www.industryemea.com
03
'20
Written on Modified on
Mobile robot revolutionizes semiconductor manufacturing process - Using image processing in robotics for transporting highly sensitive wafers
With the Semi Mobility Solution, KUKA has taken a decisive step in semiconductor production automation. Until recently, robotics have been used in the individual production steps. Kuka has created a mobile robot that is also responsible for transporting the highly sensitive wafers from station to station. On board the robot is an image processing system from Cognex that is high-performing, yet compact in size.
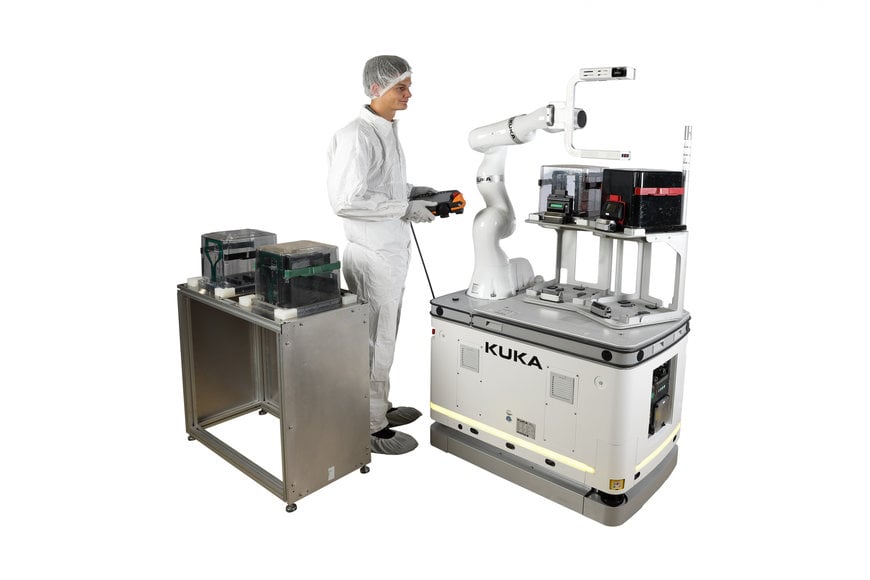
Semiconductors’ performance dictates the pace of innovation. This applies just as much to industrial automation as to digital communication via cell phones, laptops, smart building technology, and the automobile industry. And the market is continuing to grow. In 2018, the international semiconductor industry achieved $481 billion in sales revenue and this figure is set to reach $525 billion as early as 2022 according to a study by PwC.
The robotics industry is also taking advantage of this trend, as, for example, the latest generation of controls and controllers offer additional functions. Conversely, however, the innovative capacity of robot manufacturers is also accelerating the efficiency and productivity of microprocessor manufacturers.
For example: KUKA offers a wide range of extremely flexible robots that can also be quickly tailored to a whole variety of handling requirements, as the life cycle of semiconductors is short and the market correspondingly volatile.
Mobile handling system for cleanrooms
Using robotics, individual production steps can be automated very well and to a high-quality standard. However, up until now, robotics have not been used to transporting semiconductor substrates (wafers) from one workstation to the next. Ideally, semi-conductor manufacturers would prefer end-to-end automation, because pristine cleanroom conditions can be much better achieved with “unmanned production.” Until now, however, this aspect of the process was untenable due to the lack of precision with which mobile robots move and grasp.
KUKA has now developed the world's first single-source solution for the automated transport and handling of semiconductor cassettes: the “Semi Mobility Solution.”. In this instance, a lightweight robot from the LBR iiwa series is mounted on a KMR 200 CR autonomous automated guided vehicle (AGV). The AGV can maneuver in the smallest of spaces and KUKA's engineers have developed a sophisticated gripper system for the handling.
System solution: AGV plus robot arm plus gripper
The Semi Mobility Solution goes to a handover point where wafer transport boxes are located. When the AGV has reached its destination, the robot arm is in place to precisely determine its position with the help of an integrated image processing sensor and performs a fine calibration.
This moves the robot into the position to grasp the transport box with a high degree of accuracy and deposit the sensitive wafers without any vibrations in a storage space on the AGV platform. Using this approach, the robot can pick up and transport two different sizes of boxes for wafers with a diameter of 200 or 300 mm. Once it has reached its destination, the robot puts down the transport boxes on the respective processing line.
The Semi Mobility Solution moves around the room on the basis of stored destinations but chooses the route there itself. The navigational capacity of the LBR iiwa platform enables it to move autonomously in a safe and sensitive way. Environment tracking is supported by laser scanners. They perceive the environment in real time, thus preventing collisions.
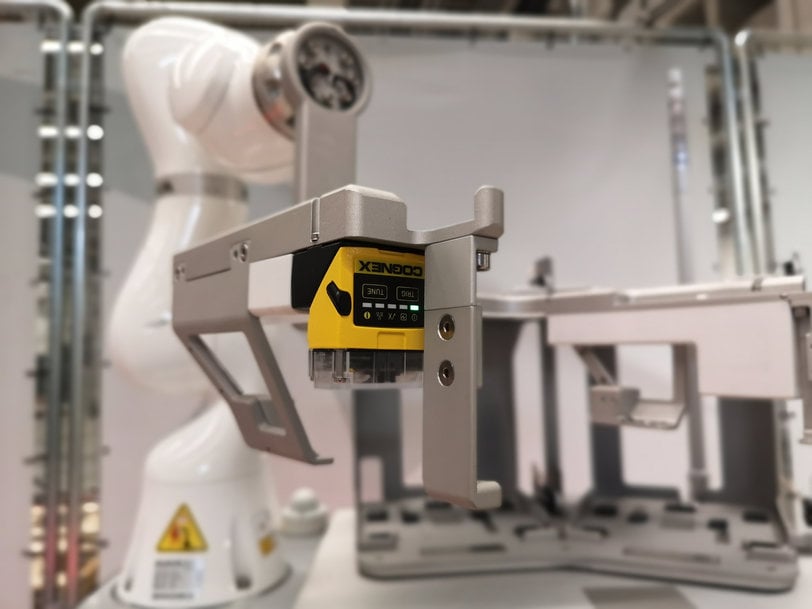
The safety-oriented environment recognition also creates the preconditions for being able to use the platform as a cobot (collaborative robot) without a safety fence near the operators. The gripping process itself is guided by image processing. Extremely high precision and reliability are essential in this process, because the wafers are sensitive. Vibrations must be avoided.
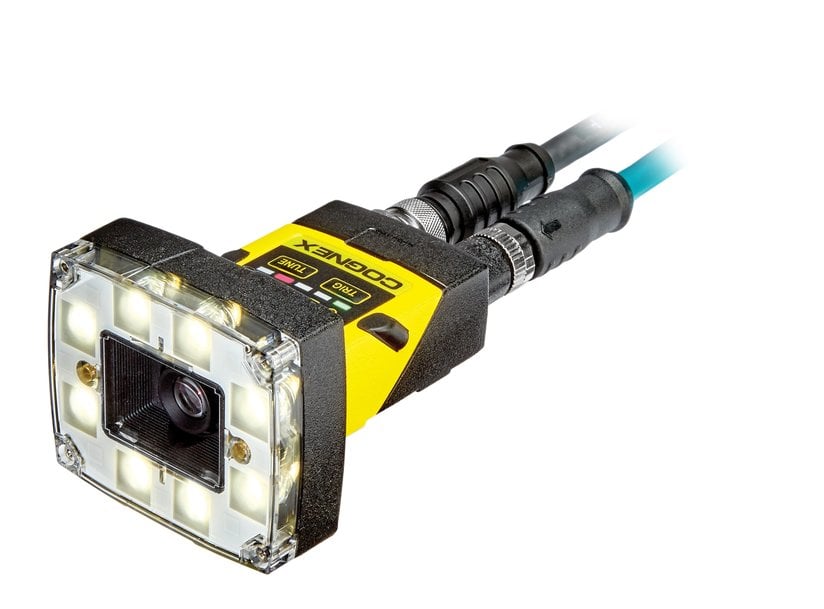
Image processing: High-performance in a compact space
When selecting the image processing system to guide the robot, KUKA's developers chose Cognex’s In-Sight 2000 sensors. These sensors combine the performance of image processing systems with the ease and low cost of an industrial sensor. They also offer maximum flexibility when mounting in space-constrained environments. This attribute was highly desired in this application because the IP sensor travels on the robot arm. Minimizing wiring requirements was also a key criterion and the In-Sight 2000 provided easy integration via Ethernet and PoE connections, which was another factor behind the decision.
In addition, KUKA's engineers appreciate the fact that with In-Sight 2000 the logic circuit is integrated into the device and the image processing quite simply lets itself be taught. Ralf Ziegler, Business Development Manager Electronics at KUKA: “The extensive communication possibilities that the sensor offers, its ‘built-in’ intelligence and the good programmability are also advantageous.”
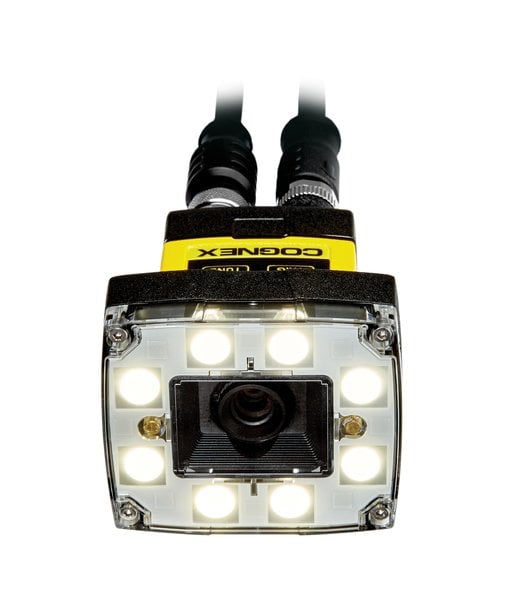
Another advantage for the In-Sight 2000: The In-Sight 2000's patent-pending integrated LED lighting provides uniform illumination over the whole image, regardless of the prevailing lighting conditions. This is particularly important in mobile applications because there is not the same lighting everywhere and even the time of day or the season can affect the image quality.
In practice: IP-controlled fine positioning over the last few centimeters
In practice, the Semi Mobility Solution first drives the robot gripper up to the transport box. At this point, the image processing is activated. It recognizes the offset from the destination point stored in the control system and on this basis references the position of the gripper, which can subsequently grasp the respective transport box with the required high degree of millimetric precision. An integrated calibration function guarantees consistently accurate positioning.
KUKA has already delivered the first Semi Mobility Solutions to international semiconductor manufacturers. The mobile robots work under cleanroom conditions and are certified in accordance with ISO Class 3 (IPA), UL 1740 and UL 1998. They can also be used in a fleet and using Cognex’s state-of-the-are image processing grasp the boxes with the highly sensitive wafers both reliably and accurately. This innovative solution marks an important automation step in the microprocessor production chain.
Tried-and-tested cooperation between KUKA and Cognex
Cognex supported KUKA during the development of the Semi Mobility Solution through the choice of the sensor, as well as providing global end user support.
Supplying the In-Sight 2000 for the Semi Mobility Solution is not the first collaboration between KUKA and Cognex. Cognex's sensor and camera systems are also used in the high-performance “KUKA.VisionTech” solutions for image processing algorithms that KUKA has developed. For example, they enable reliable quality or completeness checks to be made on components even in unstructured environments.
KUKA appreciates working with Cognex not only for the high-performance products and solutions but also because of their straightforward collaboration and global presence. Ralf Ziegler: “With our partner Cognex, we can offer our clients and integrators good solutions and comprehensive support all around the world. If spare parts are needed, Cognex can supply our clients and integrators within a very short space of time.”