www.industryemea.com
27
'17
Written on Modified on
Field distribution systems – new intralogistics drives
Novel plug&play drive design facilitates installation and operation
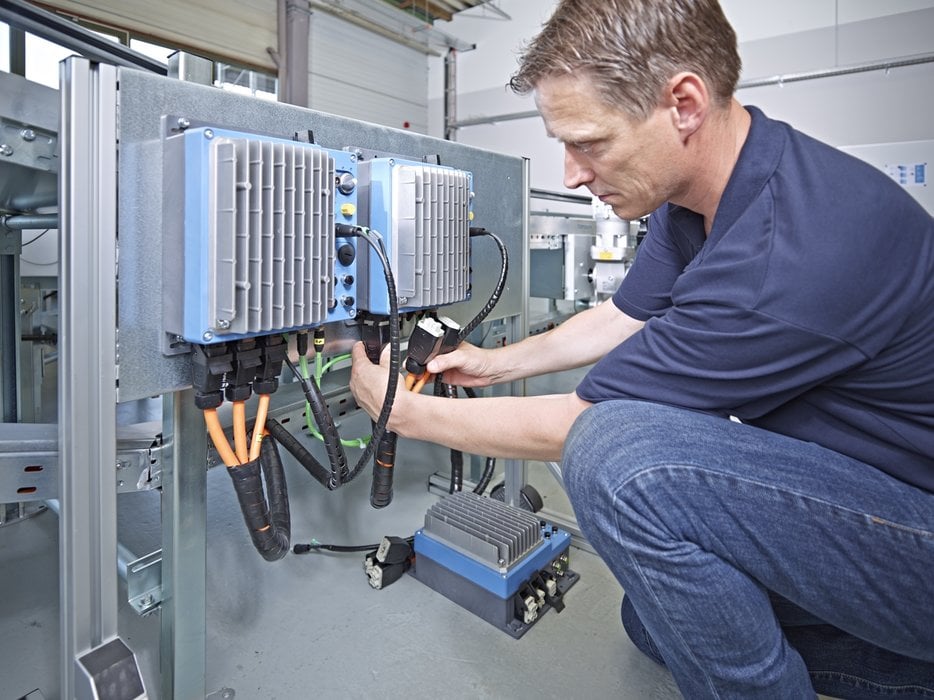
NORD DRIVESYSTEMS has developed a new line-up of user-friendly, low-maintenance electronic drives for intralogistics systems. These new frequency inverter and motor starter models for distributed installations are especially easy to deploy and operate. Coded plug-in connectors ensure comfortable handling throughout a system's lifetime, from the initial installation, to maintenance, to eventual replacement. The devices provide very flexible mechanical and feature customization options that can all be configured to individual requirements: interface ports, manual switches, and a range of functions that even include closed-loop control and sequential control managed by an integrated PLC.
Distributed drives must execute commands from a higher-level central control system with absolute reliability. In many scenarios, however, operating staff and service technicians may also require optional direct access to individual drives or drive axes on location. Such access enables them to quickly resolve small problems like a jammed conveyor belt that might otherwise lead to a shut-down of the entire line, sometimes putting hundreds of conveyor modules out of work for a considerable amount of time. NORD DRIVESYSTEMS has therefore developed the new NORDAC LINK drive electronics line for particularly convenient and time-saving operation and maintenance. Key features of the new drives are coded plug-in connectors for all power and communication lines, as well as for various sensors, actuators, and encoders. These greatly facilitate correct, quick, and safe connections. LEDs on the field distribution systems enable error diagnostics on the production floor, and operators can remedy problems then and there using the maintenance and control switches on the drives. The compact units are designed for wall or frame mounting. Featuring a busbar for the mains supply, they can be daisy-chained with short cabling from one drive to the next, which saves time and expenses. The field distribution systems are able to control asynchronous or synchronous motors. They come with comprehensive certifications for operation everywhere in the world. The drives support Profibus, CANopen, DeviceNet, and AS-i communication, as well as the Industrial Ethernet protocols ProfiNet, Ethernet POWERLINK, EtherCAT, and EtherNet/IP.
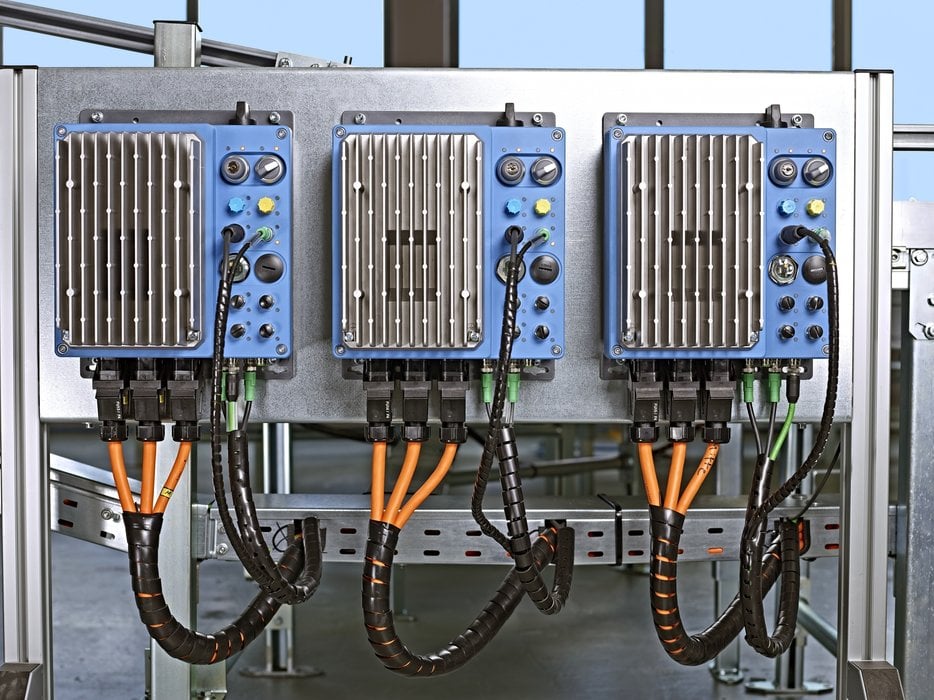
Expertise for conveyor drives
Distributed conveyor drives have been a focus for drive technology developments at NORD for many years, resulting in a versatile portfolio of distributed drive electronics that cover a considerably wider range of functions than competing products. In 2009, NORD first introduced motor-integrated frequency inverters featuring rotary encoder feedback, position control, hoist functions, and Safe Stop. 2015 saw the addition of a PLC in motor-integrated drive units. Now, years of experience in various sectors and close cooperation with customers have led to the new line of field distribution systems. These intelligent drives with a proven user-friendly user interface can be flexibly configured for a wide range of conveying tasks. An integrated PLC and PI controller functions even enable the establishment of autonomous modular systems. Frequency inverters and motor starters in the 0.55 to 3 kW performance range are immediately available. Later in 2017, inverters for motors up to 7.5 kW rated output will be added to the line.
Reliable drives with a high overload capacity
NORDAC LINK motor starters control soft starts and stops, as well as reversing operation in fixed speed applications. Just like inverter-type field distribution systems, these wear-free electronic switches integrate extensive monitoring and protection functions – this saves the cost for typical control cabinet components such as motor circuit breakers and reversing contactors. In more demanding drive applications, frequency inverters ensure efficient and precise speed control and wear-free brake actuation. Employing field-oriented vector control, they deliver the required speeds reliably even under great load fluctuations and provide full torque even at standstill (0 rpm). These AC vector drives have a high overload capacity of 150% for one minute and up to 200% for brief periods. An integrated load monitor prevents damage to the equipment in case of blocked applications. The inverters also support direct connection of incremental and absolute encoders. Multiple drives in master/slave operation can synchronize speed or positions. Additional optional features include the STO (Safe Torque Off) and SS1 (Safe Stop 1) safety functions according to EN 61800-5-2.
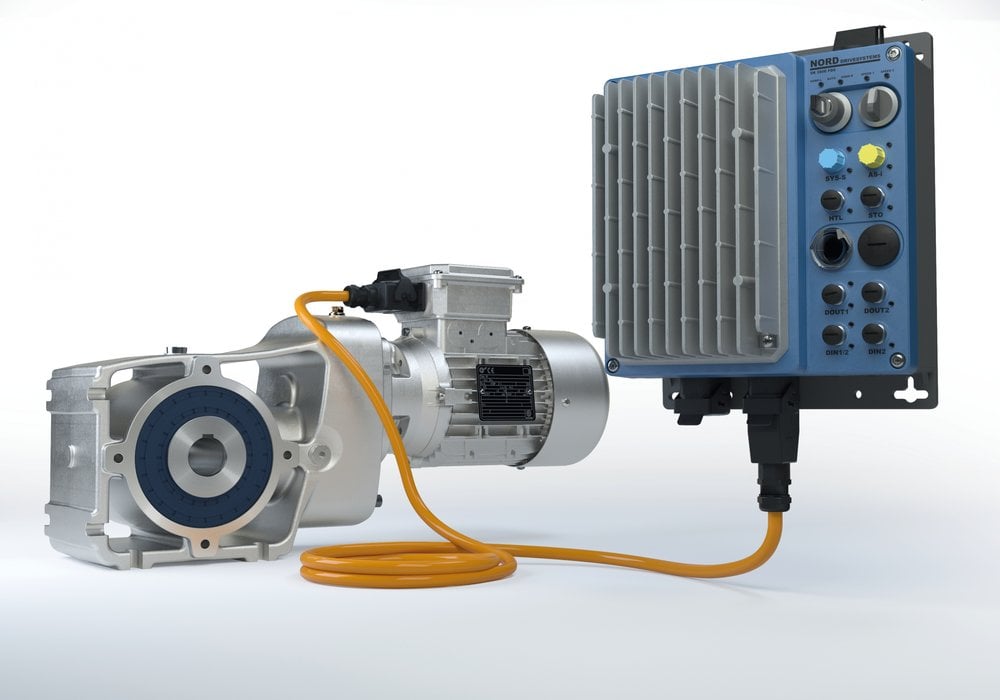
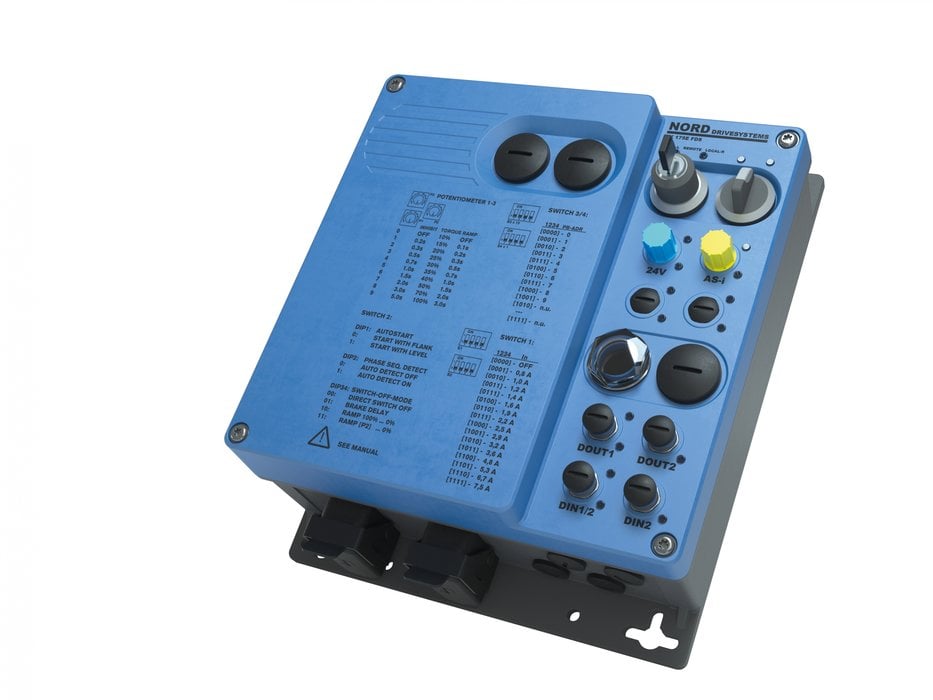
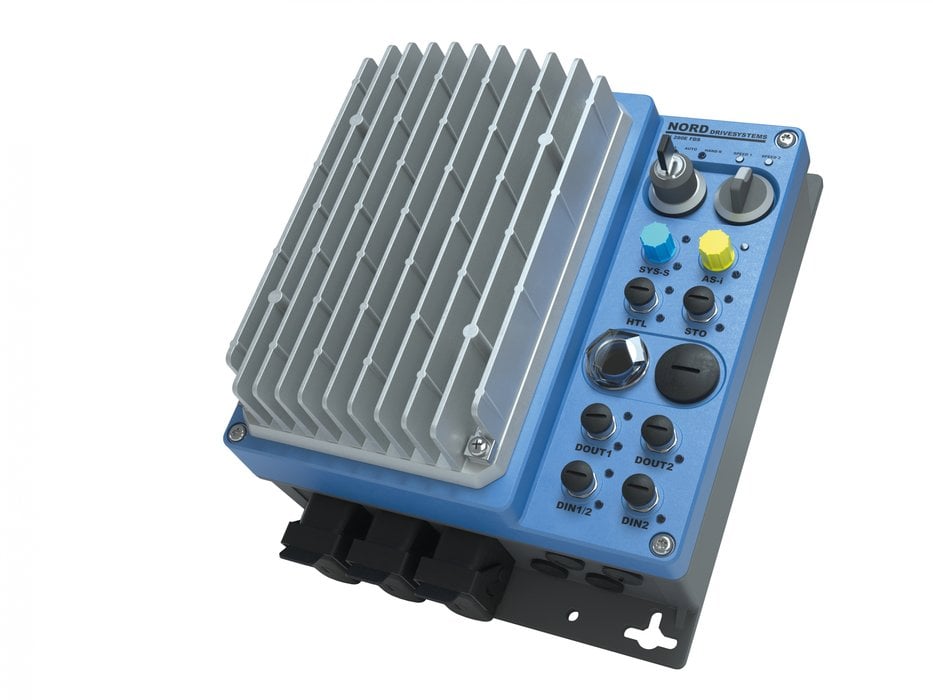
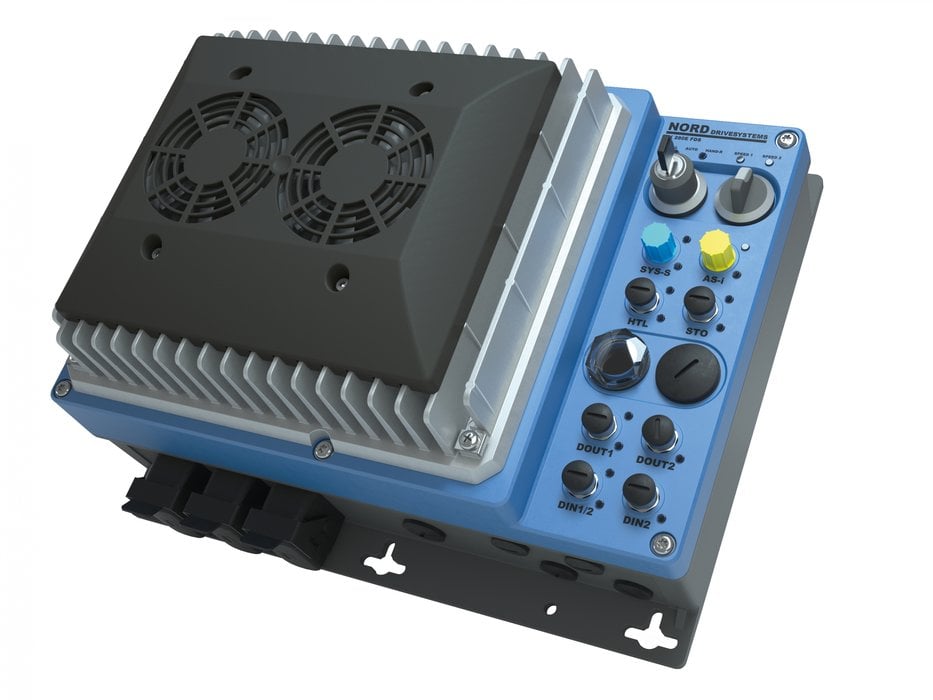