www.industryemea.com
03
'22
Written on Modified on
GF Machining Solutions and GF Casting Solutions present their unique aerospace capabilities at Farnborough International Airshow 2022
At Farnborough International Airshow 2022 (18–22 July 2022), GF Machining Solutions and GF Casting Solutions will demonstrate their expertise in the aerospace industry in Hall 4, Stand 41150.
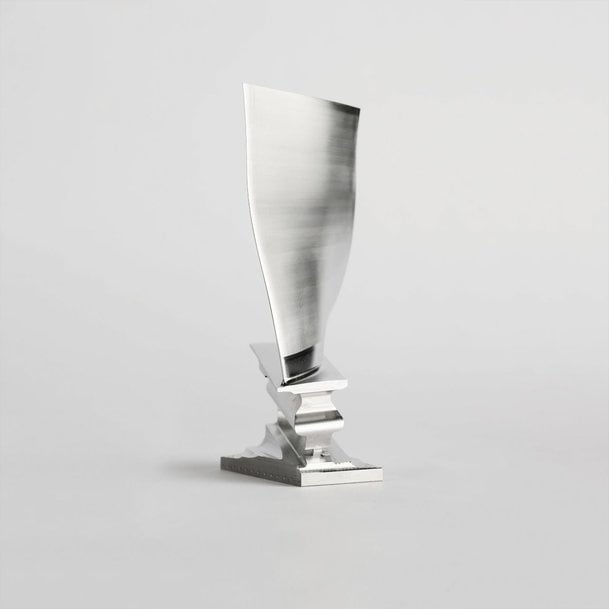
With more than 50 years of experience, GF Casting Solutions is one of the largest European solution providers in precision casting and additive manufacturing. In precision casting, GF Casting Solutions specializes in nickel- and cobalt-based super alloys as well as stainless steel. The company provides highly complex structural castings and solid hollow airfoils to the engines’ OEM around the world. In additive manufacturing, GF Casting Solutions has become a technological leader for large parts for aeronautics and space applications, following the Nadcap certification in 2019.
With additive manufacturing, production speed and flexibility can be taken to a new level. The highlight part from GF at the Farnborough International Airshow is a combustion chamber for rocket engines, which combines the expertise of both divisions of the GF Corporation, GF Casting Solutions and GF Machining Solutions. The extremely complex geometry of the part emphasizes the high design freedom of additive manufacturing, which is hardly possible with other manufacturing processes. Very complex shapes with hollow structures and thin walls (<1 mm) are combined in one part without compromising on functional integration. Thanks to the reduction of manufacturing steps AM moreover results in cost savings through the simplification of the supply chain. Nevertheless, the combustion chamber does not only convince with its complex design; with a printing space of 500x500x500mm, the dimensions of this one-piece solution are impressive.
GF Machining Solutions provides value-added manufacturing solutions for engine, aero-structure, equipment systems and avionic companies. These comprise dedicated solutions for blisks, discs, vanes and laser cooling hole drilling. Thanks to the premium expertise provided by Liechti and the Turbine Group, GF Machining Solutions develops manufacturing processes with top aerospace research centers and OEMs.
On its booth at Farnborough, GF presents four different applications that highlight the company's unique aerospace expertise in different technologies – wire-cutting and die-sinking EDM and milling.
The first application shown on the booth is a turbine fir-tree disk machined with wire-cutting EDM. GF Machining Solutions' dedicated wire-cutting EDM solution, the AgieCharmilles CUT 200 Dedicated, is already replacing the conventional broaching process in aerospace applications, bringing a cost-competitive manufacturing process to customers. A tilting and rotary axis combined with an integrated probe ensures accurate part repositioning for fir-tree slot machining. The EDM technology ensures a minimum heat-affected area, while providing maximum cutting speed. In addition, the eTracking software enables real time quality monitoring and data traceability to ensure a complete repeatable process that preserves surface integrity while providing a great machinability on the hardest materials.
Visitors of the booth will also have the opportunity to discover a turbine vane with seal slots manufactured with die-sinking EDM, for example with the machine FORM P 600. GF Machining Solutions helps seal slot producers to reduce costs with the best balance of machining speed and electrode wear, allowing better precision and minimal recast layers to ensure surface integrity.
Further application examples at the booth are of an Adaptive Milled compressor blisk/IBR and a turbine blade. Maintenance Repair and Overhaul (MRO) companies often request this machining methodology.
The TURBOSOFT Plus software ensures a fully automated adaptive milling process. Done in three basic steps, the process consists of a best fit, part probing, and finally machining. The Adaptive Milling module within TURBOSOFT Plus uses a BestFit calculation to fit the actual part to the CAD model. The BestFit improves the measurement quality while providing a faster and more powerful process, eliminating the need for measuring iterations on the machine. The calculated BestFit is the basis for the machine probe to extract the data for the adapted geometry from the physical part.
The software retrieves the probe data automatically from the NC control to re-calculate the new geometry. The profile geometry is adapted for seamless blending between the existing finished part and areas to be machined. New tool-paths based on the adapted geometry are automatically generated and delivered back to the control ready for machining, offering the user a 100% automated process with no manual intervention. In addition to Adaptive Milling, TURBOSOFT Plus offers the programmer a complete toolbox to work with for any process required: geometry optimization for perfect tool-paths, kinematic analysis of feed-rates and machine, dynamic analysis of workpiece and tool, and cutting forces for optimal cutting performance.
www.gfms.com