www.industryemea.com
07
'16
Written on Modified on
Single-cable solutions – new possibilities opened up by high-quality components and an open protocol
Single-cable solutions are increasingly gaining traction in the field of servo drive technology. In addition to the growing number of drive manufacturers offering single-cable solutions, this trend is fuelled by the increasing number of manufacturers of rotary encoders that allow the implementation of such solutions in the first place. They differ not only in the protocol used, but also in technical details such as resolution and stability. Helukabel GmbH and Hengstler GmbH are two well-established companies that tackle this topic from different vantages. However, they are united in their common mission of providing customers with high-quality components that are innovative, effective and safe and that harness the tremendous potential offered by the single-cable technology.
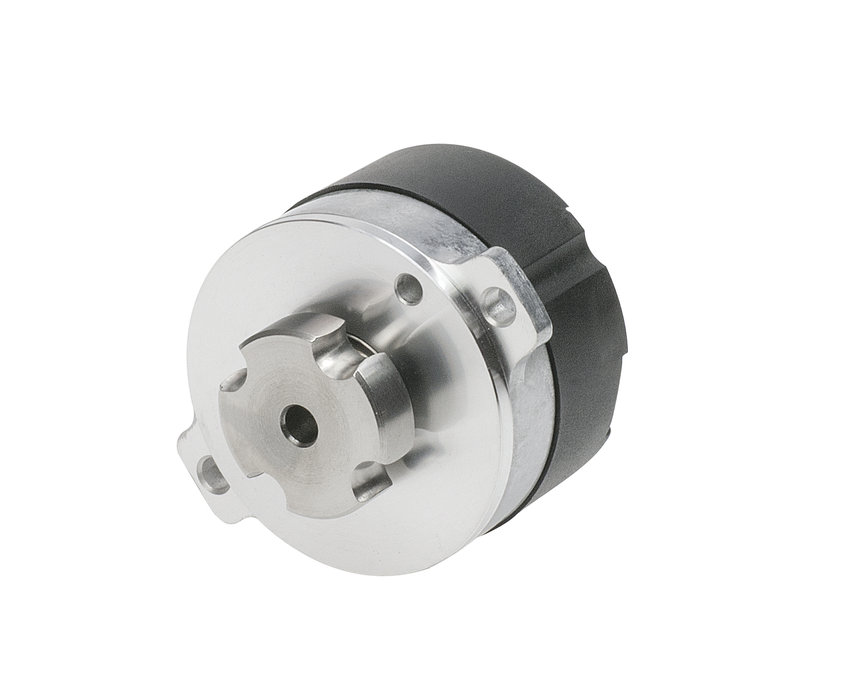
In single-cable solutions, the cores for the encoder’s signal transmission are integrated into the servo cable, which means that two cables are thereby combined to form a hybrid cable. This solution’s success is down to the benefits of space and weight optimisation, and in particular to the reasonable price and reduced connection technology. In areas with limited space, this translates into additional advantages for machinery, control cabinets and drag chains, for example.
Basic requirement for the set-up of a single-cable solution between a servo motor and a servo controller is a digital encoder that is specifically developed for this type of communication. The encoder is permanently connected to the servo motor. For this reason, the manufacturer of the servo motor needs to provide its customers with an end-to-end solution: Not only the servo motor needs to be equipped with a rotary encoder, the controller needs to be adapted to the concept of a single-cable solution as well - as communication is always established between two units. Hengstler offers special rotary encoders in its new product range that use the ACURO®link interface, an open protocol, creating the ideal symbiosis to meet the high requirements of single-cable solutions. “The ACURO®link interface was specifically designed to support two- and four-wire applications,” explains Johann Bücher, Director of Encoder Strategy at Hengstler.
Helukabel’s challenge as cable manufacturer consists in securing a sustainably stabile and fail-safe data transmission. The two-cable solution uses up to three shields to protect the signal pairs from the disruptive influences of the power cores in the traditional set-up. In addition, it is generally recommended that the maximum possible distance between the servo and encoder cables is considered when laying the cables. However, the feedback cores of a hybrid cable are routed into the servo cable directly. It reduces the physical distance almost entirely and the requirements for EMC shielding attain a new quality level.
Whether the motor rotates or not is based on the signal’s quality that arrives at the receiver. The fewer external disruptions that penetrate the signal element, the better the data quality is that arrives at the receiver. The shielding of the data cores accounts for the protection from EMC emissions. The longer the shielding remains intact while in use, the longer the protection will be maintained. The service life of the shielding can be nearly “infinite” if the hybrid cable is installed in a stationary application. The service life only starts to shorten when mechanical load is placed on the cable in a dynamic application, such as a drag chain. The reliability and fail-safe quality of data transmission is a product of the individual disruptions, which means that the longer a cable, the more critical the application. Hengstler’s research & development team tests two- and four-wire versions of their encoder using a 100-m cable in each case under load. Based on the acquired practical experience, these tests provide adequate assurance that the cables can withstand even future challenges arising in increasingly complex applications. It is now possible to have high-performance multi-turn control thanks to the Hengstler AD37 rotary encoder. It sets new standards with a 10-Mbaud transfer speed and data exchange rates reaching 32 kHz, while combined with the transfer of entire positioning data providing an extremely high electromagnetic compatibility (EMC). In addition, the data protocol of the electrical interface fulfils the requirements of SIL3 in accordance with IEC 61508 and Cat. 3PLe, in compliance with EN ISO 13489, while the AD37 rotary encoder itself and the IP core in the control can meet all requirements from non-SIL, SIL1, SIL2 to SIL3, depending on the customer’s specific application.
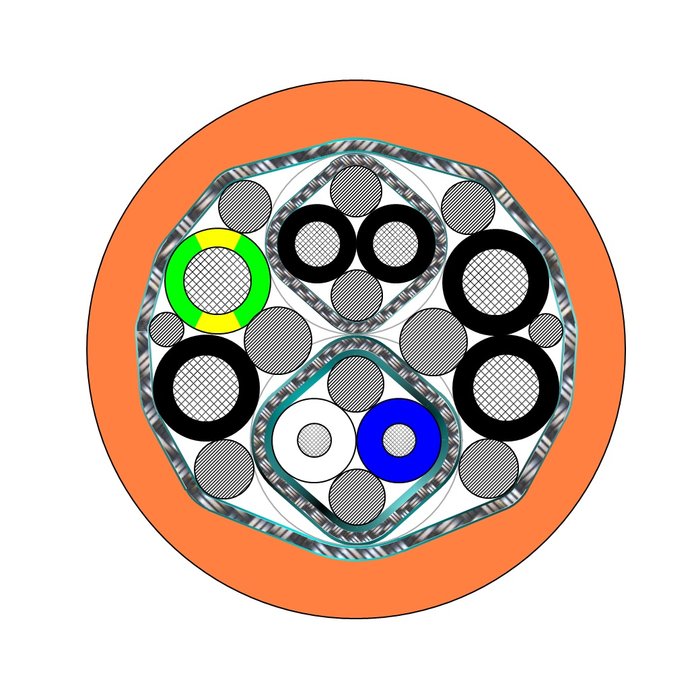
The loads that cables are subjected to in the field are growing as the market requirements of the manufacturers of machinery and plants increase. Machine designs are smaller than ever before, as the axes in the field of traditional machine tools become more dynamic and faster. These developments reduce the available space to a minimum, and the bending radii of the drag chains become tighter. Cables and wires need to be tailored to the specific application in order to provide with high stability in drag chain applications while maintaining competitive prices, which means that the design team at Helukabel GmbH selects different designs for specific requirements. They depend on parameters such as movement distance, minimum bending radius, speed, acceleration and minimum number of cycles. In addition to the design, the choice of materials also plays a decisive role. They primarily depend on external factors such as ambient temperatures and/or the required durability of the materials (aggressive coolants and lubricants, for example). In addition, there are other properties that need to be taken into consideration such as flame-resistance and halogen-free design.
The different performance requirements of the motors translate in different cross-sections for the supply cables. The larger the cross-section, the thicker the cable. It is necessary that the tests include different bending radii in order to draw conclusions for all other cross-sections, as it is not enough to test one cross-section and cable construction in a drag chain. The Helukabel Group tests cables on nine different testing systems that can differentiate between the lengths and the acceleration and speed parameters when testing. These tests are very intricate and require constant monitoring and supervision. However, they are also necessary in order to ensure the quality and stability of data transmission.
Helukabel was the first cable manufacturer who confirmed the durability of its hybrid cables with a system test involving more than five million cycles. In the meantime, several hundreds of kilometres of these hybrid cables have been installed and are in use in different applications around the world.
“We are the cable manufacturer with the greatest advantage in terms of experience. We invested a great deal of time in this solution from a very early stage and have gathered vast experience in the field to be able to develop working, reliable solutions for drive specialists. Our Topserv Hybrid has become established as the standard for the two-wire solution”, says Thomas Pikkemaat, Product Manager for Drive Technology at HELUKABEL® GmbH.
Drag chain test systems at Helukabel’s research and development center.