www.industryemea.com
03
'14
Written on Modified on
All in one: One cable for all applications
Single-cable technology in servo drives: More than ten years of practical experience
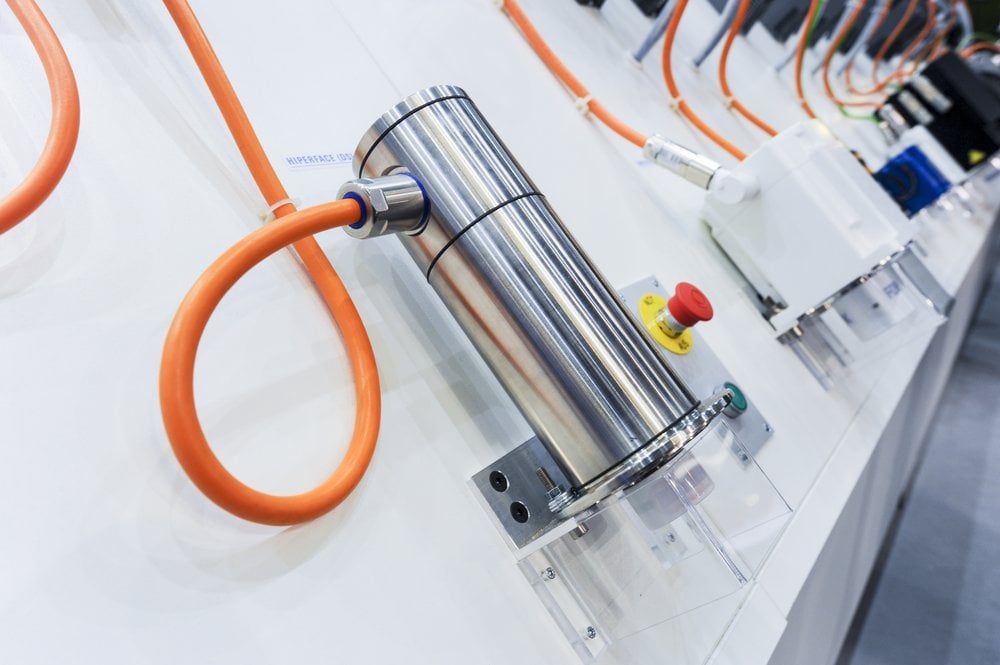
The key theme of the discussions is essentially recognized; and the questions from neighboring disciplines, too. It goes something like: when does decentralized drive technology become worthwhile? When is it advisable to leave the frequency converters in the control cabinet? How high are the additional costs for shielded motor cables in centralized solutions when compared to higher device investment in robust "outdoor technology" with a high degree of protection? Machine and plant engineering now faces a similar question once again regarding the single-cable technology of servo motors. Kollmorgen brought this option onto the market ten years ago and now offers them as standard for synchronous servo motors of the AKM series.
At the time when Kollmorgen was developing the first AKM synchronous servo motor in single-cable technology, innovation was dominated by individual customer solutions. Today such close-knit partnerships in development are appropriately described using the term "co-engineering". The experience with single connection cables that has been amassed since then shows that the benefits of this trend in technology – which is currently being revived by other manufacturers – are only achieved in full if the conditions for application are appropriate.
Quick routing
The benefits of connecting servo motors to their controllers with just one cable are enjoyed across the entire value-added chain in machine engineering. As encoder signals from the synchronous machine are physically transmitted via the motor cable, one interface is no longer necessary. The saving is realized through the omission of a cable and two plug connections. As a result, installation times are reduced, as is the space requirement for the cabling. The benefits have their price, of course, and this is in the cables themselves. Motor and encoder cables form part of the standard portfolio of recognized cable manufacturers. The same goes for connectors. The high production quantities combined with established technologies have a natural cost-reducing effect. However, if feedback and motor cables are inserted into a casing, then special attachments, impedances and particularly special shieldings are necessary. Solutions of this kind are thus no longer to be described as "market-standard" – with a corresponding impact on the price. Ignoring monetary aspects, cable lengths of over 50 meters are viewed critically, because with such systems they lead to faults. Additionally, continuously increasing integration as a whole is viewed sceptically by the cable manufacturers. For example, if one single wire breaks, then the whole cable has to be replaced, even though the rest is still functioning perfectly.
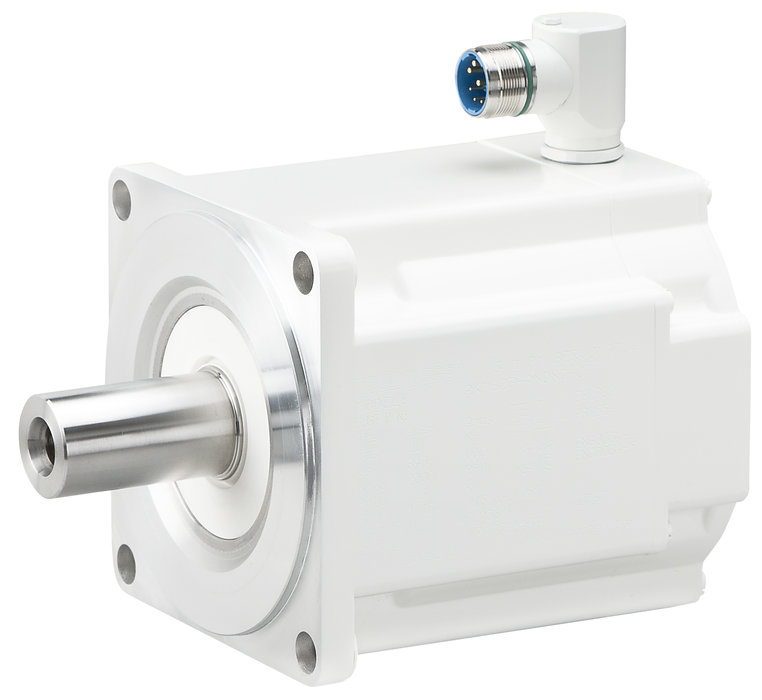
AKM servo motors in the "Food" or "Washdown" design are available for applications in the packaging and food industry.
SFD: the digital resolver interface
As part of total costs of ownership and life-cycle costs, Kollmorgen has devised a solution for its own products that brings savings to the customer from the first meter onwards between motor and servo controller. Compared to other industry solutions distance is shorter, because Kollmorgen found
a way to continue using resolvers, instead of more expensive feedback systems, from the very beginning. In this regard, using the Smart Feedback Device developed around ten years ago, the inexpensive yet robust technology becomes a digital feedback system with 24Bit resolution on the motor and regulator. The main task of the digital resolver (SFD interface) is to convert the analog encoder information internally into an interferenceresistant, purely digital RS-485 signal.
With the conversion from analog to digital, Kollmorgen clears the way for being able to address the motors in the automation system, for example. The company's own SFD also boasts an EEPROM which has saved all relevant motor data as an electronic ID plate. This configuration allows automatic setup on the controller and ID plate recognition with all specific motor parameters in the controller. In practice, users benefit from shorter commissioning times and altogether more convenient and fault-free engineering, which is not ordinarily available with traditional resolvers. An additional benefit: The monitoring of the temperature sensor in the motor is integrated within the SFD via the digital position feedback, also without additional cabling work.
Different feedback, one cable
If an application renders higher feedback system resolutions necessary, then a servo motor with Hiperface DSL interface simply comes into use – and without changing the cables. Kollmorgen has designed the single-cable servo solution so well that a universal cable-type can transmit the signals both from the digital resolver SFD and from the digital encoder. The advantage of this multi-functionality: One cable for everything means fewer warehousing costs, reduced variance in material planning and documentation, and cheaper purchasing opportunities from higher volumes.
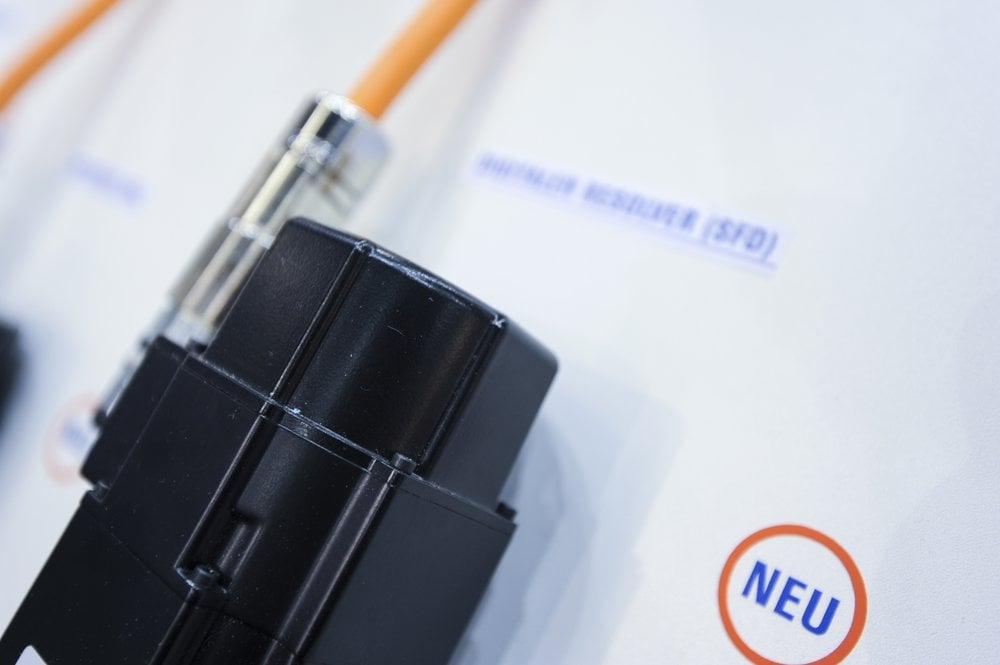
With its Smart Feedback Device (SFD), Kollmorgen has had a digital feedback system for a long time which unites benefits for many common applications under the generic term "digital resolver SFD".
In their basic versions, the AKD motors are equipped with a two-pole hollow-shaft resolver and, together with the AKD servo controller, with the digital SFD resolver interface that has already been mentioned. By way of options there are high-resolution Hiperface/DSL, BISS, or EnDat encoders and a Comcoder (incremental encoder with commutation). The variety of feedback systems ensures that drive solutions can be designed functionally and therefore also price-competitively, even in single-cable connection technology, scaled from a standard kit of motors and servo controllers and beyond.
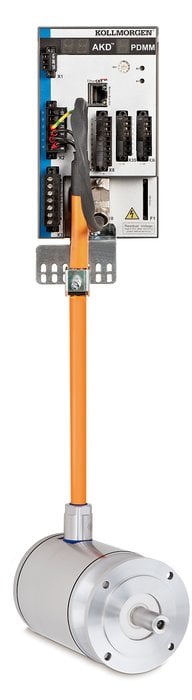
Kollmorgen also offers single-cable technology for a combination of servo motors and intelligent servo converters of the AKD PDMM range with integrated position control.
In machine and plant engineering, standardization brings you the advantage of a reduction in parts diversity, and thus also the related costs of stockpiling and keeping spares. With regard to performance, with 28 housing and length combinations the AKM series covers a wide range of applications with holding torques of 0.16 to 180 Nm. Speeds of up to 8,000 rpm also enable use in high-speed applications. Due to the high power densities, the motors can be compared with small power packs.
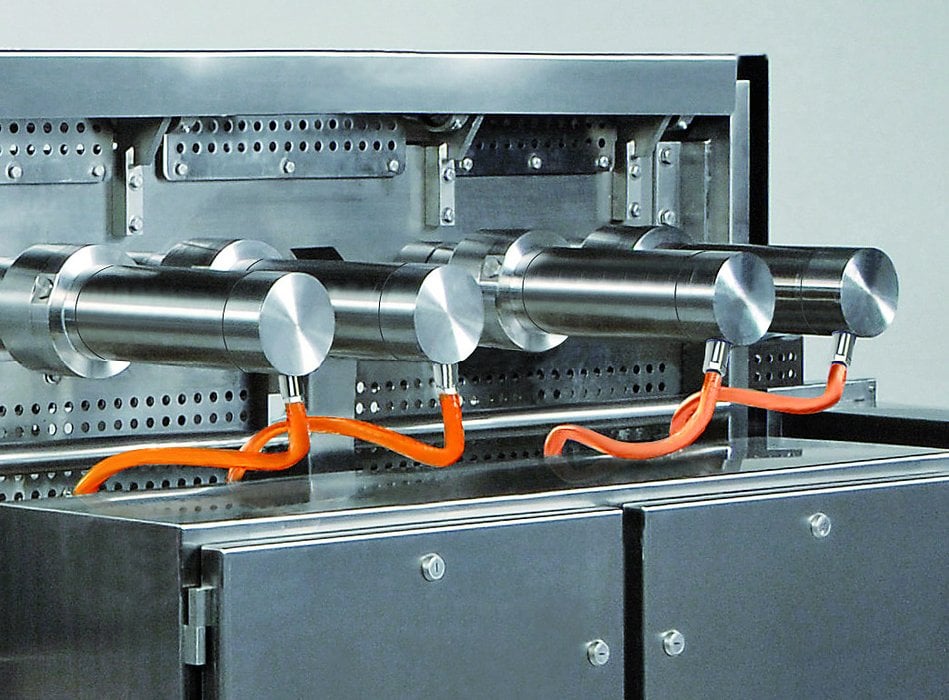
Single-cable technology offers machinery and plant constructors measurable savings from the very first meter of cable length.
The Bottom Line
The greatest benefit is derived from single-cable technology in machines that are spread out spatially with single axes that are also distributed and have long cable lengths. Long routes are also the key issue with decentralized drive technology, with the difference that the servo controller is placed right next to the motor or is integrated directly inside the motor. As feedback signals that are critical to functioning are to be transmitted with the new trend in single-cable connection technology, increasing importance is placed in the issue of shielding and compensation with this installation technology. Power cables that have been established to date are therefore not to be taken into consideration. Instead, specially shielded cables with modified impedances are used.
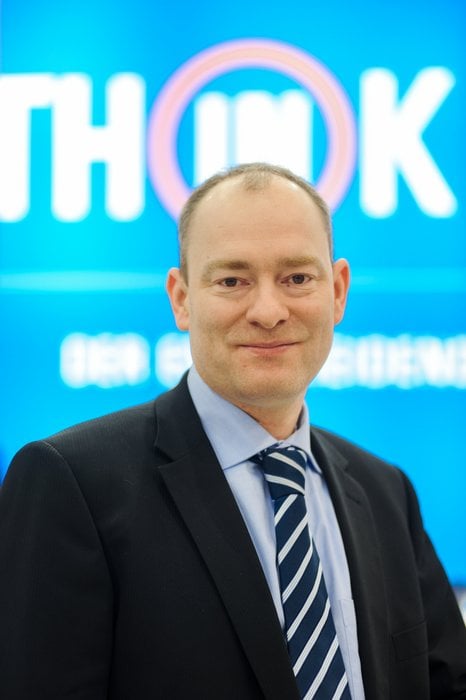
Author: Dipl.-Ing. Jörg Peters, Head of European Product Management, Kollmorgen, Ratingen.
Photos: Kollmorgen