The hl 1 high-performance plant for cutting to size offers flexible solutions for batch sizes of 1
Wherever high shift outputs are demanded in batch sizes of 1, the hl 1 cut-to-size plant from IMA Schelling is the perfect solution – delivering unbeatable flexibility together with unbeatable performance. Its modular design allows versatile adaptation to individual requirements, supports different installation variants and numerous performance classes.
www.imaschelling.com
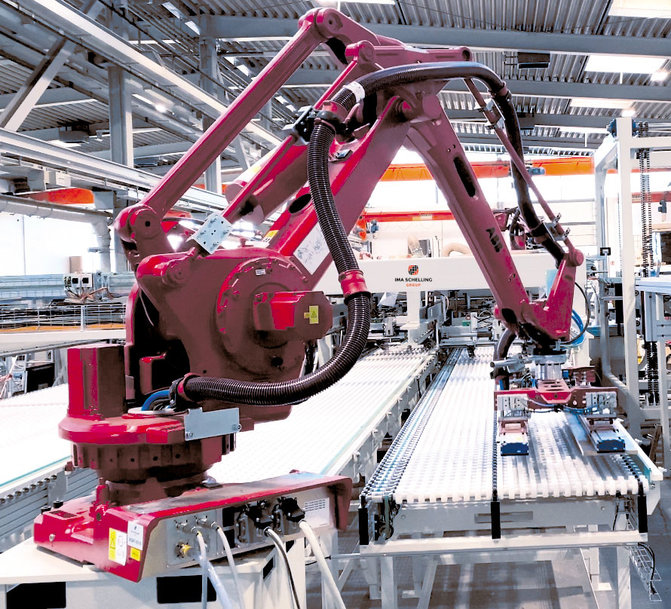
With the hl 1 high-performance plant for cutting to size, IMA Schelling is providing its customers with a customisable concept for wood processing that can be precisely adapted to the respective requirements. The basic version of the hl 1-System generates an output of up to 20 parts/min with a rip-cut saw for strip production and a cross-cut saw for cutting four strips to size at the same time. Alternatively, the hl 1-Concept, in which only the cross-cut saw is used, can produce both strips and components on a single saw line, achieving an output of up to 8 parts/min.
Flexibility for every requirement
"We've designed the hl 1 cut-to-size plant as a modular solution, providing the user with a high degree of flexibility," explains David Schelling, Cut-to-size Product Manager at IMA Schelling. "Depending on the production strategy and available setup area, we can respond to any of our customer's requirements." To do so, the area downstream of the rip-cut saw can be equipped with a buffer track or a strip buffer. It also does not matter whether the strips are transferred to the cross-cut saw with a repositioning gantry or a robot.
The cross-cut saw can be designed with three or four lanes in different widths depending on the component range. The arrangement of the saw lines relative to each other is also flexible: in a line, at an angle, in a horseshoe or even on two levels one above the other. Workpieces that require re-cuts are guided back to the cross-cut saw vertically, saving space. For projects achieving an output of up to 3000 parts per shift, strip and component production can also be performed on one saw line.
The hl 1 high-performance plant for cutting to size from IMA Schelling – an impressive concept for shifts where up to 6000 components are processed in batch sizes of 1.
Tailor-made solution for a kitchen manufacturer
The performance of the hl 1 recently impressed a well-known kitchen manufacturer, for whom the experts at IMA Schelling developed and implemented a customised solution. This consists of an hl 1-Concept with linkable lanes, which enables highly flexible production processes. For example, up to 6,000 components can be produced on a four-lane saw with strands as the starting material or up to 3000 components on a three-lane saw with half formats as the starting material.
Increased speed, proven technology
Unlike solutions previously available on the market, the hl 1 does not have multiple machining units, but instead multiple feeders and one saw blade. Strips are fed to the cross-cut saw independently of one another in up to four lanes and split jointly. In this way, four components can be produced every twelve seconds with just one unit. This not only reduces energy and tool costs, but also makes servicing significantly easier.
IMA Schelling originally developed the hl 1 in response to feedback from the field. "At the time, we realised that there was a lack of suitable concepts in this performance class," explains David Schelling, describing the impetus for IMA Schelling's development team. "In the past, many customers – if they had the space – made do with several plants with lower performance classes. But we thought there had to be a better way. The hl 1 high-performance plant for cutting to size now delivers maximum productivity for automated production."
www.imaschelling.com