www.industryemea.com
07
'14
Written on Modified on
Keyence's IM-6500 helps improve and speed up DBC Décolletage's quality inspections
Keyence's new ultrafast 2D metrology system gives the French subcontractor a leading edge.
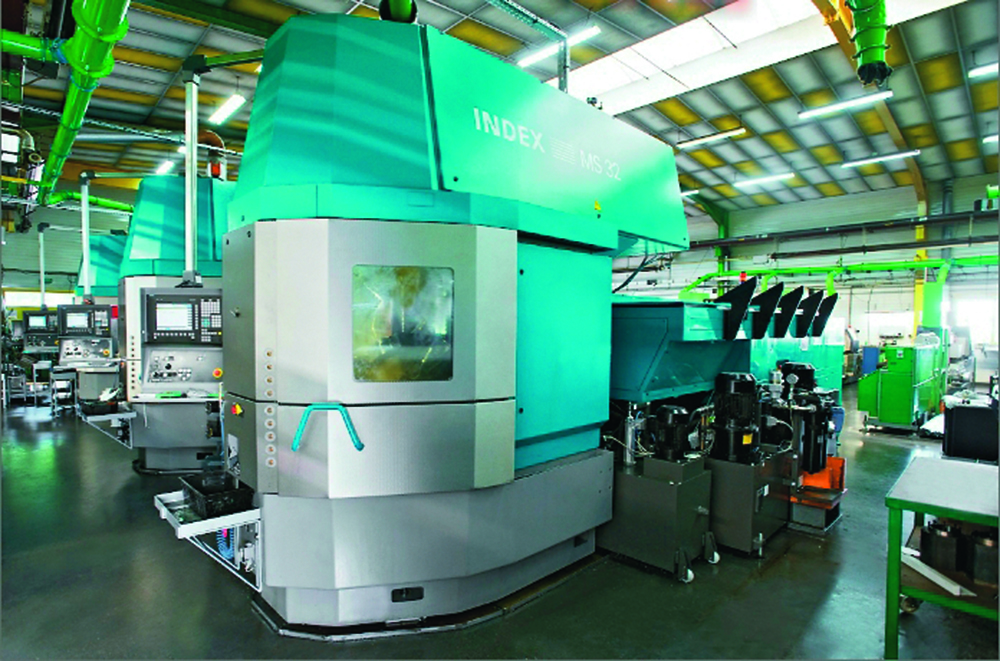
"The system is very simple to use and our entire production team knows how to use it for in-process part inspection. Before acquiring the IM Series, it took as long as ten minutes to obtain measurements. Now, you simply press a button and you get measurements five seconds later. We try to maximise the number of inspections we do. Around 300 programmes are inspected with the IM-6500 on 3500 different types of part," says for Quality Director David Firinu.
"It enhances the quality of our process and products in two ways – it allows us to inspect more dimensions much more frequently, and it eliminates variations caused by operators or measurement conditions," adds Mr Firinu.
Before acquiring the IM-6500, DBC used to perform the same measurements using instruments such as a profile projector or a micrometer.
The IM-6500 Series is a new type of measuring instrument. More than just a profile projector, a measurement microscope or an automated CNC measuring system, the IM-6500 Series image dimension measurement system is a new tool that obtains reliable measurements in a minimum of time. Simply place a target on the stage and press the button. Up to 99 points are measured in a matter of seconds with 0.5-micron accuracy. The IM-6500 eliminates tedious positioning of targets and the risk of measurements being affected by variations in operator skill levels. When edges are extracted manually with the naked eye, discrepancies between operators or due to differences in skill levels are virtually impossible to avoid. Furthermore, the longer the travel length of the XY stage, the greater the number of vibration-induced errors.
Measurements are performed automatically. The Intelligent Pattern Analysis Search System (iPASS) determines the position and orientation of targets by comparing their shapes against those of recorded targets. Anything can be measured, from inside diameters, circular pitches and angles to the most complex dimensions.
With an accuracy of one-hundredth of a pixel, Keyence's proprietary sub-pixel processing system detects edge positions more accurately than conventional vision systems. The IM-6500 Series offers a resolution of 6.6 million pixels, allowing repeatability of 1 micron and accuracy of between 2 and 5 microns.
DBC's strategy is to differentiate itself from its competitors, particularly subcontractors based in low-cost countries, through its service, its quality and the technical excellence of its products. "The IM-6500 allows us to produce complex parts and guarantees that we can check all their dimensions quickly," says Mr Firinu.
DBC's quality department is supported by a fully computerized and quality logistics system. Backed by its extensive inspection methods, DBC aims for zero defects and focuses on quality as a way to differentiate itself from its competitors. The company has been ISO/TS 16949 certified since 2006. DBC produces short-, medium- and long-run parts (from 100 to 10 million parts) from any type of metal or plastic for the connector, automotive, aerospace, medical and other sectors. DBC also assembles finished and semi-finished products.