www.industryemea.com
07
'16
Written on Modified on
Magnetic field instead of feed rollers tecodrive is developing a revolutionary process for material feed applications with the help of servo drives from Kollmorgen
tecodrive GmbH from Garbsen has named its invention "fleXfeed" – and is breaking revolutionary new ground in material feed applications used for metal processing. Thanks to an ingenious magnetic field, "fleXfeed" works on a completely contact-free basis and is much faster than conventional feed rollers. The young company is basing its new solution on the principle of linear direct drive technology. As a partner for the delivery of drive control solutions, Kollmorgen was closely involved at the development stage. The S700 servo drive play a key role in the contact-free feed process.
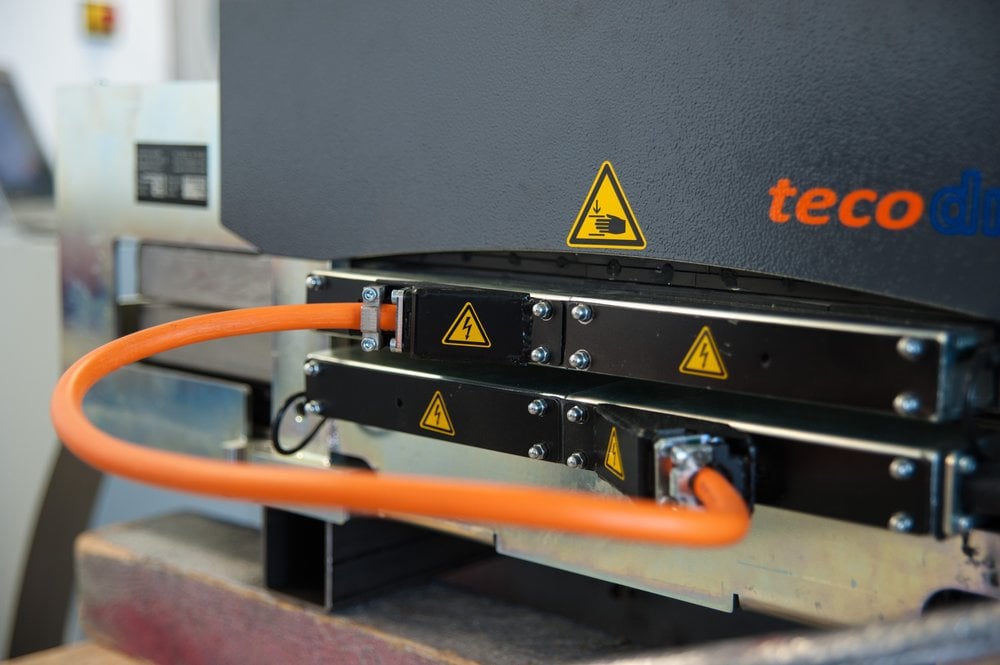
No torsion or slipping
Anyone keen to reap the full benefits of the electromagnetic solution would do well to take a cursory look at how a feed roller works. This positions a strip of metal (rolled out from a coil) and feeds it at a given rate into a machine to be processed – for example, a system for deep drawing or punching. The two rollers must close in with each cycle, building up pressure on the workpiece and transporting it as they jam against it, before finally opening again (or releasing). "The higher the speed, the higher the pressure needs to be so the material does not slip," explains Marthiens. And this is precisely where feed rollers are at a disadvantage compared with the electromagnetic approach. The pressing force exerted on the material cannot simply be increased ad infinitum, or the metal will become deformed. There is also an increased risk that finely worked surfaces may become damaged. TriluX found that this effect was creating torsion – albeit barely visible – in the aluminum fins. Following final assembly, however, this regularly caused noticeable distortion in the light generated.
These days, the lighting manufacturer is using the "fleXfeed" from tecodrive – with astonishing results. The company has doubled its production rate and is now finally able to exploit the full potential of its sheet metal processing machines. "Our mission at the start of the project was to reach 400 strokes a minute – and we achieved this really easily," recalls Hans-Jörg Lindner, who is also a managing partner at tecodrive. "Generally speaking, we are managing to ramp up existing processes by a factor of two," adds Dr. Marthiens.
Where does this performance come from? As with linear direct drive technology, the contact-free feed process also adopts the principle of magnetic attraction and repulsion. This explains why the device, at just short of 1 m long, contains two opposing stators. These generate a traveling magnetic wave in the metal strip lying between them, a wave which facilitates the feed action via the Lorentz force generated. The operating principle in the "fleXfeed" could be compared with an asynchronous linear drive, with the metal sheet assuming the role of the squirrel-cage rotor. This detail presents certain challenges from a control technology perspective, however, and the patented process is ultimately concerned with addressing these.
Developing a new control process
This is where tecodrive relies on the great performance of Kollmorgen's S700 servo drives – particularly in terms of speed and programmability. Maximum freedom is what Dr. Olaf Marthiens needed to implement a new type of control in the servo inverters, an alternative to field-oriented vector control (FOC). "I had to write a program that allows me to change both the phase angle of the current and the amplitude." Using FOC would not really work for this specific application, because the constantly changing magnetic behavior of the material being transported would make the control circuit unstable. FOC would react with great sensitivity to the so-called rotor constant – the ratio between inductance and electric resistance in the sheet metal being conveyed. In a standard asynchronous motor, the rotor is mechanically unchanged and the rotor constant is only dependent on the temperature. Even this can be enough to make an applicator white hot when using asynchronous motors in highly dynamic control applications.
By contrast, the "fleXfeed" unit is designed to position and feed the widest possible range of metal materials into a processing machine with real accuracy in highly dynamic applications. Here too, the different thicknesses and widths and the invisible changes in the structure of the material result in ever-changing resistance and inductance levels – and therefore changes in rotor constants.
Together with Kollmorgen, tecodrive has solved this problem by only having one current and position controller in this particular application. Field-oriented control no longer applies, because the S772 servo inverter is programmed to specify and fix the field. "Our special expertise comes into play here," enthuses Marthiens. In order to determine the position of the sheet metal,tecodrive uses measuring wheels developed in-house for feedback purposes. What's remarkable is the speed of the control circuit, because tecodrive calculates the next set point directly from the actual position of the sheet metal within the magnetic field – and not via a control system or the field bus. "We need there to be no delay whatsoever in order to ensure that positioning is accurate to 10 µm – even at a cycle rate of 4,000 strokes a minute. The peak values can be attributed to the high computing power of the S700 drives and the generally highly streamlined and uncomplicated programming. Marthiens still looks back fondly at the close collaboration with the Kollmorgen sales team, who were quick to recognize the significance of this invention and also arranged direct contact with Georg Jaskowski, the software developer for the S700 series at Kollmorgen.
Unimagined productivity for the feed process
tecodrive and Kollmorgen have managed to devise a feed method that achieves the kinds of figures that would never be possible with rollers – for one thing, because masses simply cannot be compensated for as quickly as this. By contrast, there is no mass with this feed method, because it only involves a magnetic field. As a result, the process is reduced – in simple terms – to just switching the current on and off, with mass playing no part. This ingenious principle delivers yet more benefits in practice. Switching is silent and does not involve any mechanical stresses. This aspect significantly extends the service life of production equipment in a high-performance environment, as the feed unit is not being exposed to mechanical wear and tear.
Lower energy consumption
Another aspect is currently grabbing the attention of companies active in and around the automotive sector too: the new development only needs a fraction of the energy used by a feed roller. "Although we need to use a Kollmorgen 35 kW servo drive to achieve the necessary magnetizing current, the effective power alone amounts to a mere 700 watts," explains Dr. Olaf Marthiens. For Hans-Jörg Lindner, who manages the business with him, these are further benefits that make the case for abandoning the old methods of feeding materials. "At TriluX, we managed to combine two systems into one. We did this without compromising productivity, and still managed to save lots of space and greatly reduce tool costs." VW at Hanover Stöcken has enjoyed similar positive experiences.
Image 1
Schematic representation: The contact-free feed process adopts the principle of magnetic attraction and repulsion. Two stators make this possible by generating a traveling magnetic wave in the metal strip. Image: tecodrive
Image 2+3
The two stators generate a powerful magnetic field in the feed unit, which is controlled in turn by a Kollmorgen servo drive.
Image 4
Programming the Kollmorgen S700 servo drive for this demanding task is relatively easy.
Image 5
Not even 2 m long: "fleXfeed" speeds up the feeding of products in metal processing applications.
Image 6
The resourceful trio from tecodrive in Hanover: Dr. Olaf Marthiens, Hans-Jörg Lindner, and Hannes Mahler (front right).
Image 7
The fleXcontrol operator interface for the feed unit. Punching is made easier by inching the strip forwards and backwards within a restricted section of feed length.
Image 8
To provide feedback regarding the actual position, tecodrive uses two high-precision and very light measuring wheels, which can also detect any potential slippage.
Image 9
The "fleXfeed" is already being used with great success by a lighting manufacturer and a vehicle manufacturer.