do with a gas sniffer.”
Innovative product identifies and stops fugitive gas emissions
In April 2018, FLIR received the Technology Innovation Award for its GF320 camera at the Oil and Gas Methane Leadership Awards, given out the Global Methane Forum in Toronto, Canada.[5] The award was given by the Center for Clean Air Policy, Clean Air Task Force, Environmental Defence Canada, Environmental Defense Fund, and the Pembina Institute.
According to the Pembina Institute, “FLIR was selected for its innovative sensing solutions including cost effective hand held cameras that can be used by industry to identify and stop fugitive emissions, thereby protecting the environment and saving money.” They also stated that organizations “have used this technology to identify the source and magnitude of emissions and inform policy development.”
References
1. Inventory of U.S. Greenhouse Gas Emissions and Sinks, - https://www.epa.gov/sites/production/files/2018-01/documents/2018_complete_report.pdf, retrieved 6/14/18, pg 191 (Energy 3-77)
2. The Science Behind Optical Gas Imaging - http://www.flirmedia.com/MMC/THG/Brochures/OGI_012/OGI_012_US.pdf, retrieved 6/11/18.
3. Optical Gas Imaging Saves Money and Resources for Jonah Energy, http://www.flirmedia.com/MMC/THG/Brochures/OGI_014/OGI_014_US.pdf , retrieved 6/11/18.
4. T. Trefiak, ConocoPhillips, OGI Pilot Study: Leak Detection & Measurement, 2006, http://docplayer.net/17797465-Pilot-study-optical-leak-detection-measurement-report-completed-by-terence-trefiak.html
5. Global methane reduction leaders honoured in Canada, https://www.pembina.org/media-release/global-methane-reduction-leaders-honoured-canada, retrieved 6/11/18.