www.industryemea.com
06
'16
Written on Modified on
Der Antrieb is in control
Smart drive systems increase manufacturing efficiency
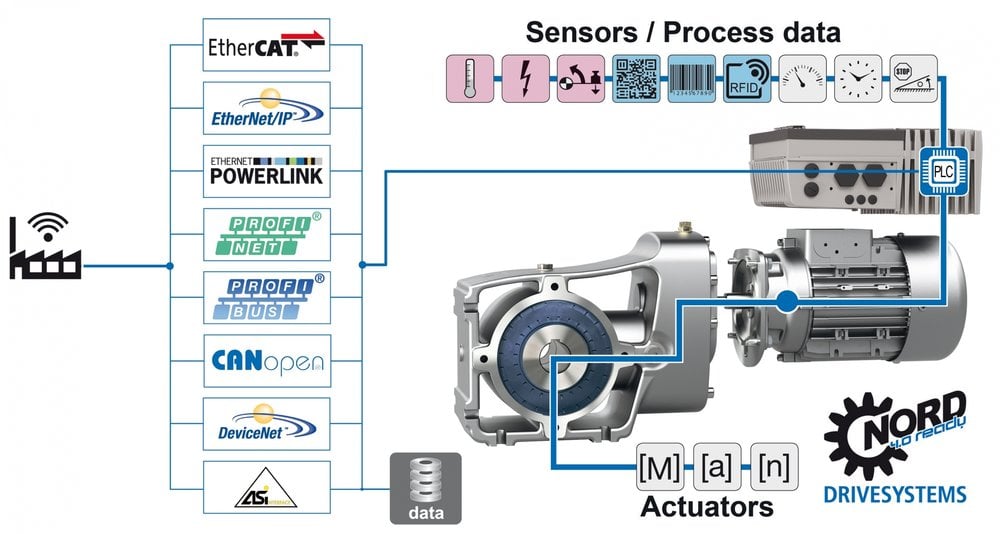
Intelligent plant concepts are taking hold in all kinds of industrial operations. Comprehensive drive solutions provider NORD DRIVESYSTEMS offers “NORD 4.0 ready” components designed to facilitate and further this development.
Modern process plants require automation technology with advanced functional intelligence. Components must be able to provide key data from the field via various different networks and make a wealth of information including data from connected sensors and actuators available. In addition, smart field devices are increasingly expected to actively monitor events in the field and react autonomously. Drive manufacturer NORD DRIVESYSTEMS addresses these demands with a modular range of geared motors, drive electronics, and software functions. The differentiated range of distributed drives facilitates the configuration of highly economical solutions tailored to a particular application’s characteristics. Featuring an on-board PLC, NORD inverters can implement logical sequence control. They offer full connectivity for communication with other nodes on the network, including flexible access from a device with a standard Ethernet interface by means of Ethernet tunneling.
Know when to act
The first and foremost prerequisite of intelligent process control – wherever the controller is installed and however it is connected (by cable or wireless, via Industrial Ethernet or Internet) – is accurate data from the field level. The components themselves must communicate their operating status in order to allow conclusions about what is happening in networked system segments. There must be appropriate interfaces for the vertical integration of sensors and actuators into control, management, and production planning systems, and high-quality data transmission must be ensured. NORD frequency inverters therefore monitor and transmit drive data and also collect information from externally connected digital and analog sensors and actuators. Moreover, they enable condition monitoring and predictive maintenance using software capabilities for efficient diagnostics. The inverters can, for example, calculate the state of the gear lubricant and indicate when an oil change is required. They can also autonomously monitor wear on the braking surface as well as the load situation for the entire drive train. Based on such data, operators can implement predictive maintenance, thus augmenting plant availability.
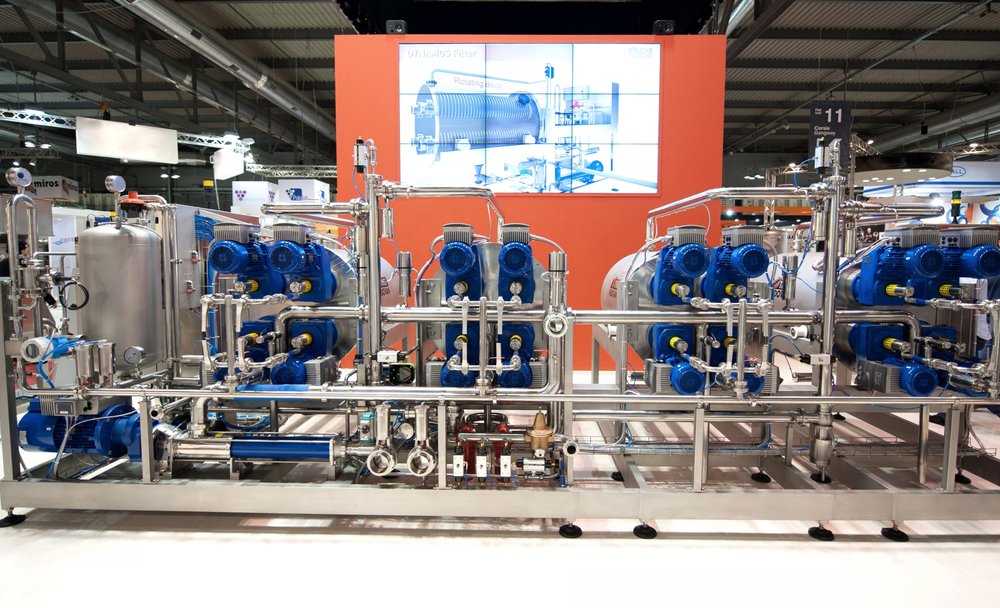
Illustration 2: Up to 24 drives from NORD DRIVESYSTEMS per beverage filtration unit – distributed drive electronics reduce the necessary cabling and all but eliminate EMC issues
Autonomous removal of obstacles
The frequency inverters can utilize their versatile sensor interfaces to do much more than just pass on data to a central controller. These drives also react to changing process conditions according to their parameterization. They can implement closed loops based on their integrated PI controller functionality. In metering applications, for example, NORD drives detect the fill level and control replenishment. In all kinds of process applications, networked drives ensure that glitches that occur will often not result in downtime with considerable costs. By monitoring the load situation, the on-board PLC of the inverter is able to detect blockages of pumps, screw conveyors, or agitators. If proper drive parameters are set for glitch scenarios, a NORD drive will, for instance, first attempt to remove a mechanical obstacle by reversing direction and by pulse operation. If this effectively resolves the blockage, the drive will then resume normal operation. If the problem persists, the inverter can submit an error signal to the control level and can possibly initiate a fallback procedure, e.g. have other networked drive units unlock a bypass. The PLC capabilities of these inverters significantly contribute to higher plant availability and lower service costs.
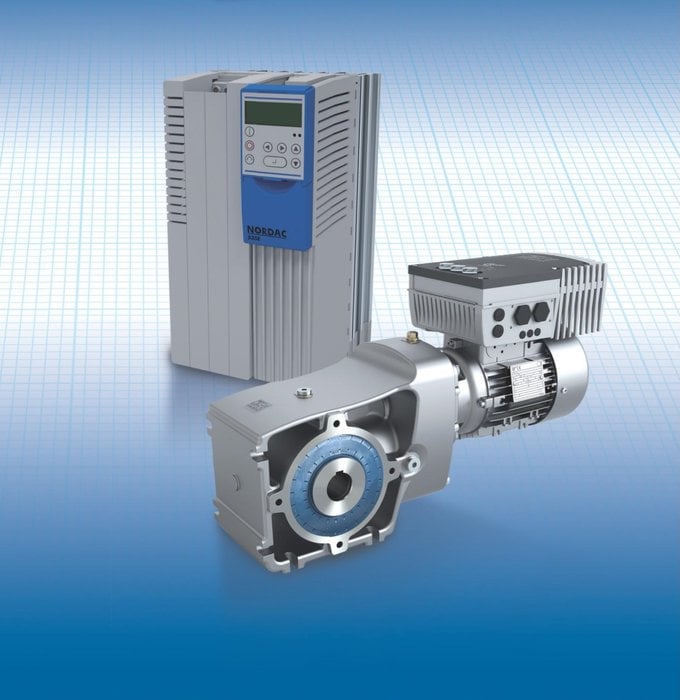
Application development made easy
NORD also facilitates application development, providing the user-friendly, free-of-charge NORD CON programming and parameterization software that supports drive-related functions according to IEC 61131-3, as well as the PLCopen motion control library. Customer-specific routines can be freely programmed in the text-based programming languages “Structured Text” or “Instruction List”. All drive-related functions can be implemented directly in the inverter PLC. Users therefore do not need to spend time and money on the development, verification, and validation of an application-specific firmware. Moreover, NORD CON enables remote access via Ethernet tunneling – for instance, from a notebook with a standard Ethernet interface –, which gives users very flexible remote diagnostics and maintenance options. NORD frequency inverters can also manage safety applications, notably for implementing Safe Stop 1 (SS1) and Safe Torque Off (STO). A library with these safety-related functions is available for free from the NORD website. It enables an evaluation of machine applications according to DIN EN ISO 13849 with the safety integrity software tool SISTEMA.
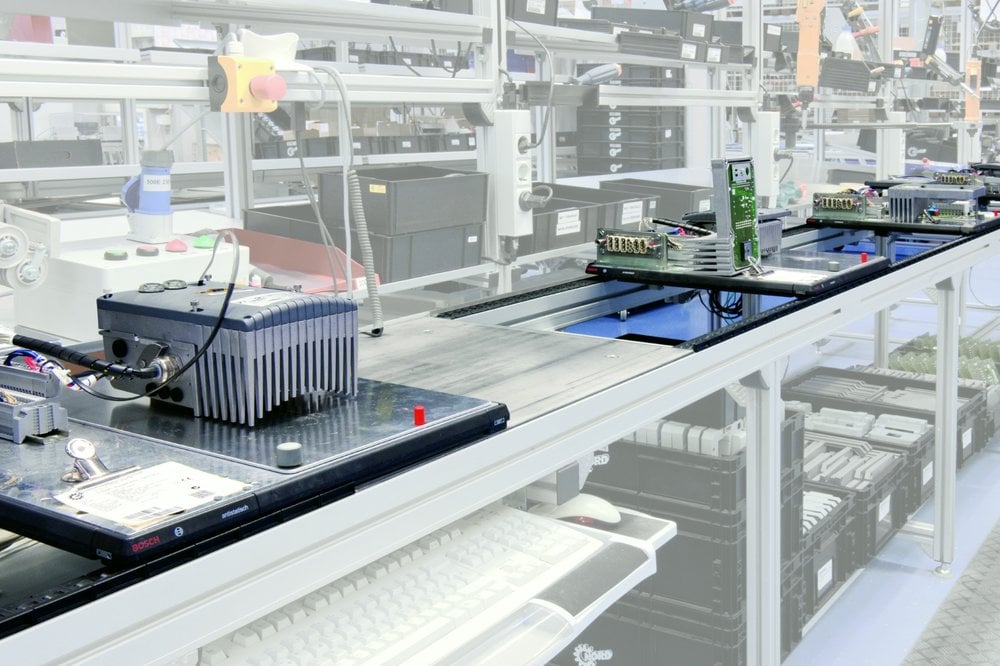
State-of-the-art decentralized automation
Distributed drive solutions for simple, low-cost, and efficient machine and system designs are still the fastest-growing product segment for NORD. Drive systems based on the SK 200E line of frequency inverters are most in demand. They offer the same extensive functional range (including positioning, on-board PLC, safety-related drive functions) as their SK 500E counterparts for control cabinet installation. The robust distributed units from NORD cover an exceptionally large performance range. This allows for versatile installations with decentralized process control of pumps, compressors, screw conveyors, etc., with motor outputs up to 22 kW. Moreover, NORD inverters feature high-performance microcontrollers and can control synchronous as well as induction motors. The company configures mechatronic drive systems based on three-phase induction motors and permanent magnet synchronous motors with efficiency ratings up to IE4 (Super Premium Efficiency), all of which are manufactured in-house. The IEC standard motors enable simple, easy-to-service, and economical drive concepts. In addition, drive systems from NORD combining a motor and an electronics unit achieve the highest level of system efficiency – an IES2 rating according to the current EN 50598-2 European Ecodesign standard.