www.industryemea.com
21
'23
Written on Modified on
FRAUNHOFER WORKS ON HIGHLY EFFICIENT AMMONIA-BASED SYSTEMS FOR CLIMATE-FRIENDLY ENERGY SUPPLY
Researchers at the Fraunhofer Institute for Microengineering and Microsystems IMM are developing ammonia-based systems for a mobile, decentralized energy supply in the infrastructure, transportation and industry sectors.
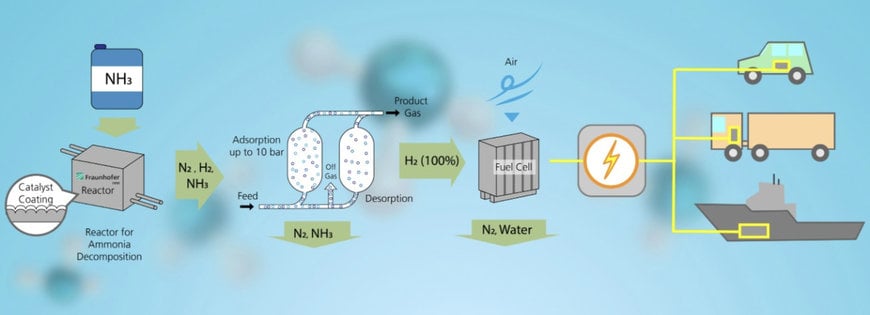
Implementing the energy transition is a huge challenge for all sectors of industry that use large amounts of fossil fuels, such as transport, logistics and the production industry. Currently, the energy requirements of these sectors are mainly met by fossil fuels, which need to be replaced with regenerative electricity or regenerative fuels.
Researchers at Fraunhofer IMM in Mainz are working on the mobile, decentralized provision and storage of electrical energy from sustainable sources. Dr. Gunther Kolb, head of the Energy division and deputy institute director at Fraunhofer IMM, explains: “An alternative to fossil fuels is power-to-X fuels, which are synthesized from electrolysis-based hydrogen. The most important power-to-X fuel is currently hydrogen itself. However, before hydrogen can be utilized as an energy source on a widespread basis, there are still some considerable hurdles that need to be overcome in terms of its transportation and storage. These include either high space requirements for its storage or other energetically unfavorable conditions. Ammonia (NH3) could become an alternative solution to allow the required hydrogen to be stored and transported with ease.”
Advantages of ammonia over hydrogen
To date, ammonia has primarily been known as a source material for agricultural fertilizers. However, it is also a high-quality energy carrier, particularly as a storage medium for hydrogen. “Because ammonia can be liquefied at a moderate temperature of -33 °C, its volumetric hydrogen content is significantly higher than that of compressed hydrogen at 700 bar. In comparison to hydrogen, liquefied ammonia makes it easier to transport large volumes to wherever it is needed. Because hydrogen produced from ammonia does not contain any carbon oxides or methane, it is also free from greenhouse gases,” explains Kolb.
Green cracked gas as a fuel gas in brick production
The conversion of hydrogen into ammonia is a viable option for using it as an energy source both on-site for industrial processes on a large scale as well as on a decentralized basis in the logistics sector. However, ammonia is not very suitable for generating energy through combustion as it is virtually incombustible in the air. “In a cracking reactor ammonia can be split into nitrogen and hydrogen when suitable catalysts are applied. A mixture of ammonia, hydrogen and nitrogen is suited for homogeneous combustion and can be used as an energy source, known as ‘Spaltgas’,” says Kolb. As part of the Spaltgas project, researchers at Fraunhofer IMM and their project partners are developing a combustion technology for this gas mixture that will be used in the brick firing process. In this way, ammonia from hydrogen produced via electrolysis can be used to make the entire brick manufacturing process chain carbon dioxide-free. The Spaltgas project is funded by the German Federal Ministry of Education and Research (BMBF) as part of the “KlimPro-Industrie” program.
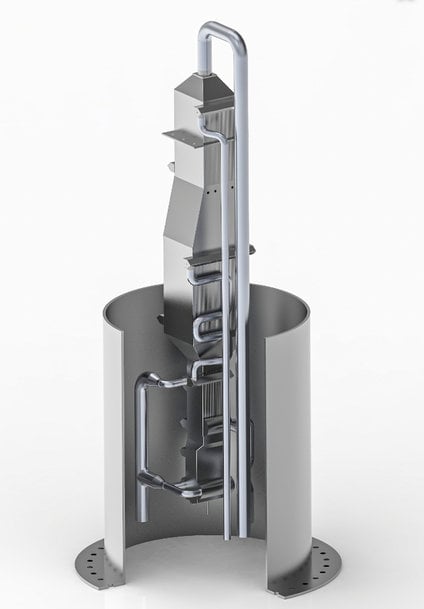
Ammonia as a hydrogen source for fuel cell drives
Ammonia can also be used for supplying hydrogen to land vehicles. It can be converted into hydrogen right at the filling station using decentralized plants. This eliminates the need to transport compressed and liquefied hydrogen — a costly and complex process. To this end, Fraunhofer IMM is developing a cracking reactor based on innovative catalyst technology and microstructured reactor technology. In this reactor, pure hydrogen is produced from ammonia through cracking and subsequent purification, which is then injected into PEM fuel cells. Hydrogen for use in fuel cell vehicles can therefore be produced sustainably from ammonia right at the filling station.
“By utilizing the off-gas of the pressure swing adsorption (PSA applied for hydrogen purification) as energy source for the cracking process, we are able to achieve an efficiency of 90 percent in comparison to 70 percent which are achieved when conventional technologies are applied. Additionally, our AMMONPAKTOR reactor is much more compact than conventional reactors, meaning that we have achieved a 90 percent size reduction. This is particularly important for mobile and space-constrained applications. Finally, our technology has a lower carbon footprint in comparison to electrically heated reactor concepts because we use the exhaust gases from the cracking process to generate the energy required and no other sources,” explains Kolb.
The AMMONPAKTOR reactor from Fraunhofer IMM, which was financed by the State of Rhineland-Palatinate using ERDF (European Regional Development Fund) funds, is also the most efficient reactor on an international scale. Even in its first generation, the cracking reactor achieved the second-highest specific hydrogen production rate ever published owing to the unique technology of Fraunhofer IMM. The second-generation cracking reactor, which is currently in the manufacturing process and has a throughput of 25 kg/hour of ammonia, produces 70 kilos of purified hydrogen per day. It will be exhibited at the Hannover Messe 2023.
In addition to supplying hydrogen to land vehicles, ammonia is also of interest for maritime propulsion systems because in this sector, it has not been possible to achieve the CO2 reduction goals using conventional fuels and there are numerous applications where compressed or liquefied hydrogen cannot be used as an alternative. In the same way as with Spaltgas reactors, partially cracked ammonia can be combusted in (ship) engines. Furthermore, as part of the ShipFC project, Fraunhofer IMM is collaborating with 13 European consortium partners to develop the world’s first ammonia-based fuel cell system for maritime applications.
www.fraunhofer.de