www.industryemea.com
10
'20
Written on Modified on
PACKAGING MACHINERY GIANT, MARCHESINI GROUP, ADOPTS CUSTOMIZED PRODUCTION BUSINESS MODEL WITH STRATASYS 3D PRINTING
Company overcomes the limitations of traditional manufacturing for on-demand, cost-effective production of machinery parts. Twelve industrial-grade Stratasys 3D printers run round-the-clock, making it one of Stratasys’ largest European customers.
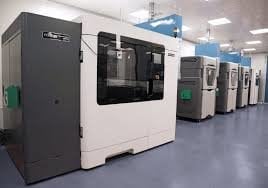
Marchesini Group S.p.A. is a world-leading Italian manufacturer of automated packaging machinery and an established supplier to some of the biggest names in the pharmaceutical, cosmetic and food industries. As one of Stratasys’ largest customers in Europe, the company today reveals how it has embraced an entirely customized production business model to meet the needs of the international packaging sector – with its arsenal of industrial-grade Stratasys 3D printers at the heart of it.
Headquartered in Pianoro, Italy, Marchesini Group has a dedicated 3D printing facility featuring ten Stratasys production-grade FDM 3D printers – a large-scale Fortus 900mc, four Fortus 450mc and five F270 systems – as well as two PolyJet multi-material 3D printers. The technology is used throughout the design, development and manufacture of the company’s flagship cartoning machines, as well as several other packaging lines. Every machine produced is tailored to a specific industry or customer’s production process, which is critical in ensuring optimum performance and efficiency when deployed in the field.
“At Marchesini Group we say that ‘extra-ordinary is our ordinary’, meaning that we are faced with challenging, entirely customized projects on an almost daily basis,” says Mirko Fortunati, Responsible for Coordinating the Mechanical Workshops at Marchesini Group. “However, producing complex, customized parts with traditional manufacturing methods has proved extremely costly and time consuming, which is no longer suited to the growing demands of today’s packaging manufacturing industry.
“Importantly for our business, Stratasys additive manufacturing has enabled us to overcome these issues and adopt a customized production model,” he continues. “Integrating our industrial-grade FDM 3D printers into our production process has drastically reduced our part lead times from several weeks to a few days. Added to that, we can cost-effectively produce the exact quantity of parts we need, without requiring expensive tooling or machining. Having this on-demand production capability enables our engineers to take advantage of the greater design freedom enabled by 3D printing, which has empowered Marchesini Group to achieve higher-quality results for our customers.”
Importantly, this on-demand production capability also extends to maintenance and repair. With its packaging machines installed at customer locations throughout the world, the company is now able to quickly and cost-effectively 3D print customized replacement parts on-demand with no minimum order requirement. Not only does this allow Marchesini Group to deliver spare parts to customers in record time, but it also eradicates the need for costly storage facilities of spare inventory.
Improving machinery performance for customers
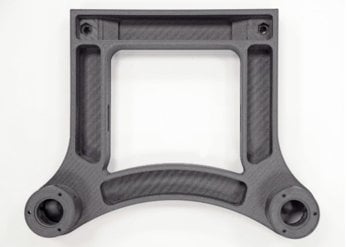
The team has 3D printed thousands of functional parts and components for its packaging machines, including protective cases, cable support systems and junction boxes to name a few. These applications are particularly important for the company’s robotic packaging systems, where every single component matters in order to ensure the robot’s agility, precision and speed of movement. This is an area where high-performance 3D printing materials have made a big impact.
“Using tough thermoplastics such as Stratasys’ FDM Nylon 12CF filament or ULTEM 9085 resin in place of traditionally machined metal components has enabled us to reduce the weight of some parts by at least 30%,” explains Fortunati. “This not only increases the speed of movement and productivity of the robot for our customers, but it also lessens the rate of degradation. These 3D printing materials also comply with specific industry regulations, which importantly enables us to expand this technology into even more production applications – helping us to further innovate our products for customers.”
Marchesini Group is also using Stratasys PolyJet technology to produce parts and components for applications requiring the combination of two or more materials. “One great example of this technology is for the production of grasping pincers, which are designed to handle light items such as package leaflets or smaller jars. With the advanced multi-material 3D printing capability, we can produce complex designs that combine hard and rubber-like materials in one single print – something that would typically take multiple processes to create costing us time and money,” adds Fortunati.
The battery of Stratasys 3D printers within Marchesini Group’s additive manufacturing department is currently running round the clock.
Fortunati concludes, “It’s fair to say that additive manufacturing is an integral part of Marchesini Group production. In 2019 alone, we recorded a total of 22,480 hours of operation for our FDM 3D printing equipment – equating to almost 15 hours a day. For our two PolyJet 3D printers, a total of 1,700 hours of operation, the equivalent of about 8 hours a day. As we continue to expand these technologies across our design and production process, we can expect these figures to be even higher in the future.”
www.stratasys.com