www.industryemea.com
23
'20
Written on Modified on
The digital transformation of track vacancy detection
How digital add-ons help to reduce maintenance costs and enhance process quality
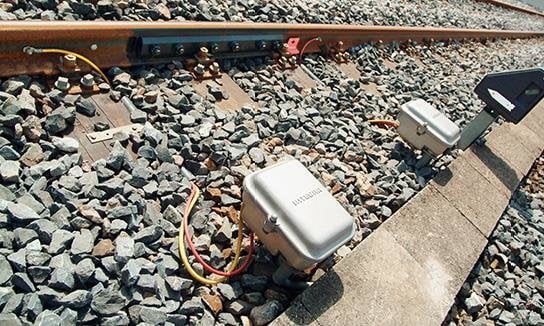
Whether it is local transportation in urban and suburban areas or mainline and regional railways, in rail transport delays cause enormous economic damage every year. Delays are also one of the biggest annoyances for passengers and for customers of rail-bound freight transport. Rail operators suffer not only from the negative
impact on their image but also from the cost of delays and the maintenance required to remedy them.
But what is the best approach for increasing the availability and reliability of rail systems and reducing maintenance costs for preventive and corrective actions? The answer is digitalization. That also applies to rail automation and track vacancy detection. Smart digital solutions create new potentials for even more reliable and
efficient operations management, ensuring more on-time trains, and expending less effort on maintenance, while ensuring safety and security.
Track vacancy detection is changing
An integral part of today’s rail automation are track vacancy detection systems that supply information about whether a track in a particular section is clear or occupied. This allows safe, trouble-free, and efficient signaling and operations management. Due to the growing use of digital interlockings as a systematic step in the development of electronic interlockings as well as the demand of generic interfaces by customers, this change is also happening in track vacancy detection. In many places and countries, the previously widespread track circuit technology has long been replaced by the superior axle counting systems. The development of those systems continues, enhancing additional functions and system benefits and adding new digital features. The goals: increased availability, cost-effective maintenance, and intelligent diagnostics are just a few examples.
But it takes more than state-of-the-art axle counting systems to really minimize reaction time, optimally increase process quality, and reliably avoid failures and infrastructure-related faults. In addition to innovative designs for products and product architecture as well as product configuration with 3rd party products, intelligent asset performance monitoring and management and intelligent engineering concepts are important solutions for keeping everything up and running.
From the tracks up to the cloud
Axle counting for track vacancy detection starts at the track level with hardware components like outdoor wheel detectors. They detect the passing wheels and the pulses are transmitted via trackside cable to evaluator modules.To keep maintenance effort to a minimum, Siemens Mobility offers highly robust, reliable, and even maintenance-free components and redundant concepts that increase the reliability of axle counting. The whole axle counting system has been developed even according to CENELEC EN 50126 , EN 50128, and EN 50129 standards and conforms to the highest safety integrity level, SIL4. These products can be configured within a system architecture providing the required security level. Digital add-ons help to get even more out of rail data by supporting operators and maintenance staff with valuable information on the performance
and the current and predicted condition of the axle counting components.
Smart outdoor hardware on the track
The Clearguard counting heads from Siemens Mobility consist of a wheel detector and a trackside connection box. The wheel detector uses a double-sensor technology with no electronics within the sensor itself that allows outstanding robustness. The joint algorithmic evaluation of the output signals of the conventional axle counting sensor and the second sensor ensures the reliable identification of every single wheel. In order to avoid systematic errors for example, during project planning of the axle counting point computers – the second sensor differs from the existing axle counting sensor in terms of its hardware and/ or software. This plausibility check procedure suppresses miscounts. The functionality of wheel detection is still preserved if either the axle counting sensor or the second sensor detects a wheel overrun, so that the availability of the entire system is increased.
Thanks to their innovative technology, Clearguard counting heads are less sensitive to environmental changes and operate under all weather conditions. They provide high resistance to miscounts and false readings like those produced by rail wear, wheel flange reduction, flooding, dirt, or small metal mass like cans and also immunity to reverse currents, magnetic rail brakes, eddy-current brakes, balise train-mounted antennas, and many kinds of EMC interference. By installing the sensor on above a sleeper, using only a different screw, it can be kept during track work.
The counting heads transmit the information on the detected wheel passage only via a two-core cable to a trackside connection box that is protected against lightnings and from there to the indoor Clearguard ACM 250 modules installed in the interlocking building. They can be located up to 21 km away from these evaluation units. To reduce time and costs related to the perimeter and station blocks, the system can also provide detection information to two independent ACM 250 modules.
Indoor evaluation hardware with a higher degree of digitalization
The Clearguard ACM 250 modules evaluate the signal pulses transmitted by the wheel detection components and compare the number of axles entering a track vacancy detection section with the number of axles leaving it. They also monitor the track vacancy detection sections and transmit clear or occupied indications to the interlocking. They can also transmit sensor and/or block information via ACM-ACM Ethernet communication.
The electronic Clearguard ACM 250 modules were developed to offer a more digital and economical solution and offer a redundant product architecture and a dual Ethernet network for high availability. Each module has two of its own IP addresses and can therefore be integrated into redundant network systems. In the event of a connection failure, communication between the module and operations control system is still possible, which ensures maximum operational reliability.
The modules are equipped with a programmable ID plug with its own software, which simplifies the handling of critical software changes: The configured data can be transferred to a replacement Clearguard ACM 250 module by simply removing and then reinserting the ID plug. To configure an axle counting system, one or more Clearguard ACM 250 modules are connected to an Ethernet network via switches. The modules are mounted on a rail and need no further access from the back: Cables are mounted to the modules from their bottom. Therefore, to replace a module during corrective maintenance only a short time slot is needed. The rail mounting also allows using existing cabinets for installation. The switches and power supply modules are standard automation modules that are available worldwide.
Digitalization also improves the diagnostics: LED indicators on the module’s front panel permit simple diagnostics on site. But the diagnostic data can also be forwarded to higher-level systems via a standardizable OPC UA interface in a single or redundant configuration. The ability to communicate with the integral Website (IP address) allows remote diagnostics via Internet or intranet from any location at any time. The integrated HTML5 Website allows the current status information to be requested: for example, using a tablet.
Shared data visibility increases operational efficiency
To remain competitive in the future, rail operators need to make the most of their assets, including axle counting and track vacancy detection systems. The software solution Clearguard APM combined with MindConnect Rail and MindSphere is a new way to acquire important insights along the operation lifecycle of the components; to identify hidden potentials in engineering, process, diagnosis, and event data; and to realize tool-supported maintenance strategies. With Clearguard APM and the integrated axle counting solution, operators and maintainers will benefit from a railway-specific ready-to-use application and extension that address major use cases involving connected assets like asset information and management systems, operation collaboration tools, and performance monitoring and predictive insights. It enables secure access from anywhere at any time so that all parties can react quickly. Especially for preventive maintenance, the digital add-ons prove to be beneficial. Because of the rare service needs and long maintenance intervals of the highly robust axle counting system, the service staff usually require instructions or guidelines if there is a need for action. The digital add-ons deliver such guided support. They also allow a more condition- and need-based reset and recalibration of the system: Instead of a fixed annual turn it is done when it is actually necessary due to detected changing environments and track conditions.
Benefits of successful asset performance monitoring with Clearguard APM
• Increased availability: The shared availability and visibility of railway data minimizes reaction time, speeds up diagnostic and troubleshooting, and therefore reduces downtime. The statistic and analytic function also provides the necessary tools for predictive maintenance.
• Increased punctuality: The transparent database allows measures to be identified that can help make the installation more robust.
• Enhanced operational performance: Thanks to performance monitoring, maintenance costs can be minimized to just-when-needed interventions. It also reduces reporting tasks for staff so that they can spend more time in the field. And the remote diagnostic option optimizes the movement of maintenance staff.
• Safe and secure operations: The performance monitoring also contributes to the operational safety. Of course, data integrity and cyber security is always given, using security solutions and components like the Data Capture Unit for secure data transmission.
System architecture for the digital performance twin
Capturing, analyzing, and using the comprehensive operation data generated by intelligent axle counting systems and components requires a digital performance twin. This twin is a virtual representation of the physical product or process that is used to predict the performance characteristics of its physical counterpart. It consists primarily of a data pool that is created in real time and updated continuously.
To design a digital performance twin requires:
• construction and master data on the physical object
• product connected IoT sensors that record the operating data
• a highly secure data diode that separates the OT network from the IT network
• a cloud where all the data comes together in a digital twin platform
• analytics algorithms that continuously examine, analyze, and interpret the platform data and make their findings available to other applications
The architecture for Clearguard APM is easily structured. The axle counting system Clearguard ACM 250 generates and transmits data to MindConnect Rail. MindConnect Rail utilizes all functions of the Siemens CoreShield Data Capture Unit (DCU), a compact and easy-to-install, but highly effective data diode that offers wide-ranging
protection of critical systems from cyber threats and secure, real-time data access at the same time. In this case, the Siemens CoreShield Data Capture Unit is used to secure the data transmission to MindSphere, the cloud-based, open IoT operating platform from Siemens. There are various deployment opportunities available with secure data access, from self-administration and on-premise license to a managed services approach with well-defined service-level agreements and a cloud license.
Conclusion
Digitalization offers great opportunities for rail operators to improve the transparency and therefore the reliability and availability of their track vacancy detection while also reducing maintenance costs and corrective actions. The process begins on the field and automation levels, where a more digital solution like Clearguard ACM 250 minimizes downtime and service efforts by using digital features to simplify configuration, fault rectifications, and device replacements – which enables system redundancies and supports intelligent diagnostics.
Digital add-ons like MindConnect Rail and the DCU for safe and secure connectivity and Clearguard APM for advanced asset performance monitoring and management take the system transparency, condition monitoring, and maintenance predictability of axle counting systems to the next level: Rail operators acquire more and precise information, analytics, and recommendations for making better and faster decisions. When indicators show that the performance of the track vacancy detection system is deteriorating, the digital add-ons also forecast the deteriorating performance and recommend actions that will prevent a further deterioration or equipment failure. Many adjustments can be done remotely, preventing many hours or even unnecessary operations in the field. If measures are really needed on site, service technicians are supported with guided instructions on rarely needed measures – and with precise information on the failure and location. Therefore, they know which material or tools they need to bring with them straight ahead, reducing maintenance time and effort.
The digital transformation of track vacancy detection is becoming more and more essential for ensuring punctuality and adherence to timetables, maintaining the assets’ condition over the long run, and guaranteeing efficient and secure processes, reliable risk assessments, and reduced maintenance costs and corrective actions.
www.mobility.siemens.com