www.industryemea.com
16
'23
Written on Modified on
System supplier in the automation process
Aerotech will attend the "LASER - World of PHOTONICS" in Munich from 27th-30th June to showcase photonics components, systems and applications.
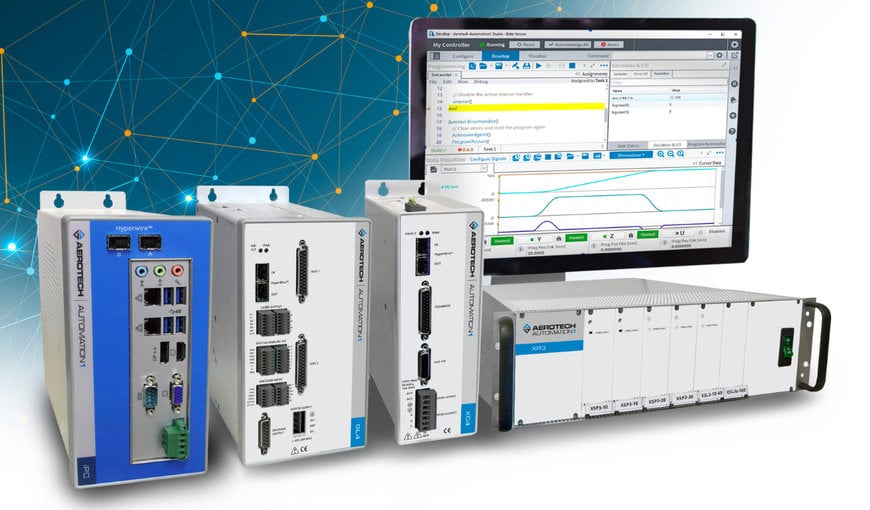
The specialist for innovative high performance motion control and positioning systems provides motion components, positioning stages to customised motion systems which offer users many benefits from ease of use to complete system documentation. In Hall A3 at Stand 245, it will be clearly demonstrated how individual components work seamlessly together to form a complete system, for example the AGV-SPO high- performance galvo scanner is mounted to an IGM (Integrated Granite Motion) linear positioning system. In addition, the motion control experts will showcase systems featuring the PRO-LM linear stages and the Fiber MAX Alignment positioning solution as well as the smallest (HEX150) and medium (HEX300) hexapods, all controlled by the Automation1 motion control platform.
For more than 50 years, Aerotech has supplied standard high performance motion components and solutions such as rotary and linear servo motors, servo drives, motion controls, positioning tables, galvo scanners and more. Custom designed motion subsystems can be designed and manufactured to customers needs including mounting on granite structures with machine bases and vibration isolation systems, as well as laser interferometer based measurement systems. The integrated systems are almost turnkey machines, developed together with customers to carry out their automated processes.
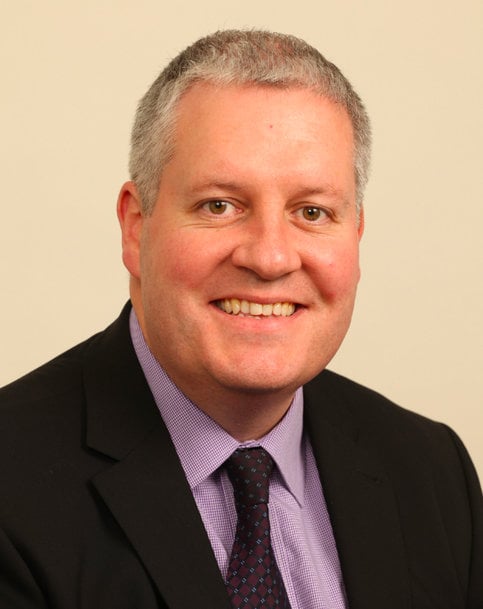
These include not only Aerotech precision motion control components, but also full automation integration for such things as parts handling, process instrumentation, safety features and custom software. Aerotech own manufactured galvo scanners are also integrated into an automation solution if required.
In the semiconductor and electronics sector in particular, many companies have neither the personnel nor the vertical range of manufacture to be able to develop mechanics and control systems in parallel. In addition, the solutions are becoming smarter and more complex, so that a single company can no longer master all the implementation steps. "Our know-how as a component and system supplier together with our mechatronics knowledge is becoming an increasingly important advantage to our customers. We offer a consultative approach to working by offering options and solutions for individual components, motion subsystems that can be seamlessly integrated into a machine or a complete automation solution," Simon Smith explains.
One control platform for all applications and systems
On the Aerotech exhibition stand 245 in hall A3, Automation1 with the new release 2.4 will be installed on all positioning solutions and systems. The motion control platform functions as a complete machine control system with all components.
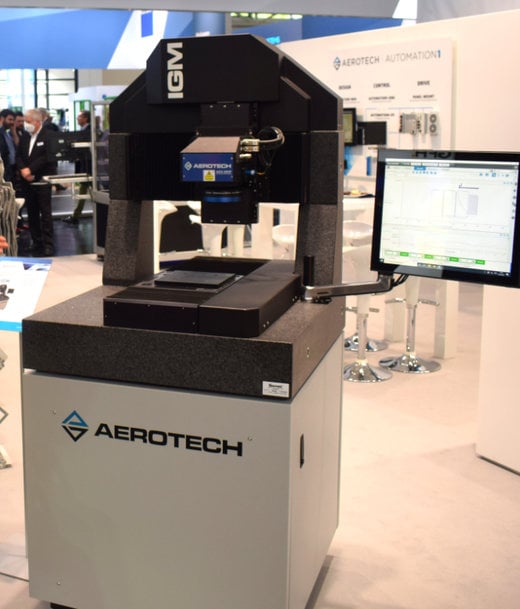
Aerotech demonstrates the strengths of this combination of flexible motion platform and high performance galvo scanner.
The machine setup, data visualisation and the Homing Setup helper‘ module have also been significantly improved. In addition, the Aerotech programmers have further simplified the uploading and downloading of MCD files and Automation1 now supports the Gantry-mode for XI4 and iXI4 Servo controllers with absolute encoder support. The device catalogue and machine setup for linear gantries now guides the user through the task of setting up gantry parameters for custom gantry configurations. 3- axis PSO with the GL4 module with IFOV (Infinite Field of View) and BiSS absolute encoders are now supported, which is important for the integration of galvo scanners and other lasers to synchronise moving servo axes with precise laser firing control, which ultimately delivers better part quality.
This also has the benefit of increased throughput, further improves positioning accuracy and eliminates stitching errors. In the machine apps, users can now drag and drop several machine app modules into the Module container, a separate area of a MachineApp to allow more configuration flexibility. To increase usability, notifications and animations can be executed directly in the MachineApp using indicators.
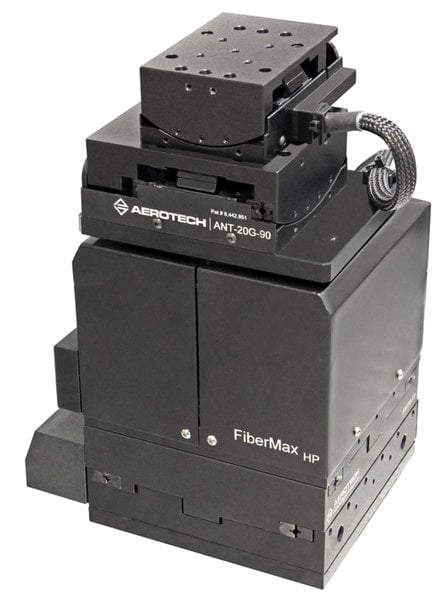
IGM brings more stiffness and dynamics to scanning
What such an integrated system can look like is illustrated by the combination of an IGM (Integrated Granite Motion system) positioning system with the AGV-20HP high- precision laser scan head with optics of wavelength 1030-1080 nm and a focal length of 255 mm. Aerotech is demonstrating new standards in high-precision laser technology. "Our IGM positioning stages are significantly more rigid due to the combination of the granite and the directly driven axes. Due to the incumbent design flexibility, we can offer even more individuality to customer requirements," explains Simon. Also, the higher rigidity of the linear table has a positive effect on the dynamics and positioning accuracy of the laser system.
As a result, the scanning speed and throughput can be significantly increased. Here, too, the motion control platform comes into its own: namely, if an AGV scanner is integrated to the linear axes of an IGM, this is done in Automation1 as a plug-and-play extension of XR3 high- performance control and GL4 Galvo control, the Galvo and Positioning stages are programmed using the same controller as just another axis.
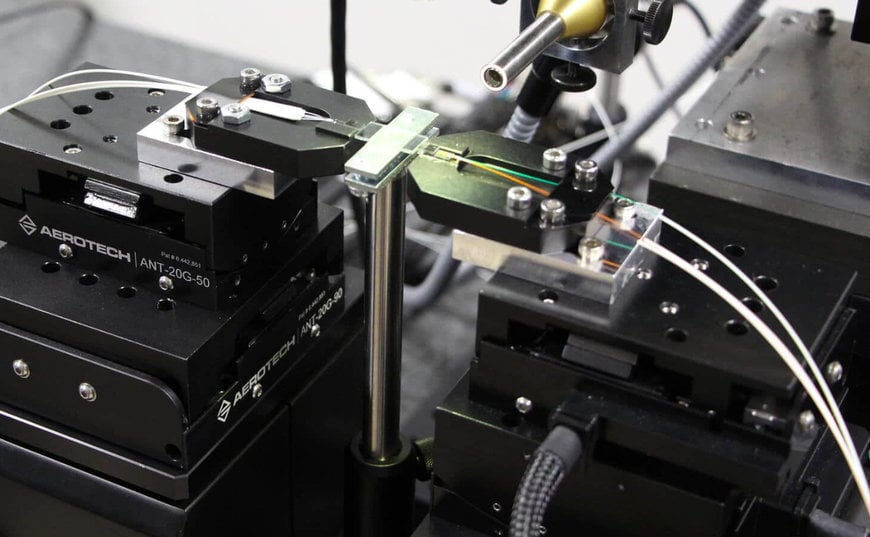
From control software to controller to hardware, Aerotech is a one-stop shop for complete optical alignment and adjustment solutions, such as the FiberMaxHP photonic alignment platform for optoelectronics, including Automation1 control software.
The advantage of this combination is that it simplifies programming, the Galvo scanner XY can be programmed in the normal methods and the controller then automatically synchronises the laser scanner with the XY stages to extend the operating window of the scanner as needed. Another advantage of the Automation1 controller is that the real time position errors in the XY stage can be compensated for with the more dynamic galvo scanner Overall the control platform offers ease of programming, more flexibility in control for Galvo scanner and XY stage integration, improves the dynamic performance, and reduces dynamic errors. For larger parts there is no stitching the part together in the classical sense. The so-called IFOV function (Infinite Field of View) comes into play here, so that linear or rotary servo axes are synchronised with the laser scanner to extend the galvos field of view.
Alignment platform for optoelectronics
Not all optical devices are the same: if the intention is to achieve competitive advantages, a close look at which peripherals optimally support your requirements is required for example positioning systems. At Stand 245 in Hall A3, the multi-axis FiberMaxHP, a high-precision optical alignment system, can be seen. It is based on the proven high-performance ANT nanopositioners and is used in large-volume production for aligning and testing optoelectronic devices and photonic components with submicrometre tolerances.
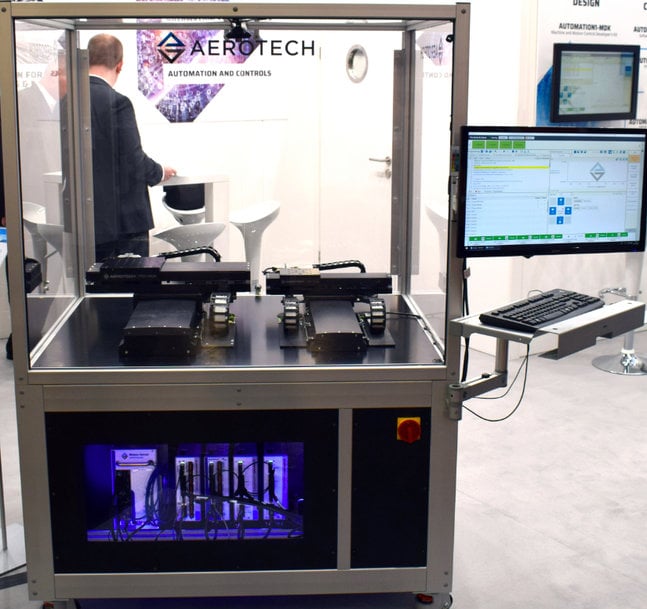
Robust and highly precise: Aerotech's PRO-LM series of high cycle rate linear positioning stages are available with either direct drive or linear motor, and are controlled by Automation1: Visible in the bottom window are the four XC4e PWM (pulse width modulation) drive controllers with HyperWire motion bus.
The precision mechanics are coupled with the Automation1 control platform to provide low-latency motion control and include optical alignment algorithms. This allows all automation processes to be programmed through a single control interface. According to Aerotech, the non-contact direct drive technology ensures extremely precise alignment with minimal incremental movement down to 2 nm at speeds up to 400 mm/s without compromising production throughput.
Aerotech Hexapods
The Hexapods from Aerotech provide true 6 degrees of freedom positioning with outstanding load-bearing capacity. The HEX150 and the larger, HEX300, can be positioned with Automation1, trade visitors can see for themselves at stand 245. Simon Smith knows the outstanding features of the hexapod: "With the comparison of the two hexapods, we want to demonstrate the significantly better minimal incremental motion on a small and large hexapod positioning system, together with larger travel range than similar sized competitor products, all in a compact yet rigid platform." In addition, the six degrees of freedom (DOF) enable precise translation in the X, Y and Z directions, as well as rotation around each of these axes. Which hexapod a user chooses for their positioning tasks depends on the load to be moved, travel range and the space available. "Our miniature hexapod is ideal for space- constrained applications with multiple DOFs that require fine positioning resolution."
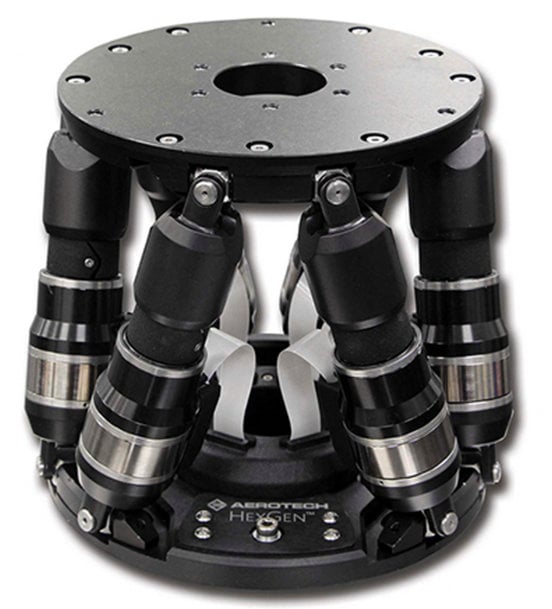
The HEX150 and HEX300 hexapods are in use at the Aerotech stand. The Automation1 control platform also integrates their simulation software "HexGen Hexapod" and thus enables easy programming and control of the hexapods.
Here, Aerotech particularly recommends applications such as alignment, assembly and interconnection of photonics components, optics inspection and alignment, optical wafer probing, aerospace and satellite sensor testing, and sample alignment in synchrotron and beamline applications. The wide range of motion as well as the simple control and programming with virtual pivot point adjustment simplify integration into complex applications and complete systems. Fast settling times ensure high throughput with repeatabilities of less than 2 μm at high payloads of up to 7.5 kg and a holding force of up to 100 N when de-energised. The small step sizes also allow for a wide range of applications for the HEX150.
The Automation1 control platform has its own "HexGen Hexapod" simulation software integrated. This enables easy programming and control of the Hexapods in any user- defined coordinate system. For collision considerations, the user can visualise and simulate the available working space. Preconfigured models from a stored library of standard designs are also available.
www.aerotech.com