www.industryemea.com
30
'20
Written on Modified on
Schneider Electric Paves the Way for Digital Transformation with Stratasys Additive Manufacturing
Puente la Reina plant wins Schneider Electric’s ‘Smart Factory’ award for accelerating Industry 4.0 transformation with Stratasys FDM technology.
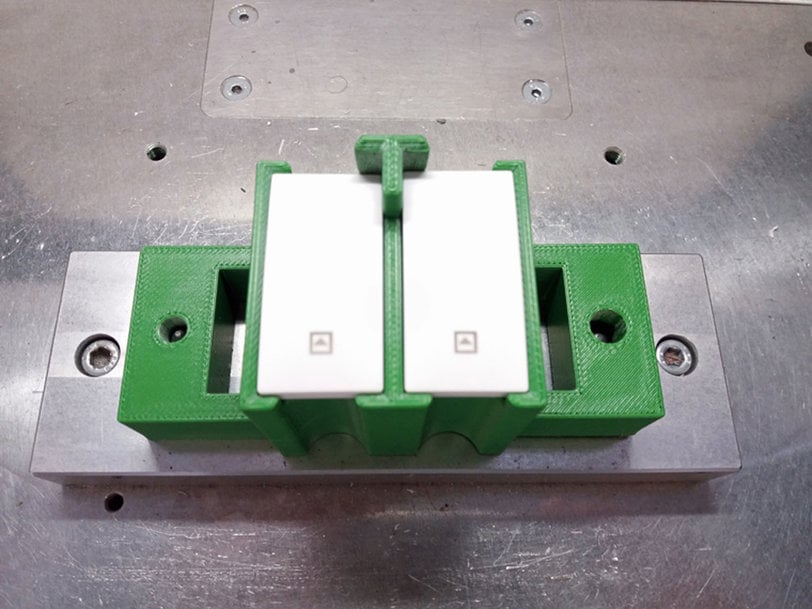
Over the past year, industrial giant Schneider Electric has embarked on a large-scale Industry 4.0 implementation across its worldwide operations. Named the ‘Smart Factory’ project, the company is strategically deploying cutting-edge technologies and the benefits of the Industrial Internet of Things (IIoT) to drive process optimization. Designed to increase operational efficiency and reduce costs for its customers, the initiative has been rolled out to every factory across the globe with each plant challenged to embrace innovation and drive digital transformation.
One of the company’s shining lights has been the Puente la Reina plant in Navarra, Spain, which has strategically adopted Stratasys FDM additive manufacturing throughout its production process. The plant is reporting significant efficiencies across its tooling operations in particular, which has led to the management team receiving high-level recognition within Schneider Electric. In fact, the Puente la Reina plant was recently named winner of the internal European-wide ‘Smart Factory’ Schneider Electric competition – recognizing the acceleration of the plant’s Industry 4.0 transformation for the vast quantities of 3D printed manufacturing tools produced, the outstanding time and cost savings achieved, and newly optimized supply chain efficiencies.
“In the past year, using Stratasys FDM additive manufacturing we’ve achieved a saving of about €20,000 in the production of assembly-line tooling alone, which has easily paid off our original investment in the F170 3D printer,” says Manuel Otamendi, Industrialization and Maintenance Manager – Global Supply Chain at Schneider Electric’s Puente la Reina plant. “With this technology we’re able to produce new high-performance production tools in just one day, whereas it would have taken at least one week to outsource the same tools previously. This crucially reduces our dependency on suppliers and gives us much more control over tool
production, which has increased the overall flexibility of our manufacturing process and accelerated our time-to-market for many products.”
Optimizing tool production across the factory floor
Purchased through Stratasys’ local partner, Pixel Sistemas, Schneider Electric’s industrial-grade Stratasys F170 3D Printer is deployed for a range of tooling applications, including assembly-line tools, jigs, fixtures, robot grippers and other end-of-arm tools – all of which were previously outsourced to third parties and produced using expensive injection molding or CNC processes. The F170 has become a staple workhorse on the Puente la Reina factory floor, cranking out over a hundred new production tool designs a year.
One such example is the production of grippers for robotic arms on the assembly-line. Leveraging its F170 3D Printer, Schneider Electric has come up with new application ideas for the grippers to not only improve the performance of the robots, but also secure major cost-savings.
“It’s not uncommon for aluminum parts of the mold to break when they collide, and when they do, be very expensive to replace,” explains Otamendi. “To circumvent this, we are now able to replace costly aluminum grippers for robotic arms with 3D printed alternatives. Not only does the 3D printed tool offer the same mechanical performances as the traditional tool, but importantly it ensures protection of more expensive aluminum parts when the molds collide. Should the 3D printing tool break, we can quickly 3D print a low-cost replacement within hours.
“To put the cost-saving into perspective – outsourcing a machined gripper used to cost us 200 euros per tool. Now we can 3D print one on-demand for around 100 euros each. The ability to also reduce the complexity of our supply chain is very important to us right now, so having this on-demand production capability in-house is essential,” he adds.
Digitalizing Operations for Increased Efficiencies
Having enjoyed significant cost-savings and a more streamlined production workflow since integrating Stratasys FDM additive manufacturing, this has had a positive knock-on effect on the plant’s overall manufacturing efficiencies and reduced time-to-market in key areas.
“Additive manufacturing has transformed the way we work and changed our entire mindset in terms of the way we think about doing things in the future,” says Otamendi. “While we will continue to utilize our F170 to further optimize the tooling process, we are actively exploring how to leverage other high-performance FDM materials in the Stratasys F123 3D Printer Series to address final end-use part applications on the production-line. The increased application use of this technology will play an important role for us in achieving our digital transformation objectives.”
Yann Rageul, Director Manufacturing Solutions EMEA at Stratasys, says, “As we work our way through the global pandemic, we’ve seen clear indications that additive manufacturing can play a key role in enhancing the traditional supply chain and conventional production lines. As business leaders seek to reoptimize their operations, we expect to see an increase in company’s adopting the technology at a strategic level such as Schneider Electric, who continue to successfully drive digital transformation across the business. Not only does additive manufacturing enable them to increase flexibility within production and reduce dependency on suppliers, but it also opens up the ability to make significant operational efficiencies across product development. While this may be a common objective for most businesses, the impact of COVID-19 has amplified its importance even further.”
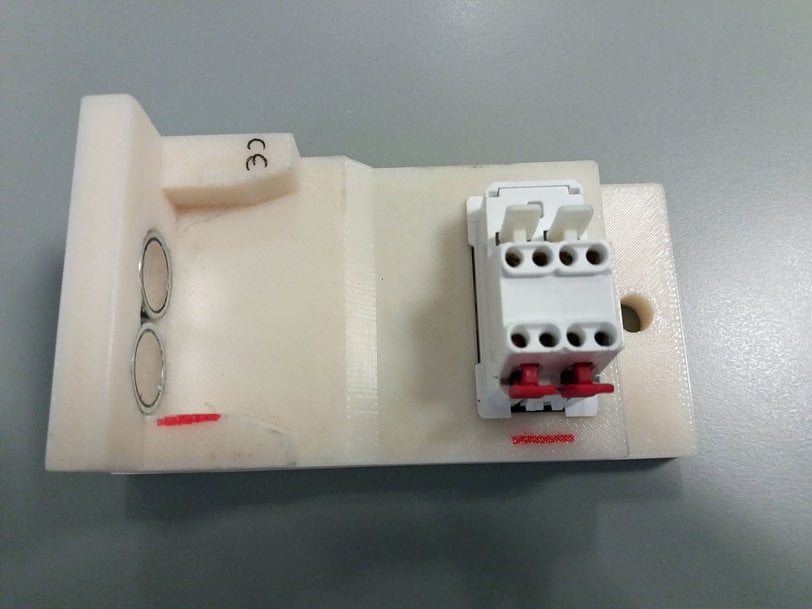
3D printed assembly-line tool designed to hold switches during laser marking operations. Produced in ASA material using the Stratasys F170 3D Printer
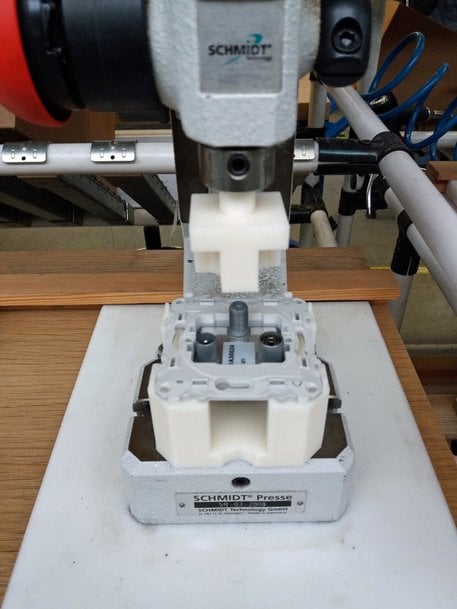
Schneider Electric designs and 3D prints the support tool and upper tool of its hand presses – optimizing assembly-line efficiencies
www.se.com