www.industryemea.com
13
'24
Written on Modified on
Reduce energy costs and improve sustainability through feed mill automation
Here, Gary Kernaghan, automation manager at systems integrator Technidrive, explores how automation can improve energy consumption management in feed mill production.
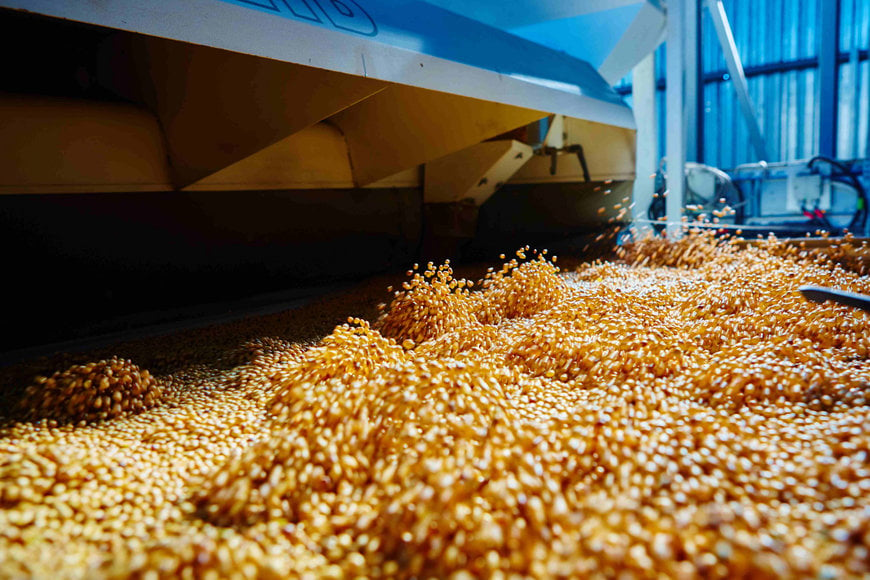
Optimising milling systems by reducing energy consumption can improve operations in more ways than one. Automating a feed mill could be the key to unlocking energy efficiency and substantial cost savings, this is done by controlling the speed of the machine that feeds the product into the mill.
From pulp and paper to flour and grain, the wider milling industry has seen a shift in priorities. Instead of focussing solely on product production, there is now an increasing emphasis on optimising operations, minimising environmental impact, and reducing costs. This shift reflects the industry’s effort to navigate the nationwide upswing in energy prices and address the ongoing climate crisis.
As an example, take ADM, one of the world’s largest nutrition companies Its Strive 35 initiative aims to reduce absolute greenhouse gas emissions by 25 per cent, energy intensity by 15 per cent, water intensity by 10 per cent, and attain a 90 per cent landfill diversion rate, all by 2035.
Energy use plays a significant role in determining the costs related to producing feed for poultry and livestock. In fact, a typical feed mill producing 250,000 tonnes of feed per year can expect to spend as much as £750,000 a year on energy, according to Finning.
There are numerous strategies that aim to enhance efficiency, including investing in newer energy-efficient equipment such as motors, drives and compressors, and improving maintenance practices. However, turning to automation stands out as one of the most effective approaches.
Automating a feed plant allows manufacturers to ensure a minimal margin of error throughout the entire processing and packaging procedure. In order to process a range of different animal feed products, mill feeding systems require regular speed adjustment. Feeding systems are responsible for transporting material into the mill itself, where grains, seeds and other raw materials are ground into smaller particles or powders.
Mills that introduce automation systems, capable of adjusting feeding speed to the desired level, not only achieve a reduction in energy usage but also contribute to enhanced sustainability practices.
In contrast, a feeding system reliant on manual labour, can struggle to strike the right balance when adjusting feeder speed. This challenge often leads to prolonged shifts and wasted energy if the speed is too slow and compromised feed quality if the feed rate is excessively fast. Implementing a consistently efficient feeding process, powered by automation enables feed manufacturers to improve throughput during each shift and minimise overall running time.
Furthermore, a system operating consistently at its peak performance level, not only conserves time but also allows facilities managers to divert their attention to other crucial aspects of the manufacturing process. This includes compliance with safety regulations and coordination with suppliers and distributors.
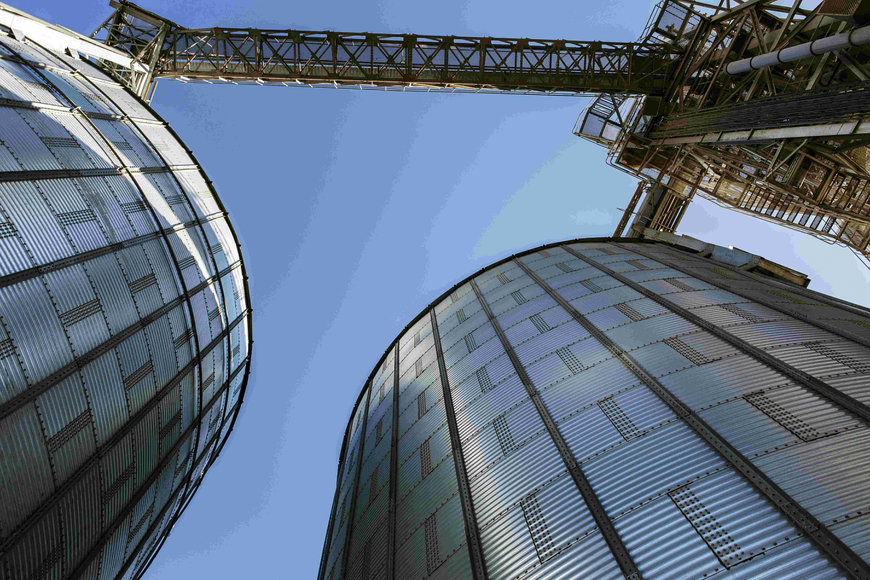
Saving energy means reducing costs
Achieving energy-efficient milling directly translates into substantial cost savings for businesses. By curbing energy consumption, manufacturers can effectively trim operational expenses, therefore enhancing their overall financial performance.
The adaptability offered by automated speed control, optimises energy usage without compromising operational efficiency. This results in improved product quality through optimal grinding, and a reduction in overall plant running hours, further contributing to sustainable and cost-effective milling practices.
Technical aspects of variable speed milling
Bespoke solutions can leverage control algorithms and precision engineering to seamlessly modulate feed mill speeds. This approach ensures a fine balance between energy savings and the preservation of feed quality and consistency. Sophisticated motor control technologies play a crucial role in achieving these outcomes.
Beyond immediate cost savings, the impact of energy-efficient milling extends to the maintenance requirements and longevity of milling equipment. Notably, these bespoke systems reduce wear and tear and offer more controlled operating conditions, ultimately contributing to extended equipment life cycles and minimised maintenance needs.
In response to industry needs, Technidrive has developed an innovative automation solution designed to optimise feed mill operations. At its core is the implementation of advanced variable speed drive (VSD) technology, which precisely controls motor speed to streamline the milling feed process.
This solution was integrated at Kerry Agribusiness, resulting in a 29 per cent increase in throughput from the mill since the installation. The automation system replaced traditional manual controls with a software interface, enabling seamless remote monitoring and control. Eliminating the need for trial-and-error adjustments, operators gain real-time insights into milling operations.
Enhanced by a smart algorithm, the system dynamically adjusts the feeder's speed, striking a balance between energy savings and operational efficiency. The benefits of this cutting-edge solution are twofold.
Firstly, it minimises unnecessary energy consumption by ensuring precise calibration of the milling process, reducing overall electricity usage and contributing to extended equipment lifespan. Secondly, the automation system significantly improves milling efficiency, resulting in increased throughput.
Streamlined operations, combined with remote monitoring capabilities, not only minimise downtime but also facilitate prompt adjustments, ultimately translating into a more sustainable and cost-effective approach for the milling industry.
www.technidrive.com