www.industryemea.com
05
'12
Written on Modified on
A very special project – Heavy duty work for industrial gear units from NORD DRIVESYSTEMS in the Alps
In an extremely demanding construction project in the Swiss Alps, at an altitude of around 1700 metres and almost 600 metres inside a mountain, large chambers are being excavated to form the new expanded underground centre of a pumped storage hydroelectric power station that will increase its present power output from 480 MW to 1480 MW. With an extreme incline of 45 degrees and a height difference of approximately 180 m, conveyor systems in a sub-station are transporting 500 t of excavated material per hour, around the clock, using conveyor belts that are driven by NORD industrial gear units.
Photo 1: A NORD SK 12407 industrial geared motor drives the lower conveyor belt
The expansion project “Linthal 2015” will upgrade three existing power station systems and increase their overall output power from 480 MW to 1480 MW.
In contrast to nuclear and river-based plant, pumped storage hydroelectric power stations can rapidly respond to changes in demand. The optimum interplay between these various types of power generation technologies ensures that a reliable and economic power supply is maintained around the clock.
Pumped storage stations assure peak-time energy
Unlike pure storage power stations, pumped storage stations cannot just generate energy at peak times; they can also convert excess power, which is generated during periods of low demand, into valuable peak-time energy. The demand for peak energy is continuously increasing throughout the entire European grid network. Apart from the general increase in annual consumption, another important reason for this is the intensive development of wind energy in the coastal regions of the European Union. This factor results in an increase in the so-called stochastic energy, which depends on random wind conditions and therefore cannot be reliably planned. If power from wind energy is generated in times of low demand, the excess can be used to pump back water into the higher reservoirs of pumped storage power stations. If there is no wind during the day, pumped storage power stations can then cover this power deficit.
Pure hydroelectric power stations have an upstream reservoir. In contrast, pumped storage plants have an additional lower reservoir. If power is generated, water from the upper reservoir flows into the pressure system. The water drives turbines, which in turn power the motor generator. The electrical power which is produced is fed into the grid. After leaving the turbine, the water flows into the lower reservoir. If too much electricity is produced, the water can be pumped back from the reservoir into the higher altitude lake, from where it can be used at a later time to generate electricity.
The scope of the project “Linthal 2015” includes excavation and construction work for the underground central station of the pumped storage power station and the tunnel system for the water that provides the power. Construction of a new heavyweight dam for the higher lake will increase its storage volume from the present 9 million m³ to 25 million m³. Expansion work for the existing compensating reservoir is also included. At an altitude of about 1700 m and some 600 m inside the mountain, the heart of this gigantic expansion project is being created with huge excavated chambers that will house underground stations for the four groups of machinery used in the new pumped storage power facility Limmern. The underground station consists of a 150 m long, 30 m wide machinery chamber with a maximum height of 53 m, as well as a separate transformer vault which is about 130 m long, 20 m wide and 25 m high.
The excavation work for the two chambers is completed. The work has been proceeding rapidly in an intensive 24/7, 3-shift operation. Every day about 800 m³ of rock has been removed from the mountain and in total almost 2,445,000 m³ have been excavated to form both chambers.
Drive systems for conveyors
Industrial gear units are used in the conveyor systems which are located in the central area of the construction project “Linthal 2015”. Two "S-conveyors" convey 500 t of material per hour over a distance of about 260 metres with an extreme incline of 45 degrees and a height difference of around 180 m. The excavated material is conveyed down to a crushing plant. This conveyor belt is driven by a NORD industrial gear unit with brake control, which simultaneously generates electricity. On the second conveyor belt, the crushed material is conveyed up to the gravel plant, where it is stored until it is needed for further processing as construction aggregate for the dams or as concrete for walls and ceilings. This conveyor has a belt speed of 2.2 m/s and is driven by two NORD industrial gear units, located at the right and left of the conveyor system and connected by a common shaft. With a protection class of IP55, these industrial gear units each have a drive power of 250 kW.
The industrial gear units for this massive construction project were developed according to the tried-and-tested UNICASE principle. The UNICASE is a one-piece housing block, into which all the bearing seats are integrated, with production carried out in a single stage using state-of-the-art CNC machines. The concept features extreme precision, rigidity and strength with no joints between the output side and the gear unit which are subject to radial forces or torque. The UNICASE principle enables a more compact design due to the staggered arrangement of the shafts and also allows the use of larger roller bearings that guarantee a long operating life. Industrial gear units can be right or left mounted.
Customer-oriented drive solution
The supplier of this complete drive solution was Getriebebau NORD AG, Switzerland - a member of the NORD DRIVESYSTEMS Group. Guido Eigenmann, Manager of Getriebebau NORD AG, Switzerland explains: "We sell customer benefits - not just products. As well as this we offer a comprehensive service package. In addition to commissioning, we also provide maintenance training, so that the customer knows what to look out for. Many users require not just drive components, but rather complete and functioning system solutions. We tailor our drive solutions to each individual customer." The plant constructor and customer of Getriebebau NORD is Marti Technik AG, which was founded in 2002. The international technology company is one of the many subsidiaries of the Swiss Marti Holding AG. Marti Technik AG is a provider of individual tailor-made solutions, principally focussed on underground construction work. The company predominantly specialises in the field of tunnel boring systems, conveyor technology, switchgear construction, plant construction engineering for stone and earthworks, infrastructure systems (equipment and maintenance) as well as electrical engineering.
Ernst Kuster, head of maintenance and responsible for the conveyor systems is very satisfied with NORD products and services. "The very good cooperation with Getriebebau NORD Switzerland is particularly positive for me. All of our requirements were catered for. What is also remarkable is the high ability to supply. It only took about ten weeks from ordering to delivery. With other suppliers, four or five months are not unusual. All-in-all we are very satisfied – a very good cost-benefit ratio, excellent advice and support, on-schedule delivery and last-but-not-least, NORD products deliver a very high performance and are of very good quality.
Photo 2: Panoramic photo of the dam. All of the conveyors with NORD drives are below ground
Photo 3: A NORD SK 12407 industrial geared motor drives the lower conveyor belt
Photo 4: A NORD SK 12407 geared motor drives the lower conveyor belt
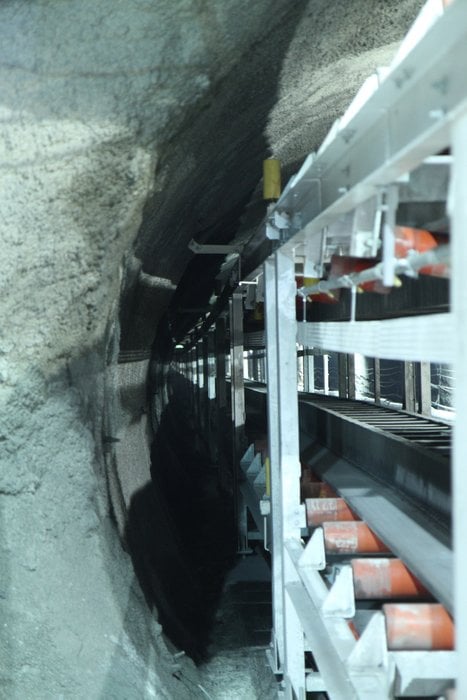
Photo 5: The upper conveyor belt moves downwards and the lower conveyor belt moves upwards
Photo 6: NORD SK 12407 industrial geared motor with brake function and energy recovery (upper conveyor belt)