www.industryemea.com
23
'23
Written on Modified on
Network connectivity solved in Automated Container Ports
When BTG needed their IRM400 range of positioning measurement systems to send real-time data over different industrial networks, they found Anybus from HMS Networks. And that was the beginning of a beautiful friendship.
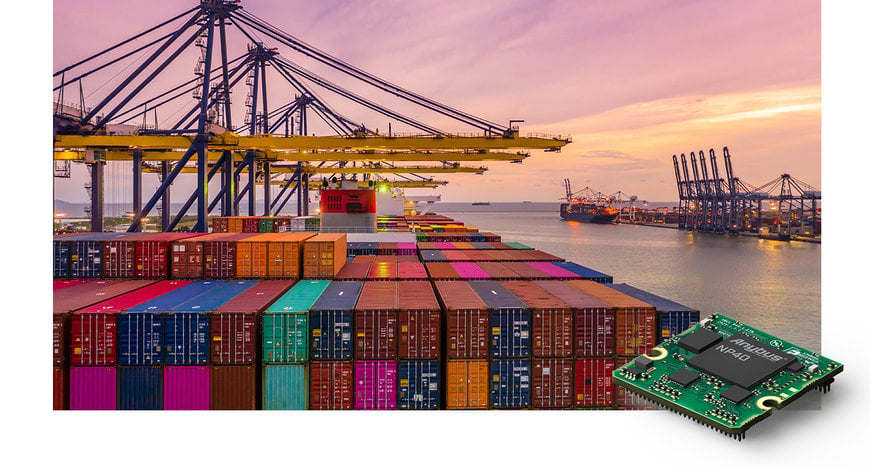
The drive to increase the efficiency of international shipping relies on high-performance cranes to transfer containerized cargo quickly and safely from ship to shore. BTG specializes in developing, producing, and installing positioning measurement systems for automated container ports. Much of the company's work is based on providing sensors to enable cranes to move cargo from ships to automated guided vehicles (AGVs). But the networking is complex and demanding. The cranes and AGVs often use different industrial networks, yet they need to transfer real-time data in harsh environments. That’s where Anybus steps in. Anybus takes care of the networking allowing BTG to focus on the position measurement systems, and together they help to increase the efficiency in automated container ports.
About BTG
BTG is a Dutch company specializing in position measurement systems used in all types of cranes and vehicles in automated container terminals. BTG has over 25 years of experience and has products in all the main automated container ports around the world.
One of BTG’s key products is the IRM400 range of measurement systems. It is designed to control sway, skew, and inclination and thereby provide accurate position control of the crane’s spreaders and their precious cargo.
Designed as a series of modular elements, the IRM can be configured for many different types and sizes of cranes. The system consists of an infrared transmitter and a high-resolution receiver unit. The transmitter is mounted on the spreader of the crane, and the receiver is mounted perpendicular above the transmitter. The system constantly measures the sway angle of the load in flight in all directions. It also measures the spreader skew angle and optionally the trim and list angle.
To achieve this level of dynamic control of multi-ton loads traveling in three dimensions at high speed, data must be collected from several sources in real-time and processed instantly so that the exact position and velocity are always known and can be adjusted.
BTG's IRM Spreader Measurement Sensor consists of a transmitter and a receiver. The Anybus CompactCom B40 was embedded into the receiver.
“We have a lot of experience and knowledge with position measurement systems in tough industrial environments, but we are not experts in industrial networks,” explains Daan Potters, chief operating officer at BTG. “That’s why we turned to Anybus.”
Networking Requirements
BTG required a networking technology that could be embedded into the IRM sensor, allowing the sensor to communicate over PROFIBUS, PROFINET, and CANopen networks. As BTG is a global company and different networks are dominant in different parts of the world, BTG also needed the possibility to easily cover more networks in the future. The networking solution also needed to be compatible with legacy equipment, tough enough to handle marine environments, and fast enough to process real-time data communication.
Time to meet the Anybus CompactCom!
Anybus CompactCom
Any Network
Anybus from HMS Networks is a product brand specializing in connecting industrial devices to any major industrial network. There’s a CompactCom product for the integration of any major Fieldbus or industrial Ethernet network, including PROFIBUS, PROFINET, and CANopen networks.
Embedded Design
The CompactCom is embedded into the relevant device, in this example the sensor’s receiver. The embedded design brings several benefits. It’s simple to install and therefore reduces the time to market for new products. It’s possible to reuse legacy equipment, enabling BTG to retrofit new electronic control systems to existing cranes. The CompactCom can be embedded in an IP67-rated enclosure, ensuring that the equipment can handle the harsh conditions found in marine environments.
Real-Time Communication
The Anybus CompactCom provides high-performance data exchange that can handle even the most demanding synchronized motion applications - up to 1448 bytes of process data in each direction.
“We chose the CompactCom B40, and we’re pleased we did”, concludes Daan Potters. “The CompactCom B40 solved all our networking needs, it’s compatible with all the required networks, and it provides real-time communication, which is essential in position measurement systems. Anybus also provided excellent support to help us to implement the CompactCom B40 as quickly as possible”.
Networking Requirements
BTG required a networking technology that could be embedded into the IRM sensor, allowing the sensor to communicate over PROFIBUS, PROFINET, and CANopen networks. As BTG is a global company and different networks are dominant in different parts of the world, BTG also needed the possibility to easily cover more networks in the future. The networking solution also needed to be compatible with legacy equipment, tough enough to handle marine environments, and fast enough to process real-time data communication.
Time to meet the Anybus CompactCom!
Anybus CompactCom
Any Network
Anybus from HMS Networks is a product brand specializing in connecting industrial devices to any major industrial network. There’s a CompactCom product for the integration of any major Fieldbus or industrial Ethernet network, including PROFIBUS, PROFINET, and CANopen networks.
Embedded Design
The CompactCom is embedded into the relevant device, in this example the sensor’s receiver. The embedded design brings several benefits. It’s simple to install and therefore reduces the time to market for new products. It’s possible to reuse legacy equipment, enabling BTG to retrofit new electronic control systems to existing cranes. The CompactCom can be embedded in an IP67-rated enclosure, ensuring that the equipment can handle the harsh conditions found in marine environments.
Real-Time Communication
The Anybus CompactCom provides high-performance data exchange that can handle even the most demanding synchronized motion applications - up to 1448 bytes of process data in each direction.
“We chose the CompactCom B40, and we’re pleased we did”, concludes Daan Potters. “The CompactCom B40 solved all our networking needs, it’s compatible with all the required networks, and it provides real-time communication, which is essential in position measurement systems. Anybus also provided excellent support to help us to implement the CompactCom B40 as quickly as possible”.
Learn more at www.anybus.com or www.btg-positioning-systems.com