www.industryemea.com
07
'13
Written on Modified on
Advances in seat control systems for the commercial vehicle sector
The need to accurately control the position of the driver’s seat on both on and off-road commercial vehicles is long-established, with the function being integral to both safety and comfort. Meanwhile, the desire for seat levelling – returning the seat to its original position after it has been lowered to allow the driver to comfortably enter or exit the vehicle – is also now widely established. John Morris of Norgren, an international market leader in pneumatic motion and fluid control technologies, explains the technology behind seat control and seat levelling and the options available to modern commercial vehicle designers.
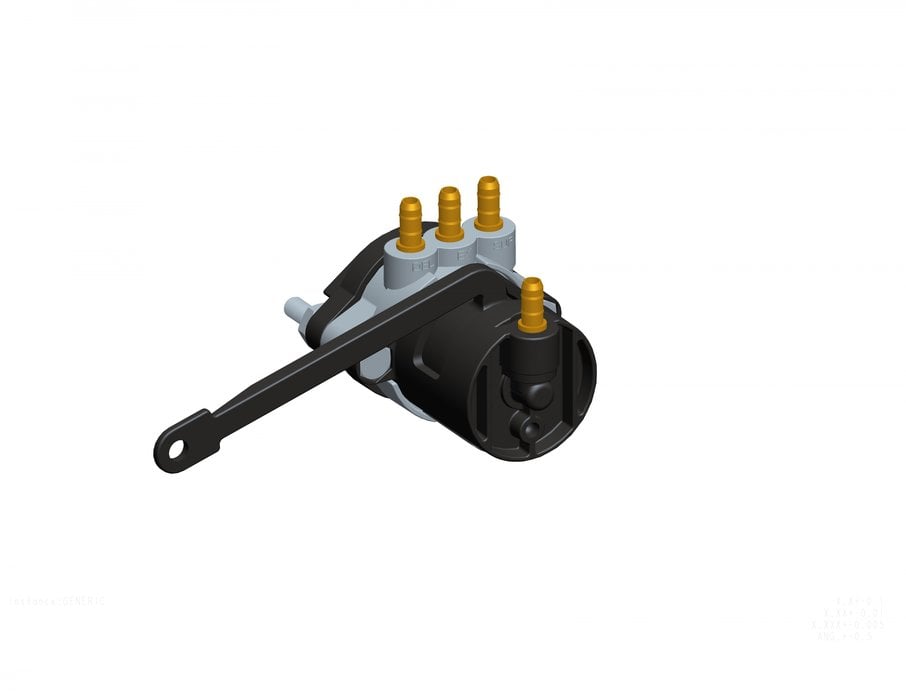
Pneumatically controlled seat adjustment valves allow, at the simplest level, adjustment of the height of the seat through the inflation and deflation of l this rubber bellows or ‘air bag’ within the seat base.
While it is in theory a relatively straightforward process for the driver to position the seat to their own personal requirements, the limited space available within the cab in most modern commercial vehicles means that for the driver to access or leave the vehicle comfortably, the seat needs to be lowered to allow sufficient space for the driver to manoeuvre comfortably under the steering wheel.
This then causes an issue as the driver must manually reposition the seat before they can start their journey – a particular nuisance on multi-drop runs where the driver may be required to leave the vehicle several times a day -which drove the development of the first automatic seat levelling systems.
Essentially these systems are based around a levelling mechanism which automatically senses the height of the seat and is able to return the seat to that position after it has been lowered for the driver to enter the vehicle. This eliminates the need to hold down a button to readjust to the required height after the seat has deflated.
The simplest systems are mechanically operated and function by linking a pneumatic levelling valve to the seat’s vertical movement. Height adjustment is achieved by altering the levelling valve’s neutral position through a system of mechanical links and/or cables to an accessible driver interface. These systems are generally a cost-effective option, but the downside is that not only can they lack accuracy and refinement, but their adjustment mechanisms take up more space than the alternatives and can be more difficult to integrate into the vehicle seat.
At the other end of the scale are solenoid valve and switch-controlled electrical systems. These systems have been commercially available for 10 to 15 years at the higher specification end of the market. They offer a number of benefits – they use electrical switches with the controls routed though wires which are easily integrated into the seat alongside other electrical functions. They can also be ‘smart’ with computing power meaning they can calculate the optimal ‘time averaged position’, while high-specification memory can store the preferred seat positions of several different drivers – a key advantage on vehicles which are commonly used by driver teams.
Most systems also offer some form of safety adjustment zone – where the levelling system can be used to prevent the operator from adjusting the seat to be too close to its vertical travel limits, reducing the risk of injury to the driver. Levelling systems also offer automatic leakage compensation, whereby if the seat’s air bag system loses some pressure, air will automatically be added into the air bag to preserve the adjusted height.
An option which delivers high levels of functionality and ease of integration without a premium in terms of cost draws on the very latest in pneumatic technologies. These systems employ a simple, air-operated disengaging clutch which can be integrated with a rotary pneumatic seat levelling valve. When the clutch receives an air signal while adjusting seat height, it automatically decouples the levelling valve from the seat during the adjusting process. Once the desired height is reached and adjusting is ceased, the clutch re-engages the levelling valve and ‘remembers’ this new seat position. Under normal circumstances, the clutch is inactive and the seat and levelling valve operate together as normal.
The levelling valve can be mounted anywhere in the structure of the seat where the full stroke of the seat can be converted to approximately 120 degrees of rotary valve motion. In many circumstances, a simple two-bar link is all that is required.
A further option is the integration of a ‘rapid dump valve’ - a 3/2 valve which can be used to rapidly deflate the seat’s air bag and so bring it to its lowest position for easier ingress and egress while disabling the automatic levelling action. When the driver returns, the deflate switch is restored to normal mode and the levelling valve automatically brings the seat back to the height from which it was ‘dumped’.
These modern pneumatic systems offer cost benefits compared with electrical systems and are simple to integrate with existing platforms as there is no need for any special mechanical adjusting linkage or control, while their functionality far exceeds that achievable with previous pneumatic control systems.
These advanced systems are becoming more and more the preferred option for vehicle and seat manufacturers worldwide seeking to achieve higher end functionality and ease of integration without the costs associated with electrically controlled designs.
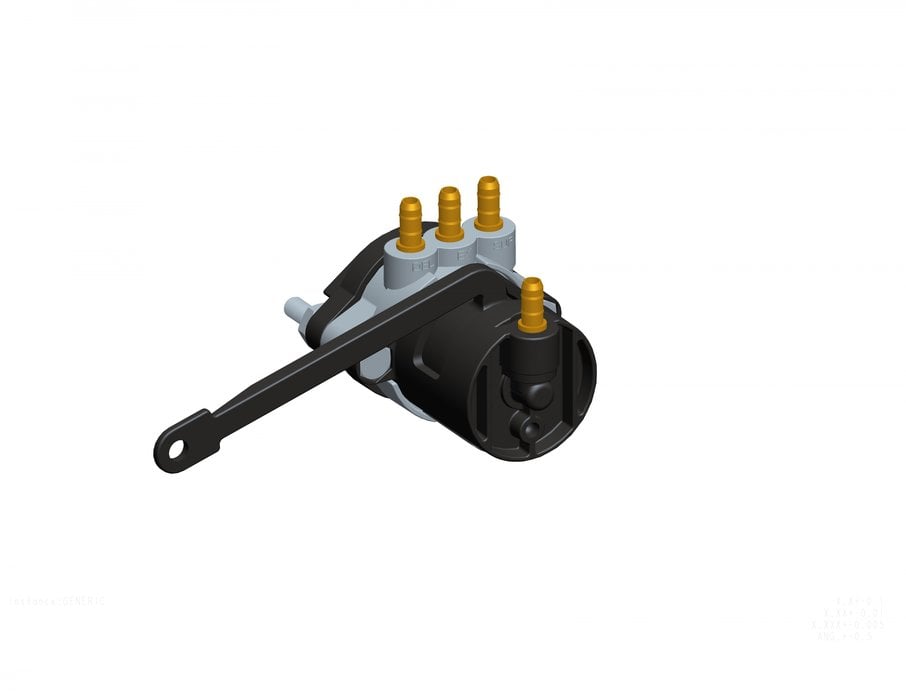
The heart of the new seat control system is a simple, air operated clutch that is integrated with the seat levelling valve.