Possibly the most valuable milliseconds in the plastics industry
Because power outages can be expensive and time-consuming, the Swiss company NETSTAL started looking for a solution for PET manufacturing that would be able to handle such outages in a cost-effective manner while affording protection from damage. Together with KEBA, such a solution was developed.
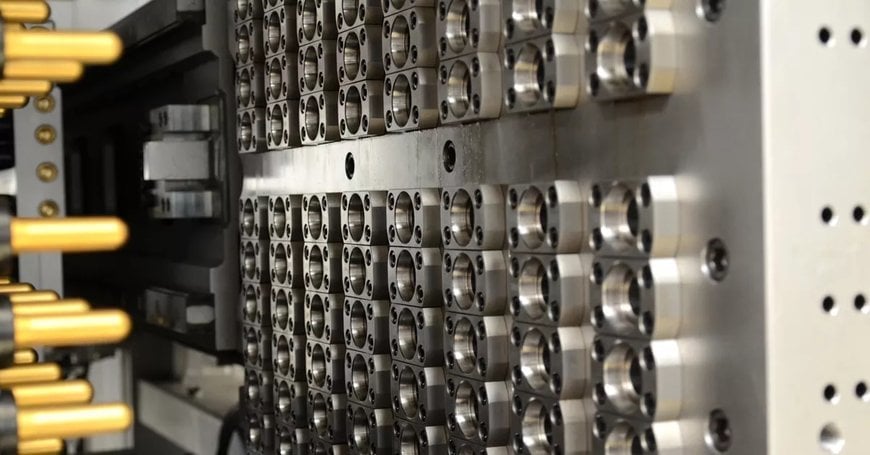
NETSTAL (Näfels, Switzerland) is a developer, manufacturer and seller of machines and complete systems for the injection molding industry, in particular medical engineering, thin-walled packaging as well as caps and PET preforms for the beverage sector.
The injection molding process is highly automated, and the machines are running 24/7. Some of the machines are located in regions where power outages can occur and where the reliability of the power grid is not necessarily a given. Power outages can be expensive and time-consuming, so NETSTAL started looking for a solution for PET manufacturing that would be able to handle such outages in a cost-effective manner while affording protection from damage.
NETSTAL PET-LINE 3000-4000
© Netstal
Trends in the PET industry
The history of the PET bottle (PET stands for “polyethylene terephthalate”) starts in the late 1960s. The international “career” of the PET bottle took off when Coca Cola introduced a 2-liter bottle in the US, which back then still came with a bottom shell made from a different material.
Today, about 1.5 trillion beverage containers in different sizes are produced annually, using a variety of materials—about one third of them (500 billion) are PET beverage containers. 80% of these are manufactured for water and carbonated sweetened beverages. This is exactly the market for which NETSTAL designed their new series launched in 2020: PET-LINE, a system tailored in particular to the processing of recycled PET (rPET) without limitations.
Due to the fact that the recycling concept for PET containers is very mature and widely used, the SUP (Single-Use Plastics Directive) did not question PET processing, unlike the approach used for other products such as cotton swabs or drinking straws. In addition, PET containers can be manufactured entirely from recycled PET (no new material needed)—the demand for recycled PET is extremely high and actually outstrips the supply.
PET beverage containers are on the rise—the PET market for beverage containers is growing by an average of about 4% each year. Food packaging also increasingly uses PET, for example in the manufacturing of clamshell containers for produce. Stefan Kleinfeld, Product Manager at NETSTAL: “During the coronavirus pandemic, many events and conferences around the world were canceled. People were unable to go on vacation. The result was a drastic collapse in the demand for PET beverage containers, especially in the small bottle segment (< 1 liter) that constitutes the lion's share of PET packaging (about 80%). Now, the market is recovering and manufacturers are investing in new machines; our order books are full.”
NETSTAL machines of the latest generation need 10-15% less energy.
Injection molding machines made by NETSTAL are a step ahead when it comes to energy consumption, speed and user friendliness. The machines of the latest generation need 10-15% less energy for comparable processes and under comparable conditions than the machines made by the competition. NETSTAL systems can be commissioned after just a few days of training—because the NETSTAL Smart Operation approach means that every machine can be controlled using just four buttons. In addition, the PET-LINE machines are currently the fastest on the market: with a lock-to-lock time of 1.9 seconds they achieve the fastest cycle time and highest output—in other words: maximum utilization.
Manuel Hausammann, Control Systems Engineer at NETSTAL (left); Stefan Kleinfeld, Product Manager at NETSTAL (right).
© KEBA
NETSTAL launched their very first PET system in 1981. The Swiss-based company sells their injection molding machines for the PET industry also in markets and regions where the reliability of the power grid is not necessarily a given and where fluctuations in the power supply can occur. This includes some very lucrative markets, such as countries in South America, Southeast Asia, etc., and this is a growing trend. Because they need to be able to continue production in a controlled manner even if a power outage occurs, NETSTAL started looking for a solution. Engineers at NETSTAL developed a theoretical model; the practical implementation was done by KEBA Industrial Automation GmbH.
Conflict: ever-higher power needs vs. unreliable power grids
The new PET-LINE comes with a high degree of electrification. Manuel Hausammann, Control Systems Engineer at NETSTAL: “We work with a nominal power of up to 240 kW—power and output in injection molding have been increasing more and more over the years. But there are still many regions where the power grids are unreliable. This combination is rather precarious. Power outages or disruptions happen time and time again, you just have to be prepared. As machine manufacturers, what we can do is to make sure that the rejects rate and the effort for restarting the machine are minimal.” If an injection molding machine stops abruptly, it means that the cycle cannot finish. The worst case is if the disruption occurs during the injection process while the cavity it not yet entirely filled with plastic, resulting in “short shots”, half-finished PET preforms. They need to be removed by hand, which can destroy the mold or damage the coating. One disrupted cycle can produce up to 144 short shots—with production losses of two to three hours due to the cleaning and restarting effort in such a case.
Controlled completion of the cycle
NETSTAL has developed a feature that bridges the time between the power outage and the end of the cycle. Hausammann: “Our goal was to finish the current cycle in a controlled manner without any external power supply—similar to shutting down the machine at the end of production— while keeping the mold and the plasticizing unit clean and making sure that the preforms made during the last cycle don't turn into rejects.”
The solution was given the name Cycle Guard and includes two main components: an ultra-fast electric energy storage unit for the brief time immediately following the power outage, and a hydraulic storage unit for larger amounts of energy for unmolding the plastic products and shutting down the machine. The idea behind Cycle Guard: if the supply from the power grid fails, the energy from the hydraulic storage unit will be used to continue the operation of the machine. In order to make this energy usable, the direction of the hydraulic pump must be reversed. This takes about 100 milliseconds. KEBA’s KeDrive D3 energy storage system is used to bridge this time and provide the missing energy.
The power outage is detected and the electric energy storage system responds within just one millisecond: for 10–20 ms, it replaces the grid power supply with a power supply of up to 300 kW. Simultaneously, all electric axes perform a quick stop, which does not interrupt the injection process. The braking energy produced by the motors is taken up by the energy storage unit, which then stabilizes the DC link of the drive system until the hydraulic pump starts working as a generator and provides energy. These initial 20 milliseconds are essential for the Cycle Guard feature.
The system continuously monitors the power supply and, in an emergency, it provides sufficient energy to shut down production in a controlled manner
This means that Cycle Guard includes two storage systems:
- An ultra-fast electric energy storage system for the reliable bridging of brief power outages or power fluctuations in the millisecond range. It consists of an energy storage unit with high-performance electrolytic capacitors and an energy manager that controls the power flow and monitors the energy storage unit. This system has been optimized for high power requirements with the shortest possible response time, small size and easy integration into the drive system. The use of storage capacitors ensures that the system can handle high load cycles at high frequency without problem.
- A slower hydraulic energy storage system consisting of a pump and a hydraulic storage unit. It stores about 100 times as much energy as the system described above. This system ensures that longer disruptions can be bridged. In case of longer power outages, the current cycle is completed in a safe and controlled manner. The injection of the preforms is completed, and they are then unmolded. After the grid power supply has been restored and after a quick system check, production can restart quickly.
The challenge is to match the configuration of these two storage systems so precisely that in any scenario, the power outage can be bridged and the cycle can be completed in a controlled manner. This fine-tuning is the job of aXos 9, the controller of the injection molding machine.
“Cycle Guard provides enormous benefits to manufacturers who use injection molding,” says Wolfgang Kapp, KEBA Sales Manager for Switzerland. “The system continuously monitors the power supply and, in an emergency, it provides sufficient energy to shut down production in a controlled manner. Cycle Guard does not use any batteries, which means it is very low-maintenance and low-cost in operation.” NETSTAL offers Cycle Guard as an optional feature—an investment that pays off very quickly, sometimes after less than ten power outages that have been bridged, depending on the product. Currently, about 40% of the PET machines shipped by NETSTAL include the optional feature.
Long-standing partnership and cooperation
NETSTAL and KEBA have been collaborating for over 14 years. NETSTAL appreciates in particular the close cooperation with the development team and the support provided by KEBA’s Swiss office. Hausammann: “Our collaboration is very easy and efficient. We have direct points of contact in development and in product management—there is a solution for almost every question and every requirement. Because of our excellent cooperation with KEBA during the introduction of a new generation of axis controllers and because of their comprehensive experience in the field of energy storage, we relied on KEBA again when it came to the development of an energy storage system. Thanks to NETSTAL’s and KEBA’s sophisticated simulation capabilities, we were able to develop the right product in a very short time span.”
Currently, NETSTAL and KEBA are planning to switch the ELION and ELIOS product lines to KEBA KeDrive D3 drive modules. “And we are already in talks about some future projects,” says Hausammann.
www.keba.com