www.industryemea.com
19
'12
Written on Modified on
Holcim, one of the largest producers of construction material worldwide, relies on drive technology from NORD DRIVESYSTEMS
In its cement plants and concrete factories in Croatia, geared motors of different performance classes are used. Heavy duty is no problem for the NORD products - they are ready for any challenge. That is why both companies have now completed a three-year-contract for the exchange of older drives.
Example I: Quarry
At the Sumber and Ocura quarries, large stones are removed through explosions, transported through conveyor belts between the working floors and bunkers to the preparation facility, then crushed in stone crushers and graded to maximum grain sizes 3.3, 8.8, 16 and 32 mm. After this, they are transported to the storage site through conveyor equipment. Different technologies are available for the transportation of the various materials, which each have their own challenges. The conveyor belts that transport the larger rocks must overcome inclines of up to 25 degrees. Minerals up to 250 µm are conveyed with bucket elevators. Fixed on a double or central chain, a sprocket chain or on a belt, large cup-shaped containers made of steel or plastic are continually loaded with material. For screw conveyors, a helical screw running in a trough transports the goods over several meters. Gravity and friction of the transported material on the trough walls make sure that the material does not rotate with the conveyor screw, but rather is continually transported longitudinally. If the friction on the wall is small with a high degree of filling, the material will only rotate at right angles to the screw axis and is not transported. Thus, with a vertical transport, wall friction must be created through centrifugal force, which requires high rotations in the order of 250 to 400 min-1. The conveyed material can be transported horizontally, inclined at an angle or moved vertically. All of this conveyor equipment is powered by NORD drive systems. Nenad Mackic, facility manager in the Sumber quarry, is completely satisfied: »We value the drive technology from NORD due to its high reliability and efficiency. Service and delivery availability are also the best. For good reason, we have been operating NORD products in our quarries for more than 10 years without experiencing problems.»
Drive spectrum for heavy-weight conveyor applications
NORD drive systems are ideal for all types of conveyors and suitable for almost all grades, lengths and speeds. Variable speed geared motors with frequency inverters are used for small bucket elevators, whilst unregulated single speed geared motors provide the higher performance required for larger systems. Because of the mass to be transported, gentle start-up via a fluid coupling is essential, while a back stop prevents the conveyor equipment from running backwards. With an efficiency of about 95 percent, the gear units are available in a shaft, foot or flange mounted versions to suit the application. The maximum capacity is up to 200 kW with a maximum torque of 50,000 Nm.
Example II: Cement plant
In the Holcim cement plant in Koromacno on the coast of Istria, NORD geared motors have also been used for more than ten years. The plant produces an average of around 500,000 t of cement per year; the maximum capacity is up to 750,000 t. Cement is produced according to a continual drying process, primarily using natural resources. The raw materials (normally limestone, clay, sand and iron ore) are mined in quarries. The material for the Koromacno location is obtained from a mine about 2 km away where the reserves for cement production are enough for 120 years. After the extraction, a crusher mills the raw materials. In the cement plant, all raw materials are crushed and simultaneously dried together in a mill. The raw material resulting from this process is then fired in a kiln at temperatures of about 1,450 °C into so-called clinker, and then cooled to 200 °C. The clinker is then crushed in a mill together with gypsum or anhydrite, yielding the finished cement product.
Drive technology in the cement plant: Ex-protection is also in demand
NORD drive solutions are used for all transportation and conveyor tasks in cement production. Some of the drives are designed for operation in explosive environments according to ATEX Zone 21 or 22. Primarily mid-size geared motors are used: Helical, parallel and bevel geared motors up to 45 kW, mostly with protection class IP55, depending on the respective task. A plus point for the difficult requirements is the UNICASE concept from NORD: All bearing seats and sealing surfaces are machined in a single stage on the latest CNC machining centres. The benefits include extremely high reliability and exceptional sealing with safe handling of even the largest torques combined with high axial and radial load bearing, quiet running, low maintenance and exceptionally long operating life.
User comments
Everyone is extremely satisfied with the NORD drive units in Koromacno. Robert Tencic, head of purchasing and Teodor Gobo, head of maintenance of Holcim Croatia: »We particularly value the high delivery availability and reliability, the very good price-performance ratio, the good service and the unique quality of the NORD products.» Through the modular structure of the products and the very well-coordinated individual components, a particularly large variety of variations and flexibility, along with short planning and assembly times and therefore quick delivery availability can be obtained. Gear units with the best efficiency combined with energy-efficient motors and centralized or decentralized inverters result in diverse system solutions with a very high efficiency and cost effectiveness. Reason enough to sign a three-year-contract, which says that Holcim will exchange older gear motors - independent of the brand - with NORD drive solutions in all factories in Romania, Bulgaria, Hungary, the Czech Republic, Slovakia and the countries of the former Yugoslavia. Holcim can profit from the international presence of the NORD DRIVESYSTEMS Group because NORD is represented in more than 60 countries with its sales and service network.
Image 1: Safe and reliable despite harsh surrounding conditions - NORD parallel geared motor powers a conveyor belt
Image 2: Low maintenance and long-life - NORD bevel helical gear motor powers a conveyor belt
Image 3: Safe and reliable despite tough surrounding conditions - NORD bevel helical gear motor powers a conveyor belt
Image 4: Low maintenance and long working life - NORD parallel gear motor powers a screw conveyor
Image 5: Low maintenance and long-life - NORD parallel gear motor powers a screw conveyor
Image 6: The conveyor technology in the Holcim factory in Koromacno (Croatia) is powered by NORD products
Image 7: The harsh surrounding conditions in the Holcim factory in Koromacno (Croatia) are mastered by NORD drive units
Image 8: The harsh surrounding conditions in the Holcim factory in Koromacno (Croatia) are mastered by NORD drive units
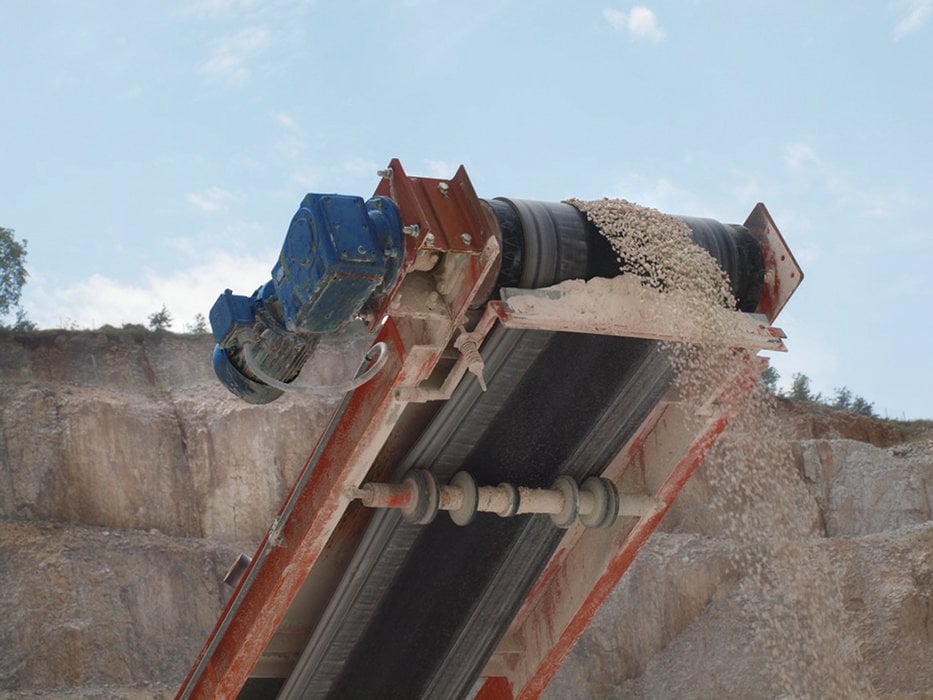
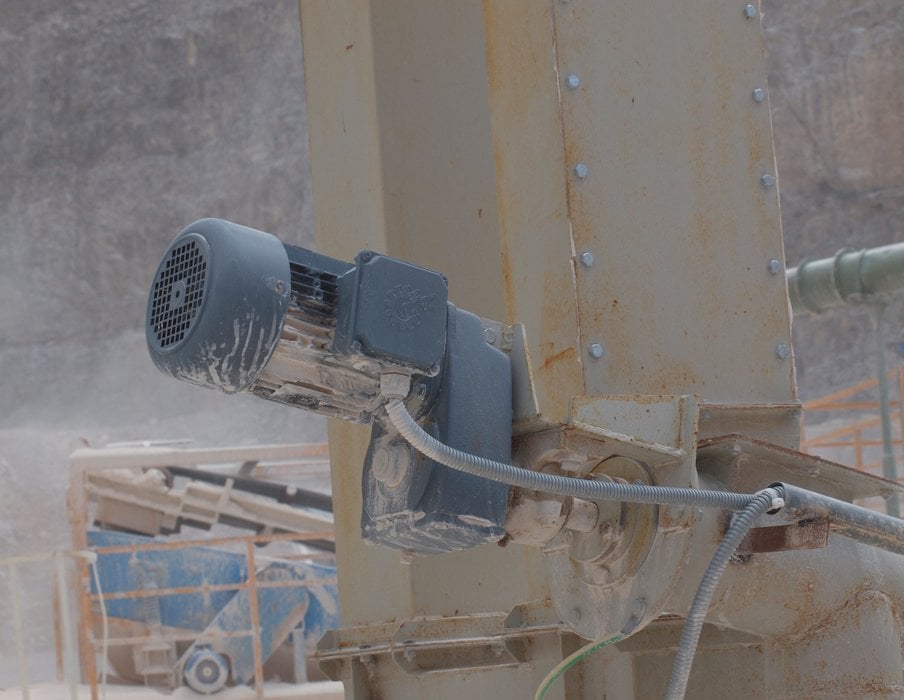
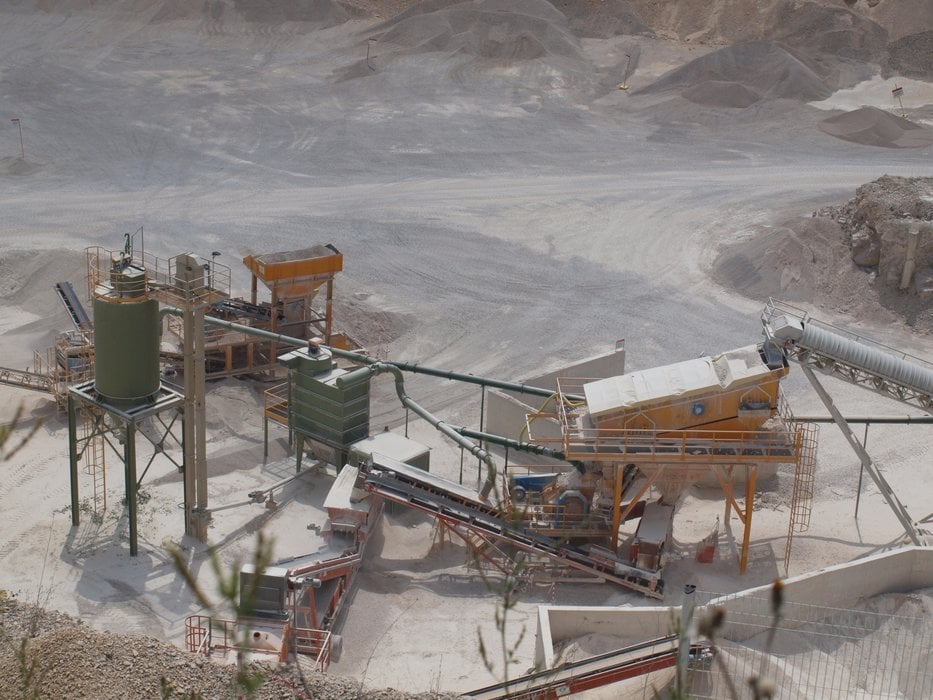
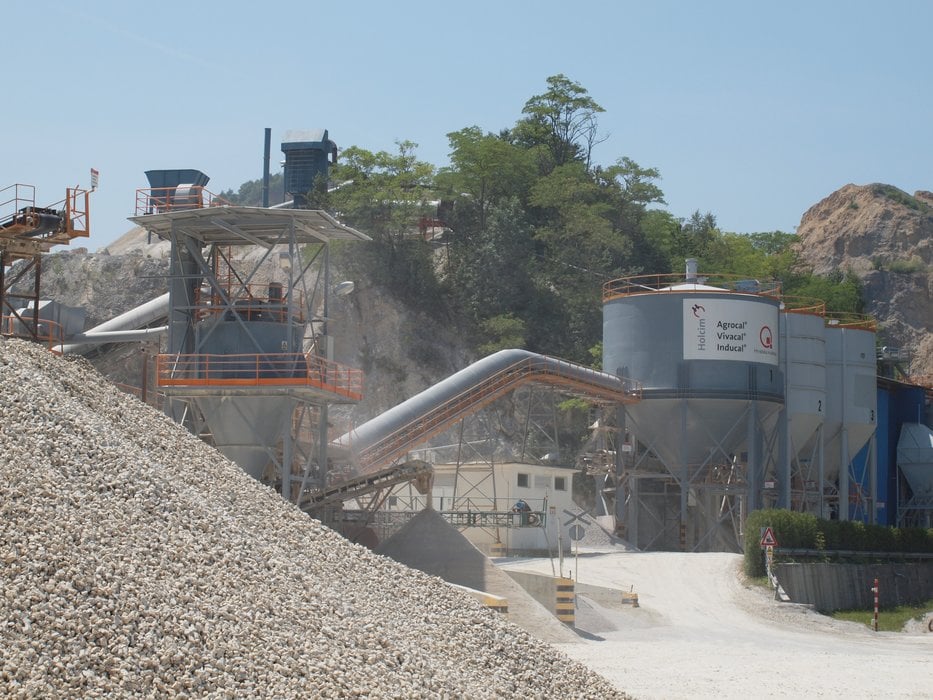
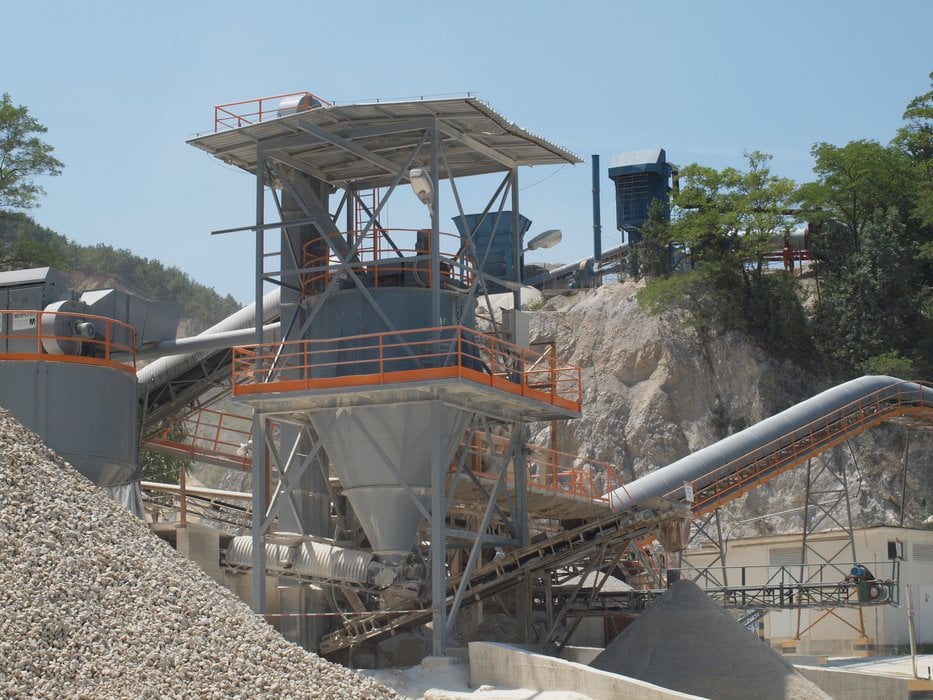