www.industryemea.com
02
'15
Written on Modified on
Staying in control in nuclear facilities
Josh Leuenberger of IMI Critical Engineering, a world-leading supplier of critical flow control solutions, examines the ever more stringent demands on safety-critical valves in the nuclear sector and how the sector’s leading players are responding with new solutions and technologies
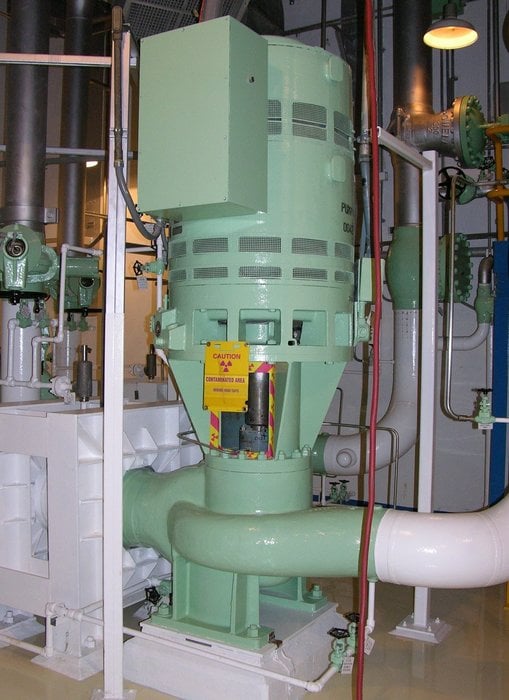
Irrespective of valve type, the specific valve design and material selection will be heavily influenced by whether or not the task is classified as safety-related. If so, the valve must adhere to the requirements of the US Nuclear Regulatory Commission 10CFR Part 50 Appendix B which is enforceable worldwide. Appendix B stipulates extensive quality assurance requirements to ensure all key design, engineering, and production processes are sufficiently controlled in order to guarantee the performance of safety-related equipment. However, beyond this, the system designer must provide the valve supplier with extensive detail on the application, including how and under what circumstances the valve should perform its safety function, so the supplier can design the valve accordingly.
A particular trend in nuclear reactor design, exemplified by systems such as the Westinghouse AP1000, is placing greater emphasis on the use of passive safety systems - such as water travelling through gravity rather than being pumped - which minimise the level of operator intervention required or the use of AC power, with valve designs having to be adapted to work in conjunction with these systems. Increasing needs for real-time plant information in the control room have also driven the development of digital valve positioners. These are smart control systems which, as well as interpreting signals and then activating valves as necessary, can record valve movements and even perform maintenance diagnostics.
Because of the vast diversity in nuclear plant designs and operating requirements, the selection of standard valve products from supplier catalogues is generally inadequate to meet the individualised specifications for safety-related applications, meaning bespoke valve designs are increasingly becoming the norm in this sector.
A poorly fitting or mis-specified valve can at best result in high levels of noise and vibration, impacting the service life and efficiency of other system components, while the catastrophic results of complete failure simply cannot be countenanced.
What this means is that, in both new and existing system applications, it makes sense for the individual responsible for writing the valve specification to engage with potential suppliers from the outset. A specification supplied with no flexibility can result in either an over-engineered component, entailing potentially unnecessary costs, or the omission of a key feature, with greater problems down the line. A specialist valve supplier will take the time to truly understand the application and what the customer is relying on the valve to do, and then design accordingly as well as undertaking extensive tests to prove the valve will be able to deliver in real operating conditions.
This is illustrated through a recent application involving a US nuclear plant with two boiling water reactors (BWRs) each with capacity of more than 1 GW per reactor. This plant was undergoing an extended power uprate for an estimated 12% increase in power, with a commensurate increase in system temperature which required greater cooling capability.
In particular, the plant needed to provide additional heat extraction under theoretical accident scenarios, one of which included reduced electrical load which meant fewer available cooling pumps – a potentially significant issue for the power uprate. This was solved by adding a cross-tie by which new piping and control valves allow the cross-connection of loops so that if one pump is unavailable, two heat exchangers can be fed by a single pump, increasing cooling capability. However, this presented a major challenge for the control valves which needed to be able to carefully balance the flow in this new mode of operation.
Firstly, the valve would be operating in a region of cavitating flow, meaning a multi-stage trim was needed for cavitation protection. Furthermore, images from underwater remote inspection cameras in place to monitor the reactors could potentially be affected by high fluid velocities, meaning more trim stages were needed to minimise exit velocities.
Most challenging, though, were the unique and highly precise requirements for flow capacity. At the full closed position, the valves were required to pass between 4,000 and 4,100 gpm to protect the pumps and prevent vibration that would occur below 4,000 gpm. As the valves are stroked off the seat, a specific Cv v. stroke profile was desired. The valves were to be remotely controlled via jog control, with an operator in the control room closing or opening the valves to balance flow. In two particular flow regions, the rate of change of flow needed to be 100 gpm per second of motor operation. A large window ported cage was also placed on top to provide 100% redundant single-stage flow capacity for worst-case emergency cooling capability.
The valve designed was extremely robust – able to operate before, during and after a seismic event. The valve trim had six distinct flow control zones to provide the unique flow profile, including the minimum flow element to guarantee the precise 4,000 gpm flow rate when closed. The characterised trim, called the disk stack, encompassed a multi-path, multi-stage design comprising a stack of individual metallic disks, each with several tortuous paths carved into it, and then brazed together to form a solid control element. Each disk was able to be designed with a different number of stages, meaning the slopes on the Cv curve could be characterised to match the individual application needs, providing variable flow resistance throughout the valve stroke.
Because accurate flow control was so critical for this application, IMI Critical Engineering developed a thorough test programme for verifying the actual hardware flow performance. The testing involved accurate measurements of the as-built Cv, with an additional step in the manufacturing process to fine tune the disk stacks based on initial Cv test data, and then final confirmation testing to prove out the valves prior to installation. Involvement of the supplier from the start of the project was key to addressing the specific application requirements and creating a bespoke, fit-for-purpose solution.
For further information visit www.imi-critical.com.