The Vital Role of C1D2 Certification in Industrial Ethernet Switches
An Article by Henry Martel, Field Application Engineer, Antaira Technologies.
www.antaira.com
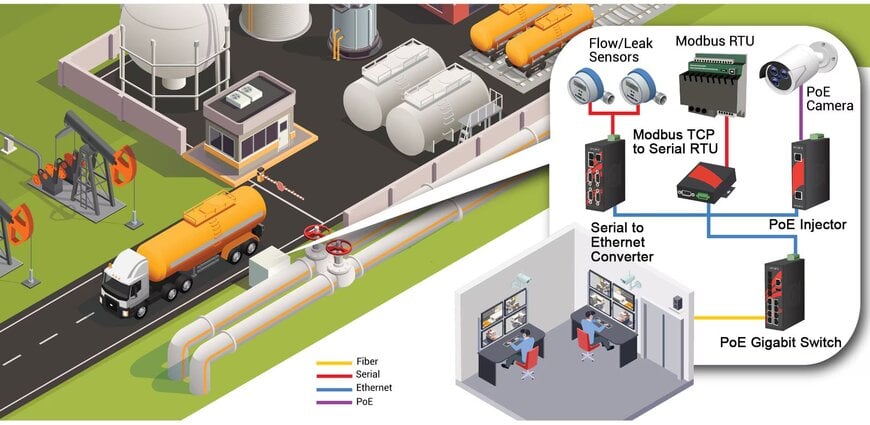
Oil pipelines require a continuous stream of data collected and transmitted over long distances via fiber optics using C1D2 Ethernet switches at field stations, eventually ending at a control room
When we think about Ethernet network switches, the word “explosive environment” rarely comes to mind. However, with the growing adoption of Ethernet networks in hazardous industrial locations, such as petrochemical processing and underground mining, the time is right to consider classification certified solutions.
Like any electrical device, a network switch generates heat while operating. Consequently, an industrial networking switch can serve as a potential ignition source when such network switches are installed in areas where explosive or flammable substances are present, also known as hazardous or classified locations.
In this article we delve into hazardous locations as they are defined in the National Electrical Code (NEC). We focus on NEC Class 1, Division II locations (C1D2) defined as where flammable gases, vapors, or liquids are present, but not normally in sufficient quantities to create an explosive atmosphere under normal operating conditions.
NEC Classifications
First published in 1897, the NEC is a standard that outlines requirements for safe electrical installations in the United States. It is updated every three years with the 2023 edition being the most current version.
Depending on the level of threat, hazardous locations are categorized in NEC Articles 500 to 503 using its Class/Division system. Divisions are further differentiated by the NEC into Groups depending on the nature of the hazardous substance. In the event that more than one explosive substance is in a hazardous area, classification takes into account the more dangerous of the substances.
The NEC’s Class/Division system works as follows:
1. The first step is to determine the hazardous substance in the area. The NEC uses three different Classes to identify the substance.
- Class I: Gas/Vapor
- Class II: Dust
- Class III: Fibers
2. Next, it must be established how often this hazardous substance is present. The NEC does this work by separating the Class into Divisions.
- Division 1: The substance is present under normal operation, continuously or for long periods of time.
- Division 2: The substance is rarely present or only under abnormal (emergency) circumstances such as a leak. It also applies where there are no other security barriers between a secure Division 1 space and a secure, non-hazardous location.
3. Due to the variety of uniqueness and safety features of certain substances, the NEC requires hazardous materials be further broken down into Groups.
- Group A: Acetylene
- Group B: Hydrogen
- Group C: Ethylene
- Group D: Propane
- Group E: Metal dusts (Magnesium, Aluminum, Titanium etc.)
- Group F: Carbon-based (coal and charcoal)
- Group G: Nonconductive dusts (Flour, wood/sawdust, plastic dust)
To help better understand NEC Classes, Divisions and Groups, consider these two examples:
- EXAMPLE 1: A Propane Tank Filling Station would be Class 1 (Gas/Vapor), Division 2 (Rarely present or under the risk or abnormal safety or security circumstances), and Group D (Propane) or C1D2-D.
- EXAMPLE 2: An Open Conveyor Belt moving coal with airborne dust continuously present would be classified as Class II (Dust), Division 1 (Normal operations), Group F (Carbon based products) or C2D1-F.
Explosion-Proof Designs
In a C1D2 location there are two ways for an industrial Ethernet switch to achieve code compliance: one, intrinsically safe equipment and two, implementing proper sealing of electrical conduits.
Intrinsically safe equipment is designed to be inherently safe and will not release enough energy to ignite a flammable atmosphere.
Proper sealing of conduits prevents the ingress of hazardous materials and helps prevent explosions.
Traditionally, the North American solution to meet C1D2 explosion proofing has been to house electrical devices inside an NEC-certified enclosure solidly constructed of cast iron or aluminum. These enclosures are specially engineered to contain blast pressures from an internal explosion occurring when an arching or sparking device ignites gases or vapors trapped within it. Although expensive, an explosion-proof enclosure is necessary for high power applications including transformers and relays.
Intrinsically Safe Network Switches
An explosion-proof enclosure isn’t always practical, efficient or necessary for an Ethernet switch or other network device. An alternative approach is the use of Intrinsically Safe equipment. Rather than isolating an explosion within an enclosure, Intrinsically Safe switches prevent the explosion all together by not accumulating enough energy to ignite a hazardous atmospheric mixture. Intrinsically Safe switches limit both electrical and thermal energy to a non-ignitable level, even in the event of a fault condition, through the use of special electronics and wiring.
Note that an Intrinsically Safe Ethernet switch must be paired with an Intrinsically Safe barrier that limits the supplied power to a safe level that will not trigger an explosion. If you plan to use this approach, ensure that the industrial switch doesn’t draw more voltage and current than the barrier is designed for and take into account capacitive and inductive impacts, including in the cable.
Advantages of Intrinsically Safe Switches
There are a number of benefits to choosing a C1D2 designated Intrinsically Safe switch. For one, installation is far more straightforward and less expensive since it eliminates the need for sealed conduits or an explosion-proof enclosure. Also, an Intrinsically Safe switch can be repaired on-site. In contrast, a standard industrial Ethernet switch mounted inside an explosion-proof enclosure must be removed from the area for servicing and the power turned off. Intrinsically Safe switches also make it possible to use a single cable for both power (Intrinsically Safe Power over Ethernet or PoEx) and data, which is the preferred solution for modern automation systems.
Conclusion
Ethernet networks continue to make important strides across a range of heavy industries. As a result, switches must be deployed in close proximity to processing operations in explosive atmospheres. To help customers maintain plant safety and achieve code compliance, Antaira offers managed switches certified for C1D2 certified for C1D2 and equipped with network redundancy, industrial-grade performance and reliability, and simplified device management.
www.antaira.com