www.industryemea.com
21
'15
Written on Modified on
Largest ever contract for IMI Critical Engineering
3,500 valves being supplied to Gorgon gas project
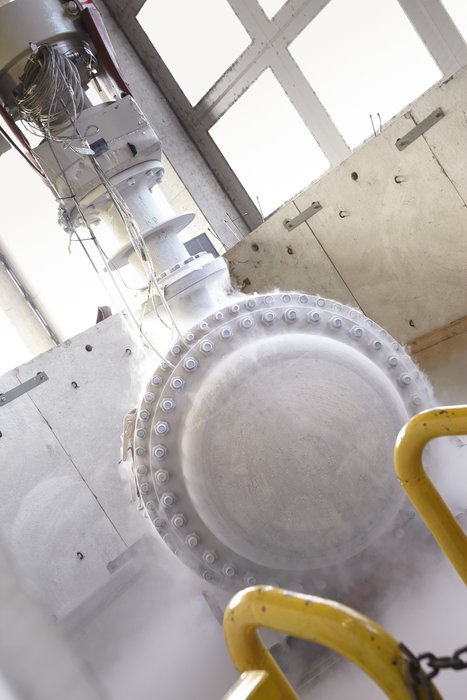
IMI Critical Engineering has won a contract worth around €70 million to supply some 3,600 of its acclaimed ball, control and triple eccentric butterfly valves to the dedicated liquefied natural gas (LNG) plant serving the Gorgon gas project, one of the world’s largest projects of its kind, located on Barrow Island off the coast of Western Australia.
With major shareholders including Chevron Corporation, ExxonMobil and Royal Dutch Shell, the LNG plant will commence operations later in 2015.
Top entry ball valves from IMI Truflo Rona were specified for their proven ability to cope with extremes of both hot and cold (down to cryogenics temperatures below -162ºC) and to provide 100 per cent shut-off. This level of reliability is key given that an unscheduled shutdown could cost upwards of US$10 million each day in lost revenue.
The control valves selected were specified to address applications that ranged from gas flare to antisurge and hot gas bypass. The largest of these valves were 36-inch inlet and outlet with plugs weighing more than one ton which were capable of moving full stroke in less than one second.
The triple eccentric butterfly valves from IMI Orton were chosen for their proven performance and Orton’s ability to design fully replaceable sealing elements. These will allow the valves to be serviced locally, instead of having to be shipped back to the manufacturer for repair, delivering significant savings on maintenance costs.
The Gorgon gas project is located in a Class A nature reserve, home to vulnerable species such as the flatback turtle and numerous other creatures not found on the Australian mainland. The need to protect the environment meant the product specifications were particularly stringent, not least in relation to extremely low allowable leakage levels and long-term sealing performance. As well as providing products to meet these, IMI Critical Engineering also applied a special coating combining optimal resistance to sea water and heat to the valves.
Enzo Stendardo of IMI Critical Engineering explained: “In an LNG processing plant, approximately two-thirds of all the valves are either ball valves or butterfly valves, making this an extremely significant project for us. Meanwhile, in a processing plant of this size, downtime cannot be countenanced because of the huge costs entailed, placing a real onus on valves to work without interruption between scheduled maintenance stops.
“The contract is therefore a strong endorsement of our ability to meet the needs of the global LNG sector from a product range which harnesses high-specification materials and innovative design to deliver outstanding performance in the most demanding operating conditions.”
For further information visit www.imi-critical.com.